Sponsored by HORIBAJun 14 2018
Developing battery technology is meeting with the demand for more portable devices, more power storage, and more time between recharges. Enhanced performance necessitates increased control over the materials used and their physical properties, including particle size distribution. In this study, the LA-950 laser diffraction particle size analyzer was utilized to execute particle size distribution measurements on a variety of the materials used in lithium ion batteries.
Introduction
Lithium batteries include disposable (primary), rechargeable (secondary), and rechargeable lithium titanate batteries. Disposable lithium batteries use lithium metal or lithium compounds as the anode. Rechargeable lithium ion batteries include an intercalated lithium compound as the electrode material. A lithium titanate battery is an adapted lithium-ion battery that uses lithium titanate nanocrystals on the surface on the anode.
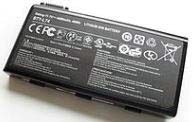
Some cathode anode materials used in lithium batteries are:
Cathode
- Lithium cobalt oxide LiCoO2
- Lithium nickel oxide LiNiO2
- Lithium manganese oxide LiMn2O4
- Lithium iron phosphate LiFePO4
Anode
- Carbon C
- Lithium Li
- Lithium titanate Li2TiO3
The particle size distribution (PSD) of the materials used in the production of batteries is tested both during R&D and in product acceptance QC, as PSD is generally a material specification. Particle size affects capacity and coulomb efficiency. A smaller PSD leads to a bigger specific surface area, changing critical battery properties and causing variations in the size of the voids between electrode particles, reducing battery capacity.
Experimental
Lithium Cobalt Oxide
Lithium cobalt oxide (LiCoO2) has been the standard cathode material used for secondary Li-ion batteries for over three decades. Five distinct lots of lithium cobalt oxide powder to be used as cathode material were examined on the LA-950 Particle Size Analyzer for a standard pass/fail test to determine if the material met the incoming material specification. The powder was dispersed in water containing 0.2% sodium hexametaphosphate, with the results displayed in Figure 1 and Table 1.
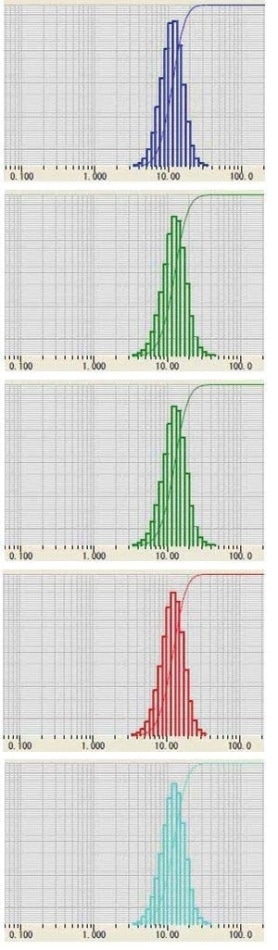
Figure 1. Five lots of LiCoO2 powder
Table 1. Five lots of LiCoO2 powder
Lot |
Median (m) |
No. 1 |
11.3 |
No. 2 |
11.8 |
No. 3 |
12.2 |
No. 4 |
12.5 |
No. 5 |
11.9 |
Lithium Manganese Oxide
While developing the method for dispersing lithium manganese oxide (LiMn2O4), the effect of using ultrasound was explored. The powder was dispersed in DI water containing 0.2% sodium hexametaphosphate. The sample was then studied both without ultrasound, and with one, three, and five minutes of ultrasound.
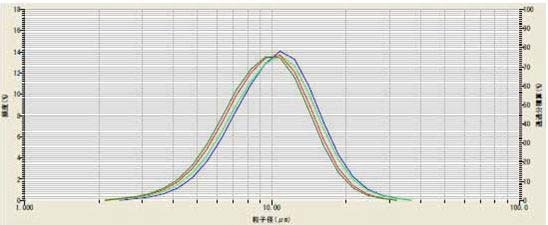
Figure 2. The effect of ultrasound on LiMn2O4
Table 2. The effect of ultrasound on LiMn2O4
Ultrasound |
Median (m) |
Color |
None |
10.46 |
blue |
1 min |
10.14 |
light green |
3 min |
9.67 |
red |
5 min |
9.42 |
dark green |
The results (Figure 2, Table 2) indicate that three minutes was the ideal time. To prove reproducibility, the method was repeated on the same sample for five days (Figure 3, Table 3).
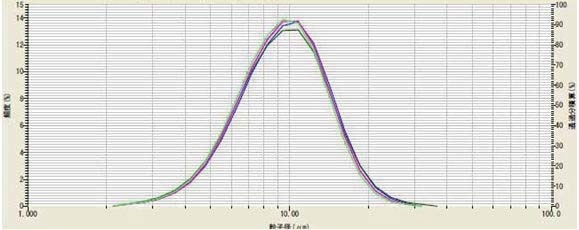
Figure 3. Method validation testing on multiple days of LiMn2O4
Table 3. Method validation testing on multiple days of LiMn2O4
|
Median (m) |
Day 1 |
9.75 |
Day 2 |
9.52 |
Day 3 |
9.18 |
Day 4 |
9.49 |
Day 5 |
9.5 |
Mean |
9.49 |
COV |
1.90% |
Lithium Titanate
Lithium titanate (Li2TiO3) is frequently applied as the anode in fast charging lithium titanate batteries. The effect of ultrasound on dispersing lithium titanate powder was investigated. The powder was dispersed in DI water containing 0.2% sodium hexametaphosphate. The sample was analyzed without and with three minutes of ultrasound. The results (Figure 4) indicate sample dispersion did not improve with use of ultrasound, so its use was discarded.
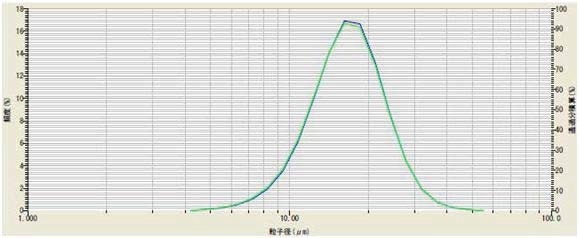
Figure 4. Li2TiO3 with (green) and without (blue) ultrasound
Two samples from different suppliers were then compared by measuring the PSD of both using the LA-950. The powders were dispersed in DI water containing 0.2% phosphoric acid and 0.2% sodium hexametaphosphate. The comparative results for Sample A (mean = 6.33 µm) and Sample B (mean= 16.7 µm) are shown in Figure 5.
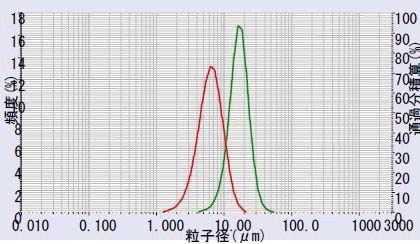
Figure 5. Li2TiO3 sample A (red) vs. Sample B (green) Reproducibility: Lithium manganese oxide/Lithium titanate
Two samples (LiMn2O4 and Li2TiO3 ) were analyzed 10 times to quantify the reproducibility of the LA-950 (Figure 6). The COV values are very low, indicating that the method is effective, and demonstrating the high performance level of the LA-950 particle size analyzer.
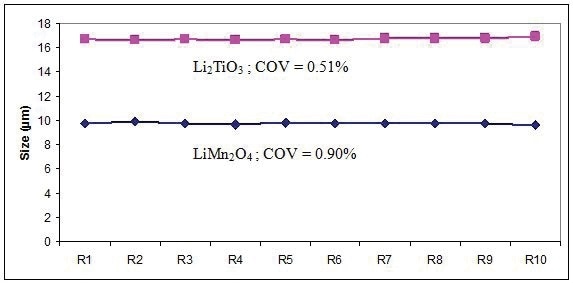
Sample |
LiMn2O4 |
Li2TiO3 |
R1 |
9.75 |
16.70 |
R2 |
9.93 |
16.6 |
R3 |
9.75 |
16.7 |
R4 |
9.66 |
16.6 |
R5 |
9.83 |
16.7 |
R6 |
9.78 |
16.6 |
R7 |
9.76 |
16.8 |
R8 |
9.75 |
16.8 |
R9 |
9.79 |
16.8 |
R10 |
9.6 |
16.9 |
Ave |
9.76 |
16.7 |
COV |
0.90% |
0.51% |
Figure 6. Reproducibility over 10 results for LiMn2O4 and Li2TiO3
Instrument to Instrument Agreement
Test results from different laboratories need to be compared by companies that have multiple locations. Samples of lithium manganese oxide and lithium titanate were studied on two different LA-950 systems in order to quantify the level of agreement between instruments (Figure 7).
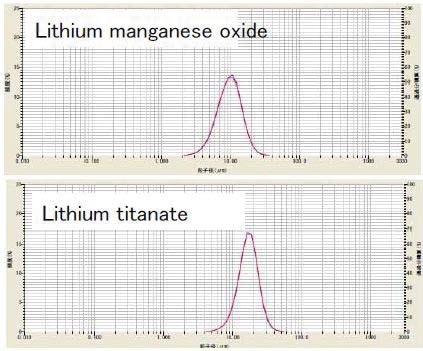
|
950 1 |
950 2 |
Δ |
LiMnO |
9.75 |
9.64 |
0.1 |
LiTi |
16.7 |
16.9 |
0.2 |
Figure 7. Instrument to instrument agreement for LiMn2O4 and Li2TiO3 on two different LA-950 systems
Conclusions
When measuring the PSD of many battery materials, the LA-950 demonstrated excellent reproducibility and agreement between systems. This performance has been recognized by several manufacturers of battery materials, leading to numerous sales to suppliers and users around the world.
Acknowledgements
Many thanks to the HORIBA Applications Center in Kyoto for generating the excellent data shown in this application note.

This information has been sourced, reviewed and adapted from materials provided by HORIBA.
For more information on this source, please visit HORIBA.