Induction heating uniformity problems can cause a number of issues with part quality. Frequently, we see these issues due to irregular heating patterns, as a result of unusual part shape or nontraditional heating needs.
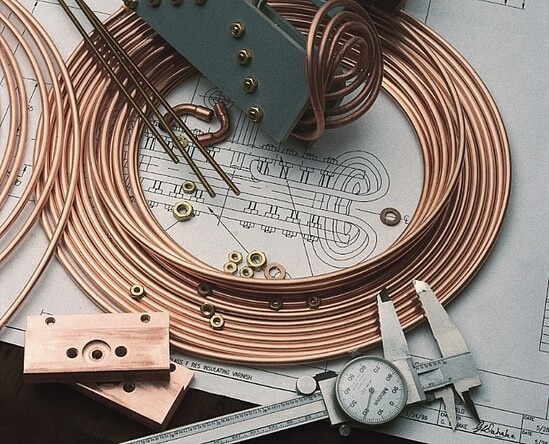
Below are six ways you can augment your heating process or induction coil design to combat common heating uniformity problems are outlined.
1. Taper Your Coil
If the coil extends over the end of a shaft-like part, a deeper pattern is created on the end. The coil must be brought to a point even with or slightly lower than the end of the shaft in order to minimize this effect.
2. Shorten Your Coil
In the heating of a disk or a wheel the same condition is present. If the coil overlaps the part then the depth of heating will be larger at the ends than in the middle. The coil can be shortened, or the diameter at the ends of the coil can be made larger than at the middle, thus decreasing the coupling at the former location.
3. Part Rotation
When the high flux field next to to the coil turns creates a spiral pattern on the part, barber poling occurs. Rotate the workpiece throughout heating to stop barber poling. For the majority of short-duration hardening operations, rotational speeds generating a minimum of 10 revolutions during the heating cycle are ideal.
4. Put Steps in Your Coil
By annealing the coil after winding and pressing it between two boards in a vise, stepping is achieved easily. An even horizontal heating pattern is the final effect, versus a standard coil whose ends would extend higher or lower than the main coil.
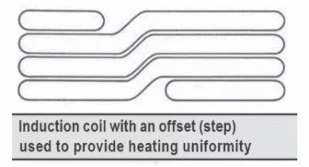
5. Use Flattened Tubing
Using flattened tubing forms a bigger heating surface area for your coil. When employing flattened tubing, coupling distance will decrease and coil OD will be heightened to lessen the spacing between the coil and the workpiece. Flattened tubing should be located so that its larger dimension is adjacent to the workpiece.
6. Use Coil Liners
A coil liner is a sheet of copper brazed or soldered to the inside face of the coil. This liner expands the area over which the current travels, and so a wide field per turn can be produced.
By controlling the dimensions of the liner, the height of this field can be altered in order to suit the application. The current path from the power supply passes through the connecting tubing when a liner is utilized.
The tubing is used solely for conduction cooling of the liner between the two connections. When fabricating coils with liners, it is necessary only to tack-braze the tubing to the liner at the first and last connection points, with extra tacks employed for mechanical strength.
For optimum heat conduction, the common surfaces which remain between tubing and liner can then be filled with a low temperature solder, as the coil-water temperature will never surpass the boiling point of water, which is well below the flow point of the solder. The copper may be unable to conduct heat fast enough from the inside of the coil so this may be necessary.
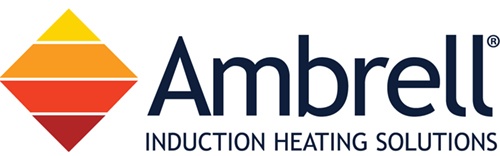
This information has been sourced, reviewed and adapted from materials provided by Ambrell Induction Heating Solutions.
For more information on this source, please visit Ambrell Induction Heating Solutions.