Fine powders and granular materials are extensively used in industrial applications. To manage and to enhance processing techniques, these materials have to be exactly characterized. The characterization techniques are connected either to the properties of the grains (granulometry, chemical composition, morphology, and so on) and to the behavior of the bulk powder (density, flowability, electrostatic properties, blend stability, and so on).
However, concerning the physical behavior of bulk powder, most of the methods used in quality control or R&D laboratories are based on traditional measurement methods. During the past 10 years, Granutools has updated these methods to match the current requirements of production departments and R&D laboratories. Specifically, the measurement processes have been automatized and demanding initialization techniques have been formulated to gain reproducible and interpretable results. Furthermore, the use of image analysis methods enhances the precision of the measurements.
A range of measurement techniques has been developed to meet all the requirements of industries processing granular materials and powders. However, in this article, the focus will be on the GranuPack instrument.
GranuPack
The tapped density, the bulk density, and the Hausner ratio measurement (generally referred to as “taptap test”) are very common for powder characterization as they are simple and offer speed of measurement. Furthermore, the density and the ability of a powder to expand its density are crucial parameters for transportation, storage, caking, and so on.
The suggested procedure is defined in the pharmacopeia. This basic test has three big drawbacks. First, the result of the measurement relies on the user. Actually, the filling technique influences the primary powder volume. Second, the volume measurements using naked eyes induce strong flaws in the results. Finally, with this simple technique, the compaction dynamics is fully missed between the first and the final measurements.
The GranuPack instrument is an automated and enhanced tapped density measurement technique based on recent fundamental research results. The behavior of the powder submitted to successive taps is examined with an automatized device. The Hausner ratio Hr, the initial density ρ(0), and the final density after n taps ρ(n) are measured precisely. The tap number is usually fixed at n = 500. Furthermore, a dynamical parameter n1/2 and an extrapolation of the maximum density ρ(∞) are taken out from compaction curves. Extra indexes can be used but they are not discussed in this article.
The powder is put into a metallic tube with a rigorous automated initialization process. Later, a light hollow cylinder is positioned on top of the powder bed to maintain the powder/air interface in a flat manner during the compaction process. The tube holding the powder sample rose to a fixed height of ΔZ and performs free falls. The free fall height is usually fixed to ΔZ = 1 mm or ΔZ = 3 mm. The height h of the powder bed is measured automatically following each tap. From the height h, the volume V of the pile is calculated.
As the powder mass m is identified, the density ρ is assessed and plotted after each tap. The density is the ratio between the mass m and the powder bed volume V. With GranuPack technique, the results are reproducible using a small quantity of powder (usually 35 mL). The Hausner ratio Hr is associated to the compaction ratio and is calculated by the equation Hr = ρ(500)/ρ(0), where ρ(0) is the primary bulk density and ρ(500) the tapped density computed acquired after 500 taps.
Powders Description
Three food powders were chosen to make a comparison between the GranuPack and Densi-Tap instruments. They are called Powder A, B, and C. While Powder A and powder B are vegetal powders, powder C is a protein. Each sample was examined under the same temperature/humidity conditions (1% and ±1 °C). All measurements were done by the LRGP (Laboratoire Réactions et Génie des Procédés - University of Lorraine, Nancy, France) by Assia Saker under the supervision of Pr. Philippe Marchal.
Table 1. Food powders SEM pictures. For each powder, magnifications are 20 µm, 50 µm, and 100 µm (from left to right).
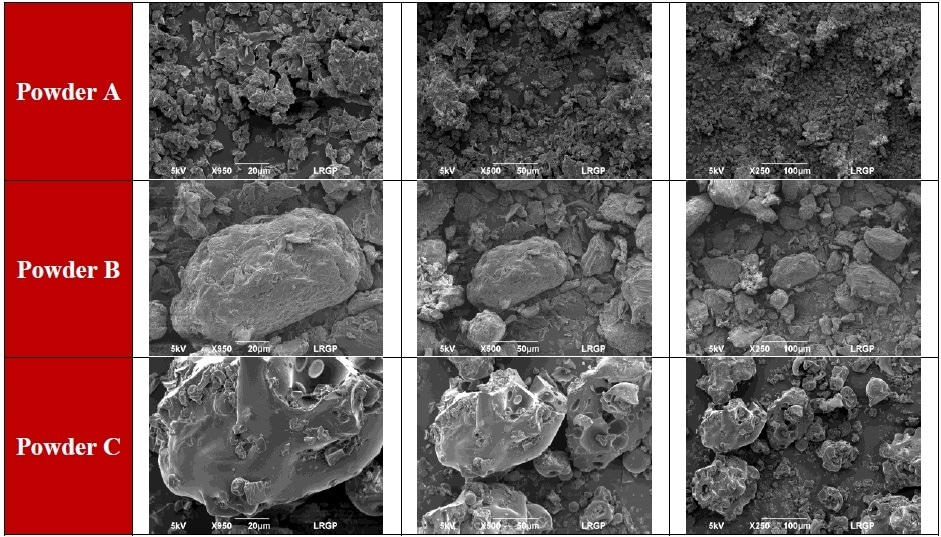
Table 2. Particle size, morphology, and densities of food powders
Sample name |
Particle Size Distribution ±1 μm |
Morphology |
Ture density ± 0.01 (g/mL) |
d(4.3) |
d(3.2) |
d10 |
d50 |
d90 |
Span |
Powder A |
8 |
15 |
6 |
14 |
38 |
3 |
Agglomerate |
1.46 |
Powder B |
24 |
82 |
14 |
74 |
155 |
2 |
Irregular |
1.47 |
Powder C |
184 |
282 |
123 |
267 |
472 |
1 |
Isometric rough |
1.23 |
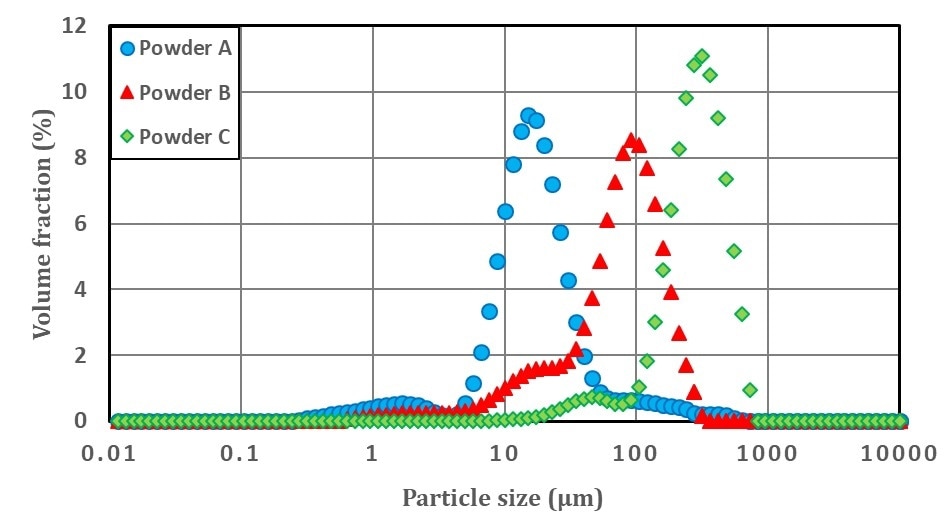
Figure 1. Particle size distribution of food powders
Densi-Tap Analysis
Densi-Tap is engineered to measure the bulk density of both powders and formed particles (maximum size around 5 mm). The sample is poured into a graduated cylinder (total volume of 250 mL) hinged on a tapping device. Prior to the taps, the first sample volume is read by eyes on a cylinder graduation. Finally, when tapping is finished (in this article, 500 taps were done), the tapped volume is read in the same manner. These steps allow to establish initial, final bulk density and to compute the Hausner/Carr ratios. For each powder, measurements have been repeated thrice (by the same person — as Densi-Tap is user-dependent) to confirm results reproducibility.
Table 3. Densi-Tap experimental results for powders A, B, and C
Powder A |
|
|
|
|
|
|
mp (g) |
65.87 |
|
|
|
|
|
T(°C) |
Vi (mL) |
Vf(mL) |
ρi (g/mL) |
ρf (g/mL) |
Hr |
Cr |
23.4 |
184 |
150 |
0.36 |
0.44 |
1.23 |
18.48 |
23.6 |
184 |
149 |
0.36 |
0.44 |
1.23 |
19.02 |
23.8 |
184 |
150 |
0.36 |
0.44 |
1.23 |
18.48 |
|
|
|
|
Average |
1.23 |
18.66 |
Powder B |
|
|
|
|
|
|
mp (g) |
115.92 |
|
|
|
|
|
T(°C) |
Vi (mL) |
Vf(mL) |
ρi (g/mL) |
ρf g/mL) |
Hr |
Cr |
21.6 |
170 |
139 |
0.68 |
0.83 |
1.22 |
18.24 |
21.8 |
174 |
141 |
0.67 |
0.82 |
1.23 |
18.97 |
22.2 |
170 |
140 |
0.68 |
0.83 |
1.21 |
17.65 |
|
|
|
|
Average |
1.22 |
18.28 |
Powder C |
|
|
|
|
|
|
mp (g) |
75.85 |
|
|
|
|
|
T(°C) |
Vi (mL) |
Vf(mL) |
ρi (g/mL) |
ρf (g/mL) |
Hr |
Cr |
21.6 |
182 |
149 |
0.42 |
0.51 |
1.22 |
18.13 |
21.7 |
182 |
149 |
0.42 |
0.51 |
1.22 |
18.13 |
21.7 |
182 |
149 |
0.42 |
0.51 |
1.22 |
18.13 |
|
|
|
|
Average |
1.22 |
18.13 |
Table 3 illustrates that every powder is diverse with regards to the initial and final bulk densities. However, for all tests, the Densi-Tap instrument cannot reveal the variance between powders for the flowability values. Actually, for powder A, B, and C, Hausner and Carr ratios are virtually the same. These assumptions may be described by the small measurements accuracy (sample volume determination done with eyes). Finally, as the Densi-Tap instrument just provides information on the first and final densities, it is unable to display sample compaction kinetics.
GranuPack Analysis
The central purpose of this part is to establish the high accuracy of the GranuPack instrument and to emphasize the significance of samples compaction kinetics. To confirm these assumptions, tests have been done a number of times with the same powders (cf. Table 4, with 500 taps and a tap free-fall of 3 mm) and full average compactions variation (ρ – ρ(0)) curves were plotted (for users who are interested in every bulk density measurements can take a look at Appendix 2).
Table 4. GranuPack experimental results for every food powder
Sample name |
ρ(0) |
Mean ρ(0) |
ρ(n) |
Mean ρ(n) |
n½ |
Mean n½ |
Hr |
Mean Hr |
Cr |
Mean Cr |
ρ(∞) |
Mean ρ(∞) |
τ |
Mean τ |
Powder A test 1 |
0.369 |
0.367 |
0.487 |
0.483 |
13.7 |
13.8 |
1.318 |
1.316 |
24.1 |
24.0 |
0.516 |
0.513 |
9.5 |
10.5 |
Powder A test 2 |
0.363 |
0.479 |
13.7 |
1.319 |
24.2 |
0.509 |
11.0 |
Powder A test 3 |
0.369 |
0.484 |
14 |
1.311 |
23.7 |
0.514 |
11.1 |
Powder B test 1 |
0.652 |
0.651 |
0.792 |
0.790 |
9.3 |
9.1 |
1.216 |
1.215 |
17.7 |
17.7 |
0.826 |
0.824 |
7.9 |
8.1 |
Powder B test 2 |
0.649 |
0.788 |
8.9 |
1.214 |
17.6 |
0.822 |
8.2 |
Powder C test 1 |
0.42 |
0.418 |
0.482 |
0.481 |
14.6 |
14.7 |
1.147 |
1.151 |
12.8 |
13.1 |
0.500 |
0.500 |
18.9 |
21.1 |
Powder C test 2 |
0.425 |
0.482 |
16.3 |
1.136 |
11.9 |
0.501 |
24.8 |
Powder C test 3 |
0.41 |
0.479 |
13.1 |
1.169 |
14.5 |
0.500 |
19.7 |
Table 4 emphasizes the reproducibility of GranuPack and by the looks of every value/constant, it is clear that a high accuracy (about 0.4% — for the bulk density values) and the non-user dependency are realized.
Figure 2 illustrates that GranuPack instrument is able to categorize the powders. As a result of its high accuracy and non-user dependency, the high differences in terms of Hausner and Carr ratios can be shown. Actually, Powder C has the ideal flowability (Hr = 1.151); it is rapidly followed by Powder B (Hr = 1.215). Lastly, Powder A has the inferior flowability with a Hausner ratio close to 1.316.
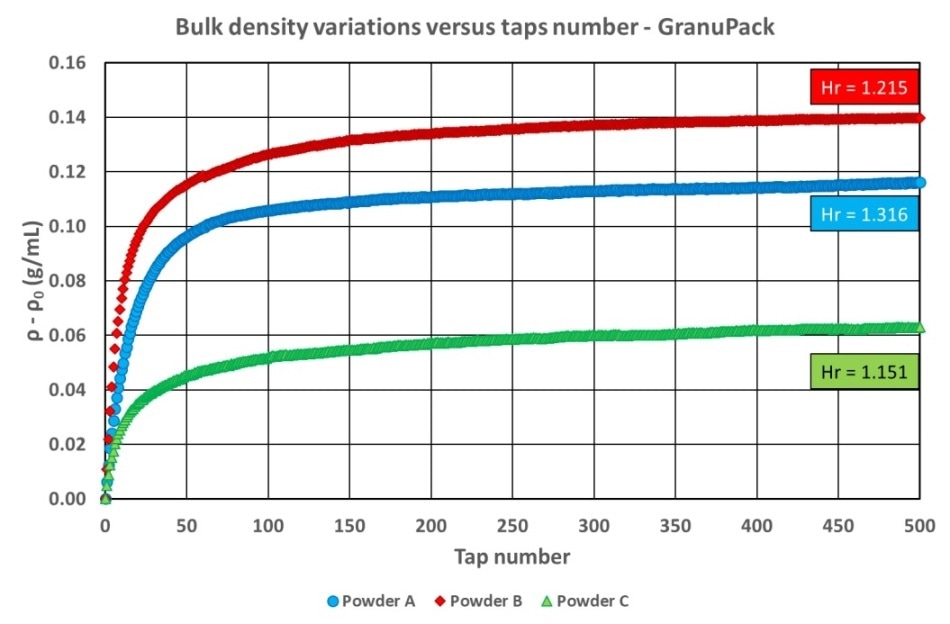
Figure 2. Bulk density variations versus taps number for every powder—GranuPack Instrument.
With the n1/2 and τ constants (refer to Appendix 1), the GranuPack instrument can characterize powders compaction kinetics. Actually, with these constants, it can be observed that powder B has faster compaction compared to Powder A, which is better than Powder C.
Finally, with the comparison between ρ(n) and ρ(∞), it can be concluded that the number of taps was not sufficient to realize the final (ideal) bulk density, which is 0.513 g/mL for Powder A, 0.824 g/mL for Powder B, and 0.500 g/mL for Powder C. This information (which is not shown by Densi-Tap instrument) allows users to outline Standard Operating Procedures (SOP) and to establish with precision how many taps are required to attain the ideal bulk density. The key purpose is to minimize time and energy for all forthcoming experiences.
Conclusions
- For certain powders, Densi-Tap instrument cannot emphasize difference with regards to flowability (with Hausner and Carr ratios) because of its low accuracy and user dependency (powder manually poured into the measurement cell and volume lecture made with eyes).
- Densi-Tap only gives two values (first and final bulk density), thus it is incapable of examining the compaction kinetic.
- With its high measurement precision (3 digits for Hausner/Carr ratios and bulk density — error is nearly 0.4% in bulk density measurements) and its non-user dependency, GranuPack instrument can categorize a lot of varied samples with high accuracy.
- GranuPack offers powders full compaction curves, which permit the user to emphasize the compaction kinetics of every sample. It allows gathering information about the compaction ease phenomenon.
- ρ(∞) values can help outline Standard Operating Procedures (SOP) and to know simply if the number of applied taps has been adequate.
Appendix
Appendix 1: GranuPack Theoretical Background
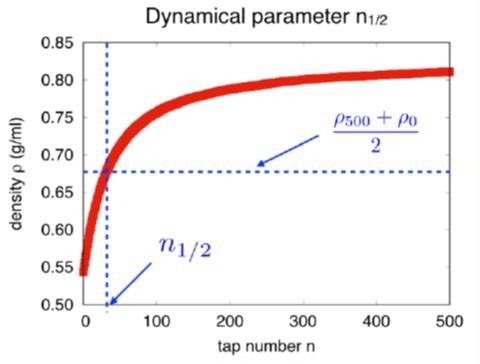
The dynamical parameter n1/2 corresponds to the number of taps needed to reach one-half of the compaction curve.
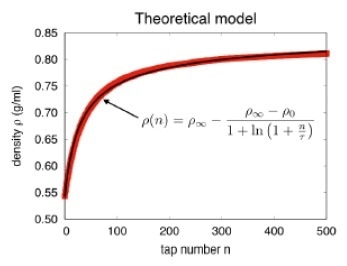
The compaction curve is fitted by a theoretical model to obtain the characteristic tap number τ.
Appendix 2: Experimental Results for All Samples with GranuPack Instrument
In this appendix, the following figure illustrates all the experimental results. The y-axis scale in every chart is narrow. Such a choice is done to reveal the high accuracy of the GranuPack measurement (error bars are always shown, but occasionally, they are too small to be visible).
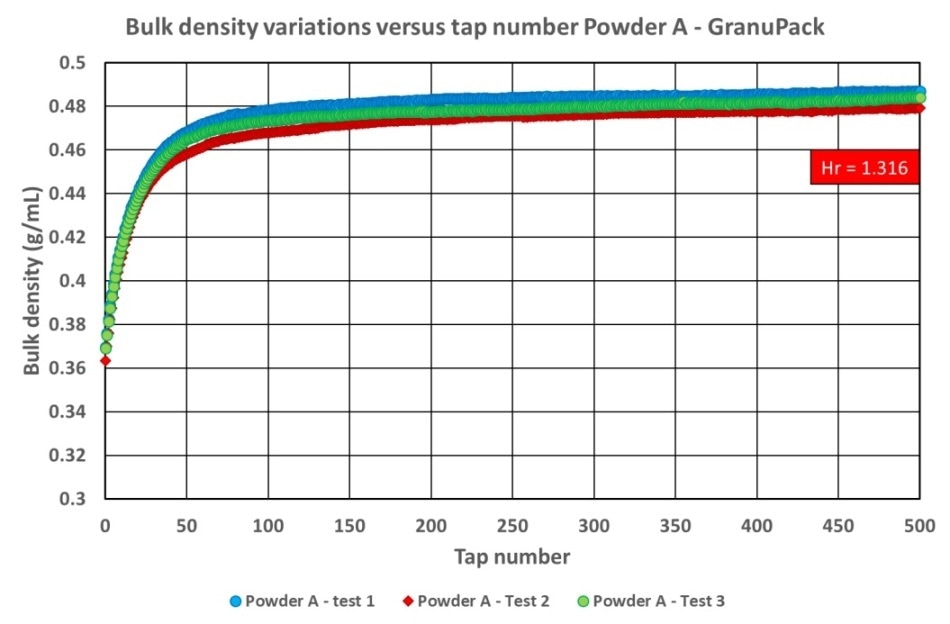
Figure 3. Powder A bulk density versus number of taps
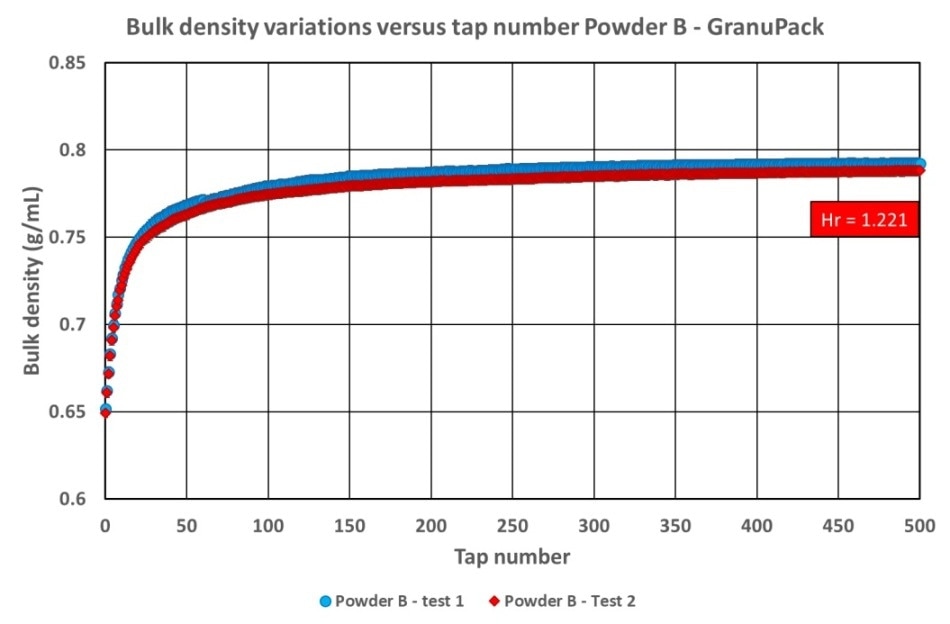
Figure 4. Powder B bulk density versus number of taps
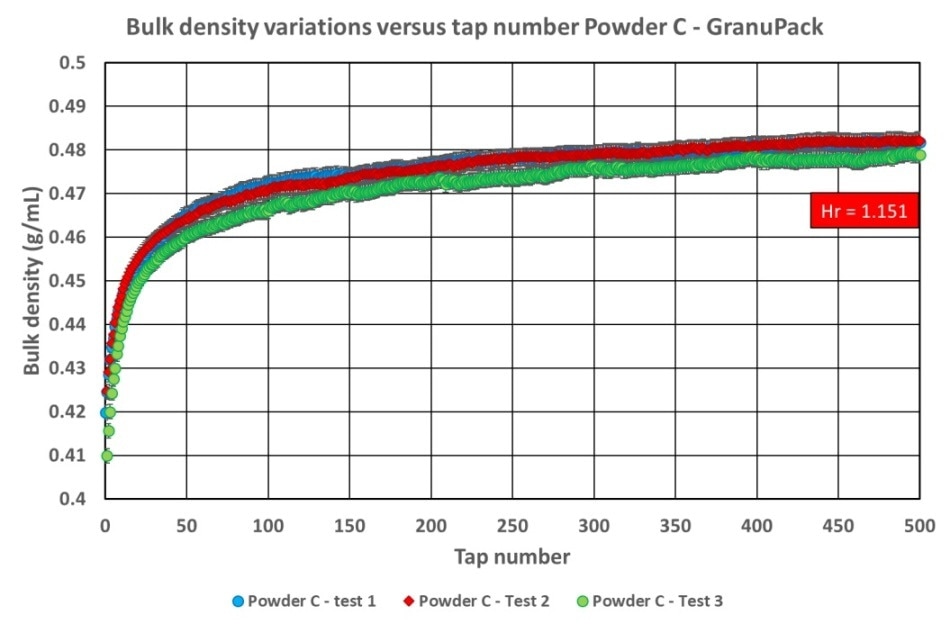
Figure 5. Powder C bulk density versus number of taps
Bibliography
- Cascade of granular flows for characterizing segregation, G. Lumay, F. Boschin, R. Cloots, N. Vandewalle, Powder Technology 234, 32-36 (2013).
- Combined effect of moisture and electrostatic charges on powder flow, A. Rescaglio, J. Schockmel, N. Vandewalle and G. Lumay, EPJ Web of Conferences 140, 13009 (2017).
- Compaction dynamics of a magnetized powder, G. Lumay, S. Dorbolo and N. Vandewalle, Physical Review E 80, 041302 (2009).
- Compaction of anisotropic granular materials: Experiments and simulations, G. Lumay and N. Vandewalle, Physical Review E 70, 051314 (2004).
- Compaction Dynamics ofWet Granular Assemblies, J. E. Fiscina, G. Lumay, F. Ludewig and N. Vandewalle, Physical Review Letters 105, 048001 (2010).
- Effect of an electric field on an intermittent granular flow, E. Mersch, G. Lumay, F. Boschini, and N. Vandewalle, Physical Review E 81, 041309 (2010).
- Effect of relative air humidity on the flowability of lactose powders, G. Lumay, K. Traina, F. Boschini, V. Delaval, A. Rescaglio, R. Cloots and N. Vandewalle, Journal of Drug Delivery Science and Technology 35, 207-212 (2016).
- Experimental Study of Granular Compaction Dynamics at Different Scales: Grain Mobility, Hexagonal Domains, and Packing Fraction, G. Lumay and N. Vandewalle, Physical Review Letters 95, 028002 (2005).
- Flow abilities of powders and granular materials evidenced from dynamical tap density measurement, K. Traina, R. Cloots, S. Bontempi, G. Lumay, N. Vandewalle and F. Boschini, Powder Technology, 235, 842-852 (2013).
- Flow of magnetized grains in a rotating drum, G. Lumay and N. Vandewalle, Physical Review E 82, 040301(R) (2010).
- How tribo-electric charges modify powder flowability, A. Rescaglio, J. Schockmel, F. Francqui, N. Vandewalle, and G. Lumay, Annual Transactions of The Nordic Rheology Society 25, 17-21 (2016).
- Influence of cohesives forces on the macroscopic properties of granular assemblies, G. Lumay, J. Fiscina, F. Ludewig and N. Vandewalle, AIP Conference Proceedings 1542, 995 (2013).
- Linking compaction dynamics to the flow properties of powders, G. Lumay, N. Vandewalle, C. Bodson, L. Delattre and O. Gerasimov, Applied Physics Letters 89, 093505 (2006).
- Linking flowability and granulometry of lactose powders, F. Boschini, V. Delaval, K. Traina, N. Vandewalle, and G. Lumay, International Journal of Pharmaceutics 494, 312–320 (2015).
- Measuring the flowing properties of powders and grains, G. Lumay, F. Boschini, K. Traina, S. Bontempi, J.-C. Remy, R. Cloots, and N. Vandewall, Powder Technology 224, 19-27 (2012).
- Motion of carbon nanotubes in a rotating drum: The dynamic angle of repose and a bed behavior diagram, S. L. Pirard, G. Lumay, N. Vandewalle, J-P. Pirard, Chemical Engineering Journal 146, 143-147 (2009).
- Mullite coatings on ceramic substrates: Stabilisation of Al2O3–SiO2 suspensions for spray drying of composite granules suitable for reactive plasma spraying, A. Schrijnemakers, S. André, G. Lumay, N. Vandewalle, F. Boschini, R. Cloots and B. Vertruyen, Journal of the European Ceramic Society 29, 2169–2175 (2009).
- Rheological behavior of β-Ti and NiTi powders produced by atomization for SLM production of open porous orthopedic implants, G. Yablokova, M. Speirs, J. Van Humbeeck, J.-P. Kruth, J. Schrooten, R. Cloots, F. Boschini, G. Lumay, J. Luyten, Powder Technology 283, 199–209 (2015).
- The influence of grain shape, friction and cohesion on granular compaction dynamics, N. Vandewalle, G. Lumay, O. Gerasimov and F. Ludewig, The European Physical Journal E (2007).
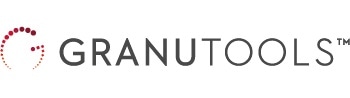
This information has been sourced, reviewed and adapted from materials provided by Granutools.
For more information on this source, please visit Granutools.