With the increasing need for improved vehicle fuel economy, the automotive industry is optimising designs to reduce vehicle body weight. Optimised designs of outer body panels must meet several performance criteria including stiffness, oil canning or critical buckling load and dent resistance. Dent Resistance of Automotive Panelling Stiffness is a fundamental concern for the perceived quality of a body panel. Along with oil canning (the ‘popping’ of a panel when pressed) it determines bow the panel ‘feels’ to a customer. Dent resistance is important to avoid panel damage in-plant and minimise dents and dings on external parts in service. The importance that automotive companies attach to these criteria are well illustrated by the criticism in a recent ‘Which?’ report directed at a product of one well known European car manufacturer for the flimsy bodywork and poor resistance to dents. Poor panel quality in used cars will generally depress resale values and possibly influence the decision to purchase a particular brand. Causes of Dents in Automotive Panelling From a practical point of view, dents can be caused in a number of ways and on the full range of external body panels. Considering doors as an example, denting can occur from stone impacts (dynamic denting) or, to the frustration of the vehicle owner, from the careless opening of an adjacently parked vehicle door. Denting can occur where the door surface is smooth and may not have sufficient curvature to resist ‘door slamming’ (quasi-static denting) or along prominent feature lines where ‘creasing’ can occur. Testing Dent Resistance of Automotive Panelling Panel dent resistance and stiffness has been the subject of considerable research. Despite this there is no industry-wide, generally adopted method of testing. For quasi-static dent testing, a wide range of purpose built dent resistance/stiffness test equipment configurations have been employed within the automotive industry. In addition, the configuration of a tensile testing machine for compression testing and similar modified equipment has allowed suitable data to be obtained. Whichever system is used, the principle of force application resulting in deflection and ultimately plastic deformation of the panel remains the same. Variables can include method of load application (hydraulic or stepper motor), speed of load application, indentor shape and size and panel assembly conditions. Some reported methods of testing are based on repeated application and removal of force at increasing levels. Others involve the continued application of a steadily increasing force until denting occurs. In some cases, stiffness is assessed using the same basic test equipment but with a much larger radiussed loading head to prevent localised deformation. Force and displacement measurements are generally incorporated into a data acquisition system. Results from Dent testing of Automotive Panelling A typical output from such a test is represented in figure 1. Initial stiffness is given by the slope of the curve in the first region, until the buckling load is reached. After ‘oil canning’, the panel continues to deform elastically, before the onset of plastic strain in the material. When the load is reversed, the permanent deformation of the panel is indicated since the lower portion of the curve does not return to zero. 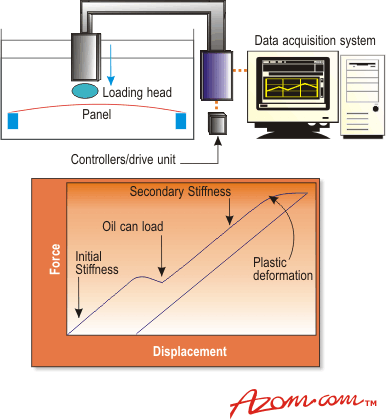 | Figure 1. Schematic of a typical dent resistance vs. stiffness measurement system, with typical force vs. displacement output graph. | Dynamic Dent Testing of Automotive Panelling Experimental testing of dynamic dent resistance has previously concentrated on drop weight rigs, using various indentor masses and drop heights to achieve a range of denting energies. Even higher energies can be achieved through the use of a compressed air operated ball bearing gun. The key issue to be considered is that test conditions (denting force, impact speed etc) must be genuinely representative of those conditions existing in the field, i.e. if the energy input to cause a perceptible dent in-service is 10 J, then the dent testing procedure should reflect this. Test results generated from the above techniques will typically be compared against performance standards set by an individual manufacturer. Standards widely known include those published by the American Iron and Steel Institute which defines a minimum dent resistance of 9.7 J and a stiffness that should exceed 45 N.mm-1. Predicting Dent Resistance of Automotive Panelling Based on testing using the practical techniques outlined, empirical formulae predicting the force and energy required to initiate a dent have been presented in recent years. Typically:  where • W is the denting energy • k is a constant • σy is the material yield strength • t is the panel thickness • S is the panel stiffness Panel Stiffness Panel stiffness depends upon the elastic modulus, the panel thickness, shape and geometry and boundary conditions. High strength steels offer more dent resistance at the same thickness as mild steel, or the opportunity for weight saving and equivalent dent resistance at reduced panel thickness. Polymeric panels deform in a different way to steel panels and many polymers can exhibit superior dent resistance performance by virtue of their low modulus. Material properties and their effect on dent resistance therefore become a prime consideration in panel design. The new Land Rover Freelander 4x4 vehicle incorporates two new material applications for body panels, which as well as offering other benefits, provide improved dent resistance performance. On a vehicle designed for off-road use, the enhanced dent resistance of the plastic front fenders and zinc coated high strength steels provide significant customer benefits. Dent Resistance and Design of Automotive Panelling Given the many iterations of automotive body panel design that can take place, it is usually late in the product development process that the first production representative parts are available for dent and stiffness testing. With press tooling already produced, it is generally only initial material properties that can be changed or local reinforcements added to improve the stiffness/dent resistance. It is not surprising, therefore, that currently much attention is being focused on the use of analytical tools such as finite element analysis for body panel performance predictions. Thus, given a certain part geometry and dimensions, predictions of stiffness and dent resistance can be made. Based on material gauge and grade and in the case of metallic panels, strain levels in the material, optimisation of the design can take place. The Future As the accuracy of such techniques improves the use of dent and stiffness testing equipment may in future be limited to selected verification of such performance predictions and quality control issues. |