Omniseal Solutions powers many of the world’s mobility from behind the scenes. They provide “mighty” and almost “invisible” critical sealing and polymer solutions. Such solutions are used to move and protect us daily in core systems for automotive, aerospace, space, life sciences and other industries.
.jpg)
This article discusses ten fascinating facts about Omniseal®, Rulon® and Meldin® products and how they make the difference to everyday lives.
Omniseal® Spring-Energized Seal: The Polymer Solution for Extreme Hot & Cold
Fact #1: For Over Sixty Years Omniseal Solutions Has Traveled into Outer Space
Omniseal® RACO® spring-energized seals were used to resolve elastomer seal failures on rocket launches back when NASA was first created in 1958. Over the last 60 years these seals have been used regularly on missions to space in the main engine, life support, and tanks with hypergolic fuels due to their proven ability to handle cryogenic and high temperatures. The seals have travelled over 500 million miles over 132 space shuttle missions since the first human spaceflight. The seals have also been used on:
- The Atlas V rocket that launched the Mars Rover Curiosity in 2012. The rover is still actively exploring Mars and its progress can be followed through the Mars Curiosity Rover Twitter account. Interestingly Omniseal Solutions Rulon® ball bearings were also used on the Curiosity drilling tools.
- The Delta IV heavy rocket in the slip joint system in 2013. Known for its delivery of exceptionally demanding payloads the heavy rocket is the most powerful rocket currently flying. This will be surpassed in 2021 when the Space Launch System (SLS) rocket is launched. Omniseal Solutions huge six foot wide cryogenic seals are also on this incredible rocket!
- The longest continuous human presence in low Earth orbit - the International Space Station from 1998 to the present day. There are thousands of seals on the station, for example in core systems supporting the astronauts' lives plus experimental equipment used to conduct testing.
- The Falcon Heavy launched in 2018 with a Tesla vehicle. The rocket is actually three rockets in one. There have been nine different Falcon rockets and the seals have been used in every one.
Fact #2: Omniseal Solutions Has Gone Deep into the Ocean on the First ever Subsea Gas Compression Station
A collaboration between Omniseal Solutions oil and gas team and a key customer on the world’s first subsea gas compression station resulted in the installation in the Åsgard field offshore Norway in 2015. The customer has invested 11 million man-hours on the Åsgard project, and it required the development of more than 40 new technologies.
Omniseal Solutions spring-energized seals was chosen to provide a reliable tight seal in 3000 meter deep water (9842 feet) and in severe environments with pressures above 15000 psi (1034 bar) and temperatures over 150 °C (302 °F). These seals have been proven to address harsh chemicals, high-pressures, and extreme temperatures in oil and gas exploration. The oil and gas team at Omniseal Solutions has also contributed to the following:
- The development of a technical engineering manual with selection guidelines for polymer lip seals in API 6D isolation valves for a major U.S. oil and gas customer. This was a result of proven success and expertise in leading standards such as NORSOK M710 and API 6A. Widely distributed among operations, this documentation was used to increase awareness of how important seals are in severe service operations.
- In order to lower fugitive emissions in oil and gas Omniseal® spring-energized seals were developed for single stem sealing on quarter-turn valves.
Fact #3: Surgeons Have Been Given More Confidence in One of the First Full-Powered, Reusable Endoscopic Staplers in the World Through Omniseal Solutions
In 2013 the world's first full-powered, reusable endoscopic staplers incorporated Omniseal Solutions Omniseal® seals and Meldin® bearings. Simplified tool design and portability allows for easier installation of surgical staples with these devices. Tight fitting and extremely small seals (¼ inch or smaller) were required to withstand multiple steam autoclave sanitation cycles and low torque operating conditions.
Fact #4: The World's First Supplier of Industrial CO2 Dyeing Equipment Incorporated Omniseal Solutions Rotary Lip Seals and Helped to Protect the Environment
In 2015 spring-energized seals were installed in Netherlands-based DyeCoo’s environmentally-friendly industrial dyeing machines. Billions of gallons of toxic chemicals are prevented from being dumped into waterways using carbon dioxide.
Omniseal® Rotary Lip Seals: The Polymer Solution for Extreme Speed and Caustic Chemicals
Fact #5: Omniseal Solutions Lip Seals are Supporting Firefighters in Combating Wild Fires
A higher rate of wild fires occur in hot weather. Firefighters are using Omniseal Solutions Omniseal® rotary lip seals in pump systems, propelling fluids and foam retardant. Unlike most lip seals, these lip seals will survive the demanding chemicals used.
Fact #6: Omniseal Solutions Lip Seals Have Been Used on Track During “Superfast” Racing Competitions
Widely used in the racing industry, these rotary lip seals are installed in crankshaft, distributor, fuel pump, and cam seal applications. They are used by many NASCAR teams and in Indianapolis car engines. At Indianapolis this year all of the top qualifiers and finishers used lip seals in at least the front and rear crank shaft. A specific design created for NASCAR was patented to address frequent problems causing PTFE split seals to fail.
Fact #7: The Auxiliary Power Unit on US Airways Flight 1549 was Protected by Omniseal Solutions Lip Seals
US Airways Flight 1549 (Miracle on the Hudson) deployed the Auxiliary Power Unit (APU) to provide electrical power and to help land the plane safely. Considered critical to flight, this system must work 100% of the time. Omniseal Solutions lip and spring-energized seals were installed in this core system.
Rulon® PTFE Materials: The Polymer Solution for Extreme Wear and Tear
Fact #8: When Earthquakes Strike Omniseal Solutions PTFE Materials are Providing a Strong Foundation
Well known buildings in Japan employ selsmic systems which for many years have used Rulon® materials. Recently California has been hit with several earthquakes and so this technology may also prove useful there.
A laminated bearing with a sliding mechanism make up the sliding seismic isolation units, which are installed between the ground and upper structure. When an earthquake strikes these offer low friction, high resistance to wear, and resistance to deformation. The building is detached from the ground using isolation materials. This results in reduced motions that don’t transmit up through the building.
Omniseal Solutions PTFE materials are also used for the following:
- To protect cable connections under the road on the world’s largest suspension bridge from earthquake and wind and wave vibrations
- In several hospitals
- Protecting the grandstand roof on a leading Japanese baseball stadium
Fact #9: Many Places to Eat, Play and Travel Use Omniseal Solutions PTFE Materials
Rulon® 641 bearings are being employed in many restaurants in industrial equipment like fryers where heat is an issue. Manufactured from FDA and USDA compliant materials this specific grade is perfect for food processing applications.
The PTFE Rulon® J material has been used on trains. For example, in order to make the train more stable they were used as sliding elements on the bogie of the 7000 series trains in Washington DC. Selected for their wear and friction properties, Rulon® J materials are also hidden in the brake calipers and seat belt retractors on rollercoasters and rides at amusement parks.
The PTFE material is also used in higher-end bicycle suspension systems to improve the performance of the bicycle’s rear shock absorber and increase comfort for the rider. Improved control and traction, and therefore a safer ride, is achieved through the use of bicycle suspension systems that help to keep one or both wheels in contact with the ground – a particular advantage when riding a mountain bike over rough terrain.
Meldin® Thermoplastic Parts: The Polymer Solution for Tolerance and Efficiency
Fact #10: A KA-Raceing Team Won Formula Student Germany
With The Help of Omniseal Solutions Thermoplastic Parts
The Formula Student Electric KA-Raceing team at the University of Karlsruhe in Germany had full support of Omniseal Solutions automotive team when they sponsored them and their winning KIT16e electric racecar. Although they had competed in competitions since 2007 this was the first time they had won.
Meldin® 4000 thrust washers, designed specifically for the racecar’s gearbox, were selected due to their excellent tribological and mechanical critical properties. They have a temperature range from cryogenic through +600 °F (+316 °C) for continuous operation and can be used intermittently up to +900 °F (+482 °C).
Formula 1 cars and MotoGP motorbikes have also used Meldin® 5330 gerotors in oil and scavaging pumps. A combination of the words “generated” and “rotor”, the gerotor is a positive displacement pumping unit consisting of two elements - an inner rotor and an outer rotor. There is an additional tooth on the outer rotor in comparison to the inner rotor. The central axis of the outer rotor is positioned at a fixed eccentricity from that of the inner rotor and the shaft.
Typical working conditions in this type of motorsport application include temperatures of approximately 150 °C, low pressure of a few bar and high speed of over 20,000 RPM. It has an aluminium counter surface and oil provides lubrication.
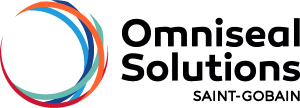
This information has been sourced, reviewed and adapted from materials provided by Omniseal Solutions.
For more information on this source, please visit Omniseal Solutions.