As the environmental costs of petroleum-based plastics mount, researchers are exploring renewable and biodegradable alternatives that are less harmful to ecosystems.
One such alternative gaining momentum is algae-based polymers—biopolymers derived from various species of algae, including macroalgae (seaweed), microalgae, and cyanobacteria.1,2
These organisms produce natural polymers with distinct structural and chemical properties, offering a sustainable pathway to reduce dependence on conventional plastics.
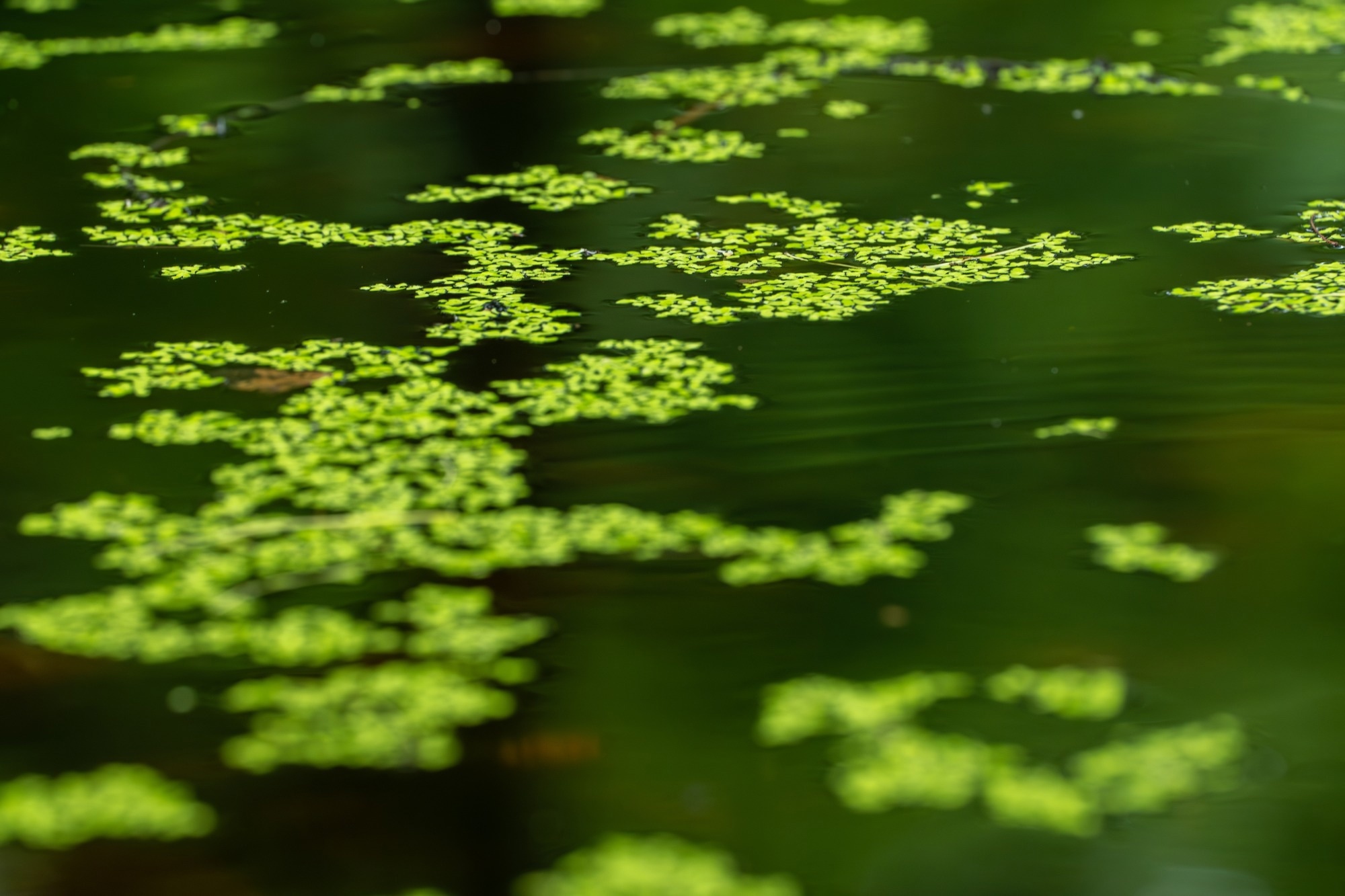
Image Credit: Ray Hugo Tang/Shutterstock.com
How They’re Made
The production of algae-based polymers involves three key stages: cultivation, extraction, and polymer synthesis. Each step can be adapted based on the algal species and the type of polymer being produced.3
Cultivation
Algae can grow in diverse environments, including freshwater, marine systems, and even wastewater streams. Depending on the species, they grow through autotrophic, heterotrophic, or mixotrophic modes.
To optimize polymer yield, algae are typically cultivated in two phases: an initial growth phase that encourages high biomass production under nutrient-rich conditions, followed by a stress phase, such as nitrogen starvation or altered salinity, that triggers the accumulation of intracellular or extracellular polymers.4
Commonly used strains include Chlorella, Spirulina, and Nannochloropsis, known for their high yields of lipids, polysaccharides, and polyhydroxyalkanoates (PHAs). Some cultivation systems also double as wastewater treatment setups, combining biomass generation with environmental remediation.5
Polymer Types and Origins
Algal biopolymers are sourced either from the cell walls or intracellular compartments, depending on the species.
Macroalgae, for instance, yield polysaccharides like alginate, agar, and carrageenan. Alginate, obtained from brown algae, is a linear copolymer composed of mannuronic and guluronic acids. Red algae are known for producing carrageenan and agar, both of which are widely used for their gelling and thickening capabilities.1,2
Microalgae and cyanobacteria, on the other hand, synthesize intracellular polymers like PHAs, a family of biodegradable polyesters composed of repeating ester units. PHAs exhibit thermoplastic or elastomeric behavior, are air-stable, and can dissolve in various solvents.2
Download your PDF copy now!
Extraction
After harvesting, several methods are used to extract these polymers:
- Solvent Extraction uses chemicals to isolate polymers like alginate and carrageenan. While effective, it requires large volumes of solvents and careful control to prevent degradation.
- Microwave-Assisted Extraction is a greener alternative that uses electromagnetic radiation to rapidly heat biomass and extract compounds like fucoidan. It reduces solvent use and shortens processing time.
- Ultrasound-Assisted Extraction relies on acoustic cavitation to disrupt cell walls, enhancing polymer release. It's faster than conventional methods and can increase yield by over 30 %.
- Subcritical Water Extraction is a high-efficiency, chemical-free process that uses pressurized hot water to extract thermally stable polymers. It has been used successfully for extracting fucoidan and alginate at higher yields than traditional approaches.6
Each method is selected based on the polymer’s properties and the production scale.
Polymer Synthesis
Once extracted, the raw biopolymers may be purified, blended, or chemically modified to enhance their properties. For instance:
- PHAs, such as polyhydroxybutyrate (PHB) and polyhydroxyvalerate (PHBV), are synthesized by microalgae under nutrient stress and are processed similarly to thermoplastics.
- Polysaccharides like alginate, carrageenan, and laminarin are directly used or processed into hydrogels, films, or composite materials.
- Composite fabrication often involves mixing algae-derived polymers with polylactide (PLA), PVA, or other bio-resins using techniques like electrospinning, melt casting, or ultrasonication to improve strength and durability.7
The outcome is a wide spectrum of bio-based materials—from soft gels and biodegradable films to high-strength composites—suitable for packaging, medical, and industrial uses. Optimization of particle size, filler shape, and processing parameters continues to improve scalability and performance.3
Love This Kind of Content? Subscribe to One of Our Expert-Curated Newsletters
Applications in Industry
Thanks to their renewability, biocompatibility, and chemical tunability, algae-derived biopolymers are being explored across multiple industries. Key areas of application include biosensing, environmental remediation, biomedical engineering, and additive manufacturing.
Biosensors
In biosensing, algae-based polysaccharides such as chitosan and carboxymethyl cellulose have been used to fabricate thin-film electrochemical sensors. These biopolymers form stable, non-toxic films and support enzyme immobilization, making them well-suited for real-time diagnostics.8
For example, laccase-based biosensors using algal matrices have been developed to detect pharmaceutical compounds through enzyme-substrate interactions, offering a greener alternative to synthetic sensor substrates.9
Pollutant Removal
Algae-based polymers also play a growing role in wastewater treatment. Materials like alginate, cellulose, and chitosan have demonstrated strong adsorption capacity for heavy metals, hydrocarbons, and pharmaceutical residues. When combined with clays or functionalized with chemical groups, their efficiency and reusability can be significantly enhanced.10
One study showed that phosphate-modified cellulose extracted from algae could remove dyes such as Rhodamine B and Amitriptyline at capacities exceeding 45 mg/g, while reducing the risk of secondary pollution.10
Biomedical Engineering
In biomedical applications, algae-based composites are used for tissue scaffolding, wound dressings, and bone regeneration. Chitosan combined with hydroxyapatite (HAp) sourced from marine algae has been used to mimic the mineral structure of bone in orthopedic implants.11
Polylactide (PLA) reinforced with brown algae (Sargassum vulgare) has also shown promise in producing collagen-like membranes for skin grafts. These materials offer the necessary mechanical strength, water retention, and biocompatibility needed for wound healing and tissue scaffolding, while eliminating the toxic residues common in petroleum-based alternatives.12
3D Printing
Algae-based materials are increasingly being adapted for additive manufacturing. In one example, PVA bio-composites incorporating Nanochloropsis salina algae have been used to create tailored 3D structures.13
These printed forms have found use in both environmental and medical domains, ranging from catalytic supports for pollutant degradation (e.g., methyl orange breakdown via TiO₂ composites) to bioactive scaffolds for stem cell growth. The material properties can be tuned for specific applications through compositional or surface modifications.13
Watch: How Plastic Made With Algae Can Clean Waterways
This short video from Business Insider illustrates how algae-derived plastics are already being developed and deployed to reduce pollution and improve water quality in real-world settings.
How Plastic Made With Algae Can Clean Waterways | World Wide Waste | Business Insider
Can Algae-Based Polymers Really Replace Plastic?
Algae-based polymers offer a sustainable alternative to conventional plastics. They are biodegradable and compostable, breaking down naturally without harmful residues.
Sourced from non-arable land and not reliant on freshwater, algae are more eco-friendly than crop-based bioplastics. These polymers are also non-toxic, reducing environmental harm during degradation and making them suitable for packaging and biomedical use.1, 13
However, technical and economic barriers remain. Scaling production is often cost-prohibitive, with inconsistent yields and polymer qualities tied to species variation and extraction conditions. Material performance—particularly in terms of mechanical strength, moisture resistance, and longevity—still lags behind established plastics.1, 3
To realize their full potential, future research must focus on process optimization, cultivation scale-up, and material standardization. Addressing these issues will be critical to making algae-based plastics commercially viable and positioning them as a key solution in the transition to a circular, fossil-free materials economy.
To learn more about emerging biomaterials and sustainable material innovations, explore:
References and Further Readings
1. Joshi, J. S.; Langwald, S. V.; Ehrmann, A.; Sabantina, L., Algae-Based Biopolymers for Batteries and Biofuel Applications in Comparison with Bacterial Biopolymers—a Review. Polymers 2024, 16, 610.
2. Alazaiza, M. Y. D.; Albahnasawi, A.; Eyvaz, M.; Al Maskari, T.; Nassani, D. E.; Abu Amr, S. S.; Abujazar, M. S. S.; Bashir, M. J. K., An Overview of Green Bioprocessing of Algae-Derived Biochar and Biopolymers: Synthesis, Preparation, and Potential Applications. Energies 2023, 16, 791.
3. Mal, N.; Satpati, G.; Raghunathan, S.; Davoodbasha, M., Current Strategies on Algae-Based Biopolymer Production and Scale-Up. Chemosphere 2022, 289, 133178 DOI: https://doi.org/10.1016/j.chemosphere.2021.133178.
4. Kartik, A.; Akhil, D.; Lakshmi, D.; Gopinath, K. P.; Arun, J.; Sivaramakrishnan, R.; Pugazhendhi, A., A Critical Review on Production of Biopolymers from Algae Biomass and Their Applications. Bioresource Technology 2021, 329, 124868.
5. Chandel, N.; Ahuja, V.; Gurav, R.; Kumar, V.; Tyagi, V. K.; Pugazhendhi, A.; Kumar, G.; Kumar, D.; Yang, Y.-H.; Bhatia, S. K., Progress in Microalgal Mediated Bioremediation Systems for the Removal of Antibiotics and Pharmaceuticals from Wastewater. Science of the Total Environment 2022, 825, 153895.
6. Roja, K.; Sudhakar, D. R.; Anto, S.; Mathimani, T., Extraction and Characterization of Polyhydroxyalkanoates from Marine Green Alga and Cyanobacteria. Biocatalysis and agricultural biotechnology 2019, 22, 101358.
7. Tran, D.-T.; Lee, H. R.; Jung, S.; Park, M. S.; Yang, J.-W., Lipid-Extracted Algal Biomass Based Biocomposites Fabrication with Poly (Vinyl Alcohol). Algal Research 2018, 31, 525-533.
8. Biswas, M. C.; Jony, B.; Nandy, P. K.; Chowdhury, R. A.; Halder, S.; Kumar, D.; Ramakrishna, S.; Hassan, M.; Ahsan, M. A.; Hoque, M. E., Recent Advancement of Biopolymers and Their Potential Biomedical Applications. Journal of Polymers and the Environment 2022, 1-24.
9. Lu, Y.; Biswas, M. C.; Guo, Z.; Jeon, J.-W.; Wujcik, E. K., Recent Developments in Bio-Monitoring Via Advanced Polymer Nanocomposite-Based Wearable Strain Sensors. Biosensors and bioelectronics 2019, 123, 167-177.
10. Upadhyay, A.; Singh, R.; Singh, D. V.; Singh, L.; Singh, D., Microalgal Consortia Technology: A Novel and Sustainable Approach of Resource Reutilization, Waste Management and Lipid Production. Environmental Technology & Innovation 2021, 23, 101600.
11. Sathiyavimal, S.; Vasantharaj, S.; LewisOscar, F.; Selvaraj, R.; Brindhadevi, K.; Pugazhendhi, A., Natural Organic and Inorganic–Hydroxyapatite Biopolymer Composite for Biomedical Applications. Progress in Organic Coatings 2020, 147, 105858.
12. Bahmani, A.; Comeau, P. A.; Montesano, J.; Willett, T. L., Extrudable Hydroxyapatite/Plant Oil-Based Biopolymer Nanocomposites for Biomedical Applications: Mechanical Testing and Modeling. Materials & Design 2019, 174, 107790.
13. Liu, J.; Sun, L.; Xu, W.; Wang, Q.; Yu, S.; Sun, J., Current Advances and Future Perspectives of 3d Printing Natural-Derived Biopolymers. Carbohydrate polymers 2019, 207, 297-316.
Disclaimer: The views expressed here are those of the author expressed in their private capacity and do not necessarily represent the views of AZoM.com Limited T/A AZoNetwork the owner and operator of this website. This disclaimer forms part of the Terms and conditions of use of this website.