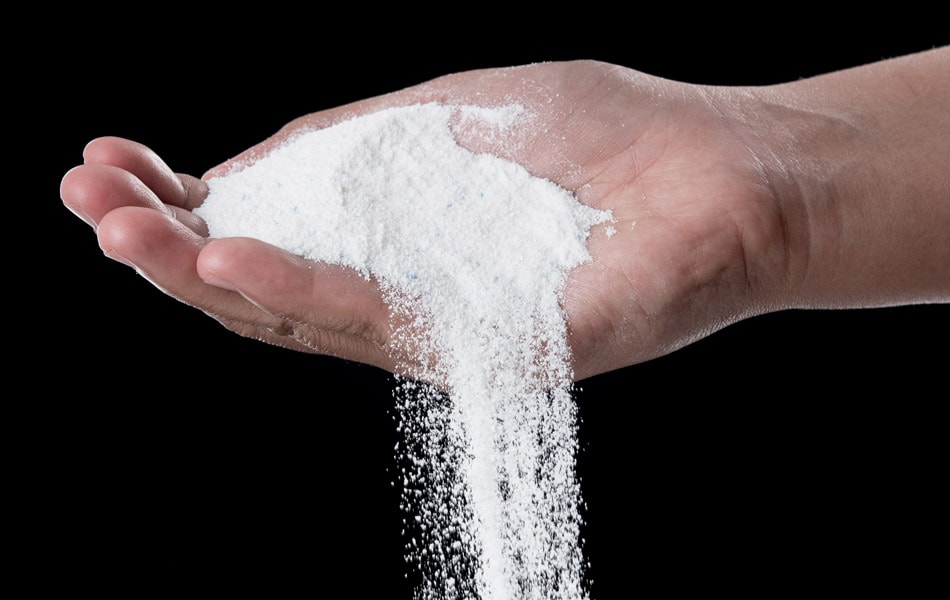
Image Credit: Stable Micro Systems Ltd
It has been estimated that powders account for 50% of materials used in industry. Handling and processing of powders, particulates and granules is central to, among others, food and drink processing, paints, coatings and adhesives, and pharmaceutical industries. But these procedures have traditionally been fraught with problems due to their unpredictable and irregular behaviour, specifically with respect to flowability.
Many common manufacturing problems are attributed to incorrect powder flow, including non-uniformity (segregation) in blending, under or over-dosage, inaccurate filling and obstructions and stoppages. These in turn lead to excessive rejected material, machine downtime and defective end-products. Storage, handling, production, packing, distribution and end use can all be negatively affected by common powder flow problems.
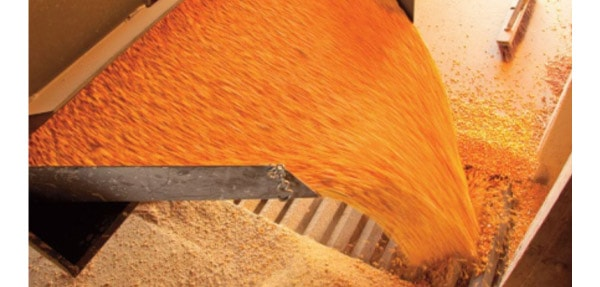
Flowability is key to avoid manufacturing downtime. Image Credit: Stable Micro Systems Ltd
With so many raw materials, semi-finished and finished products in powder form, this sector stands to gain significant manufacturing and commercial benefits from improvements in the assessment of powder flow. Knowing a powder's characteristics and the factors which impact on it is essential. This allows the optimisation of formulation, equipment and incorporates quality control principles throughout production, thereby assisting in process design, performance evaluation and troubleshooting.
Whilst any method of assessing powder flow will take time, the benefits to be gained can far outweigh this delay in proceedings. For example, product development teams can evaluate new constituents and ingredients and predict their behaviour prior to commencing large scale production. They can also check how new powders interact with existing constituents, manufacturing procedures and equipment. This speeds up development time and minimises trial and error tactics. This in turn maximises speed of production, reduces the risk of stoppages and improves blend quality, filling procedures and end product quality. A number of end products that reach consumers need certain consideration of flowability, as well. For instance, while pouring a product like artificial sweetening powder from a jar, lumps and cakes will give the product a low-quality impression.
Accurate Flow Measurement
A Powder Flow Analyser (PFA) is the most suitable way to evaluate the flow behaviour of powder. Stable Micro Systems has replaced conventional manual pouring techniques by patenting a helix blade design that regulates the flow of a powder sample.
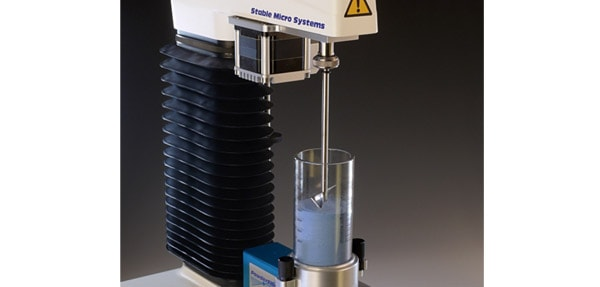
Powder Flow Analyser for the measurement of powder flowability. Image Credit: Stable Micro Systems Ltd
The sample movement is caused by a rotor or blade, which is passed via a powder column based on the settings fixed by the user – both rotating and moving vertically. This process conditions the powder and removes any loading variation between operators. It offers a basic quality control test for differences between sources and/or batches.
Exponent software is integral to the Texture Analyser and Powder Flow Analyser and performs real-time display of data. Tests are configured rapidly and easily, and data analysis is set up to automatically gather critical parameters from each test in simple or advanced ways.
A wide array of methods can be used to perform many different tests on the Powder Flow Analyser:
Caking Test
This is the propensity of a powder to develop large agglomerates during transportation and storage. A powder’s tendency to form a cake is closely associated with its cohesiveness. The cake’s strength will rely on several factors such as particle-to-particle interactions, packing efficiency, and humidity. Understanding the caking properties of a powder are important as most powders will be stored in hoppers or silos, or transported at some point in the production process. A powder that cakes easily and forms a strong cake may not discharge easily from a silo when required. However, the caking process can be intentional and a desired result such as in a granulation process or when required to form a ‘cake’. The caking test smoothly compacts the powder column to a force preset by the user, and then slices back to the top of the column with the least disturbance, before re-compacting. This is repeated for the set number of cycles, and then, the compacted cake is sliced by the rotor blade. Column and cake height ratios, cake strength work and mean cake strength force are measured as indicative parameters.
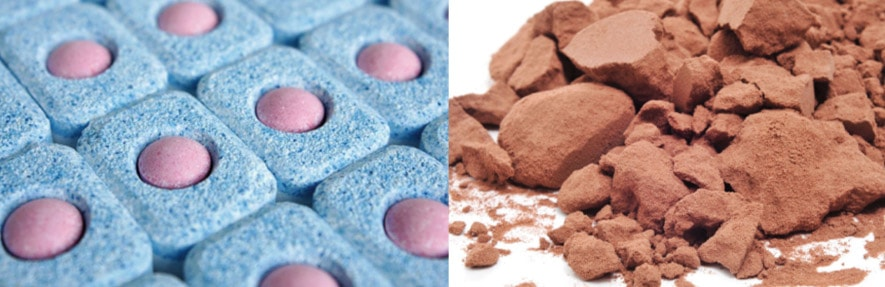
Examples of caking when you need it and when you don’t want it. Image Credit: Stable Micro Systems Ltd
Cohesion Test
Cohesiveness is the propensity of the particles of powder to stick together and agglomerate (develop larger clusters of particles). The PFA quantifies this cohesion feature by operating the blade such that the powder is lifted. A more cohesive powder will stick to itself and to the blade, thereby decreasing the force applied on the base of the vessel. A change in the cohesive properties of a powder may have an important effect on production processes such as die filling that could impair production efficiency and product quality.
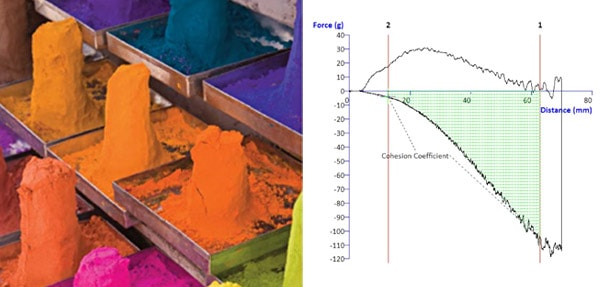
A cohesive powder and a typical graph showing area where cohesiveness is quantified. Image Credit: Stable Micro Systems Ltd
Powder Flow Speed Dependence Test
The flow properties of powder may change with decreasing or increasing flow speeds. For instance, a powder may turn highly resistant to flow as it is pushed to flow faster. Alternatively, it may become free-flowing as the flow speed intensifies. This issue can result in under- or overfilling due to process changes to match increased output demand. The PFA quantifies this property by evaluating the force needed to move the blade through the powder at accelerating speeds.
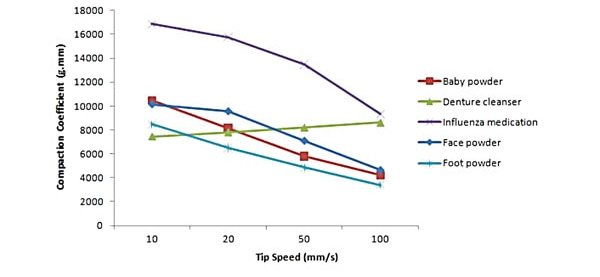
Graphs comparing dependence on flow speed for a variety of powders. Image Credit: Stable Micro Systems Ltd
Bulk Density Measurement
A vessel that divides into two with a hinge is available to help remove excess powder (after conditioning) and leaves behind a particular volume. The PFA’s ability to measure weight enables the automatic calculation of bulk density. In the case of solid objects, density is the ratio between volume and mass. The structure of powders is highly variable, however; therefore, their density can be freely modified by alterations to their packing. The conditioning cycles on the PFA facilitate a reproducible density measurement by treating each powder sample in a repeatable and systematic way prior to each test. At the time of the conditioning process, filling stresses and variances in filling methods are eliminated by directing the blade to slice/aerate (lift) via the sample. This creates an even sample, which supports comparison and repeatability of results.
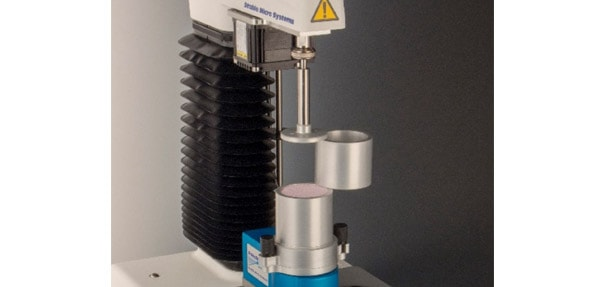
Bulk Density can also be measured by using an alternative vessel. Image Credit: Stable Micro Systems Ltd
The above methods are a summary of example tests that can be performed on a Powder Flow Analyser. However, a number of other tests are available and complete flexibility of the operation of the blade movement allows for development of alternative methods bespoke to an operator’s testing needs.

This information has been sourced, reviewed and adapted from materials provided by Stable Micro Systems Ltd.
For more information on this source, please visit Stable Micro Systems Ltd.