From the perspective of a customer, a good quality part is one that exactly meets their specifications. For the manufacturer or fabricator, good quality control means that good quality parts can be produced at the lowest reasonable cost.
Production costs increase when manufacturing processes are out of control and this is considered ‘the cost of poor quality.’ Studies have shown that, on average, the cost of poor quality is around 25%, but this can be as high as 40%. Various factors contribute to the cost of poor quality in manufacturing including scrap, rework and customer returns.
When supplying critical industries like automotive or aerospace, poor quality can cost more than just money if a part fails in the field.
Conversely, good internal quality control can help to minimize replacement and rework costs as well as helping the production environment run more efficiently. It will help determine where time and money are lost and bring processes under control.
As a result, it will help with production planning, on-time delivery and capacity management. Heavy-weight quality methodologies, for example six-sigma, keep work-in-progress and stock levels to a minimum and so help with cash-flow.
Where Can Quality Go Wrong?
It is relatively straightforward to introduce steps to control processes in fabrication or manufacturing. However, as part of a supply chain, any errors made by suppliers can create quality problems unless action is taken to check incoming material.
Using the incorrect alloy in production, for example, could affect the workability of the material, how the part performs or fails to comply with industry legislation. Poor quality can cost the manufacturer anything from the small costs of a reworking a part and sending the part back, to damage to reputation if the part fails widely in the field.
The incorrect alloy might enter production in various ways:
- Certificate or stamp loss
- Wrong alloy from the supplier
- Material mix-ups in the warehouse
- Mixed up or even forged certificates
As a manufacturer, steps can be taken to ensure that the above do not happen and so prevent issues impacting on customers further down the supply chain.
.jpg)
How to Get it Right?
The cost of quality can be minimized by using the correct PMI (positive material identification) equipment because verification and checks can be done easily and quickly. Here’s how:
Incoming Inspection
Verifying incoming materials in order to ensure the quality of raw materials and that the material matches the certificate is straightforward.
In metal production, it is important to verify that the metal meets grade specific limits for trace and main elements in metal production. Similarly, in fabrication, it is critical to ensure what is coming from the metal production company and this includes testing for elemental composition.
The range of stationary and mobile OES analyzers (optical emission spectroscopy) from Hitachi provides high accuracy testing that quickly tests the composition and trace elements of metal alloys. As a result, incoming materials can be verified in seconds in metal manufacturing.
Factory Floor Process Control
Operators can carry out a quick test on the material before machining using a portable analyzer and this ensures that the correct part has been taken from stock in order to avoid material mix-ups. Techniques like this are also useful for checking composition of processed parts in order to double-check your own procedures.
Depending upon material and process, handheld XRF or LIBS analyzers, or mobile OES are appropriate. XRF is an accurate and completely non-destructive test for almost any material, including metal alloys and the Vulcan handheld LIBS analyzer from Hitachi High-Tech can perform alloy identification in one second. Mobile OES can also be used to reliably detect trace elements such as sulfur, carbon or boron in steel or nitrogen in duplex steels.
Final Inspection
XRF is the technique required for final inspections before shipping to the customer because it is non-destructive (NDT). This enables the verification of the material composition and takes any necessary readings for regulatory compliance screening.
The handheld XRF range from Hitachi, the X-MET8000, is perfect for a final inspection environment. Highly accurate readings can be completed in seconds on the drill-sized device and no marks are left on the measured surface.
The range of analyzers from Hitachi High-Tech can be used across the metal production, product manufacturing and fabrication process to help reduce cost and ensure quality control.
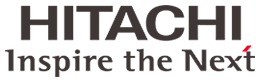
This information has been sourced, reviewed and adapted from materials provided by Hitachi High-Tech Analytical Science.
For more information on this source, please visit Hitachi High-Tech Analytical Science.