Using multiple thermal curatives in epoxy resins is a key strategy in developing advanced materials. Benzophenone tetracarboxylic dianhydride (BTDA) can be effectively combined with most liquid monoanhydrides, provided the blend remains in liquid form. Compatible monoanhydrides include Methyl tetrahydrophthalic anhydride (MTHPA), Methylhexahydrophthalic anhydride (MHHPA), Hexahydrophthalic anhydride (HHPA), Tetrahydrophthalic anhydride (THPA), and NADIC methyl anhydride (NMA). These anhydrides are generally chemically compatible with BTDA and suitable for epoxy formulations.
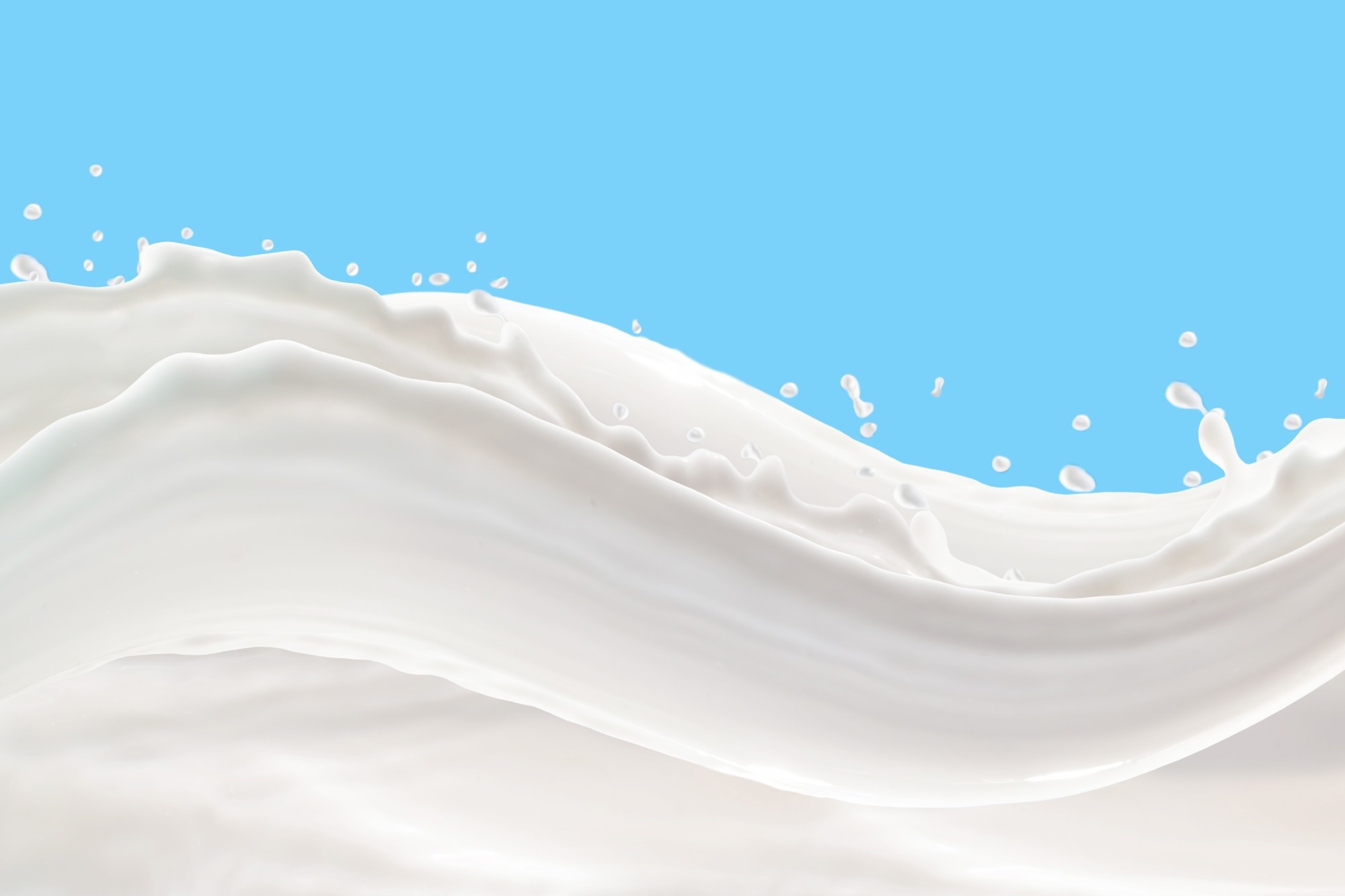
Image Credit: CK Foto/Shutterstock.com
A 50:50 weight ratio is a practical starting point for blending BTDA with liquid monoanhydrides, but the ratio may need adjustment based on rheological and curing effects. BTDA enhances crosslinking density, improving thermal resistance, electrical insulation, and mechanical strength.
Increasing the proportion of BTDA raises the mix viscosity, which may be advantageous for controlling flow. However, excessive viscosity can hinder processing, so a balance is essential. Particle size also plays a crucial role, since smaller BTDA particles disperse more easily, improving mixture homogeneity and uniformity of cure. Reducing the BTDA content can lower viscosity while still maintaining adequate performance.
BTDA/liquid monoanhydride systems are versatile and applicable across several applications:
- Adhesives and Potting Compounds: Tunable viscosity and performance make them ideal for two-component adhesives and potting systems.
- Encapsulation: These formulations effectively protect components from moisture and extreme temperatures.
- Composites: Suitable for fabricating high-strength, thermally stable composite parts such as pipes, cylinders, and complex structures.
- Electrical Insulators: Ideal for mass-cast applications requiring excellent thermal and electrical insulation properties.
Despite their advantages, these systems present some challenges. Incomplete dispersion can cause poor curing and inconsistent material properties. Incompatible fillers, especially those containing reactive groups, such as hydroxyl or carboxyl, can interfere with curing. Moisture in fillers can also trigger unwanted reactions with anhydrides. Therefore, filler selection and drying are critical.
Combining BTDA with liquid monoanhydrides provides a flexible approach to enhancing epoxy resin performance for demanding applications. By fine-tuning mixing ratios, viscosity, and crosslinking density, manufacturers can tailor properties to specific needs. Attention to dispersion, filler compatibility, and moisture control is essential to avoid processing issues. With these factors managed, the resultant curative system enables the development of high-performance materials across various industrial uses.
Acknowledgments
Produced from materials provided by Vinay Mishra, PhD, Technical Director, Thermoset Additives, Jayhawk Fine Chemicals Corporation.

This information has been sourced, reviewed and adapted from materials provided by Jayhawk Fine Chemicals Corporation.
For more information on this source, please visit Jayhawk Fine Chemicals Corporation.