Pumps to move liquids and gases are used in industrial and fleet applications. A majority of pumps used in industrial applications are either centrifugal or positive displacement. In both scenarios, bearings are the component that must be lubricated and observed. Rotary positive displacement pumps have gears, lobes, vanes, or screws which are also lubricated, typically by the fluid they are pumping, whether it is an oil/air mix or a lubricant.
Ask the Expert: Pump Oil Analysis
After mechanical seals, bearing failures is the second leading cause of pump repairs. Pump maintenance using oil analysis concentrates customarily on the bearings and bearing life. Many pump bearings do not reach their theoretical (L10) fatigue life. Two-thirds of all rolling element bearings in service, which had to be substituted, failed ahead of time. Only one-third of bearings fail because of fatigue spalling (L10 Life). Of the two-thirds that failed prematurely, the split up is as follows:
- 30% of bearings fail early because of lubrication issues:
- Degraded lubricant
- Poor or incorrect lubricant
- Lack of lubricant
- 17% fail because of contamination getting into the bearing. This is the most problematic factor because contaminants are all over.
Common contaminants are:
- Air
- Particulates
- Water
- Cleanup/process chemicals
Checking pumps using oil analysis is an accepted technique for enhancing the MTBF of the pump.
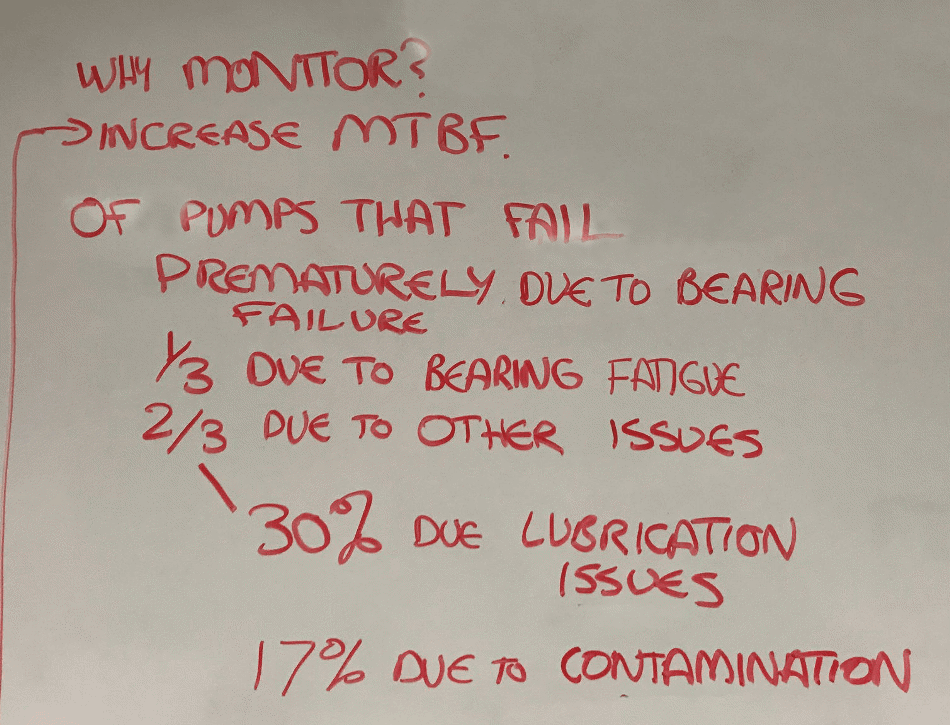
Kinematic Viscosity
Kinematic viscosity can be defined as the resistance of a fluid to flow under gravity. Viscosity is the most critical physical property of a lubricant for pumps. The lubricants’ viscosities differ based on their grade or classification, as well as the degree of oxidation and contamination in service. Oil viscosity is projected to rise over time and use, and loss of viscosity is said to be more severe than an increase. In the case of rotary screw systems where the oil is blended with lubricant and then separated, the viscosity must be taken after the separator, or else the air or gas will influence the result. Viscosity is regularly measured immediately after an oil change to check if the right oil was added, as well as on a systematic basis. New technologies make it simple to measure kinematic viscosity: there are solvent-free, low volume systems that integrate user-friendliness with data logging capability.
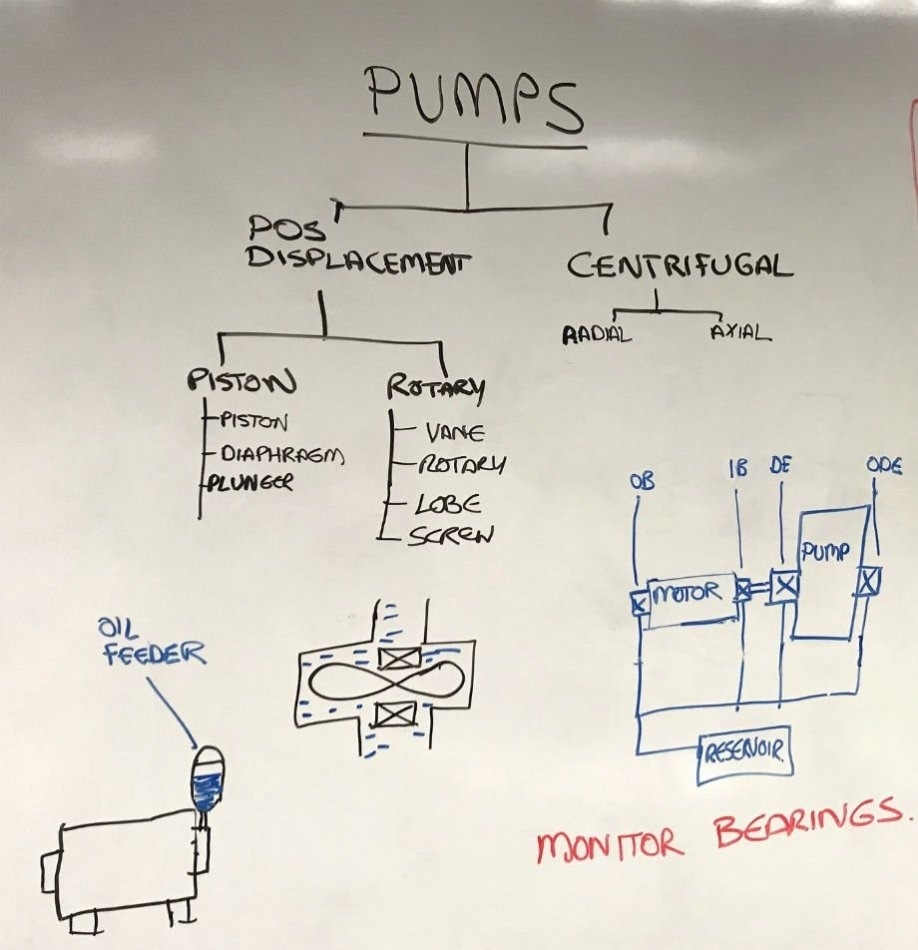
Water Contamination
Globally, water is the most common liquid contaminant in pumps, and hence always needs to be monitored. Too much water in a system damages a lubricant's ability to separate opposing moving parts, allowing extreme wear to happen with ensuing high frictional heat. Water contamination should not surpass 0.25 % for the majority of equipment, though centrifugal pumps used in power plants stipulate much tighter limits such as 500 ppm for boiler feed pump bearings. Numerous new technologies exist to detect water contamination in lube oils, and on-site results correlate very well with laboratory methods.
Particle Counting
Particle counting measures a fluid’s cleanliness and is an important test for centrifugal pumps, where rolling element bearings or sleeve bearing are being tracked. For positive displacement pumps, it helps to establish if ingression or wear is happening on other moving parts besides bearings. Gear and vane pumps possess very tight tolerances, and are vulnerable to jamming if the oil is not filtered well. When particle counts are high, it is essential to understand the reason. Latest technologies such as LaserNet Fines count particles and report to SAE AS 4059 or ISO 4406, as well as provide more specifics about particle morphology to assist the user in understanding where the particles are originating from. Particle imaging enables maintenance teams to instantly notice sand/dirt particles and also the level of ferrous debris that is adding to the count. This level of detail enables better work orders to be formed, concentrating on removing the root cause of the particle.
Total Acid Number
Total Acid Number (TAN) denotes a titration technique meant to specify the relative acidity in a lubricant. When the TAN value touches a preset level for a specified lubricant and application, it means it is time to change the oil. A sudden rise in TAN would be indicative of irregular operating conditions (for example, overheating) that require analysis.
Elemental Spectroscopy
Elemental spectroscopy is a method for detecting and quantifying elements in a used-oil resulting from contamination, wear, and additives. The oil sample is energized to make each element discharge or absorb a quantifiable amount of energy, which specifies the element concentration in the oil. The results obtained reflect the concentration of all dissolved metals (from additive packages) and particulates. This test is critical for all off-site and on-site oil analysis, as it provides information on contamination, machine, and wear condition comparatively accurately and quickly.
For pumps, bearing wear from nonferrous roller components can be identified with the help of elemental spectroscopy.
Infrared Spectroscopy
Infrared spectroscopy is an excellent method for detecting organic contaminants, water, and oil degradation products in a used-oil sample. These are detected by examining the infrared spectrum of a used oil and looking for absorption at particular peaks that match the presence of different components. The concentration of these components is relative to the amount of light absorbed at the wavelength of interest.
Oxidation can be defined as a measure of the degradation byproducts in the oil. If oxidation becomes extreme, the lubricant will corrode crucial pump surfaces, and also deposit silt or lacquer at servo valves. The more the "oxidation number", the more the level of oxidation.
WDA (Wear Debris Analysis/(Analytical Ferrography)
WDA defines either a patch or an analytical method that divides magnetic wear particles from the oil and places them on a glass slide called a ferrogram. Microscopic inspection of the slide or patch allows characterization of the wear mode and probable sources of wear in the machine. This method is called analytical ferrography. It is a superior indicator of abnormal ferrous and non-ferrous wear; however, it is typically only performed by a skilled analyst.
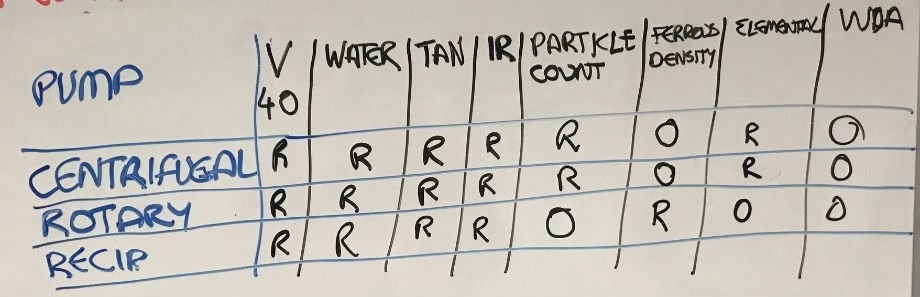
Recommended oil analysis test packages for pumps
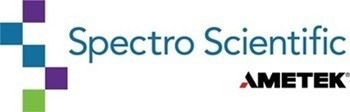
This information has been sourced, reviewed and adapted from materials provided by AMETEK Spectro Scientific.
For more information on this source, please visit AMETEK Spectro Scientific.