Steel is an essential structural material and its production worldwide has shown significant increases over the last few years. In 2007, around 1.344 billion tons of steel were sold with new manufacturers entering the market to meet the increasing demand. To ensure that steel fulfills its application requirements, quality control has become highly important.
Quality Issues in Steel Manufacture
One of the basic quality issues in steel production is "cleanliness". During the manufacturing process a number of influencing variables may cause impurities within the product.
Non-Metallic Incusions in Steel
These include mainly non-metallic inclusions that may originate from the slag formed on top of the cast or the lining of the furnace. It is also common that inclusions are formed by chemical reactions with alloying elements, precipitating gases or contaminating elements from recycled scrap metal.
Using Light Microscopy to Detect Non-Metallic Inclusions in Steel
The kind and quantity of non-metallic inclusions impacts the physical and mechanical properties of the steel considerably, such as the tensile strength, toughness or fatigue limit, and may cause critical failure of the entire component. In this respect, one of the most essential inspection methods is based on the assessment of the microscopic content of non-metallic inclusions in steel using light microscopy (LM).
This evaluation technique is regulated in detail by a number of international standards, mainly ASTM E45, other standards include "Shuttle & Find" correlative microscopy technique DIN 50602 and the new European standard EN10247. However, only the latter is specifically designed for fully automated analysis by LM techniques and allows the rating of inclusions found in modern steel grades, e.g. mixed or colored inclusions.
Inclusion Types
The common inclusion types are sulfides, oxides and silicates and can be detected by their color, shape and appearance by using Light Microscopy. It is however not possible to determine their exact chemical composition. Furthermore, modern steels increasingly contain non-metallic inclusions that cannot be assigned to either of the "typical" inclusion types. Thus, to be able to have effective quality control, it is essential to reliably identify any of these conspicuous inclusions.
Scanning Electron Microscopy and X-Ray Elemental Analysis
This can be achieved by scanning electron microscopy (SEM) and associated x-ray element analysis techniques. The main challenge is, however, to accurately relocate the small inclusions in the SEM which were previously identified in the Light Microscope, while it is alsoi essential to maintain an effective and user-friendly workflow at the same time. The normal practice is to mark conspicuous inclusions manually e.g. by drawing a circle with a marker around the inclusion on the sample surface and thus contaminating the sample surface.
Light and Electron Microscopy (CLEM)
Carl Zeiss has developed a CLEM solution based on a special specimen holder with three markers defining a coordinate system that can be calibrated very quickly and semi-automatically with the AxioVisionM "Shuttle & Find" software module. The software module itself incorporates itself seamlessly into the established AxioVision user interface and is able to communicate directly with the SEM control unit.
Instrumentation and Results
The experiment involves inspecting the microscopic content of non-metallic inclusions in a mechanically polished steel sample (16MnCr5 grade) at 100 x magnification in the LM. The sample was initially mounted into the CLEM "Specimen Holder CorrMic Mat Universal A", which in turn was fixed on the motorized scanning stage of the compound LM Carl Zeiss AxioImager Z.2m. The coordinate system of the sample holder was then calibrated using the Shuttle & Find module.
As anticipated, the majority of the non-metallic inclusions can be classified as elongated sulfide stringers and mostly unaligned oxides as shown in Figure. 1. When inspection was done, a number of conspicuous inclusions were detected that apeared to be rather large mixed inclusions surrounded by an unidentified third phase.
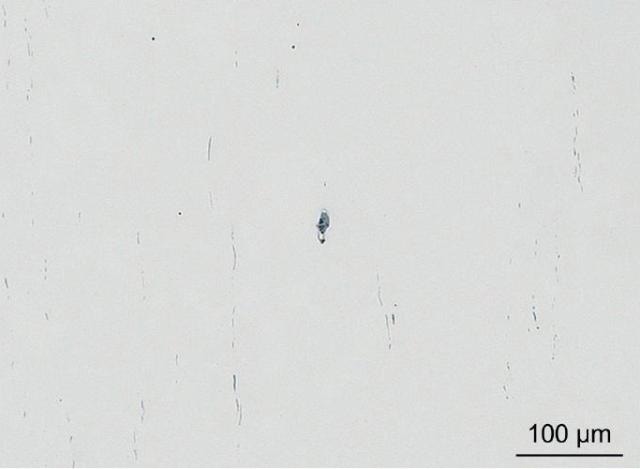
Figure 1. LM image of 16MnCr5 steel grade showing elongated and aligned sulfide inclusions (grey) and small globular oxide inclusions (black). Note that the rather large conspicuous inclusion in the center of the image consists of at least three different phases.
Digital color images of the conspicuous inclusions were obtained with the Carl Zeiss AxioCam HRc at 500x magnification as shown in Figure 2. Regions of interest (ROIs) were subsequently defined in the LM images with the Shuttle & Find software module for further investigation with SEM techniques.
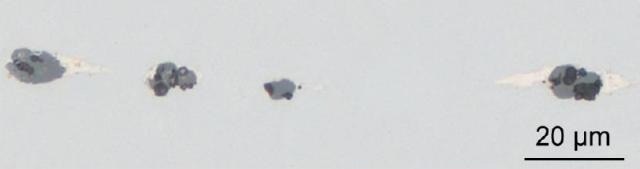
Figure 2. LM image of 16MnCr5 steel grade showing a conspicuous inclusion stringer. Note that the particles consist of at least three different phases (clear white and different shades of grey).
The resulting element distribution maps confirms that the core of the investigated mixed inclusions comprises the primary inclusion constituents MnS and Al2O3. It was however, strange to notice that the unidentified phase is generally made up of Bi, and small amounts of Cu and P. According to the chemical composition data sheet of this steel grade, only P is allowed in minor quantities, however it must not contain Bi and Cu.
It could thus be proven that the analyzed steel sample is out of specification.
As to the origin of these elements, it is most likely that they represent contaminating remnants from recycled scrap metal that was added to the primary melt.
The specimen holder was then transferred to the Carl Zeiss SUPRA 40VP FE-SEM for comprehensive morphological analysis of the inclusions at high magnification. After re-calibrating the holder coordinate system and easily loading the LM digital image with its related ROIs into the Shuttle & Find module, the selected areas were moved quickly and accurately in the SEM where the sample was imaged using the back-scattered (BSE) and secondary electron (SE) detection as shown in Figure. 3.
The chemical composition was evaluated using EDS mapping as shown in Figures 4 and 5. For each inclusion two mappings are displayed to visualize different elements contained in the particular phases.
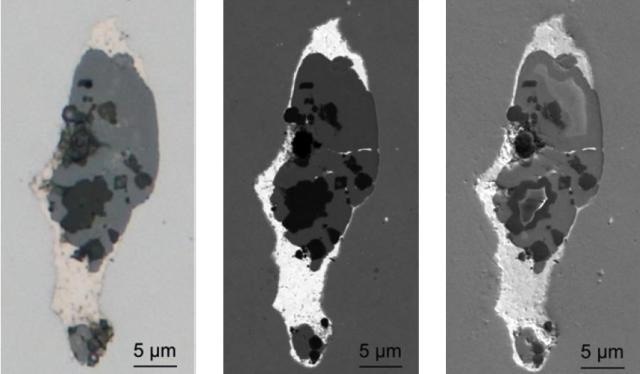
Figure 3. Brightfield image in LM (left) as well as BSE (center) and SE (right) images in SEM of the conspicuous mixed inclusion shown in Fig. 1. Images were acquired using the CLEM technique with the "Shuttle & Find" module. Note that the bright phase surrounding the core has a rather high density as can be deduced from the BSE image.
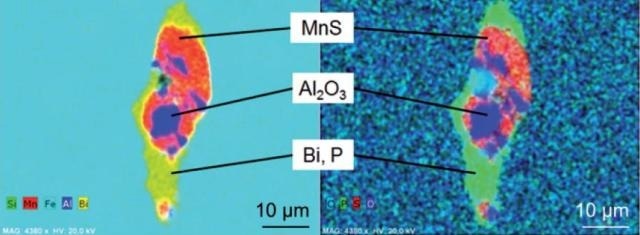
Figure 4. EDS mapping of the conspicuous mixed inclusion shown in Fig. 3. The core of the mixed inclusion consists of the "typical" inclusion types MnS (red) and Al2O3 (blue) whereas the surrounding bright phase contains the elements Bi (yellow) and P (green).
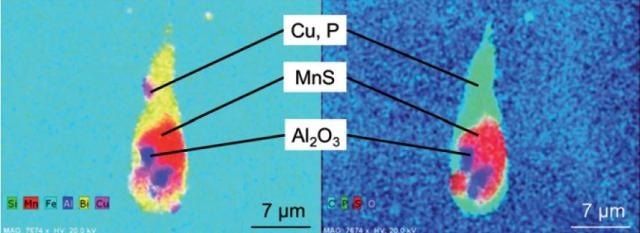
Figure 5. EDS mapping of the conspicuous mixed inclusion shown in Fig. 2 (left most particle). The core of the inclusion consists of the "typical" inclusion types MnS (red) and Al2O3 (blue) whereas the surrounding bright phase contains the elements Bi (yellow), Cu (pink) and P (green).
Correlative Microscopy from Carl Zeiss
Carl Zeiss is the major provider of light and electron microscopes and is therefore dedicated to developing correlative microscopy solutions that allow exciting new insights into the micro and nano worlds. By providing integrated product solutions for easy sample transfer, quick coordinate recovery and powerful image correlation the company endeavors to obtain the shortest time-to-result and maximum information from customer samples.
Conclusion
Shuttle & Find bridges the worlds of efficient LM and high resolution SEM for the Carl Zeiss product series and adds additional value to the evaluation of nonmetallic inclusions in regular routine inspection tasks.
Automated LM analysis such as the Carl Zeiss AxioImager Z.2m and the AxioVision NMI-module, enables a quick and effective scanning of large sample areas in true colour as required by the relevant standards.
The rating of non-metallic inclusion content based on five international standards is possible in only one single analysis run and thus a resource and cost efficient screening of polished steel samples can be attained.
Conspicuous inclusions obtained during the inspection process can easily be documented in the LM and further morphological analysis can be collected in the SEM by applying the CLEM technique. This allows detailed structural imaging and accurate information about the inclusion's chemical composition and crystallographic orientation by X-ray analysis techniques in the SEM like EDS, WDS, or EBSD. Therefore, this effective and streamlined workflow tool significantly increases productivity and sample throughput.
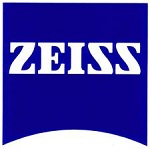
This information has been sourced, reviewed and adapted from materials provided by Carl Zeiss Microscopy GmbH.
For more information on this source, please visit Carl Zeiss Microscopy GmbH.