The automotive industry is in need of innovative means to improve the performance, efficiency, and sustainability of its products. One of the emerging trends is the use of fiber-reinforced polymer composites (FRPCs) as alternative materials for various components.
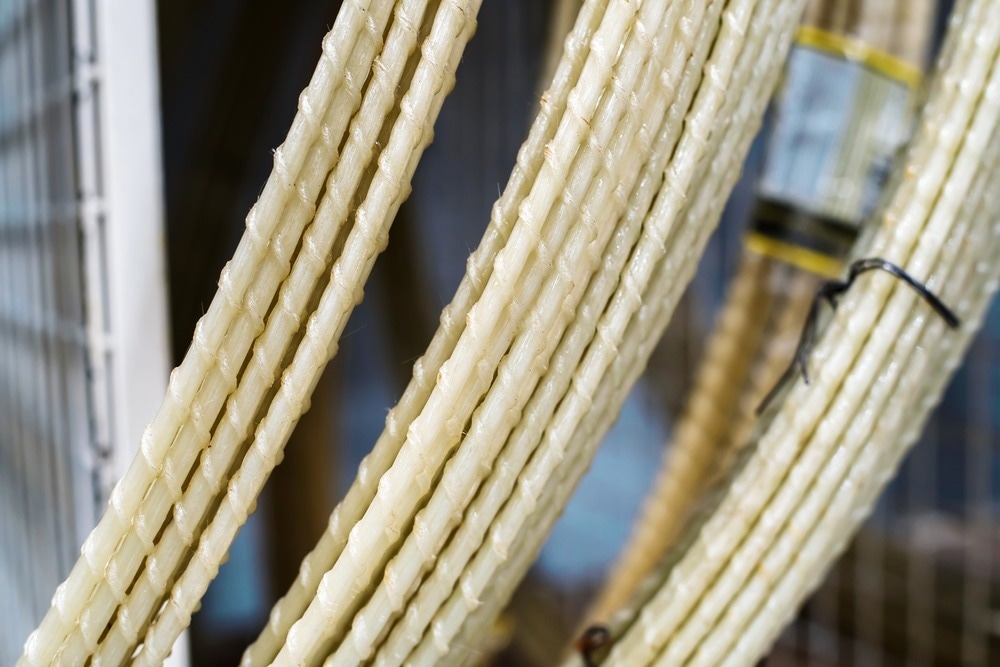
Image Credit: Dmitry Markov152/Shuttesrtock.com
FRPCs are composed of fibers such as glass, carbon, or natural fibers embedded in a polymer matrix, such as thermoplastics or thermosets.
FRPCs provide several advantages more than conventional materials, such as metals and synthetic fibers, in terms of weight reduction, cost reduction, energy saving, environmental friendliness, and recyclability. Nevertheless, FRPCs encounter challenges, including achieving a high-quality surface finish, maintaining mechanical and physical properties under extreme conditions, and ensuring compatibility and integration with other materials and systems.
In this article, we will explore the role of FRPCs in the automotive industry, addressing the current and potential applications, the technical considerations, and the Manufacturing techniques.
Understanding Fiber-Reinforced Polymer Composites
Fiber-reinforced polymer composites (FRPCs) are composite materials that consist of strong fibers embedded in a resin matrix. The fibers provide strength and stiffness to the composite and generally carry most of the applied loads. The matrix acts to bond and protect the fibers and to transfer the stress from fiber to fiber through shear stresses. The most common fibers are glass, carbon, and synthetic fibers. FRPCS are nonconductive, noncorrosive, and lightweight. This synergy between the polymer matrix and reinforcing fibers results in a material that is not only lightweight but also has high strength, stiffness, and durability.
Why are FRPCs used in the Automotive Industry?
Light Weight
Fiber-reinforced polymer composites boast a higher strength-to-weight ratio than metals, allowing them to withstand higher loads with less mass compared to metals. This reduction in weight contributes to reduce fuel consumption, thus reducing polluting emissions. Moreover, FRPCs enhance vehicle performance by increasing stiffness, damping, and crashworthiness.
Flexibility and Overall Performance
The high degree of design flexibility is one of the important characteristics of FRPCs, as they can be easily molded, shaped, and tailored to fit specific requirements and applications for different designs. This allows automotive engineers to create novel and functional designs that can improve the aerodynamics of vehicles. Moreover, FRPCs can also enhance the aesthetic appeal of vehicles, as they can produce smooth and glossy surfaces, as well as various colors and textures.
Corrosion Resistance
FRPCs have a high resistance to corrosion, as they do not react with water, oxygen, or other chemicals. This property gives them an advantage over metals, which can rust and deteriorate over time. Corrosion can affect the performance, safety, and appearance of vehicles, as well as increase the repair and replacement costs. Therefore, using FRPCs can extend the service life of vehicles and reduce the environmental impact of waste and emissions.
FRPCs Manufacturing Techniques
1- Prepreg Manufacturing
Prepreg manufacturing is the process of producing composite materials that consist of fibers pre-impregnated with a partially cured resin matrix. Prepregs provide various advantages over traditional composite materials, including higher quality, consistency, and performance, as well as lower labor, waste, and environmental effects.
Prepregs are manufactured through two main methods: hot melt process and solvent dip process.
The hot melt process begins by coating a thin film of heated resin on a paper substrate and then impregnating the fibers with the resin under heat and pressure. This method can produce high-quality prepregs with good surface finish and dimensional accuracy.
In the solvent dip process, the resin is dissolved in a solvent bath, and then the fibers are dipped in the resin solution. The solvent is then evaporated using a drying oven, leaving behind the prepreg. This method can produce low-cost prepregs with high fiber content and low void content.
Both methods require careful control of the resin viscosity, temperature, pressure, and curing time to ensure optimal properties and performance of the prepregs.
2- Molding Techniques
Molding is essential for shaping FRPCs into complex designs. Molding techniques are mainly divided into two methods used in the automotive industry: compression molding and injection molding.
Compression Moulding
In this method, the prepreg material is placed in a mould followed by pressurization and heating. This process ensures the consolidation of the fibers and the curing of the resin, resulting in a high-strength composite with the desired shape.
Injection Moulding
This technique is particularly useful in producing intricate and detailed components. In this method, the prepreg material is injected into a mold under high pressure, allowing for the production of complex shapes with precision.
3- Automated Layup and Automated Tape Laying
In this process a robotic system is used to precisely position and layer the prepreg materials. This method ensures consistency in fiber orientation and uniform resin distribution, which in turn minimizes variations in mechanical properties. This method is widely used for large-scale production of structural components such as chassis and body panels.
Automated Tape Laying (ATL) is a common type of automated layup, where layers of prepreg tape are laid down on a mold surface in a specific direction to build up layers. The process is similar to additive manufacturing, as material is added layer by layer.
Applications in the Automotive Industry
Structural Components
(FRPCs) are increasingly used in various structural components of vehicles; critical parts that are responsible for bearing the load and impact forces during normal operation and collision events, such as chassis, body panels, and structural reinforcements, benefit from the high strength and stiffness of these materials. This not only enhances safety standards but also contributes to the overall performance of vehicles.
Interior Components
Characteristics of FRPCs, such as easy molding, shaping, and tailoring to fit specific requirements and applications, enabled automotive engineers to create functional designs that can improve the appearance of the interior parts, such as dashboards, door panels, and seat structures. Moreover, FRPCs can also reduce the weight of the interior components, which in turn improves the overall fuel efficiency and performance of the vehicle.
Exterior Components
High impact resistance and durability are important features of FRPCs, as they can deform and recover without breaking or cracking.
These features give them importance for manufacturing the exterior components, like bumpers, fenders, and hoods, which are prone to damage during collisions. Additionally, FRPCs can also reduce repair and replacement costs, as they can retain their shape and functionality after minor collisions.
Alternative Powertrain Components
(FRPCs) find applicability in alternative powertrain components like battery enclosures, electric motors, and power electronics. They contribute to weight reduction, enhance thermal management, and provide protection against mechanical and electrical stresses. By using FRPCs, electric and hybrid vehicles can increase their energy efficiency and extend their driving range, as well as reduce the environmental impact of battery production and disposal.
Conclusion
(FRPCs) in the automotive industry promote efficiency, sustainability, safety, and enhanced performance. With a high strength-to-weight ratio, FRPCs enabled vehicle manufacturers to achieve significant weight reduction, high efficiency, strong structure and reduced CO2 emissions.
The flexibility of their design and different manufacturing methods facilitate the development of designs that improve aerodynamics, which in turn improve fuel efficiency.
From structural components to internal and external elements, FRPCs enhance safety and reduce maintenance costs. As alternative powertrains gain prominence, FRPCs play a pivotal role in developing lightweight components for electric vehicles, fostering a greener and technologically advanced automotive landscape. Challenges notwithstanding, the growing integration of FRPCs promises a dynamic and sustainable future for the automotive industry.
More from AZoM: Mass Spectrometry in the Characterization and Discovery of Metamaterials
References and Further Reading
Holbery, J., & Houston, D. (2006). Natural-fiber-reinforced polymer composites in automotive applications. JOM. [Online] Available at: https://link.springer.com/article/10.1007/s11837-006-0234-2.
Robinson, A. L., Taub, A. I., & Keoleian, G. A. (2019). Fuel efficiency drives the auto industry to reduce vehicle weight. MRS Bulletin. [Online] Available at: https://link.springer.com/article/10.1557/mrs.2019.298.
Thomas, G. P. (2013, April 16). Composite Prepregs – Manufacturing, Benefits and Applications. AZoM. [Online] Available at: https://www.azom.com/article.aspx?ArticleID=8353.
Disclaimer: The views expressed here are those of the author expressed in their private capacity and do not necessarily represent the views of AZoM.com Limited T/A AZoNetwork the owner and operator of this website. This disclaimer forms part of the Terms and conditions of use of this website.