PEEK (Polyether ether ketone) is a commonly found, high-performance synthetic thermoplastic. PEEK is a polyaryletherketone (PAEK), with similar features to polyetherketoneketone (PEKK), polyetherether-ketoneketone (PEEKK) and polyetherketone (PEK).
PAEK polymers are popular because of their high chemical inertness and favorable mechanical behavior. PAEK polymers also show a high thermal stability meaning their beneficial properties remain present at high temperatures.
PEEK was only introduced to the market relatively recently, in the late seventies, though it is already used in a wide range of applications, such as biocompatible prosthetics and implants, molded components such as gears and plates, insulators for wires and motors, and tubing.
In terms of a performance material PEEK is comparable to fluoropolymers as they share similar beneficial properties, such as a service temperature up to 260 °C (500 °F); however, in contrast, PEEK provides more versatility.
This means it can be used in a wider range of applications. At the time of writing PEEK is the most popular PAEK polymer, with new applications still being developed.
Synthesis and Structure
The first synthesis of PEEK took place in 1977, with industrialization of the process achieved by 1981.1,2 Synthesis of PEEK most commonly involves the reaction of disodium hydroquinone with difluorobenzophenone (Figure 1). PEEK contains no fluorine, despite being frequently grouped with fluoropolymers like PFA or PTFE.
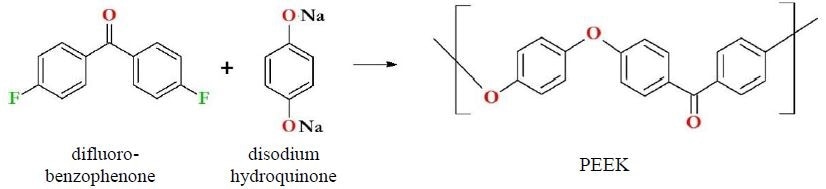
Figure 1. PEEK synthesis and immediate precursors. PEEK is synthesized most immediately from difluorobenzophenone and disodium hydroquinone. Note that PEEK does not contain fluorine and therefore is not a fluoropolymer.
Conventionally the synthesis of PEEK was difficult as it is not soluble in the majority of common organic solvents.2,3 Early attempts produced PEEK of a low chain length that precipitated early and had a fully amorphous structure.3
The synthesis was improved by the use of high boiling point solvents that allowed PEEK chains to be synthesized at a higher length.2,3 Adjusting the chain length of PEEK molecules allows manufacturers to select for specific tensile strengths or glass transition temperatures (Tg).
PEEK is typically not a rubber (i.e. elastomer) and the straight-chain, non-crosslinked form of PEEK synthesized using modern methods is a hard, semi-crystalline plastic.
PEEK has a structure consisting of alternating ketone and ether bonds (Figure 2). Whilst these bonds provide PEEK with some flexibility it is still considered a rigid polymer. The ketone and ether bonds in PEEK stop it from having a planar conformation, however π- π stacking between PEEK’s aromatic groups improve its crystallinity. The presence of ether bonds also makes PEEK suitable for melt-processing in extrusion molding.
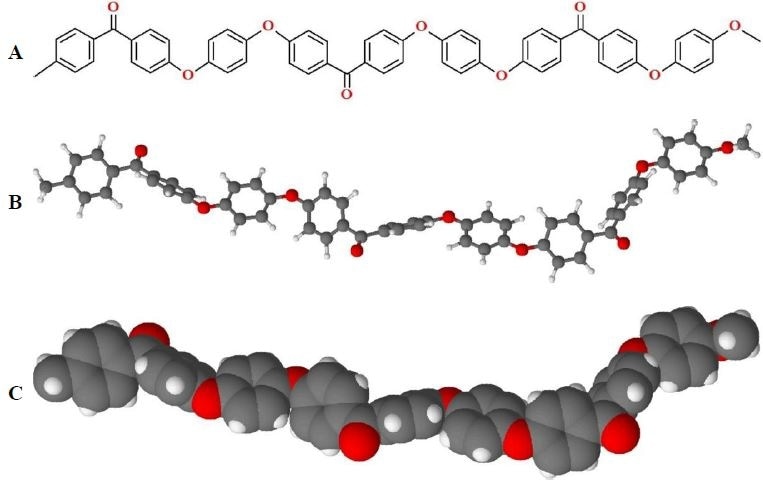
Figure 2. Structure of PEEK. A) Stereo bond-line drawing, B) ball-and-stick model, and C) space-filling model of PEEK. (Conformations of PEEK are variable during melt and amorphous phases).
These seemingly small modifications to an aromatic chain structure make PEEK a consistently high-performing and versatile polymer.
Processing
PEEK is a melt-processable thermoplastic; however, it is relatively more expensive to process than other thermoplastics due to its high melting temperature of 343 °C (649 °F). PEEK’s fluidic melt state has good stability allowing it be processed using standard industrial systems between temperatures of 360 °C to 400 °C (680 °F to 752 °F), (Table 1).4 In this temperature range PEEK produces no corrosive gases, meaning it does not damage processing equipment.
Table 1. PEEK processing suitability. PEEK can be processed by several means but is generally is not suitable for blow molding.
Processing Method |
Suitability |
Injection molding |
Yes |
Extrusion
(profiles, films, sheet, tubing, heat shrink tubing, and cable coating) |
Yes |
Blow molding |
No |
Compression molding
(overmolding, etc.) |
Yes |
Impregnation and coating |
Yes (as coating) |
The rate at which PEEK is cooled has a significant impact on the crystallinity, and therefore mechanical properties, of the final product. If PEEK is cooled rapidly it will be less crystalline, i.e. more amorphous, and have a more transparent appearance. If PEEK is cooled slowly it will have a more crystalline structure with an opaque appearance. In order to prevent the formation of voids or bubbles in PEEK components the polymer should be fully dried prior to processing.4
PEEK Properties
Physical and Mechanical
PEEK is a popular material because of its combination of good mechanical behavior in terms of strength, toughness, creep and stiffness.5-7 Similarly to other semi-crystalline polymers the properties of PEEK are dependent on its crystallinity. PEEK has an elastic modulus comparable to the bones of humans, making it a popular choice for implants.
PEEK’s working temperature is higher than the majority of most commercial polymers (including some fluoropolymers); though it tends to have a lower density than other high performing polymers; with the exception of nylons and polyethylenes. PEEK’s low density means it can be used to produce low-weight components.
The chemical resistivity of PEEK means it can be used as a medical implant or in challenging industrial environments. When used in implants PEEK can be sterilized using methods use as gamma irradiation, autoclaving or ethylene oxide (ETO) sterilization.10,11
The combination of a relatively low weight with exceptional mechanical and physical behavior makes PEEK a popular alternative to other commercial polymers (Table 2), with it considered a high-performance thermoplastic. Even at temperatures close to (or sometimes exceeding) its working temperature PEEK retains many of its desirable mechanical properties; including impact, flexural and tensile strength (Table 3).7
Table 2. PEEK typical physical properties. PEEK’s physical properties support its use in areas ranging from harsh chemical environments to medical applications. (Methods are ASTM test standards except where indicated or by *).
Property |
ASTM |
Value (natural polymer) |
Appearance |
– |
Opaque; light tan or brown |
Density (g/cm3) |
D792 |
1.3 |
Specific Gravity (23 °C) |
D792 |
1.3 |
Water Absorption (50% rh; %) |
D570 / ISO 62-1 |
0.07* – 0.45* |
Refraction Index |
D542 |
1.67 |
Limiting Oxygen Index (LOI) 3.2 mm thickness |
D2863 |
35 |
Biocompatible |
USP Class VI |
Yes |
Chemical Resistance |
– |
Excellent |
Sterilization |
– |
Autoclave, Gamma, ETO |
Table 3. Typical PEEK mechanical properties. PEEK exhibits exceptional mechanical properties as a thermoplastic. Several PEEK properties are retained at temperatures above PEEK’s typical maximum service temperature.
Property |
ASTM |
Value (natural polymer) |
Tensile Strength (MPa) |
D638 |
99 |
Elongation at Break (%) |
D638 |
40 – 45 |
Modulus of Elasticity (GPa) |
D638 |
3.7 – 4.0 |
Flexural Modulus (GPa) |
D790 |
3.8 – 4.2 |
Flexural Strength (MPa) |
ISO 178 / D790 |
125 – 165 |
Hardness (Shore D) |
D2240 |
84.5 |
Impact Strength (23 °C; kJ/m)
notched
unnotched |
ISO 180 |
8.0
No Break |
Coefficient of Friction |
D1894 |
0.58 |
PEEK is an appropriate material with which to make components for use in high-friction environments because it is resistant to wear. In addition, PEEK can withstand exposure to high doses of gamma radiation, allowing it to undergo radioactive sterilization – alongside PEEK’s previously mentioned biocompatibility this makes it even more useful for implants. Despite strong gamma resistivity PEEK is sensitive to UV radiation meaning it is not as suitable for outdoor applications as other polymers.12
Exposure to UV radiation can result in the polymer becoming embrittled.13,14 One way around this is the use of a carbon additive to provide UV resistance.
Thermal
PEEK displays exceptional thermal stability (Table 4) with degradation and outgassing only occurring at temperatures significantly higher than the melt temperature.7 The thermal stability of PEEK makes it more processable as it improves its viscous flow when melted. In addition, the relatively low thermal expansion coefficient of PEEK means components produced from the polymer display a good thermal stability over large temperature ranges.
Table 4. PEEK thermal properties. PEEK exhibits a large operating temperature window and resists burning and outgassing. (Methods are ASTM test standards except where indicated).
Property |
Method |
Value (natural polymer) |
Thermal Conductivity (W/m-K) |
D433/ISO 22007-4/C-177 |
0.29 – 0.32 |
Maximum Service Temperature (°C) |
UL 746 |
260 |
Minimum Service Temperature (°C) |
UL 746 |
-70 |
Melting Point (°C) |
D4591/D3418/ISO 12086/DOW Method |
343 |
Glass Transition Temperature (°C) |
E1356 (DSC) or E1545 (mechanical) |
143 |
Decomposition Temperature (°C) |
E1131 |
541 |
Coefficient of Thermal Expansion, Linear (µm/m-°C) |
D696 |
45 |
Flammability Rating (UL 94) |
D2863 |
V-0 |
PEEK has a low surface temperature of at least −70 °C (−94 °F)15,16 and, like the majority of plastics, at very low temperatures PEEK is more brittle.
Electrical
PEEK displays excellent insulating properties (Table 5). As all of the bonding modes in PEEK are covalent, with no mobile electrons, the polymer can be polarized in the presence of an electronic field. This behavior, in addition to the fact that PEEK is halogen-free, means that it can be used for the storage of electronic energy and behave as a dielectric material.
Table 5. PEEK electrical properties. PEEK’s covalent bonding and aryl moieties allow it to function as a dielectric (insulator) and store electrical energy. (Methods are ASTM except where indicated).
Property |
ASTM |
Value (natural polymer) |
Dielectric Constant (1 MHz) |
D150 |
2.2 – 2.8 |
Dielectric Strength (V/mil) |
D149/IEC 60243-1 |
584.2 |
Volume Resistivity (Ω–cm) |
D257/IEC 60096 |
4.9 × 1016 |
The breakdown voltage of PEEK is the voltage at which the polymer begins to breakdown. This term is also called the dielectric strength, as the higher this value is the better a material is at behaving as an insulator. The dielectric behavior or PEEK, when considered alongside its exceptional mechanical properties, is the reason PEEK is found in so many different electrical applications.
Finishing
Components produced using PEEK can be shaped into many different types and forms; including sheets, piping and tubing, monofilament fibers, and films. In fact, it is possible to shape PEEK into almost any form possible using metal.
The machining of PEEK can be achieved using standard methods and systems, with most vendors providing methodology for PEEK processing. As polymers such as PEEK can be susceptible to stresses during the machining process it is common to incorporate some annealing steps into the machining process to alleviate this. Additionally, the level of mechanical and thermal stress applied to PEEK during the process should be monitored to ensure no warping or deformations occur.4
PEEK can easily be shaped into new forms and configurations for use in a huge range of both common and technical applications.
Applications
Extrusion engineered PEEK components are some of the best performing thermoplastics, being able to even compete with fluoropolymers. However, it is the high processability of PEEK that makes it different from other polymers and makes it so useful in specialist applications (Table 6).
Table 6. Survey of PEEK applications. With its retention of several key properties at temperature extremes, its chemical resistance, and heat shrinkable options, PEEK is one of the most widely utilized commercial plastics.
Application or Industry |
Key Benefits |
Oil and gas |
Chemical, heat resistance |
Fiber optics |
Thermally stability, data transfer integrity |
Fluid management |
Chemical resistance |
Wire and cable insulation |
Abrasion resistance, dielectrics |
General industrial |
Toughness, machinable |
Heat shrink |
Encapsulation, connector protection |
Replacement for metal |
Weight savings |
Braiding
|
Strength reinforcement |
When used in tubing, PEEK’s high chemical inertness means it can be used for fluid management without contamination of the fluid that it is containing. As explored previously, the halogen-free constitution of PEEK makes it highly useful in dielectric applications; with wires, slot liners and phases insulated by PEEK having been demonstrated to improve the performance of motors when used concurrently.17
When applied as a spray for coating applications PEEK can be used in aqueous environments to protect components from corrosion, or for dielectric purposes.18 Heat shrinkable PEEK, such as Zeus’ PEEKshrink®, can also be produced for the protection of connectors, wiring and splices. The insulating properties of PEEK make it useful in surface mounted potentiometers and several kinds of switches. In addition, the dielectric behavior of PEEK means it can be used in electric circuits that process low-intensity outputs and signals.
It is possible to use fibers produced from PEEK as braiding reinforcements in tubing such as catheters and hoses. PEEK’s thermal stability is also advantageous for optical fiber coating applications, where it improves the optical sensing of the system.19
In addition, the low outgassing of PEEK means that thermal and chemical sensors protected using a PEEK coating are less likely to be impacted by chemicals leeched by PEEK. PEEK protected systems can bring new advantages to any components designed for use in harsh chemical, electrical or thermal environments.
Summary
PEEK polymer is now used globally in industries ranging from aerospace, automotive, oil and gas, fiber optics, alternative energy, to medical. Thought of as one of the best performing materials, this relative newcomer to the thermoplastics industry can be extruded, injection molded, or used as a coating.
PEEK’s aryl and ketone moieties support its thermal stability during both the melt processing stage and as finished parts. Electrical industries prefer PEEK due to these same features resulting in high dielectric strength and insulating capabilities.
Aside from its ability to abide harsh industrial chemical environments, PEEK’s chemical resistance also means that it does not react when used in the body. Additionally, PEEK exhibits many similar mechanical attributes to bone. As a final benefit of PEEK, its rugged mechanical attributes and machinability allow it to replace heavier metal parts in many applications where weight savings is vital. In its relatively short commercial lifetime, PEEK has proven to be an incredibly valuable material from the toughest to the most sensitive environments (Table 7).
Table 7: PEEK advantages and limitations. PEEK offers many mechanical benefits including strength even at elevated temperatures. PEEK’s chemical resistance and bone-like traits make it especially adapted to medical uses and prosthetics.
Advantages / Benefits (+) |
Limitations (–) |
- High temperature tolerance (260 °C/500 °F)
- Excellent chemical resistance
- Retention of mechanical attributes
- High dielectric strength Zero halogen structure
- Can replace some metals; comparatively light-weight
- Melt processable
|
- Requires high processing temperatures
- Low impact strength
- Low UV resistance
- Cost
|
References
- Yao F, Zheng J, Qi M, Wang W, Qi Z: The thermal decomposition kinetics of poly(ether-ether-ketone) (PEEK) and its carbon fiber composite. Thermochimica Acta 1991, 183:91-97.
- Rose JB: Production of aromatic polyketones. In: US Patent US4396755 (A). C08G61/00; C08G61/12; C08G65/00; C08G67/00; (IPC1-7): C08G67/00 edn. United States: Imperial Chemical Industries Ltd.; 1983.
- Mullins MJ, Woo EP: The Synthesis and Properties of Poly(Aromatic Ketones). Journal of Macromolecular Science, Part C 1987, 27(2):313-341.
- PEEK Processing Guide. In.: Victrex; 2004.
- Lu S, Cebe P, Capel M: Thermal stability and thermal expansion studies of PEEK and related polyimides, vol. 37; 1996.
- Jenkins MJ: Relaxation behaviour in blends of PEEK and PEI, vol. 41; 2000.
- PEEK Materials Properties Guide. In.: Victrex; 2012.
- Kurtz SM: Chapter 1 - An Overview of PEEK Biomaterials. In: PEEK Biomaterials Handbook. Edited by Kurtz SM. Oxford: William Andrew Publishing; 2012: 1-7.
- Garcia-Gonzalez D, Jayamohan J, Sotiropoulos SN, Yoon SH, Cook J, Siviour CR, Arias A, Jerusalem A: On the mechanical behaviour of PEEK and HA cranial implants under impact loading. Journal of the mechanical behavior of biomedical materials 2017, 69:342-354.
- Monich PR, Berti FV, Porto LM, Henriques B, Novaes de Oliveira AP, Fredel MC, Souza JCM: Physicochemical and biological assessment of PEEK composites embedding natural amorphous silica fibers for biomedical applications. Materials science & engineering C, Materials for biological applications 2017, 79:354-362.
- Sheiko N, Kékicheff P, Marie P, Schmutz M, Jacomine L, Perrin-Schmitt F: PEEK (polyether-ether-ketone)-coated nitinol wire: Film stability for biocompatibility applications. Applied Surface Science 2016, 389:651-665.
- Page D: Neutron and Gamma Radiation Effects On The Viscoelastic Behavior Of Poly(aryl ether ether ketone). Kingston, Ontario: Royal Military College of Canada; 1997.
- Mylläri V, Ruoko T-P, Järvelä P: The effects of UV irradiation to polyetheretherketone fibres – Characterization by different techniques. Polymer Degradation and Stability 2014, 109:278-284.
- Nakamura H, Nakamura T, Noguchi T, Imagawa K: Photodegradation of PEEK sheets under tensile stress. Polymer Degradation and Stability 2006, 91(4):740-746.
- AZoM: Supplier Data - Polyetheretherketone (PEEK). In.: Goodfellow; 2003.
- PEEK - Polyetheretherketone. In.: DesignerData (Promolding BV).
- Bigham KJ: Test Report: Impact On Low Voltage Motor Performance. In. https://www.zeusinc.com/; 2016: 8.
- Normand B, Takenouti H, Keddam M, Liao H, Monteil G, Coddet C: Electrochemical impedance spectroscopy and dielectric properties of polymer: application to PEEK thermally sprayed coating. Electrochimica Acta 2004, 49(17):2981-2986.
- Davis M, Fant J: Test Report: PEEK Coated Optical Fiber Evaluation. In. Edited by Bigham KJ. https://www.zeusinc.com/; 2016: 10.
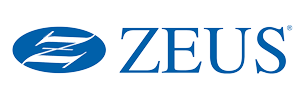
This information has been sourced, reviewed and adapted from materials provided by Zeus.
For more information on this source, please visit Zeus.