Sharp Corporation has developed a new technology to blend plant-based plastic that uses corn as the raw material, and waste plastic recovered from scrapped consumer electronics. Using a mix of plant-based plastic and waste plastic blended by means of this technology in consumer electronics can significantly reduce environmental impact compared to using common plastics derived from petroleum-based feedstocks. In the future, Sharp will be conducting tests to assess commercial potential, with the goal of using blended plastic in Sharp products within fiscal 2006. In the future, when the price of plant-based plastics is reduced to a level on a par with general plastics, it is estimated that the percentage of renewable resources (plant-based plastic and waste plastic) used in all products will increase to 30% by fiscal 2010. At present, raw materials used in consumer electronics rely almost entirely on fossil materials such as petroleum, but efforts to shift as much as possible to renewable resources (plant-based and recycled materials) are moving forward from the perspective of limiting emissions of greenhouse gases, with the aim of building a sustainable recycling-oriented society. At the same time, plant-based plastics have the potential to reduce the impact on the environment given that incinerating these materials does not cause the concentration of carbon dioxide gas in the atmosphere to rise. However, problems remain in terms of impact/shock resistance, thermal resistance, cost and other factors, and their adoption in the area of consumer durable goods, particularly electronic products, remains limited. Against this background, Sharp has been conducting research since 1999 on technologies to recycle waste plastic from consumer electronics, and in May 2003, put such a recycling technology into practical use to enable repeated re-use of polypropylene (PP) and polystyrene (PS) recovered from four categories of discarded household electrical appliances falling under the Home Appliance Recycling Law (air conditioners, TVs, refrigerators and washing machines) in components in new manufactured products in these four categories without loss of physical properties such as material strength. Major Features of Technology to Blend Plant-Based Plastics and Waste Plastic • Development of technology to compatibilize*1 plant-based plastic with waste plastic. • Improved impact resistance, thermal resistance, etc., to a practical level, previously a problem with plant-based plastic. • Three patent applications pending. *1 Technology to cause microdispersion (increase compatibility at the molecular level) by uniformly blending non-homogeneous plastic materials. Reference Technology to Compatibilize Plant-Based Plastic with Waste Plastic In blending plant-based plastic (polylactic acid [PLA]) and waste plastic (polypropylene [PP]), the two materials tend not to be mutually compatible, causing a gap to form at the boundary surfaces of the PLA and PP and leading to a significant loss of physical properties (such as impact resistance and thermal resistance) (see Figure 1). 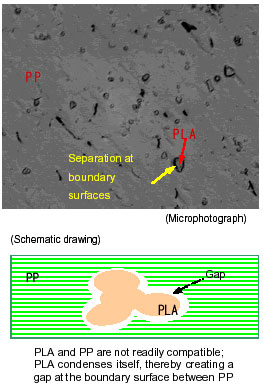 Figure 1. When PLA and PP are mixed using typical methods. But blending in an appropriate amount of a newly developed compatibilizer (Figure 2) and mixing the PLA and PP in an optimal proportion, the PLA forms an ultrafine dispersion and facilitates compatibility between the two materials, thereby dramatically improving the physical properties of the blended material. (Figure 3).  Figure 2. Schematic diagram of compatibilizer at work. 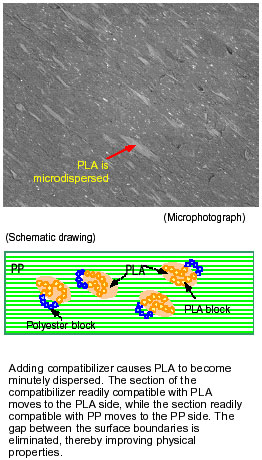 Figure 3. PLA is microdispersed as a result of blending with a compatibilizer. |