Within the food industry, it is important to have a reasonable packaging size – not only to guarantee the success of the packaging process but also to reduce the cost of transporting products. This article explores how measuring the bulk density and tapped density determines the size of the food powder container.
This research displays how an automatic tapped density tester – The BeDensi T1 Pro – was used to analyze three types of protein powders, including whey protein, soy protein and whey-soy protein mixture.
The conclusion of this research underlines how much the instrument in question relies wholly on food manufacturers being provided with reliable information in order to determine the ideal packing size, along with a suitable choice of container for the customer’s needs.
Most food industries operating today handle particulate food, which takes the form of various powders made from ingredients. These powders can range from sugars, spices and flours to end products like instant coffee and protein powder.1
It is important that great care is taken during the handling process in every aspect of production, including packaging, storage, transportation and distribution.
A direct and important role is played by bulk properties, such as the bulk density and tapped density, within food packaging.2 Bulk density is defined as the ratio of the mass to the volume of a loose powder, whilst tapped density is defined as the ratio of the mass to the volume of powders tapped for a defined period.
The tapping process, in effect, simulates the vibration that all powders experience from production to distribution. As Figure 1 demonstrates, the interstitial space between the particle is clearly included.3 The amount of interstitial air is reduced after tapping is generated during storage and transit, which reduces the volume.
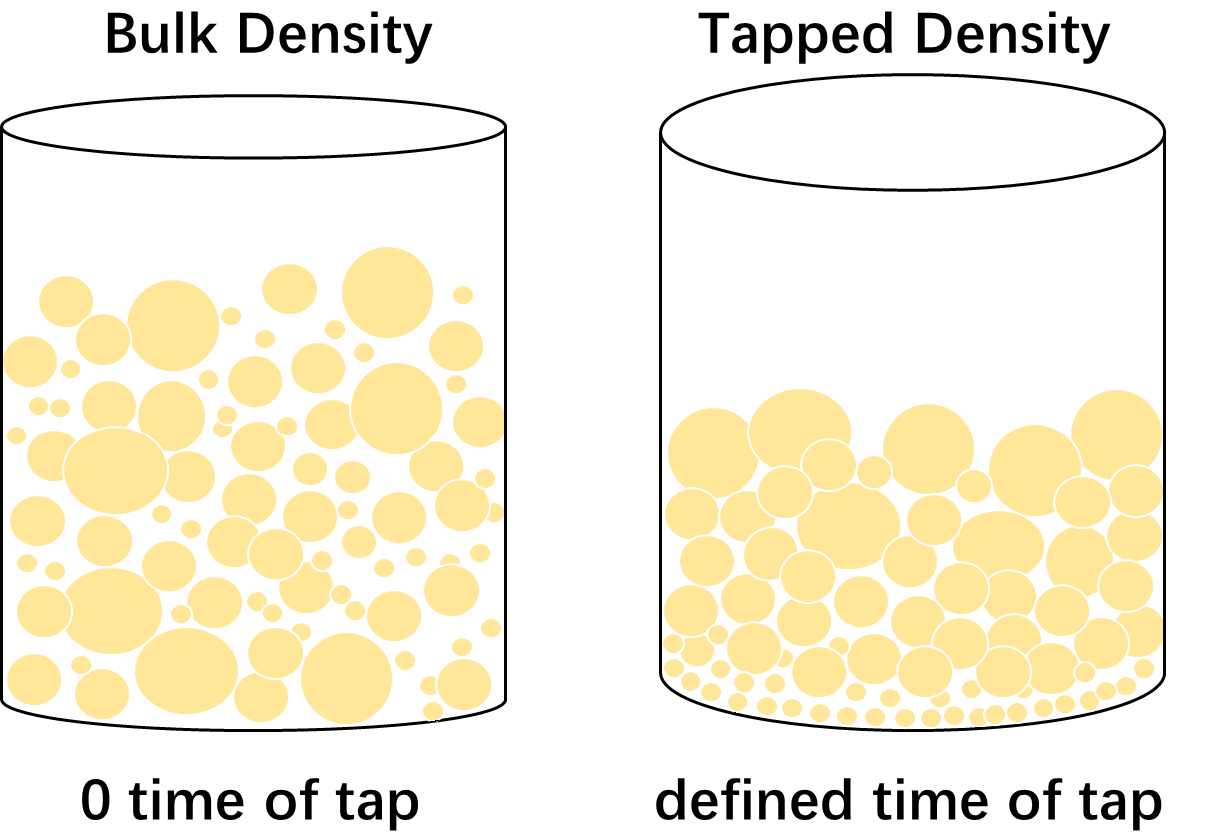
Figure 1. Comparison of bulk density and tapped density. Image Credit: Bettersize Instruments Ltd.
Powders are initially packed in a bulk container or bag and, after distribution in the shops, are subsequently transported over a long distance for consumption. To establish the optimized size of powder packaging containers, the density of the powders is an important parameter to establish.
When it comes to light bulk density powders, for example, removing air from the product during and after filling is an effective method for designing a more compact packaging. The optimum packaging size can therefore be calculated accurately by confirming the tapped density and the bulk density and is highly significant in the economics of transporting powder.
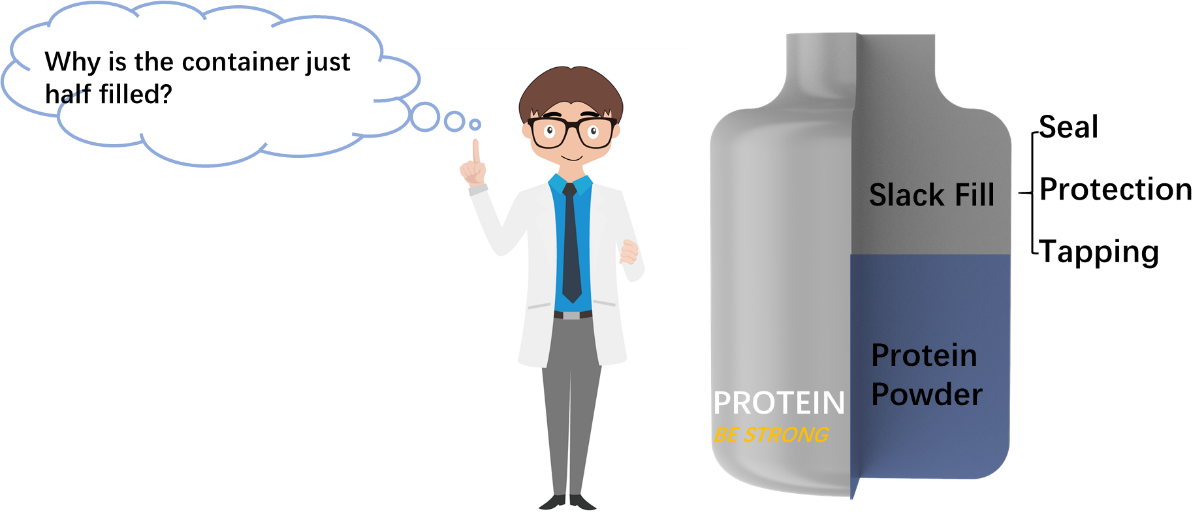
Figure 2. A protein powder container with slack-fill. Image Credit: Bettersize Instruments Ltd.
It is also essential to ensure that there is a correct fill volume in each consumer pack.4 Fill volumes with too much void space in the container on opening, or which are otherwise unreasonable, are unlikely to meet the customer’s standards and could even lead to accusations of misleading the customer based on the Federal Food Drug & Cosmetic Act (FDCA).5
For example, within the protein packaging industry, there exists an interesting phenomenon that protein powder containers are typically not filled to their full capacity, which is caused by something known as slack-fill.
Slack-fill is defined as the difference between the true capacity of a container and the volume of product inside it. The slack-fill covers the appropriate volume of material for the appropriate sealing and protection of the product and is caused by vibration of the powder throughout shipping and storage.
When the products arrive on supermarket shelves, it is possible that there might appear to be excessive empty space inside because of this tapping.
Therefore, it is necessary to determine the tapped and bulk densities of protein powders so that factories can improve upon the current disparity between the slack-fill and a container’s actual capacity. This article explores defining the tapped densities of different protein powders to achieve optimal and customer-friendly packing sizes for the manufacturers.
Method
The whey protein and soy protein were purchased in a local supermarket in Shenzhen, China. The whey-soy protein was created by mixing the soy protein and the whey protein powders. The tapping conditions need to be quoted in order to make density results meaningful.
The BeDensi T1 Pro was used to perform the tapping test in accordance with the ISO standards.6,7 A 250 ml graduated cylinder with 50 g sample was tapped at room temperature 625 times using the tapped density tester. The measured density was obtained by the given formula below:
ρx = m/Vx
Where x is the number of taps, ρ is the density, m is the mass, V is the volume. ρ0 and ρ625 are the measured density, in grams per milliliter, after transfer and after 625 taps, respectively.
To establish the appropriate container size, three different slack-fill containers (10, 20, and 30 vol%) were filled with 500 g of whey protein powder before the tapping process commenced. Feedback from 20 Bettersize colleagues on the different size containers colleagues was collected after tapping 625 times.
Result
Pure Protein
This process obtained the tapped densities of soy protein powder and pure whey protein powder. As Table 1 displays, both ρ625 and ρ0 of soy protein are larger than whey protein. This means that a smaller container is more appropriate for the packing of pure soy protein.
Table 1. The densities of pure protein powders. Source: Bettersize Instruments Ltd.
Protein |
ρ0 |
ρ625 |
(g/ml) |
Whey |
0.33 |
0.50 |
Soy |
0.42 |
0.59 |
Mixed Protein
The automatic tapped density tester was also used to measure the tapped density of mixed whey-soy protein powders. Table 2 presents the various densities of mixed protein with 25, 50 and 75 wt.% whey proteins, wherein the soy protein tapped density increases accordingly with the mass fraction of whey protein.
Table 2. The densities of mixed whey-soy protein with different fractions. Source: Bettersize Instruments Ltd.
Protein |
ρ0 |
ρ625 |
(g/ml) |
Whey-soy (3:1) |
0.33 |
0.54 |
Whey-soy (1:1) |
0.39 |
0.57 |
Whey-soy (1:3) |
0.41 |
0.59 |
When it comes to storing different protein products, it is necessary to establish applicable bags or containers.
In addition, the measured tapped densities slightly exceed the calculated tapped densities founded on the mass weight of the two powders, as evidenced by Figure 3. The calculated values were obtained by the equation below:

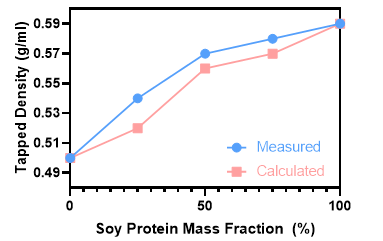
Figure 3. The measured and calculated tapped densities of the protein mixtures. Image Credit: Bettersize Instruments Ltd.
Discussion
The process was undertaken successfully, and the bulk density and tapped density of three different types of protein powders were measured accurately. The results from each of the powders could determine the appropriate container size for each of the powders.
In addition, the appropriate slack-fill percentage was investigated for customer satisfaction. In order to do this, the packaging of 500 g whey protein powder was simulated with different slack-fill volumes and different container sizes.
Where the calculated tapped density of the mixture is ρmix, the mass fraction is ω.
As explored earlier in this article regarding tapping and transportation, small particles can displace the air between the larger particles. This displacement reduces the volume and increases the density.
Calculating the tapped density with a simple model of component properties is not an appropriate method to calculate the tapped density of protein powder mixture, given that the density is also affected by particle shape, distribution and size and surface structure.8 As a result, manufacturers require a standard tapped density tester for them to be able to scientifically and accurately study the tapped density of the powders.
The slack-fill volumes of the loose and tapped products packed in different volume containers are shown in Table 3.
Table 3. The slack-fill volume changes in loose and tapped product. Source: Bettersize Instruments Ltd.
Container
Volume (ml) |
500 g Loose Protein Powder |
500 g Tapped Protein Powder |
Customer Emotion |
Volume (ml) |
Slack Fill (vol%) |
Volume (ml) |
Slack Fill (vol%) |
1683 |
1515 |
10 |
1000 |
41 |
 |
1893 |
20 |
47 |
 |
2164 |
30 |
54 |
 |
The schematic of slack-fill changes of the simulated sample is shown in Figure 4 in order to facilitate understanding of the change.
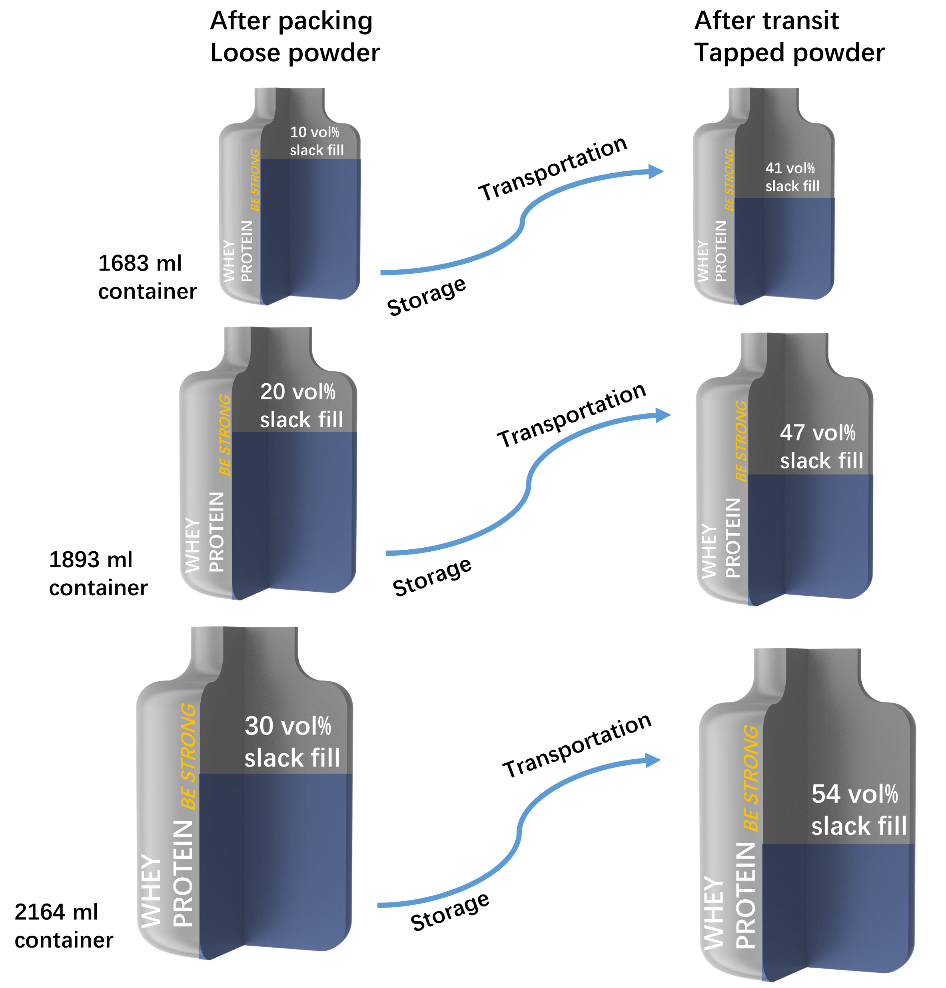
Figure 4. The slack-fill changes of the simulated sample during storage and transportation. Image Credit: Bettersize Instruments Ltd.
The slack-fill percentage increased after transit due to a rise in tapped density. For instance, there is a marked increase of 30 vol% of slack-fill percentage in the loose product to 54 vol% in the tapped product. The slack-fill percentage increases with the packaging size: so, the larger the packaging size, the higher the slack-fill percentage.
As evidenced by the feedback, the majority of Bettersize employees were dissatisfied with the 30 vol% initial slack-fill (as presented in Table 3).
In this instance, a protein container with a 30 vol% slack-fill will have a tapped slack-fill of over 50 vol%, which would be contrary to a customer’s expectations. Equally, customers are likely to have a higher degree of satisfaction if the slack-fill is less than 20 vol%. This research suggests that controlling the initial slack-fill to less than 20 vol% can achieve a reasonable packing size.
Conclusion
The BeDensi T1 Pro was successfully used to measure the tapped density of the pure and mixed protein powders. Different types of protein powders have different tapped densities, so the packing sizes need to be confirmed on the premise of the density when it comes to pure protein powder.
The tapped density is different thanks to the change of mass ratio in the protein mixture. Rather than using a simple model of component properties, the tapped density should be measured by a standard tapped density tester. A reasonable packing size for the whey protein product can be achieved under a 20 vol% initial slack-fill, based on the tapped testing results.
Thus, a standard tapped density tester is an absolute necessity for all manufacturers who wish to study the tapped density of the powder accurately and, from this information, design appropriately sized packaging.
The BeDensi T Pro series can provide food powder producers with reliable information to determine an optimum packing volume which will be useful in determining a packaging that is eye-catching, fit for purpose and customer-friendly.
References
- Pablo J., Guatavo V. (2010). Food Powder Flowability Characterization: Theory, Method, and Applications. Annual Review of Food Science and Technology, 1(1), pp. 211-239
- Malave, J., Barbos-Canovas, G.V. and Peleg, M. (1985). Comparison of the Compaction Characteristics of Selected Food Powders by Vibration, Tapping and Mechanical Compression. Journal of Food Science, 50, pp. 1473-1476
- Merkus H. (2009). Particle Size Measurements: Fundamentals, Practice, Quality. 1st ed. The Netherlands: Springer.
- Onwulata C. (2005). Encapsulated and Powdered foods. 1st ed. Boca Raton: CRC Press 4
- Federal Food Drug & Cosmetic Act (FDCA) Section 403(d) (21 U.S.C. 343(d)).
- ISO8967/IDF134 Dried milk and dried milk products – Determination of bulk density.
- Lin R, Wang Y., Selomulya C. (2022) Physical Properties of Dairy Powders. Encyclopedia of Dairy Sciences. pp. 504-520
- Merkus, H., Meesters G. (2014) Particulate Products: Tailoring Properties for Optimal Performance. 1st ed. Netherlands: Springer.
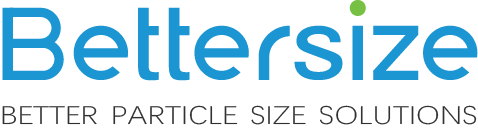
This information has been sourced, reviewed and adapted from materials provided by Bettersize Instruments Ltd.
For more information on this source, please visit Bettersize Instruments Ltd.
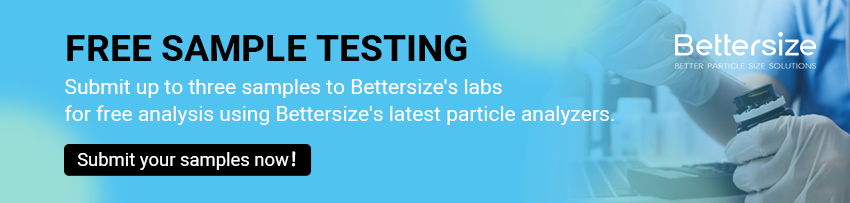