Article updated on 17 August 2021
Medical implants are an ideal field for 3D printing, requiring the rapid manufacture of highly intricate and customizable products. Research in additive manufacturing continues to improve the quality of these implants and increases the number of applications 3D printing has in the medical industry.
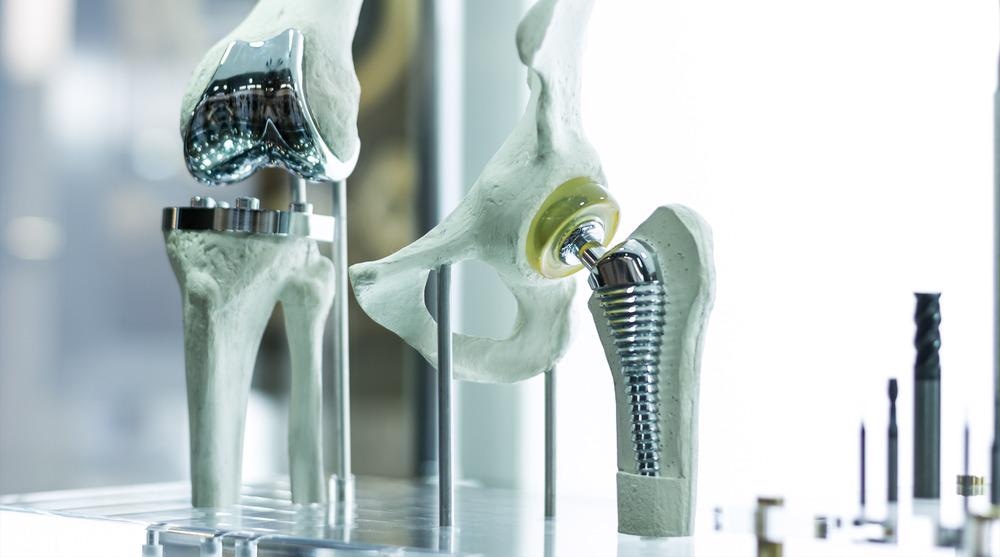
Image Credit: Monstar Studio/Shutterstock.com
Creating medical implants is a difficult process, as it involves the collaboration of multiple intensive and vastly different bodies of research. These products must be analyzed from a medical, biomechanical, and material science perspective.
One of the most difficult issues to overcome in medical implants is biocompatibility. This issue refers to the implant’s ability to behave and perform adequately in the body over long periods of time. Incorrectly manufactured synthetic implants can emit ions, negatively affecting the tissue around the implant, or the immune system can reject the implant as a foreign body altogether. Toxicology, immune system response, and surface treatment are all essential fields to consider when ensuring biocompatibility.
Beyond biological considerations, implants are also difficult to design from a mechanical perspective. Biomechanics of body parts can be vast and complex: single components can vary in properties as small as collagen content and lamellae orientation across their bodies, giving distinct and essential mechanical properties. Joints can move countless cycles for decades with little to no wear. Recreating these biomechanical properties synthetically is incredibly difficult.
3D Printing Medical Implants
The geometry of bones and tissue differs from patient to patient. The nature and extent of the damage that the patient has endured is also entirely unique to them. Because of this, implants must be custom-made and uniquely designed to fit their patient.
In almost all circumstances where small batches of uniquely designed products are manufactured, additive manufacturing becomes the most attractive, cost-effective method. Building complex pieces with intricate internal structures and minute but essential variations is much simpler to manufacture layer by layer, straight from a computer-aided design (CAD) drawing.
Additive manufacturing is not a new concept in the medical implant industry. Knee implants, for example, are 3D-printed from CAD models. These models are extracted from 3D scans of the patient’s knee, which prevents the invasive surgeries that would traditionally take place. 3D printing has been used for other implants across the entire human body for over a decade.
Advancements in 3D printing technologies - from a more expansive range of filament materials to increased precision - mean this manufacturing method is likely to be increasingly implemented for medical implants.
Recent Technological Advancements in 3D Printed Implants: Nitinol Arterial Stents
Advancements in materials 3D printing - made as recently as 2020 - have led to monumental strides in the medical field.
Research at the Australian government’s scientific research agency CSIRO concluded in the past year that Nitinol can be 3D printed, allowing mass production of arterial stents for circulation disease.
Nitinol, a titanium and nickel alloy, is a highly desirable material for peripheral artery disease (PAD) due to its shape memory retaining properties. PAD is caused by fat deposits in the arteries in the legs or arms, causing a reduction in blood flow to the limbs. Stents placed in these defective arteries must be able to deform but retain their shape as the user moves their limbs. Therefore, Nitinol is a beneficial option when creating these stents.
CSIRO research has now concluded that Nitinol stents can be 3D printed. This is a notable advancement in the metallurgy of additive manufacturing (nitinol is rarely used in 3D printing) and an improvement in the geometries of these stents. These 3D-printed stents have a complex mesh geometry, allowing them to expand and contract more efficiently than traditional stents.
With this research comes all the benefits of additive manufacturing for PAD sufferers. Arterial stents can be custom-made to the user and manufactured rapidly. Rapid manufacture also leads to wider accessibility of the product.
Manufacturing Methods of 3D Printing and Applications in Medical Implants
To truly understand the potential of 3D printing in the medical industry, it is important to note how expansive the field of 3D printing is. These two previous examples, the arterial stents and the knee implants, are manufactured using one method of 3D printing: powder bed fusion. Other techniques are available, all of which allow different properties to their products.
Powder bed fusion refers to the fusion of substances to form layers of solid material from powder using a heat source such as a laser. The powder is then placed on the previously fused cross-section, and the process is repeated, building the product up layer by layer.
This process is one of the most widely used, as it allows for precise and complex structures to be made easily. In the case of the electron beam, the precision of this method is in the range of a few microns. The process also allows for a wide range of materials to be used.
There are downsides to this method, however. Like all additive manufacturing methods, powder bed fusion creates products with rough surfaces, requiring treatment to smooth them. This can be an issue with delicate components. Furthermore, using lasers in powder bed fusion can lead to crack propagation due to small fluctuations in temperature. Finally, some powders may be hard to source. The nitinol stents are an example of this as the nitinol powder has to be custom-made.
The other most common method for 3D printing is extrusion. Material extrusion, rather than melting a sheet of powder, will have the powder (or filament) in a specialized nozzle. This nozzle, which can move across all 3 axes, heats and feeds the material onto a hotbed, forming the layers of the product. Extrusion printers are what most people think of when they hear “3D printing”.
Material extrusion is more cost-effective than powder bed fusion and has less waste. However, it suffers the same issues of rough surfaces and is unable to compete with powder bed fusion’s precision when it comes to certain biological factors. For example, powder bed fusion has been shown to efficiently mimic the porosity of human bone. These minuscule pores are essential in recreating the mechanical properties of biological material and are a circumstance in which powder bed fusion overcomes material extrusion methods.
3D printing is essential to the advancement of medical implants, and a mixture of these two main manufacturing techniques should be implemented to continue this. As the technology develops, so too do the possible applications for this printing method.
References and Further Reading
Badylak, S. F. (Ed.). (2015). Host response to biomaterials: the impact of host response on biomaterial selection. Academic Press.
Attarilar, S., Ebrahimi, M., Djavanroodi, F., Fu, Y., Wang, L. and Yang, J., (2020). 3D Printing Technologies in Metallic Implants: A Thematic Review on the Techniques and Procedures. International Journal of Bioprinting, 7(1). https://doi.org/10.18063/ijb.v7i1.306
Hendrixson, S., (2020). 3D Printed Nitinol Opens New Possibilities for Arterial Stents. [online] Additivemanufacturing.media. Available at: https://www.additivemanufacturing.media/articles/3d-printed-nitinol-opens-new-possibilities-for-arterial-stents (Accessed 22 June 2021).
Hendrixson, S., (2020). 4 Ways 3D Printing Is Changing Medical Implants. [online] Mmsonline.com. Available at: https://www.mmsonline.com/articles/4-ways-3d-printing-is-changing-medical-implants (Accessed 20 June 2021).
Disclaimer: The views expressed here are those of the author expressed in their private capacity and do not necessarily represent the views of AZoM.com Limited T/A AZoNetwork the owner and operator of this website. This disclaimer forms part of the Terms and conditions of use of this website.