Sep 13 2002
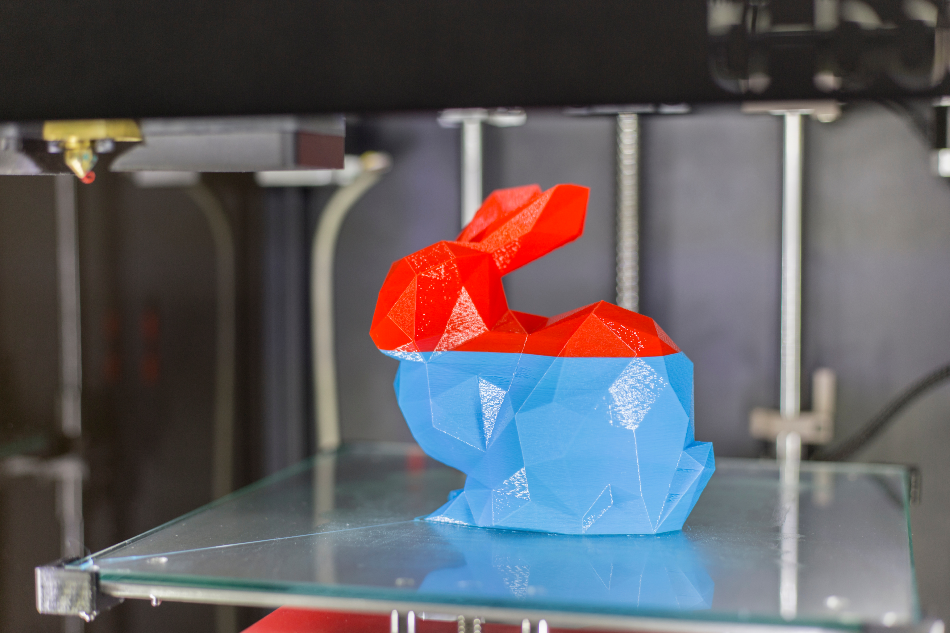
Ulas Tigin / Shutterstock
Apart from cost and quality, time to market has also become an increasingly crucial factor for the success of a product. A significant contributor to product development cycles is the time required to make prototypes.
In markets where customers are looking for individually customized components, the time and cost required to produce molds or tools can be huge.
Rapid Prototyping (RP), also referred to as Solid Freeform Fabrication (SFF) processes, helps to resolve these issues. Additive processes are generally used for developing intricate shapes, creating components without using any tools.
Filament Extrusion
Fused deposition modeling (FDM) system is the main commercial filament extrusion method. It involves using a thermoplastic build material like polymer or wax that serves as a binder and carrier for the ceramic material. The material is first extruded from a small heated nozzle and the component is created layer by layer. The green shape is then thickened through binder removal, as well as sintering or infiltration, to make a completely dense structural ceramic component.
The FDM technique can be used to make piezoelectric and structural components. Materials like Al2O3, Si3N4, SiO2, and lead zirconate titanate (PZT) have been made with the same FDM technique. Normally, filaments contain 50–65 vol% particles combined with a thermoplastic binder of plasticizer, polymer, surfactant, and wax.
FDM Applications
The following are examples of FDM applications:
- A fine-scaled piezoelectric composite structure can be produced, which is composed of polymer and PZT. The composites’ piezoelectric properties are analogous to or better than traditionally processed PZT composites.
- Si3N4 components with good microstructure and excellent mechanical properties were created with a filament containing 55 vol% of ceramic. After FDM, green parts were thickened by hot pressing, resulting in four-point bend strengths analogous to that of hot isostatic pressed parts.
- Composites with regulated composition distribution and an array of microstructures can be produced by mixing filaments of varying compositions.
Advantages of FDM
Relative simplicity is the main benefit of the FDM technique. The method does not require laser systems and uses comparatively low-cost binders, as well as materials that can be changed easily.
The main challenges are regulating the temperature inside the growing part, the need to offer support structures for the model being developed, and the precision, which is restricted to the diameter of the nozzle.