Under specific conditions, hydrogen can diffuse in metal, leaving a long-term effect on the material’s properties. Close investigation of the behavior of materials and components in hydrogen-rich environments must therefore be conducted at varying temperatures, pressures, and oscillating load. ZwickRoell supplies various versions of servohydraulic testing machines that effectively meet these requirements.
Hydrogen is considered the future energy carrier. Developing advanced storage and distribution systems with high energy density potential is vital to ensure it is used efficiently.
Part of this development requires thorough investigations of hydrogen’s impact on metallic materials. Metals become brittle when directly exposed to hydrogen, reducing ductility and elongation at break. This may lead to sudden brittle failure when the material is stressed. Here, materials testing, sometimes at extreme temperatures and pressure, is a significant challenge beyond the capabilities of standard tests.
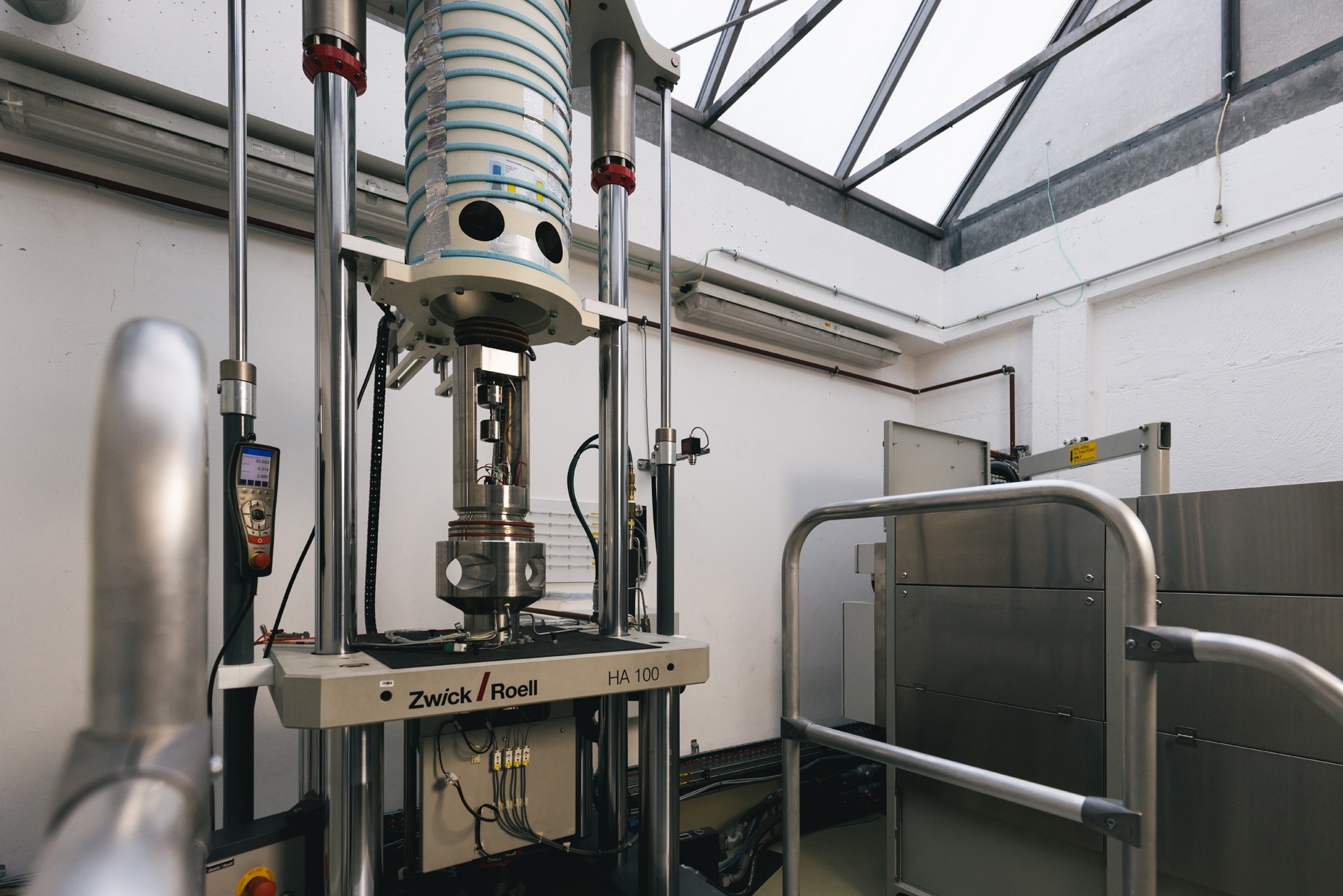
Figure 1. HA 100 servohydraulic testing machine with hydrogen tank. Image Credit: MPA
Servohydraulic Testing Machine with a Compressed Hydrogen Tank
Specializing in research, development, manufacturing, and implementation of pipeline inspection solutions, the Rosen Group is constructing its first hydrogen testing laboratory in Lingen, Germany.
The laboratory will focus on static tensile tests, fracture mechanics investigations, and slow strain rate tests (SSRT) on CT specimens, threaded-end specimens, and notched threaded-end specimens.
Among other systems, the company uses ZwickRoell’s HA series servohydraulic testing machine with Fmax 100 kN and a compressed hydrogen tank for pressures up to 400 bar. The compressed hydrogen is prepared using a hydrogen compressor.
ZwickRoell supplied the complete testing system, including the hydrogen pressure tank.
The advantage of this complete solution is that the pressure tank is precisely adapted to materials testing requirements and that testing-related parameters such as alignment, force measurement and strain measurement have been taken into account.
Dr. Marion Erdelen-Peppler, head of the hydrogen focus group, Rosen.
Standard versions of the HA series fatigue testing machines in the 50, 100, 250, and 500 kN ranges have the actuator mounted below the test area in the lower crosshead. This makes them well-suited for test arrangements that require temperature chambers or furnace installation in the test area. This prevents heated air from rising and heating the actuator, while oil cannot drip into the heated test area.
The HA series load frames are extremely stiff and are specifically designed for high-cycle fatigue tests and identifying short fatigue life at low vibration cycles.
A material or component is subjected to stress with a periodically changing (cyclic) load during the high cycle fatigue (HCF) test to DIN 50100 / ASTM E466-15 / ISO 1099. The objective is to establish the finite life fatigue strength and high cycle fatigue strength for compression, flexure, tensile, and torsion loading.
Particularly in the case of components, weak points can be eliminated through construction or material alterations. Material fatigue less than 104 to 105 cycles is established using the low cycle fatigue (LCF) test. In this range, materials and components are stressed to the point that plastic deformations appear throughout the cycle, and the material fails at an early stage.
Here, the testing machine and controller face significant challenges. During the transition from elastic to plastic deformation, the stiffness of the specimen changes significantly, and the controller must react rapidly, for instance, to ensure that the adjustment of the speed to the increase in strain remains constant. Here, the exceptionally high stiffness of the testing machine plays a key role.
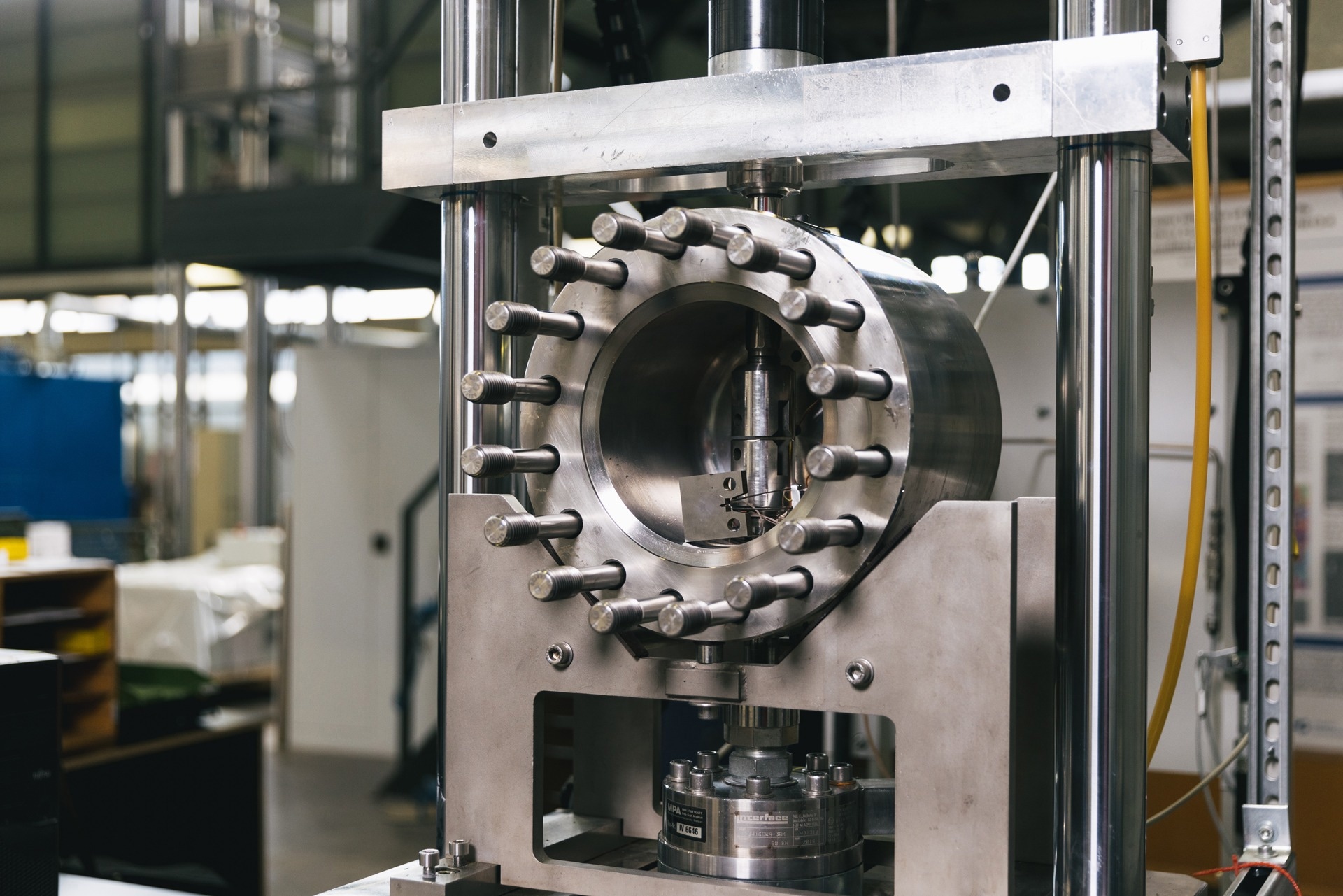
Figure 2. HC Compact 25 servohydraulic testing machine. Image Credit: MPA
Materials Testing Down to -269 °C
The University of Stuttgart’s Materials Testing Institute (MPA), Germany, has many years of extensive experience in this field. The variety of tests conducted include material behavior in compressed hydrogen and liquid hydrogen at temperatures of 563 K down to 4 K, and therefore near to absolute zero.
Tests incorporate deformation and failure behavior, such as crack initiation and propagation under static and oscillating loads.
ZwickRoell employs HA and HC series servohydraulic testing machines with a dynamic nominal force of up to 100 kN to conduct the tests. Compressed hydrogen tanks for pressures up to 400 bar are integrated into the testing machines as standard.
Special versions are also available for up to 1000 bar, and a hydrogen compressor is used to prepare the compressed hydrogen. In addition to conducting other tests, the testing machines evaluate slow strain rate behavior (SSRT), the fracture mechanics on CT specimens, or fatigue properties utilizing notched threaded-end specimens.
The HC Compact series testing machine benefits include confined space compatibility and availability in two versions. The first version with either 10/25 kN was developed for fatigue tests on smaller components and includes a T-slot platform.
The second 50/100 kN version is compatible with static and dynamic tests. The HC series can also be fitted with a temperature chamber with minimal installation effort.
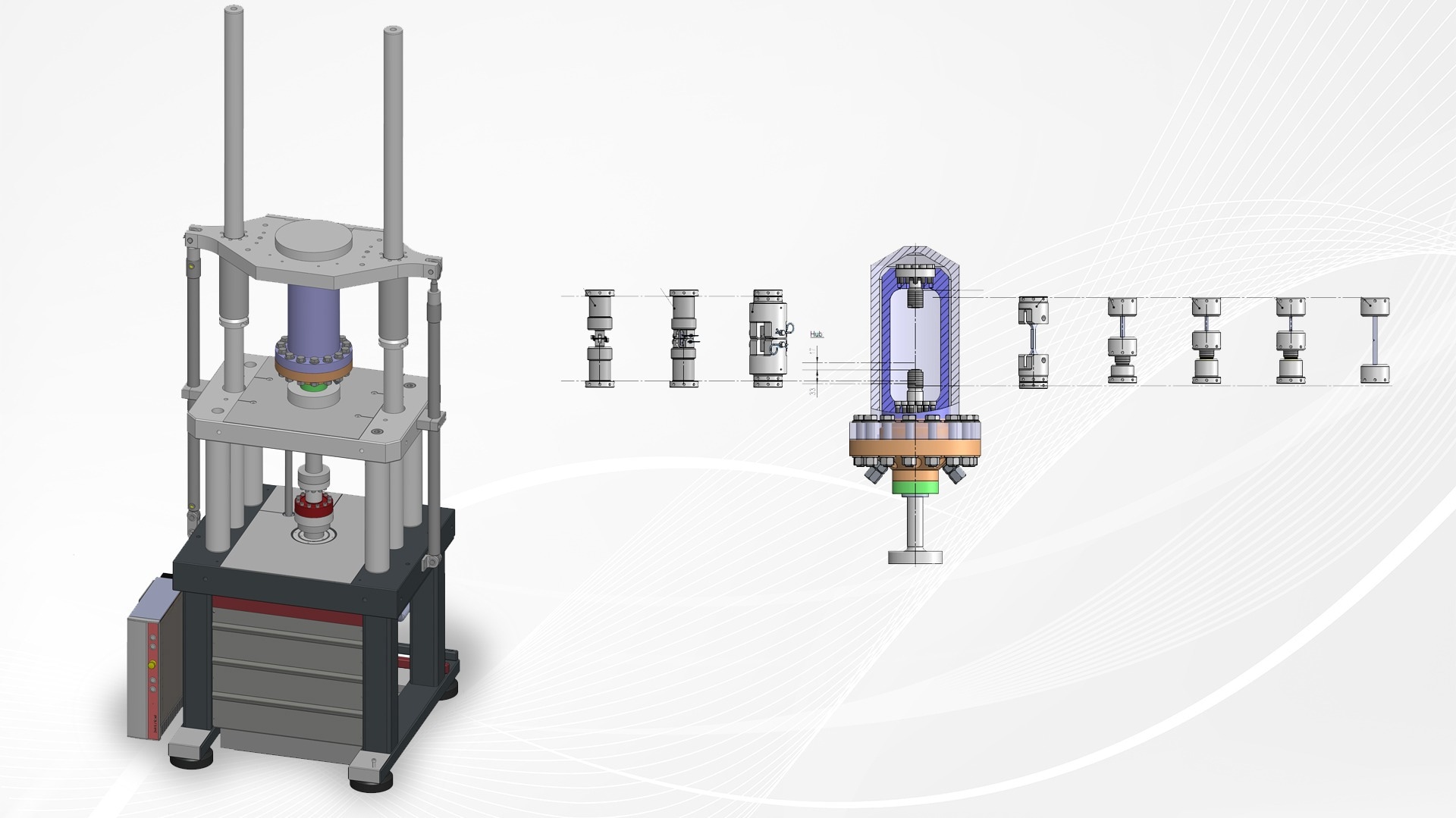
Figure 3. Servohydraulic testing system for various fatigue tests under hydrogen atmosphere. Image Credit: ZwickRoell GmbH Co. KG
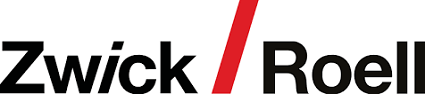
This information has been sourced, reviewed and adapted from materials provided by Zwick GmbH & Co. KG.
For more information on this source, please visit ZwickRoell GmbH Co. KG