Fine powders and granular materials are extensively used in industrial applications. It is essential to precisely characterize these materials in order to control and optimize processing techniques. The characterization techniques are related to the properties of the grains (morphology, granulometry, chemical composition, etc.) or to the behavior of the bulk powder (density, flowability, electrostatic properties, blend stability, etc.).
However, when it comes to characterizing the physical behavior of bulk powder, a majority of the methods used in quality control or R&D laboratories are based on outdated measurement methods. In the past 10 years, these methods have been updated by Granutools to satisfy the current demands of production departments and R&D laboratories. Specifically, automation of the measurement processes has been performed and stringent initialization techniques have been created to achieve interpretable and reproducible results. Furthermore, the precision of the measurements can be improved by using image analysis techniques.
A wide array of measurement techniques has been devised to fulfill all the demands of industries that process granular materials and powders. However, the focus of this article will be on the GranuDrum, GranuPack, and GranuCharge instruments.
GranuDrum
Granutools’ GranuDrum instrument employs an automated method for the measurement of powder flowability based on the rotating drum principle. A horizontal cylinder that has transparent sidewalls, known as a drum, is half filled with the powder sample. The drum rotates around its axis at an angular velocity of 2–60 rpm. Snapshots (30–100 images separated by 1 second) are taken by a CCD camera for each angular velocity. An edge detection algorithm is used to detect the powder/air interface on each snapshot.
Then, calculation of the average interface position and the fluctuations around the average position is performed. Afterward, for each rotating speed, αf, the flowing angle (also called as “dynamic angle of repose”), is calculated from the average interface position and σf, the dynamic cohesive index, is measured from the interface fluctuations. Generally, the value of the flowing angle αf is inversely proportional to the flowability. A broad range of parameters affects the flowing angle — the shape of the grains, the friction between the grains, and the cohesive forces (electrostatic, van der Waals, and capillary forces) between the grains.
The dynamic cohesive index σf is related only to the cohesive forces acting between the grains. A cohesive powder results in an intermittent flow, whereas a non-cohesive powder results in a regular flow. Therefore, a dynamic cohesive index close to zero represents a non-cohesive powder. An increase in the cohesiveness of the powder leads to a corresponding increase in the cohesive index.
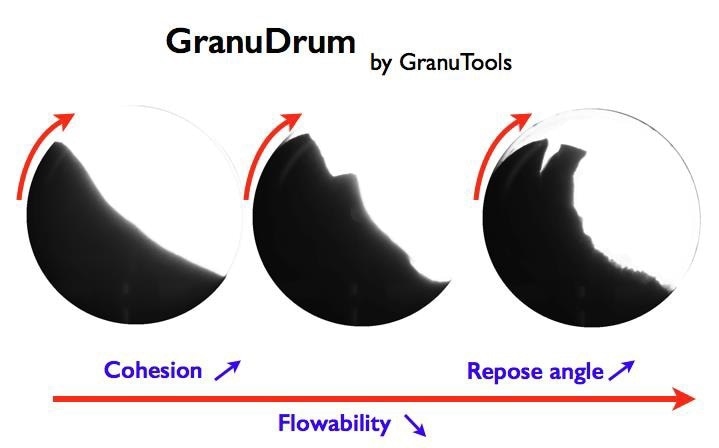
Apart from measuring both the flowing angle αf and the cohesive index σf as a function of the rotating speed, GranuDrum enables the powder aeration and the first avalanche angle to be measured during the flow.
GranuPack
The tapped density, the bulk density, and the measurement of Hausner ratio (usually referred to as “taptap test”) are the most preferred for powder characterization due to not just the simplicity but also the rapidity of the measurement. Furthermore, the density and the potential of a powder to increase its density are crucial parameters for transportation, storage, caking, and so on. The recommended procedure is specified in the pharmacopeia.
There are three main disadvantages to this simple test. First, the measurement result is dependent on the operator. In fact, the filling technique has an impact on the initial volume of the powder. Next, strong errors are induced on the results by naked-eye volume measurements. Finally, this simple technique completely misses out the compaction dynamics between the initial and final measurements.
Granutools’ GranuPack instrument employs an improved and automated tapped density measurement technique that is based on the latest fundamental research results. The behavior of the powder subjected to consecutive taps is analyzed using an automated device. It is possible to precisely measure the initial density ρ(0), the final density after n taps ρ(n), and the Hausner ratio Hr. In general, the tap number is fixed at n = 500. Furthermore, an extrapolation of the maximum density ρ(∞) and a dynamical parameter n1/2 are derived from compaction curves. Although it is feasible to use additional indexes, they have not been discussed in this article.
A stringent automated initialization process is followed for placing the powder in a metallic tube. Then, the powder/air interface is maintained flat during the compaction process by placing a light hollow cylinder on the top of the powder bed. The tube that holds the powder sample rises up to a specified height of ΔZ and performs free falls. Normally, the free fall height is fixed at ΔZ = 1 or 3 mm. The powder bed height, h, is automatically measured following each tap. The volume V of the pile is calculated from the height h.
As the mass m of the powder sample is known, the density ρ is measured and plotted following each tap, where the density is the ratio between the volume V and the mass m of the powder bed. The GranuPack technique provides reproducible results even with a small quantity of powder (usually 35 mL). The Hausner ratio Hr is related to the compaction ratio and is computed by using the equation Hr = ρ(500)/ρ(0). Here, ρ(0) is the initial bulk density and ρ(500) is the calculated tapped density obtained after 500 taps.
GranuCharge
During a flow, electrostatic charges are produced within a powder. The triboelectric effect — a charge exchange at the contact between two solids — causes this apparition of electric charges. When a powder flows inside a device (silo, mixer, conveyor, and so on), the triboelectric effect occurs at the contact between the device and the grains and also at the contact between the grains. Therefore, the powder characteristics and the nature of the material used to construct the device are crucial parameters.
GranuCharge instrument measures the amount of electrostatic charges produced within a powder during a flow in contact with a chosen material in a precise and automatic manner.
The powder sample flows inside a vibrating V-tube and fall in a Faraday cup connected to an electrometer. The charge that the powder acquires during the flow within the V-tube is measured by the electrometer. Reproducible results are achieved by using a vibrating or rotating device to regularly feed the V-tube.
Selected Powders
During this study, a polyamide 12 (PA12) powder sample provided by Materialise (Leuven, Belgium) was selected:
- An SLS powder grades Polyamide 2200 (PA12) produced by EOS (Krailling, Deutschland)
The PA12 is analyzed in its virgin, recycled form. A mix of PA12 virgin and recycled (50% of sieved virgin and sieved recycled) will be also analyzed.
Listed below are all the available data related to the PA12 Virgin:
- Average sphericity of 0.86
- Percentage of particles that have a diameter <10 µm: 2.5%–5.0%
- (D90–D10)/D50: 0.7–1.1
- D50: 50–62 µm
Thanks to the wide thermal processing window (between crystallization and melting peaks) of the polyamide material, it is less sensitive to thermal fluctuations that occur at the time of processing. It is possible to process the virgin material with the required attention (tendency to curl/warp upon being solidified), where the material offers excellent part properties with respect to mechanical resistance and porosity. Once the material is recycled, it can be easily processed (less warpage) but exhibits unsatisfactory properties (fundamentally).
Therefore, based on the particular grade of PA12, it is essential to produce a mix of used and virgin material. The mix is based on the degree of aging and offers a trade-off between exhibiting excellent final part properties and being well processable. Hence, it is somewhat challenging to classify between the materials, but they can be arranged with respect to ease of process, from best to worst, as follows: Recycled — Mixed — Virgin. They can be arranged according to final part properties, from best to worst, as follows: Virgin — Mixed — Recycled.

Figure 1. EOS Virgin PA12, medium magnification (S. Berretta et al.)
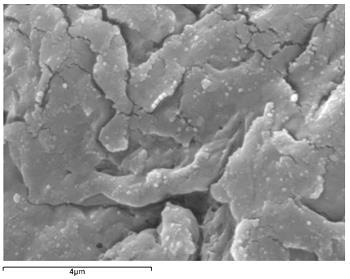
Figure 2. EOS Virgin PA12, high magnification (S. Berretta et al.)
GranuPack Analysis
Experimental Protocol
Each experiment using the GranuPack involved applying 500 taps to the sample with a tap frequency of 1 Hz and the measurement cell free-fall was 1 mm (∝ tap energy). Prior to an experiment, hygrometry and air temperature are recorded. Certain samples were investigated twice. The main aim is to establish the GranuPack instrument’s high accuracy and to stress the aging of powders and its effect on their flowability.
Experimental Data
Prior to each experiment, the powder mass is recorded. The software instructions are followed (i.e. without user dependency) for pouring the sample into the measurement cell. Bulk densities of the powders were analyzed under the same moisture conditions (40% RH and 20 °C).
The full compaction curves, that is, the variations in bulk density (ρ(n) − ρ(0)) versus the number of taps, for polyamide 2200 are illustrated in Figure 3. Although the error bars are displayed, they are too small to be seen (bulk density error is approximately 0.4%).
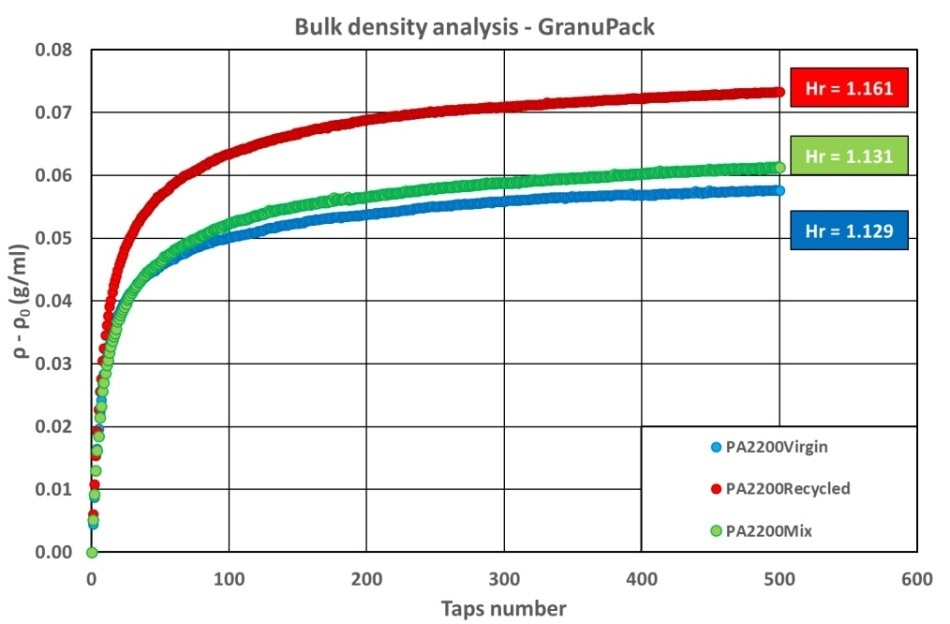
Figure 3. Bulk density versus tap number for polyamide 2200 powders.
Table 1 gives the complete results, where ρ(0) is the initial bulk density in g/mL and ρ(500) is the bulk density following 500 taps, in g/mL. The optimal bulk density, ρ(∞) (in g/mL), is calculated by using a model available in the GranuPack software and estimates the minimum density that can be achieved through the tapping test. Cr and Hr are the Carr and Hausner ratios, and n1/2 and τ are two parameters associated with the compaction (cf. Appendix 1).
Table 1. GranuPack results - comparison between all powders
Sample |
ρ(0) (g/mL) |
ρ(500) (g/mL) |
n½ |
Hr |
Cr |
ρ(∞) (g/mL) |
τ |
PA 12 Virgin |
0.445 |
0.503 |
9.2 |
1.129 |
11.4 |
0.518 |
10.7 |
PA 12 Mix |
0.467 |
0.528 |
12.0 |
1.131 |
11.6 |
0.546 |
14.8 |
PA 12 Recycled |
0.456 |
0.530 |
11.4 |
1.161 |
13.8 |
0.549 |
12.9 |
Results Interpretation
From Table 1 and Figure 3, it can be observed that the GranuPack instrument differentiates between all the powders with exceptional accuracy.
In relation to initial bulk densities, it can be observed that the PA12 Mix is the heaviest sample with a bulk density of approximately 0.467 g/cm3, and the Recycled powder takes the second place with a bulk density of 0.456 g/cm3. Lastly, the lightest of all is the virgin powder, with a bulk density of approximately 0.445 g/cm3. The SLS process can offer a better explanation for the difference between the recycled and virgin powder; in fact, the post-condensation mechanism can result in an increase in molecular weight and might also modify the shape of the unused polyamide 12 powder and the particle size distribution, and hence, can result in a higher bulk density. Furthermore, the sieving process, which preserves the small particles, could be the reason behind the high density of the recycled and mixed PA12.
Following the compaction process, the tapped density of the virgin powder is the lowest (0.503 g/cm3), whereas the mixed and recycled powders achieved a comparable final density (approximately 0.530 g/cm3). These differences are connected to the flowability of the powder, highlighted by the Hausner ratio (equal to final density divided by the initial one). In fact, it can be observed that virgin powder has the highest flowability (Hr = 1.129), whereas the recycled sample has the lowest flowability (Hr = 1.161).
In relation to the compaction dynamic (n1/2 parameter), it can be concluded that the compaction is more rapid for the virgin sample (n1/2 = 9.2) when compared to the other samples (n1/2 of approximately 12.0).
GranuDrum Analysis
Experimental Protocol
In order to perform an experiment using the GranuDrum, powders were poured into the measuring cell immediately after opening the box. The amount of powder used was roughly 50 mL. Each powder sample was investigated under standard conditions (20 °C and 40% RH). In total, 20 GranuDrum velocities were investigated (from 2 to 60 rpm), and for each velocity, 50 pictures were captured to improve the repeatability/accuracy of measurement.
Experimental Results
The cohesive index and the dynamic angle of repose as a function of the rotating speed of GranuDrum are illustrated in Figures 4 and 5. All the measurements presented were carried out by increasing the speed of the drum. The dynamic angle of repose quantifies the flowability of the powder (it takes the three cohesive forces — electrostatic, van der Waals, and capillary — into consideration, as well as the contact forces between grains). The cohesive index is connected to the fluctuations of the interface (air/powder) position, and it represents only the three contact forces. Therefore, the flowability of the powder is characterized by the dynamic angle of repose, while its spreadability is quantified by the cohesive index.
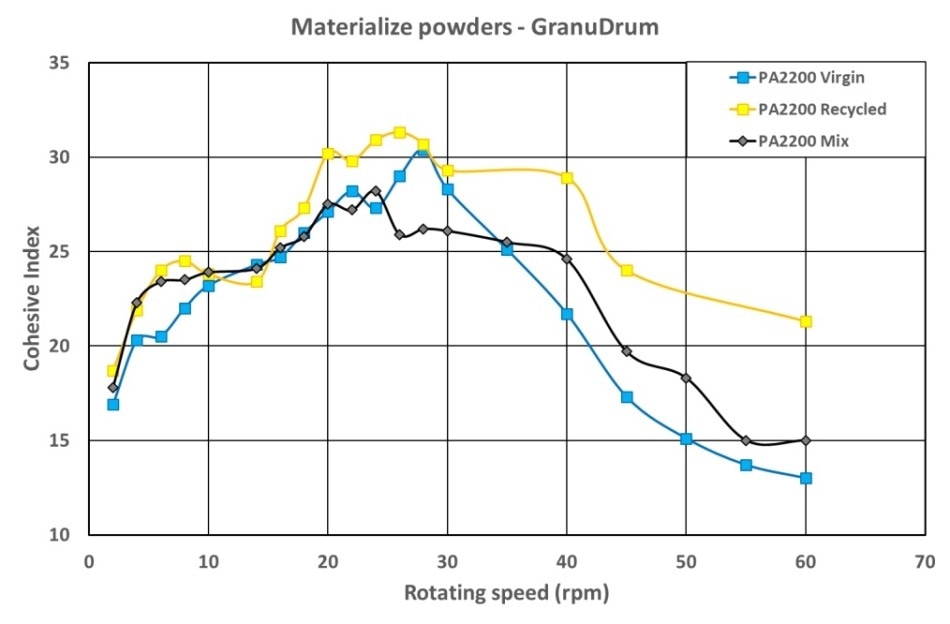
Figure 4. Cohesive index versus rotating drum speed for PA12 powders—increasing velocity.
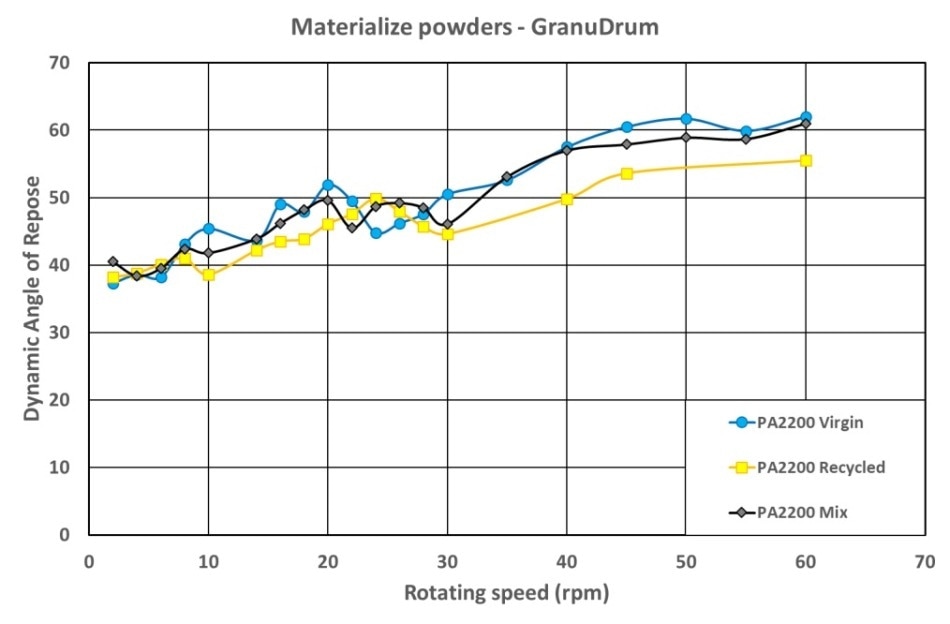
Figure 5. Dynamic angle of repose versus rotating drum speed for PA12 powders—increasing velocities.
Discussion
Regrettably, similar flowing behaviors of powders (cf. the corresponding Hausner ratio) hamper the ability of the GranuDrum to highlight the difference between the powders (with the dynamic angle of repose). However, a look at the low dynamic angle of repose (of 38°–60°) and the low cohesive index (of 13–32) suggests that the spreadability and flowability of the powders for a recoater process are excellent (G. Yablokova et al., 2015).
However, its original image treatment algorithm, that is, the cohesive index, enables achieving the powder classification. In fact, for high velocities (more than 30 rpm, 125 mm/second; see Appendix 2 for speed conversion), the recycled powder exhibits the lowest spreadability for all samples, followed by the mixed powders. Lastly, the virgin powder will be ideal for a recoater process (more than 125 mm/second).
The Materialise company noticed that the most challenging of all to process was the virgin powder. However, a slight increase in their process (to more than 40 rpm, that is, 170 mm/second) led to an increase in the spreadability of the powder, thus making the recoater process easier.
GranuCharge Analysis
Experimental Protocol
The GranuCharge instrument was used for analyzing the triboelectric effect of the powders. A rotating feeder and stainless-steel 316L pipes were used for each experiment with the GranuCharge (cf. Figure 6).
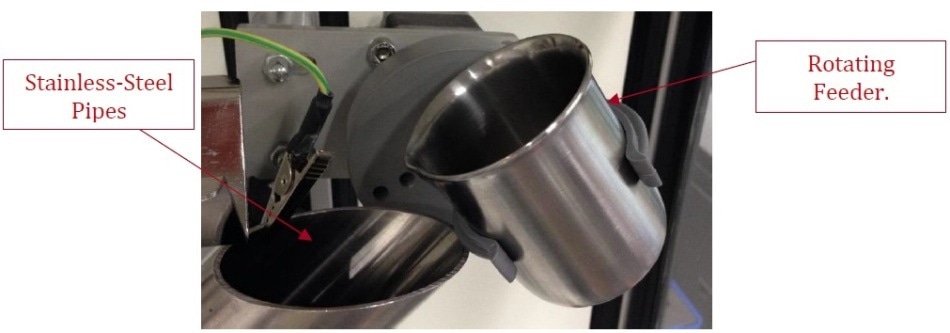
Figure 6. Photography of the rotating feeder used during the tests.
The amount of powder used for every measurement was 50 mL, and the powder was not reused following a measurement. Tests were repeated three times and the average value was plotted. All the powder samples were investigated under standard conditions of 20 °C and 40% RH.
At the start of the test, the powder is introduced into the Faraday cup to measure the initial powder charge density (qi, in nC/g). Upon completing this step, the powder is filled into the rotating feeder, and the experiment is started after that. The final charge density is evaluated at the end of the experiment (qf, nC/g).
All the results achieved using the GranuCharge instrument are summarized in Table 2. Each value of the charge density corresponds to the average value computed between the two tests. ∆q = qfMean − q0Mean, in µC/kg).
Table 2. Synthesis of the results obtained with the GranuCharge instrument
Sample name |
q0 (nC/g) |
qf (nC/g) |
qf - q0 (nC/g) |
PA 12 Virgin |
0.058 |
-2.353 |
-2.411 |
PA 12 Recycled |
0.219 |
-0.416 |
-0.635 |
PA 12 Mix |
0.107 |
-0.590 |
-0.697 |
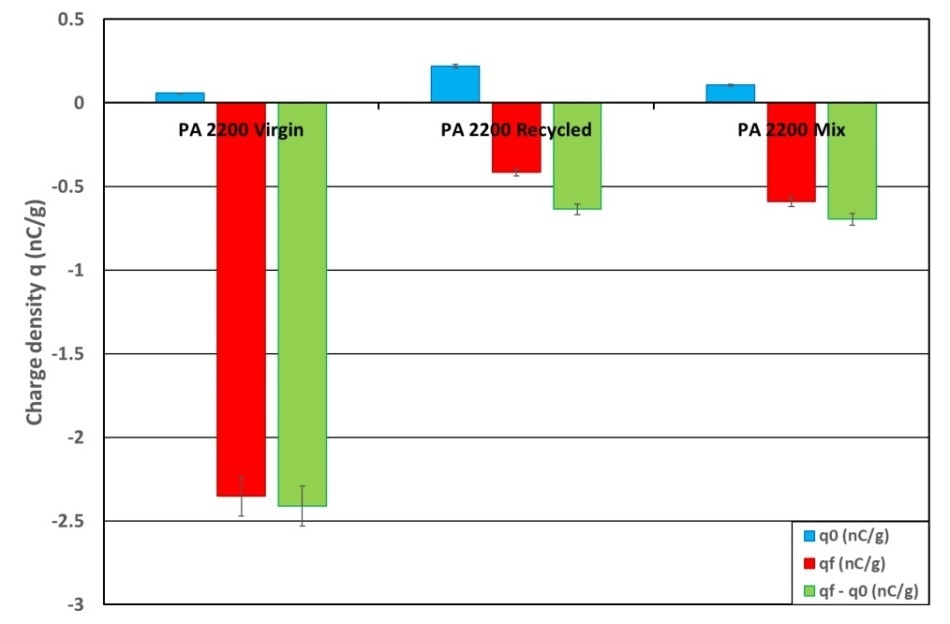
Figure 7. Histogram of the comparison between the initial and final charge densities for PA12 powders.
Results Interpretation
Figure 7 is fascinating since it demonstrates that the GranuCharge instrument can be used to differentiate between powders with excellent accuracy (4%). It is observed that even the initial charge densities are considerably different from one powder to the other. In fact, the virgin powder exhibits the lowest initial charge density of 0.06 nC/g), whereas the recycled sample exhibits the highest initial charge density of 0.219 nC/g. In the case of the mixed sample, the charge density value is midway between that of the other PA12 powders (0.107 nC/g). Furthermore, since each initial charge density value is positive, all the PA12 powders analyzed are cationic.
Following a flow in contact with stainless-steel 316L pipes, the electrical charges produced by the powders are negative. At the end of experiment, the virgin powder appears to be the most charged, with qf = −2.353 nC/g, the recycled powder is the least charged (with qf = −0.416 nC/g), and the mixed sample exhibits a charge in between (qf = −0.590nC/g). The differences can be explained by various factors, such as the surface properties/oxidation (for particles in close contact with a laser in SLS process), the particle size distribution (specifically since the recycled and mixed powders were sieved), and the water adsorption abilities that can vary from one powder to another (a fortiori in case the surface properties are different).
Eventually, it can be observed that the virgin powder’s high sensitivity to accumulate charge will make it stickier and it will probably create agglomerates than other samples. Hence, it may be challenging to achieve its processability.
Conclusions
- It is difficult to highlight the aging of PA12 powders using classical methods (Hall flowmeter, for instance). However, thanks to the high resolution of Granutools’ instruments, it is feasible to quantify the aging of powders.
- The GranuPack instrument is highly sensitive to particle form factors like elliptic smoothness, aspect ratio, and solidity. The GranuPack is also accurate when it comes to analyzing blends (for example, a mix between recycled and virgin powders).
- The combination of GranuCharge and GranuPack experiments quantifies the differences not just between recycled, virgin, and mixed powders but also between powders of similar nature with different thermal histories because of the SLS process.
- The GranuCharge instrument clearly differentiates between the aging states of the powders with excellent accuracy
- The original image treatment algorithm enables the GranuDrum instrument to quantify the differences between the given polyamide samples
- The GranuCharge technique is extremely sensitive to the state of the particles surface such as pollution, oxidation, roughness, etc.
- Further analysis of these systems should allow a reproducible and consistent characterization of powders for AM, the goal of which is to discard powders that are not appropriate for the SLS process anymore
Appendix
Appendix 1: GranuPack Theoretical Background

The dynamical parameter n1/2 corresponds to the number of taps required to achieve one-half of the compaction curve.
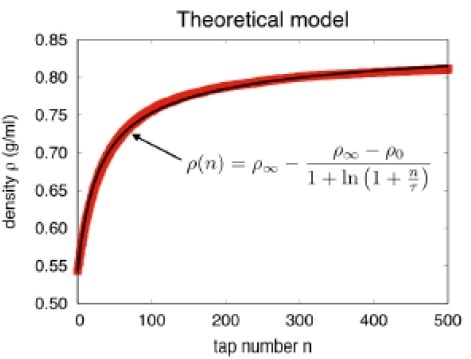
A theoretical model is used to fit the compaction curve to obtain the characteristic tap number τ.
Appendix 2: Relation Between Drum Rotating Speed and Process Speed (in mm/second)
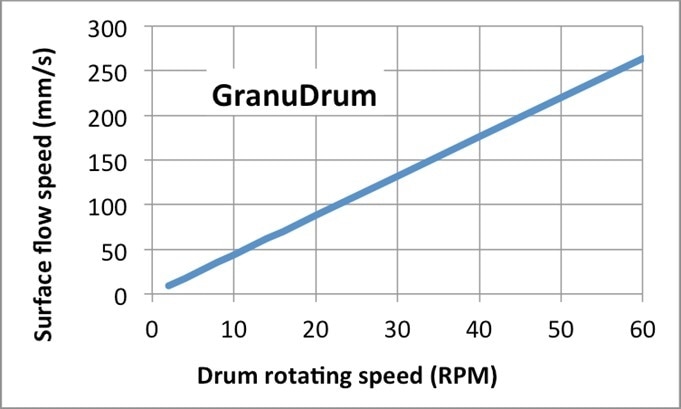
Figure 8. Relation between drum rotating speed and process speed (in mm/second)
Bibliography
- Cascade of granular flows for characterizing segregation, G. Lumay, F. Boschin, R. Cloots, N. Vandewalle, Powder Technology 234, 32-36 (2013).
- Combined effect of moisture and electrostatic charges on powder flow, A. Rescaglio, J. Schockmel, N. Vandewalle and G. Lumay, EPJ Web of Conferences 140, 13009 (2017).
- Compaction dynamics of a magnetized powder, G. Lumay, S. Dorbolo and N. Vandewalle, Physical Review E 80, 041302 (2009).
- Compaction of anisotropic granular materials: Experiments and simulations, G. Lumay and N. Vandewalle, Physical Review E 70, 051314 (2004).
- Compaction Dynamics of Wet Granular Assemblies, J. E. Fiscina, G. Lumay, F. Ludewig and N. Vandewalle, Physical Review Letters 105, 048001 (2010).
- Effect of an electric field on an intermittent granular flow, E. Mersch, G. Lumay, F. Boschini, and N. Vandewalle, Physical Review E 81, 041309 (2010).
- Effect of relative air humidity on the flowability of lactose powders, G. Lumay, K. Traina, F. Boschini, V. Delaval, A. Rescaglio, R. Cloots and N. Vandewalle, Journal of Drug Delivery Science and Technology 35, 207-212 (2016).
- Experimental Study of Granular Compaction Dynamics at Different Scales: Grain Mobility, Hexagonal Domains, and Packing Fraction, G. Lumay and N. Vandewalle, Physical Review Letters 95, 028002 (2005).
- Flow abilities of powders and granular materials evidenced from dynamical tap density measurement, K. Traina, R. Cloots, S. Bontempi, G. Lumay, N. Vandewalle and F. Boschini, Powder Technology, 235, 842-852 (2013).
- Flow of magnetized grains in a rotating drum, G. Lumay and N. Vandewalle, Physical Review E 82, 040301(R) (2010).
- How tribo-electric charges modify powder flowability, A. Rescaglio, J. Schockmel, F. Francqui, N. Vandewalle, and G. Lumay, Annual Transactions of The Nordic Rheology Society 25, 17-21 (2016).
- Influence of cohesives forces on the macroscopic properties of granular assemblies, G. Lumay, J. Fiscina, F. Ludewig and N. Vandewalle, AIP Conference Proceedings 1542, 995 (2013).
- Linking compaction dynamics to the flow properties of powders, G. Lumay, N. Vandewalle, C. Bodson, L. Delattre and O. Gerasimov, Applied Physics Letters 89, 093505 (2006).
- Linking flowability and granulometry of lactose powders, F. Boschini, V. Delaval, K. Traina, N. Vandewalle, and G. Lumay, International Journal of Pharmaceutics 494, 312–320 (2015).
- Measuring the flowing properties of powders and grains, G. Lumay, F. Boschini, K. Traina, S. Bontempi, J.-C. Remy, R. Cloots, and N. Vandewall, Powder Technology 224, 19-27 (2012).
- Motion of carbon nanotubes in a rotating drum: The dynamic angle of repose and a bed behavior diagram, S. L. Pirard, G. Lumay, N. Vandewalle, J-P. Pirard, Chemical Engineering Journal 146, 143-147 (2009).
- Mullite coatings on ceramic substrates: Stabilisation of Al2O3–SiO2 suspensions for spray drying of composite granules suitable for reactive plasma spraying, A. Schrijnemakers, S. André, G. Lumay, N. Vandewalle, F. Boschini, R. Cloots and B. Vertruyen, Journal of the European Ceramic Society 29, 2169–2175 (2009).
- Rheological behavior of β-Ti and NiTi powders produced by atomization for SLM production of open porous orthopedic implants, G. Yablokova, M. Speirs, J. Van Humbeeck, J.-P. Kruth, J. Schrooten, R. Cloots, F. Boschini, G. Lumay, J. Luyten, Powder Technology 283, 199–209 (2015).
- The flow rate of granular materials through an orifice, C. Mankoc, A. Janda, R. Arévalo, J. M. Pastor, I. Zuriguel, A. Garcimartín and D. Maza, Granular Matter 9, p407–414 (2007).
- The influence of grain shape, friction and cohesion on granular compaction dynamics, N. Vandewalle, G. Lumay, O. Gerasimov and F. Ludewig, The European Physical Journal E (2007).
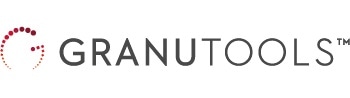
This information has been sourced, reviewed and adapted from materials provided by Granutools.
For more information on this source, please visit Granutools.