A mechanical pusher mechanism introduces the product carrier in pusher-type furnaces. The product carrier can include a rectangular boat with a lid in the case of a system equipped with a flat hearth plate, or it can include a cylindrical boat with regards to a tubular pusher system.
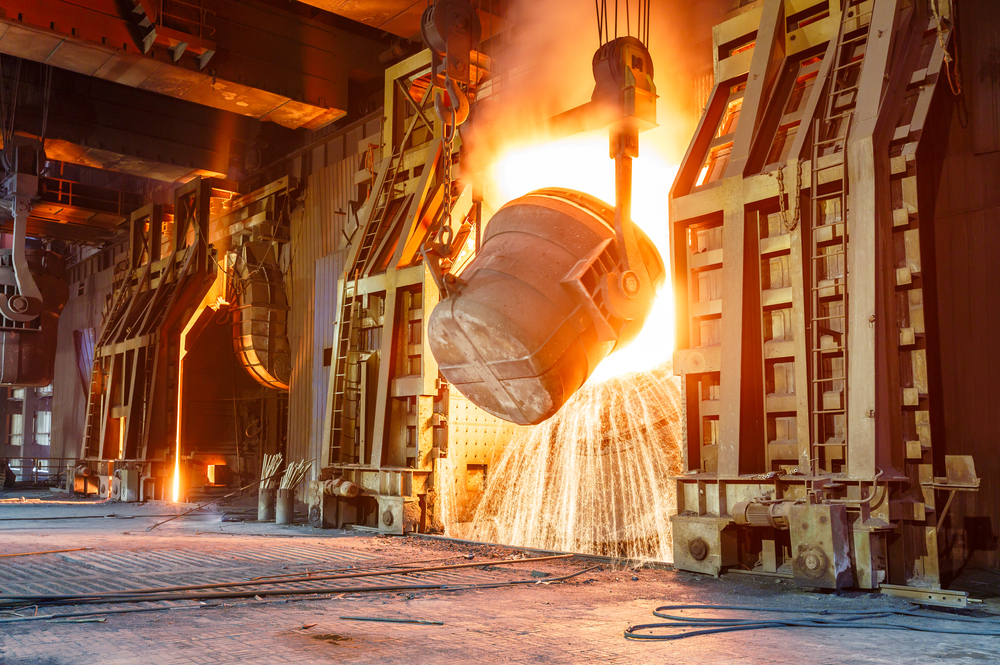
Image Credit: Shutterstock/Zhao jiankang
These product boats are pushed sequentially into the furnace, causing the train of boats to be moved in and out of the furnace system. Pusher systems are specifically developed for processes, where precise control of both the atmosphere and temperature are required. They are suitable for processes with longer residence times, which demand precise control of the limited gas/solid reaction and the product heat up rate (temperature profile).
Careful thermal analysis of the product and furnace is required to ensure that a pusher furnace is properly designed for a specified process. The product’s thermal conductivity is required to measure the time needed to achieve a uniform product temperature under varying furnace configurations. However, data on thermal conductivity is seldom available in the case of powders.
This study aims to enhance the predictive capability of furnace thermal modeling using the experimental measurements of time-to-temperature for different carbon and tungsten mixtures under a range of conditions. This data was used to determine the thermal diffusivity of the powder as a function of temperature. A model for the thermal conductivity was subsequently altered to best fit the experiments. Finally, the adjusted model was used to estimate the conductivity of different powders under a range of processing conditions.
Model for the Thermal Conductivity of the Powder Bed
The thermal conductivity model presented by Sih et al in [1, 2] was used. Some of the assumptions are briefly described in the following sections; a more comprehensive review of the model is given in [3]. It is assumed that both carbon and tungsten are spherical. It is also assumed that particles have a uniform size. Generally, in the case of small particle size, the contribution of radiation to the effective thermal conductivity is rather small, when compared to the contribution of conduction through the solid particles and through the convection in the gas phase. However, as the particle size and temperature increase, the radiation component becomes a major contributor. For the analysis presented in this article, the radiation component was included in all the examples. In the case of nitrogen atmosphere, radiation is a major contributor. Conductivity of the powder is given by the following equation
.jpg)
Image Credit: Harper
Where
kR = 4FdpσT3 (kR conductivity by thermal radiation)
F = View Factor
T = Absolute temperature of the power bed
σ = stefan - boltzmann constant
dp = Particle diameter
k = Effective thermal conductivity of the power bed
kg = Thermal conductivity of the gas phase
ks = Thermal conductivity of the solid phase
ε = Porosity of the power bed
Experimental Procedures
N990 — tungsten metal powder and carbon powder — were mixed to a 6.10 wt%C target. The milling occurred in a 330 mm ball mill, which was loaded with 45 kg of 6 mm diameter WC-Co milling media and 25 kg of the sample powder. The powder was then processed on a roll mill at 60 Hz for a period of 2 hours, and the resultant powder mixture was transferred to an alloy cylindrical canister with a five-foot extension pipe measuring 15.9 mm in diameter. Two thermocouples are housed in the extension pipe, which carried the process gas to the canister. Inside the bed material, five Inconel sheathed K-type thermocouples were inserted and a same type of thermocouple was also placed on the outside of the canister. For each test, nitrogen flowed on the outside of the canister and the furnace was maintained at positive pressure. Helium or nitrogen was used as the process gas. Using a welding torch, a layer of carbon soot was applied to the outside of the vessel in order to aid with heat transfer. Figure 1 shows a schematic diagram of the test apparatus.
.jpg)
Figure 1. Design of the powder canister used in the powder heating tests.
Image Credit: Harper
Powder Heating Experiments
Before starting, each test needed setup and furnace heat up. The setup was started by weighing the canister and adding material to a maximum height of three inches from the top of the open end of the canister. In case the packed material was required, additional material was added to attain the preferred height within the canister. Insulation was placed over the exposed material followed by a metal end cap. The end cap was tack welded at four equally spaced locations around the circumference. Next, the canister was threaded on the extension pipe and the thermocouples were subsequently inserted into the material bed through openings in the insulation and canister. Process gas was connected and the vessel purged with process gas for at least 15 minutes. The furnace was also purged with nitrogen during this time.
The furnace was heated to the same conditions for each test. Both zones one and three were heated to 1,050 °C. Zone two — the hot zone where the canister was placed — was heated to 1,150 °C. Once the furnace zones reached temperature and both the canister and tube had been purged, the canister was inserted into zone 2 to begin the test. Figure 2 illustrates the test configuration showing the position of the capsule within the furnace.
A DAQ data was used to record the temperatures using logging program. The canister was pulled back to the cool zone after all the thermocouple temperatures attained equilibrium with the furnace hot zone temperature. To prevent oxidation, the canister remained in the cooling zone under purge until the material bed temperatures fell below 400 °C. The canister was later removed from the furnace and cooled to below 100 °C prior to handling.
.jpg)
Figure 2. Furnace test set up.
Image Credit: Harper
Conductivity of the Tungsten + C Powder Bed
The thermal conductivity of the powder bed was computed in two ways:
1. Using the Sih & Barlow model (Equation 1.)
2. Modeling the canister heating tests and adjusting the thermal diffusivity α(T) to acquire the best fit between the model and the experiments for the temperature history at the center of the canister. The conductivity was determined from:
Where ρ and Cp are the density and the specific heat of the powder bed, respectively
The accuracy of the Sih & Barlow model was assessed by comparing the values of thermal conductivity calculated by each method.
For the experiments, two types of tungsten plus carbon samples were assessed at a variety of processing atmospheres and packing densities. The tests are tabulated in Table I. Before each test, the powder bed density was recorded. The rule of mixtures was used to calculate the specific heat (Table II).
Table I. Test matrix.
Test # |
Temperature
°C |
Material |
Average Particle size LM-FSSS μm |
Fill Type |
Density
g/cm3 |
Process Gas |
1 |
1,150 |
W75 |
15.2 |
Semi-loose |
5.1 |
Helium |
2 |
1,150 |
W75 |
15.2 |
Tamped |
6.2 |
Helium |
3 |
1,150 |
W37 |
2.5 |
3.6 |
Nitrogen |
Helium |
4 |
1,150 |
W37 |
2.5 |
4.7 |
Nitrogen |
|
5 |
1,150 |
W75 |
15.2 |
Vibrated |
|
|
Table II. Specific heat of W+C powder.
Temperature
°C |
Cp of W+C
J/kg°C |
0 |
170 |
100 |
204 |
500 |
245 |
1000 |
267 |
1500 |
285 |
2000 |
302 |
Modeling the Powder Heating Experiments
An axisymmetric finite element method (FEM) model was used to model the canister heating tests to solve the heat conduction equation numerically. For this model, the process gas flow was ignored as a small heat sink on the system. The boundary conditions for the canister were modeled by the application of the temperature history measured by the thermocouple TC1 that was located on the canister’s external surface.
In Figure 3, the calculated temperature histories at each thermocouple location are plotted. The thermal diffusivity of the powder bed α(T) was adjusted, in order to achieve the best fit between the model and the experiments for the temperature history at the center of the canister.
.jpg)
Figure 3. Test 1 Time Temperature Curves: SC75, Semi Loose 5.1 g/cc, Helium.
Image Credit: Harper
Measured Effect of Powder Bed Density, Grain Size and Cover Gas on Conductivity
The average thermal conductivities evaluated for the different tests are shown in Figure 4. Usually, with increasing density, the conductivity increases. The two different powder grain size tested do not seem to affect the conductivity greatly. While thermal conductivity under N2 gas is lower than the conductivity under He gas, the fact that all the tests under He used higher powder bed densities confounds it.
.jpg)
Figure 4. Average thermal conductivity calculated by modeling the powder heating tests.
Image Credit: Harper
Assessment of the Accuracy of the Thermal Conductivity Predictions
As there were a wide range of values for the conductivity of carbon reported in the literature [4, 5], high and low bounding values were used to form a range for comparison. Tungsten’s thermal conductivities were taken from [6]. There is also some ambiguity concerning the conductivity of the W particles as the particles may not be fully dense, which would impact their conductivity. The thermal conductivity as a function of temperature used to analyze the Carbon and W particles is tabulated in Table III. The wide range in the thermal conductivity of the carbon results in a “high” and “low” range in average particle thermal conductivity.
The conductivity evaluated using the Sigh and Barlow model is compared to the values calculated from the FEM modeling of the canister heating tests 1 and 5 in Figures 5 and 6. The “high” and “low” labels in the plots represent the use of the high and low values of k for carbon.
Table III. Summary of temperature dependent thermal conductivity of particles
Temperature |
Carbon - Low |
Graphite (Carbon "high" Value) |
Tungsten |
Average of Carbon and W |
Average of Graphite and W |
°C |
W/m°C |
W/m°C |
W/m°C |
W/m°C |
W/m°C |
100 |
3 |
110 |
160 |
81 |
135 |
500 |
6 |
64 |
126 |
66 |
95 |
1000 |
8 |
40 |
112 |
60 |
76 |
1500 |
8 |
33 |
104 |
56 |
69 |
Test 1 was performed under He gas. In this as well as the tests performed under He cover gas, the thermal conductivity of the bed is over-predicted by the model (Figure 5.) On the other hand, in comparing the data to a model for the case of an N2 cover gas, the thermal conductivity of the bed was under predicted by the model. Using a simple mixing rule, the data equals the thermal conductivity that was predicted, if the N2 % is increased from zero to between 40 and 65%. This not only reduces the effect of the highly conductive He on the model, but also lowers the prediction. During the test, N2 may not be completely removed from the powder and therefore it is likely that a mixture of N2 and He may have existed in the bed of material.
The results for test 5, where N2 was used as the process gas, are presented in Figure 6. Here, as well as in test 6 (not shown), the best accord between the model and the experiments is achieved with the “low” prediction of thermal conductivity. While the data are between the high and low predicted values, it is more proximal to the low prediction.
Based on these results, the Sih & Barlow model was used for additional calculations with the following adjustments:
- The low value for C conductivity must always be used
- For cases under He, the model with an atmosphere composition of 60% N2 and 40% must be used
The thermal diffusivity α(T) was calculated for the different powder bed compositions and densities using these adjustments and equation 2. The chosen densities are based on the densities in the lab for vibrated (lower bulk density) and tamped (higher bulk density) processing. The calculated α(T) values are tabulated in Table IV.
.jpg)
Figure 5. Comparison of Trial 1, W75 in He with Predicted Thermal Conductivity.
Image Credit: Harper
.jpg)
Figure 6. Comparison of Trial 5, W75 in N2 with Predicted Thermal Conductivity.
Image Credit: Harper
Table IV. Summary of thermal diffusivities calculated according to the adjusted Sih & Barlow model
Material |
W37 |
W37 |
W37 |
W37 |
W75 |
W75 |
W75 |
W75 |
Atmp |
N2 |
He |
N2 |
He |
N2 |
He |
N2 |
He |
Density |
3.6 g/cc |
3.6 g/cc |
5.6 g/cc |
5.6 g/cc |
4.7 g/cc |
4.7 g/cc |
6.2 g/cc |
6.2 g/cc |
Temp (°C) |
α (mm²/sec) |
α (mm²/sec) |
α (mm²/sec) |
α (mm²/sec) |
α (mm²/sec) |
α (mm²/sec) |
α (mm²/sec) |
α (mm²/sec) |
100 |
0.123 |
0.320 |
0.092 |
0.235 |
0.103 |
0.265 |
0.086 |
0.219 |
500 |
0.161 |
0.405 |
0.120 |
0.294 |
0.136 |
0.335 |
0.113 |
0.275 |
1000 |
0.199 |
0.508 |
0.147 |
0.366 |
0.172 |
0.422 |
0.142 |
0.345 |
1500 |
0.235 |
0.634 |
0.173 |
0.452 |
0.211 |
0.532 |
0.173 |
0.431 |
2000 |
0.290 |
0.835 |
0.212 |
0.586 |
0.271 |
0.705 |
0.221 |
0.565 |
2200 |
0.319 |
0.939 |
0.232 |
0.654 |
0.303 |
0.793 |
0.246 |
0.632 |
2500 |
0.372 |
1.121 |
0.269 |
0.771 |
0.360 |
0.947 |
0.291 |
0.749 |
1D Bed Time to Temperature Predictions
A FEA analysis was carried out for a 1 dimensional rectangular bed of a range of bed depths. This is an extension to the classical problem with an exact solution of a plane wall with diffusivities, convection and constant convection coefficients, etc. Here, the 1 dimensional problem is identical except all of the variables (specific heat, thermal conductivity, and radiation boundary condition) are dependent on temperature, and hence there is no exact solution. On the edge of the rectangular bed, the radiation boundary condition is placed and the FEA was then run with the suitable material properties. Half of the overall thickness with the boundary condition applied only to one edge of the bed is used by the model. The model assumes symmetry around the center of the bed. A model of the time temperature relation for processing at 2200 °C was generated for this pusher configuration operating under a N2 process gas. This is shown in Figure 7, with the various lines denoting the depth of the entire bed.
.jpg)
Figure 7. Time Temperate of SC75 Material, N2, 4.7 g/cc.
Image Credit: Harper
Modeling Various Pusher Furnace Configurations
A number of models (Figure 8) were prepared to study the effect of powder bed depth and boat and muffle geometry. Considering radiation and conduction heat transfer, the models are 2-dimensional thermal models. Convection heat transfer is neglected in these models as its contribution is small in heat transfer at the applied temperatures. A graphite muffle possesses a time dependent radiation boundary conditions on the outside surface which represents a time-temperature profile of a pusher furnace. The graphite muffle is immobile and the graphite boat and product move through the muffle, and therefore only the graphite boat and product are able to absorb energy. In order to simulate this condition in a 2-dimensional model, the graphite material properties of the muffle are altered by lowering the specific heat and density values by 3 orders of magnitude lower than the actual values. The thermal conductivity continues to be the actual value. The reduction of the specific heat and density causes the muffle to be at queasy steady state and absorb negligible heat content. This method of modified properties enables a 2-dimensional model to capture the effective heat transfer of a moving boat inside a stationary muffle without the computational penalty of a 3-dimensional model. The estimated specific heat and density is used by the graphite boat and product. The process gas used was N2, and the processing temperature was set to 2200 °C.
Figure 8 summarizes the calculated temperature profiles. One result is immediately obvious — as the bed depth deepens, the temperature gradient between the core of the powder bed and the outside of the graphite vessel increases. By separating the vessel into a stacked unit, the contiguous powder bed is reduced, and the gradient is also reduced. However, a considerable temperature spread is still observed to some extent because of the additional graphite mass. When compared to the lower aspect ratio shapes, the wide shallow bed leads to a reduction in time to temperature (Figure 7) of the bed material.
.jpg)
Figure 8. Powder bed modeling for various boat and muffle geometries.
Image Credit: Harper
Conclusions
The Sih & Barlow model for the thermal conductivity of a powder was applied to the calculation of the conductivity of a WC + C powder bed. The accuracy of the model was evaluated through the modeling of a set of experiments in which a powder was heated in a canister. Best results were achieved by making two adjustments to the model:1) of the reported values for the conductivity of C, used the low values of thermal conductivity reported in Table III, and 2) when working with He atmosphere, modeled the atmosphere as a mixture of 40% H2 and 60% N2.
The thermal conductivity from the Sih & Barlow model was included in the modeling of the carburization of W in a pusher furnace. A number of geometric configurations and powder bed depths were examined and the resulting temperature fields were reported.
The examples show that modeling is a very important tool that can guide the optimization of powder bed, boat, and furnace geometry. Obviously, the final design must account for other practical factors such as furnace construction, material handling, and throughput.
Future refinements to the model will include accounting for the heat associated with the carburization reaction. The changes associated with the progress of the carburization reaction are another aspect that could be addressed. As the reaction proceeds, the nature of the powder bed changes, the C particles are consumed, the W is converted to WC, the particle size changes, and the density of the bed also changes. The effective conductivity is affected by all these factors.
References
1. Sih, S. S. & Barlow, J. W., 1994. Measurement and prediction of the Thermal Conductivity of Powders at High Tempera-tures. Austin, s.n., pp. 321-329.
2. Sih, S. S. & Barlow, J. W., 1995. The Predictions of Thermal Conductivity of Powders. Austin, s.n., pp. 397-401.
3. Witting, P. & Dover, B., 2014. Analysis of the Heating of Powders in a 'Pusher' Furnace, in Proceedings of the PM2014 World Congress on Powder Metallurgy and Particulate Materials, Orlando, 2014. MPIF, New Jersey, USA.
4. Craig W. Ohlhorst, W. L. V. P. O. R. a. H.-T. T., 1997. Thermal Conductivity Database of Various Structural Carbon-Carbon Composite Materials, Hampton: Langley Research Center.
5. Page, D. J., 1991. The Industrial Graphite Engineering Handbook. Danbury: UCAR Carbon Technology Corporation.
6. Lassner, E. & Schubert, W.-D., 1999. Tungsten. New York: Plenum Publishers
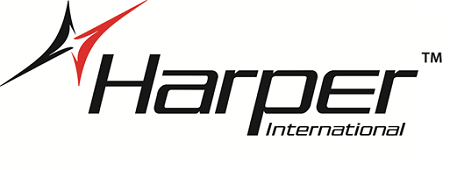
This information has been sourced, reviewed and adapted from materials provided by Harper International.
For more information on this source, please visit Harper International.