With the ever-increasing demands for higher-performing materials to meet the needs of challenging applications, understanding how a material reacts to its environment is more important than ever. Within the last 18 months, TA Instruments has introduced three all-new instruments that enable scientists to quantify the mechanical characteristics of solid materials: two instruments for dynamic mechanical analysis (DMA) and, most recently, a platform for thermomechanical analysis (TMA), the Discovery Series TMA 450. These instruments complement, and are often found alongside, TA’s market-leading thermal analysis products such as differential scanning calorimetry (DSC) and thermogravimetric analysis (TGA). This article will focus primarily on the Discovery TMA 450 thermomechanical analyzer.
Meeting and exceeding industry standards for testing (ASTM and ISO), the Discovery TMA 450 provides information about the material’s coefficient of linear thermal expansion (CTE), shrinkage, softening, glass transition and phase temperatures, deflection temperature under load and much more. Advanced testing capabilities include TA’s industry-leading Modulated TMATM for the most efficient separation of simultaneous expansion and contraction of a material, Dynamic TMA for viscoelastic properties by small amplitude, fixed-frequency sinusoidal deformation, and Creep/Stress Relaxation for viscoelastic behavior under transient conditions. These advanced options extend and empower scientists and engineers with even more valuable information about the mechanical behavior of materials.
.jpg)
Figure 1. TA Instruments Discovery Series TMA 450
How does the TMA work and what is the most commonly measured parameter?
Thermomechanical analysis (TMA) measures material dimensional changes under controlled conditions of force, atmosphere, time, and temperature. In the typical operation of a TMA, a small sample with parallel and flat surfaces is placed on a quartz stage near a thermocouple. A quartz probe is lowered against the specimen with a constant applied force. As the sample is heated or cooled, changes in dimension are measured by monitoring the motion of the quartz probe.
The most common property measured on a TMA is the coefficient of thermal expansion (CTE) per international standards documented in ASTM E831, D969, D3380 and ISO 11359 Parts 1-3. The CTE describes the mechanical expansion or contraction of a material at different temperatures. It is an important property of a material and neglecting to take into account the effect temperature has on the physical size of materials has been known to cause product failures and delamination. The mean coefficient of thermal expansion (CTE) is calculated as:
.png)
where α is the mean coefficient of thermal expansion, ΔL is the expansion of the specimen (mm) over a specified temperature range, L0 is the initial specimen length (mm), and ΔT is the temperature change (ºC) through the test. The CTE of a material is temperature-dependent, and α is a reported mean for a particular temperature range (figures 2 and 3).
.png)
Figure 2. Dimensional change versus temperature.
.png)
Figure 3. An overlay of dimensional change and CTE for various materials.
Another common test on the TMA would be the determination of the Heat Deflection Temperature (HDT) and Deflection Temperature Under Load (DTUL) which reflect the temperature at which a material subjected to a 3-point bending load deforms to a pre-determined position. ASTM standard E2092, and a related standard D648, defines DTUL as the temperature at which a precise strain (either 0.25 mm deflection or 0.20% strain as defined by sample dimensions in the procedure*) occurs under a specific stress (either 455 or 1820 kPa).
Deflection temperature under load (DTUL) testing is easily conducted on the Discovery 450 TMA. Polystyrene, polysulfone, and polyphenylene sulfide were tested using the three-point flexure probe with a 0.455 MPa (66psi) load, 0.2% strain, and 2°C/min heating (figure 4). The DTUL measurements of these materials distinguish between their ability to bare a load at elevated temperatures and determine the temperature where rigidity is lost. The deflection temperature of a material can be modified through reformulation with compatible resins and fiber reinforcement. DTUL tests with small specimens are quick and easily conducted on the Discovery TMA 450.
Table 1. Calculated values for experimental force and dimensional change at a center span when using conditions of 0.455 MPa stress and 0.2% strain (per ASTM E2092).
Sample
|
Sample Width (b) x Thickness (d) x Length (L) (mm)
|
Calculated Force, F (N)
|
Dimensional Change at center span, D (μm)
|
Polystyrene
|
2.33 x 1.76 x 5.0
|
0.431
|
4.89
|
Polysulfone
|
2.30 x 1.87 x 5.08
|
0.480
|
4.60
|
Polyphenylene sulfide
|
2.36 x 1.72 x 5.08
|
0.417
|
5.00
|
.png)
Figure 4. DTUL determination with the Discovery TMA 450 in 3-point bending mode.
In addition to determining the coefficient of thermal expansion and deflection temperature, the TMA is extensively used to determine the glass transition or softening temperature of materials; especially of multicomponent and glass-filled composites. Figure 5 represents data obtained on polycarbonate/acrylonitrile-butadiene-styrene (PC/ABS), an amorphous thermoplastic blend, using the penetration fixture, a controlled heating rate of 5 °C/min and a constant force of 0.2 N. Conditions outlined in ASTM E1545 and ISO 11359 were followed in the assignment of the softening temperature/glass transition by penetration. The softening points are easily detected as a negative deflection in dimension change, and individual softening points were observed for each component of this blend indicating the blend immiscibility.
.png)
Figure 5. Softening point determination with the Discovery TMA 450 using the penetration fixture.
Modulated TMA (MTMATM) – An advanced technique delivering benefit in understanding materials properties.
TA’s industry-leading Modulated TMATM efficiently separates simultaneous expansion and contraction in a material. Through deconvolution of the total dimensional change, an event such as the glass transition occurring in the same temperature region as stress relaxation is easily revealed. In Modulated TMA, the sample experiences the combined effects of a sinusoidal temperature oscillation overlaid on the traditional linear ramp. The output signals (after Fourier transformation of the raw data) are total displacement and the change in thermal expansion coefficient. Modulated TMA separates the total displacement into Reversing and Non-Reversing dimensional change signals (figure 6). The reversing signal contains events attributable to dimension changes and is useful in detecting related events such as the Tg. The non-reversing signal contains events that relate to time-dependent kinetic processes (e.g., stress relaxation).
.png)
Figure 6. Schematic of Modulated TMA.
An MTMATM study to determine the glass transition temperature, Tg, of a printed circuit board (PCB) is presented in figure 7. The signals plotted are the total dimension change, plus its reversing and non-reversing components. The total signal is identical to that from standard TMA, but does not uniquely define the Tg as other dimensional changes are occurring simultaneously. The component signals, however, clearly separate the actual Tg from the stress relaxation event induced by the processing conditions of the PCB.
.png)
Figure 7. Modulated TMA of a printed circuit board.
Conclusions
The Discovery TMA 450 is particularly useful for measuring mechanical material properties locally, especially in manufactured components or assemblies where the compatibility of materials is paramount. The TMA 450 delivers premium performance with advanced options and configuration flexibility intended to meet the requirements of the most demanding applications. As with all TA thermal analysis products, TA Instruments backs our promise of reliable products with the industry’s only 5-year furnace warranty.
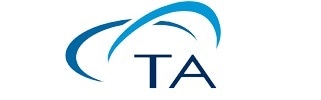
This information has been sourced, reviewed and adapted from materials provided by TA Instruments.
For more information on this source, please visit TA Instruments.