Cyclic voltammetric stripping (CVS) analysis can be used to facilitate the detection of mercaptopropylsulfonic acid (MPS). MPS is the breakdown product of bis(sodiumsulfopropyl)disulfide (SPS), an additive used in acid copper plating baths that quickens copper electrodeposition.
Where oxygen is present, MPS can quickly decompose in acid copper sulfate baths. This means that the CVS stripping peak area (Ar) will decrease in the following cycles. The slope of a plot of Ar vs. log of the CVS cycle number (or time) can provide a measurement of the original MPS concentration.
The Damascene electrodepositing process involves the use of acid copper sulfate baths, with Cu within the fine trenches and vias in dielectric material on semiconductor chips.1 In order to deliver bottom-up filling of the Damascene features, two organic additives are required.
A suppressor additive adsorbs firmly onto the Cu cathode surface. This is usually a high molecular-weight polyalkene glycol such as PEG. Because a chloride ion is present, a film that sharply increases the overpotential for Cu deposition will be formed.
An anti-suppressor or accelerator additive counteracts the effect of the suppressor additive. This provides the accelerated deposition within trenches and vias necessary for bottom-up filling.
Damascene plating requires close organic additive control. This can be achieved using Cyclic Voltammetric Stripping (CVS) analysis, a process that involves the alternate plating and stripping of Cu at a Pt rotating disk electrode.
The presence of additives can be determined from the effect that they exert on the electrodeposition rate, measured via the Cu stripping peak area (Ar).
Accelerator concentration can typically be determined by using either a linear approximation technique (LAT) or a modified linear approximation technique (MLAT).2
Additive species break down into ‘breakdown products’ during a Damascene Cu plating process. This may, in turn, affect the electrodeposition process, and as a result, breakdown products must be controlled to ensure high-quality Damascene deposits.
A process whereby suppressor breakdown can be detected has been explored in previous publications.3,4 This article outlines the detection of accelerator additives’ breakdown products widely found in Damascene copper plating. This detection is achieved through the use of CVS.
The results presented below are for the 3-mercaptopropylsulfonic acid (MPS) species. This is a breakdown product of the bis(sodiumsulfopropyl)disulfide (SPS) additive.5
Experimental Details
A QUALILAB® ELITE plating bath analyzer from ECI Technology, Inc. was used to obtain CVS measurements. A polyethylene beaker cell was also employed. This was open to the atmosphere and contained 50 mL of solution.
In some experiments, the cell was partially sealed and deaerated via nitrogen bubbling (halted during CVS measurements). This was to confirm that oxygen plays a role in MSA decomposition,
The supporting electrolyte contained the following: 40 g/L Cu, which was added as CuSO4 .5 H2O, 10 g/L H2SO4, 50 ppm chloride ion, and 2.0 g/L of 5000 molecular weight (MW) polyethylene glycol from Aldrich.
The MPS and SPS materials were obtained commercially from Raschig Chemical in Germany. The working electrode was comprised of a Pt rotating disk (4 mm diameter, 2500 rpm).
Unless stated otherwise, the potential was scanned at 100 mV/s between a positive limit of +1.575 V and a negative limit of either -0.225 and -0.325 V vs. SSCE-M. The standard silver-silver chloride electrode was altered by substituting the solution with a saturated AgCl solution also containing 0.1 M KCl and 10 volume% sulfuric acid.
A stainless steel rod of 6 mm diameter was generally employed as a counter electrode. During CVS measurements, the solution temperature was controlled at 24 °C within +0.5 °C while SPS and MPS samples were injected into the cell at the positive limit in the CVS cycle.
The effects of the two commercial additives were also investigated at normal concentrations. These were Viaform™ from Enthone Inc. and Ultrafill™ from Shipley, Inc.
Results and Discussion
MPS Analysis Method
It was found that Ar measured on the first CVS cycle (following addition of MPS to the acid copper electrolyte) varied monotonically with MPS concentration (Figure 1). A basic Ar measurement is not suitable for use with MPS analysis, however. Organic additives and other species in plating baths may also impact Ar values.
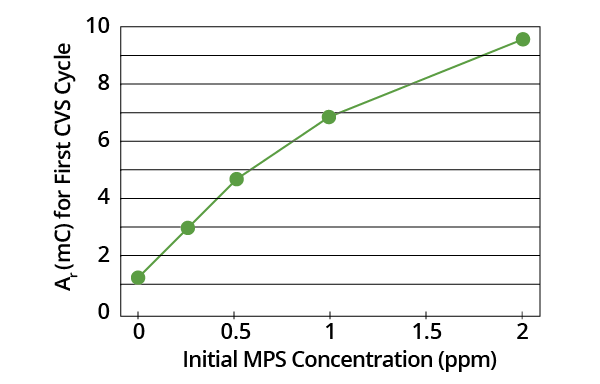
Figure 1. Plot of Ar for first CVS cycle as a function of initial MPS concentration in acid copper electrolyte (-0.225 V limit). Image Credit: ECI Technology
Ar remained a constant where acid copper baths contained SPS only. It decreased monotonically with potential cycling in the presence of the MPS breakdown product (Figure 2).
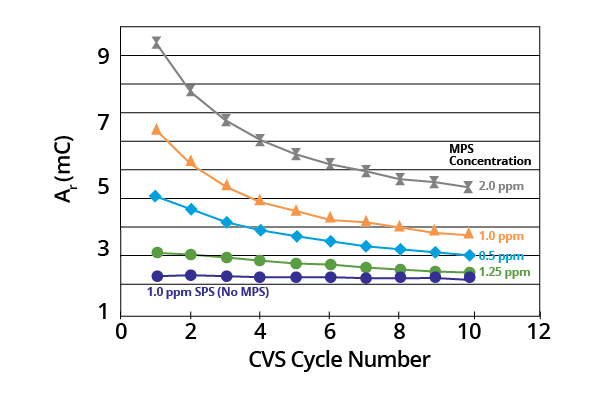
Figure 2. Plots of Ar as a function of CVS cycle number for acid copper supporting electrolyte containing SPS or various concentrations of MPS (–0.225 V limit). Image Credit: ECI Technology
The accelerant effect of MPS is stronger and much more time-dependent, though each compound tended to accelerate the copper deposition rate. When Viaform™ and Ultrafill™ accelerator additives were introduced at the standard concentrations, the Ar values were also constant (not shown).
It was found that the Ar values were smaller (1.5 and 1.4, respectively) than the value of 2.2 noted for SPS at 1.0 ppm concentration.
The CVS cycle corresponded to 38 seconds, and copper deposition occurred over a time frame of approximately 6 seconds for the potential scan rate and limits used. MPS and SPS specimens were injected at the positive potential limit.
As a result, the copper deposition rate measurement for cycle number 1 began after approximately 16 seconds and ended at approximately 22 seconds. Onset for copper deposition is around 0.0 V vs. SSCE-M).
The data suggest that MPS decomposes rapidly when its concentration is high. It also indicates that this happens much more slowly as its concentration decreases. The effects of delaying CVS cycling after the addition of the MPS sample and of interrupting CVS cycling can be seen in Figures 3 and 4.
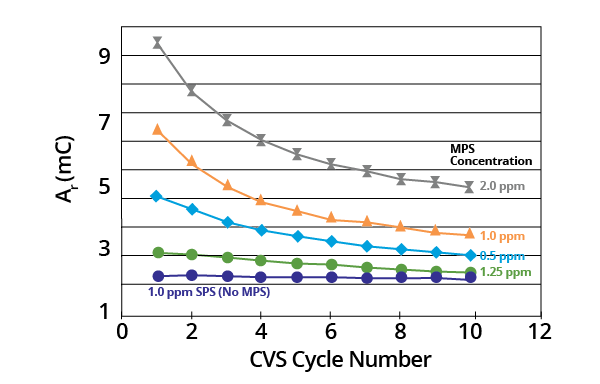
Figure 3. Effects of delays and interruptions in CVS cycling on plots of Ar as a function of CVS cycle number for acid copper supporting electrolyte containing 1.0 ppm MPS (–0.325 V limit). Image Credit: ECI Technology
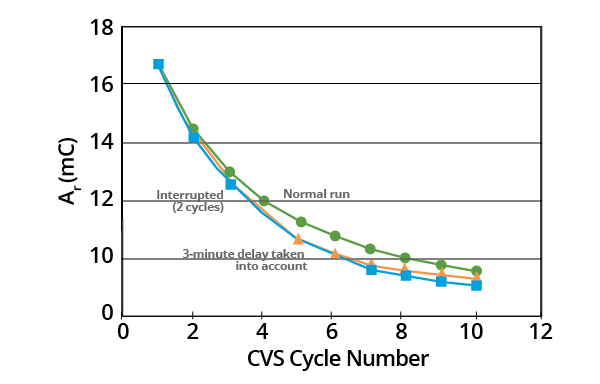
Figure 4. Plots of Ar vs. CVS cycle number for which a 3-minute delay was taken into account by shifting the first data point to the 5th cycle (conditions same as Fig. 3). Image Credit: ECI Technology
It should be noted that a comparatively negative potential scan limit of -0.325 V was employed to enhance the sensitivity of the measurement. Ar continued to decrease, even where no voltage was applied to the working and counter electrodes. This result indicates that MPS is decomposed chemically within the bath.
Where the commencement of the curve for a 3-minute delay was shifted to the 5th CVS cycle (corresponding to 3.2 minutes), the 3-minute delay curve virtually coincided with the curve whereby cycling had been interrupted for two cycles (Figure 4).
Potential cycling would appear to slow MPS decomposition – a possible result of SPS formation.
When compared against a stainless steel electrode, an exposed copper counter electrode tended to increase the rate of MPS decomposition. The same result was observed in tests where a copper electrode was utilized and partitioned from the electrolyte via a double-junction glass frit.
This effect is relatively small, however, and may be a result of the adsorption of MPS on the relatively large copper counter electrode.
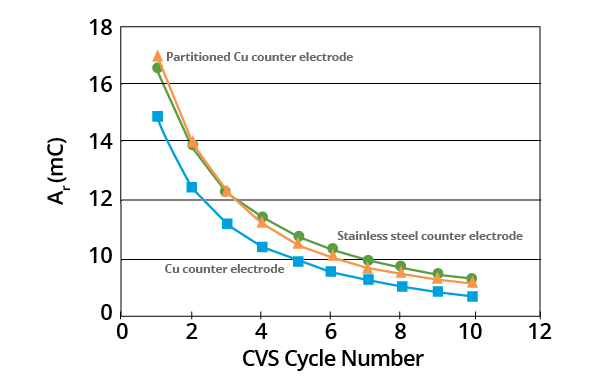
Figure 5. Effects of counter electrode on plots of Ar as a function of CVS cycle number for acid copper supporting electrolyte containing 1.0 ppm MPS (–0.325 V limit). Image Credit: ECI Technology
The observed decrease in Ar after MPS additions were found to be exponential as a plot of Ar vs. Log (CVS cycle number) is linear (Figure 6).
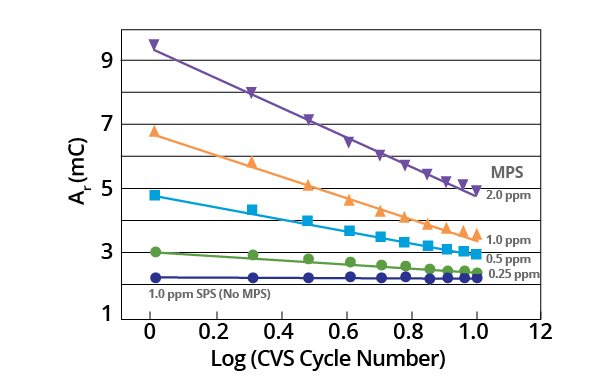
Figure 6. Plot of Ar vs. Log (CVS cycle number) as a function of initial MPS concentration for acid copper supporting electrolyte containing 1.0 ppm MPS (–0.225 V limit). Image Credit: ECI Technology
It would be challenging to ascertain a theoretical basis for this empirical relationship from present data. This is largely due to the measured copper deposition rate being a composite for a variety of potentials.
Additionally, chemical and electrochemical processes may be involved in the process of decomposition. The slope of these plots provides a measurement of initial MPS concentration (Figure 7).
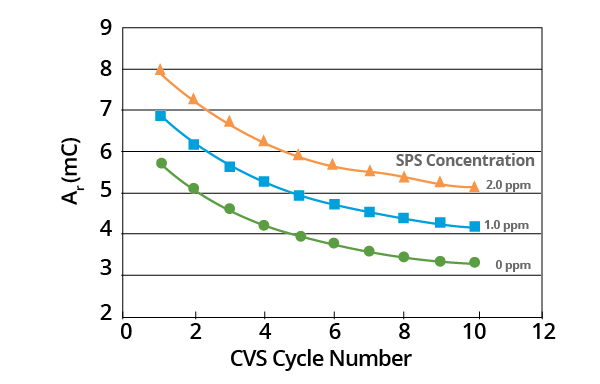
Figure 7. Effect of SPS concentration on Ar vs. CVS cycle number curve for acid copper supporting electrolyte with 1.0 ppm MPS added. Image Credit: ECI Technology
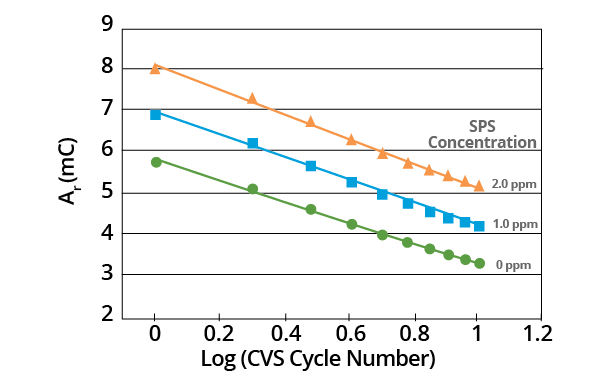
Figure 8. Effect of SPS concentration on Ar vs. Log (CVS cycle number) curve for acid copper supporting electrolyte with 1.0 ppm MPS added. Image Credit: ECI Technology
Though the slopes may vary, linear plots are obtained in all cases when the effect of negative potential scan limit on plots of Ar vs. Log (CVS cycle number) is measured. Slope is dependent on the negative potential limit. A constant negative potential limit must be maintained for the MPS analysis (Figure 9).
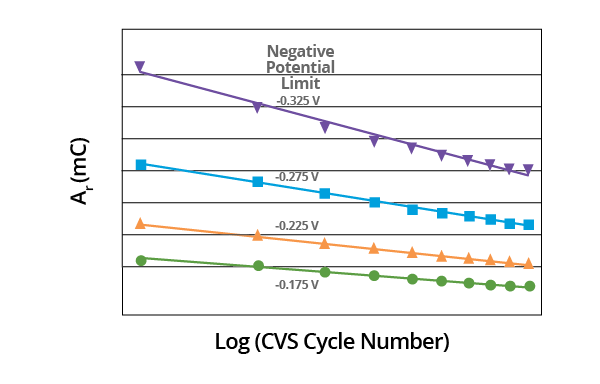
Figure 9. Plot of Ar vs. Log (CVS cycle number) as a function of negative potential limit for acid copper supporting electrolyte containing 1.0 ppm MPS. Image Credit: ECI Technology
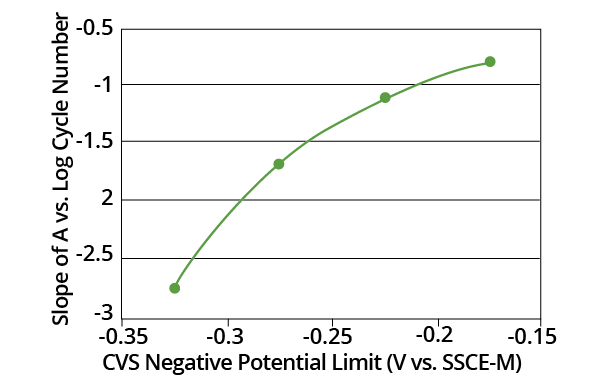
Figure 10. Plot of the slopes from Fig. 10 as a function of CVS negative potential limit. Image Credit: ECI Technology. Image Credit: ECI Technology
Previous studies by Healy et al. suggest that both SPS and MPS experience complex chemical and electrochemical reactions in acid copper plating baths.6
The SPS species (4,5-dithiaoctane-1,8-disulphonic acid) is gradually chemically oxidized in the bath, but only when in the presence of copper metal. The oxidation rate is accelerated where oxygen is present, however.
It appears a complex involving Cu(I) and MPS; for example, Cu(I)SCH2CH2CH2SO3H, may perform a key role as an intermediate in the electrochemical reduction of SPS. This may also be the case in the oxidation of both MPS and SPS in acid copper baths.
Healy et al. concluded that oxidation of MPS via this intermediate does not result in regeneration of the SPS species.6 Moffat et al., on the other hand, obtained compelling evidence that decomposition of MPS will eventually result in the formation of SPS in acid copper baths.5
After approximately two days, the CVS stripping peak area (Ar) for a 1.0 ppm MPS acid copper electrolyte was found to decay at a constant value that corresponded to that of a 1.0 ppm SPS electrolyte (Figure 11).
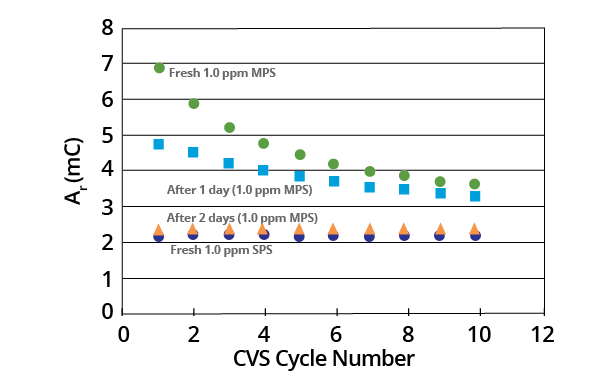
Figure 11. Effect of aging on the Ar values for a 1.0 ppm MPS acid copper electrolyte compared to the constant Ar value for a 1.0 ppm SPS electrolyte. Image Credit: ECI Technology
The concentration of the two species was the same in terms of their respective weights (1.0 ppm). This suggests that the molar concentration of the MPS electrolyte was initially twice that of the SPS electrolyte.
Equivalent Ar values were noted for both the aged MPS electrolyte and the fresh SPS electrolyte. These suggest that the MPS dimerized to SPS, resulting in the same molar concentration of SPS in each solution.
These results support the conclusion of Moffat et al.; that MPS dimerizes to form SPS in acid copper baths.5
This process would appear to be reversible under certain conditions, particularly because the initial Ar value for the MPS solution aged for one day was found to be slightly greater than the final Ar value from the previous day (using fresh MPS solution).
As partial deaeration of the solution was found to markedly lower the decomposition rate, that is, it slowed the decrease in Ar value with time. It appears oxygen also plays a role in the decomposition of MPS in acid copper baths.
Stirring of the solution was found to have little effect, implying that mass transport is not a noteworthy factor. Similarly, the removal of the Pt rotating disk electrode from the solution had no effect.
These experiments aimed is to provide metrology that enables chemical suppliers, tool manufacturers and end user to understand and better manage acid copper plating processes. Future studies will be necessary in order to determine the effects of acidity and copper ion concentration.
Conclusion
Mercaptopropylsulfonic acid (MPS) is a breakdown product of the bis(sodiumsulfopropyl)disulfide (SPS) additive used in acid copper plating baths. It can be detected via the use of cyclic voltammetric stripping (CVS) analysis.
Decomposition of MPS in acid copper baths is suspected of involving dimerization to SPS. This process would appear to be further accelerated in the presence of oxygen.
References
- P. C. Andricacos, Electrochem. Soc. Interface, p. 32, Spring 1999.
- P. Bratin, Proc. AES Analytical Methods Symp., Chicago, IL (March 1985)
- P. Bratin, G. Chalyt, A. Kogan, M. Pavlov, J. Perpich and M. Tench, “Detection of Suppressor Breakdown Contaminants in Copper Plating Baths”, 203rd ECS Meeting, Paris, France (Apr. 27 – May 2, 2003)
- M. Pavlov, E. Shalyt and P. Bratin, Solid State Tech. 46(3), 57 (2003)
- T. P. Moffat, B. Baker, D. Wheeler and D. Josell, Electrochem. Solid State Lett. 6(4), C59 (2003)
- J. P. Healy, D. Pletcher and M. Goodenough, J. Electroanal. Chem. 338, 167 (1992)
Acknowledgments
Produced from materials originally authored by M. Pavlov, E. Shalyt, P. Bratin and D. M. Tench from ECI Technology.
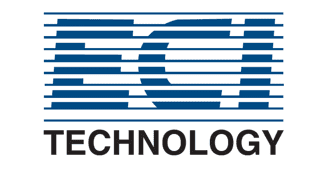
This information has been sourced, reviewed and adapted from materials provided by ECI Technology.
For more information on this source, please visit ECI Technology.