In-situ monitoring and controlling of etching processes represent an essential component of micro- and nano-structuring of materials and thin films.
Traditional techniques primarily include laser end-point detection and optical spectrometry. Although both methods monitor thickness or composition of etched layers and materials, neither provides in-situ instantaneous 3D topography measurement of the etching process with sub-micron lateral resolution.
In contrast, conventional optical and mechanical profilometers are scanning-based methods, providing static 3D topography measurement capabilities. The unique DHM® non-scanning imaging technology allows users to record time sequences of real-time 3D topographies at camera rate with interferometric vertical resolution.
DHM® can also perform measurements through glass and liquids, facilitating in-situ measurements across all environmental settings. This application can also be extended to dry and plasma etching processes.
The metallic sample coated in polymer resist is patterned with trenches of varying widths. It is placed in a liquid electrolyte where current is applied to initiate electrochemical etching. Measurements are taken through the transparent window of the etching chamber. DHM® can monitor etching depth and surface roughness in situ.
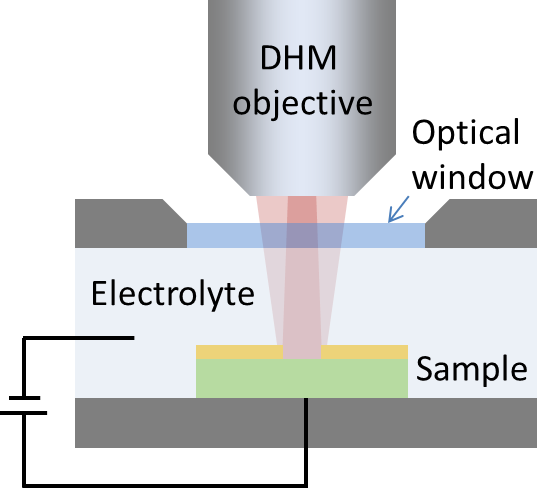
Schematic setup of in situ etching monitoring through optical window by DHM®. Image Credit: Park Systems
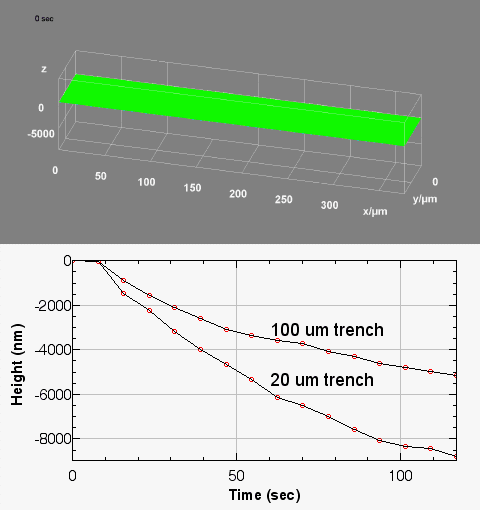
In situ monitoring of electrochemical etching of 20 um and 100 um trenches. Image Credit: Park Systems
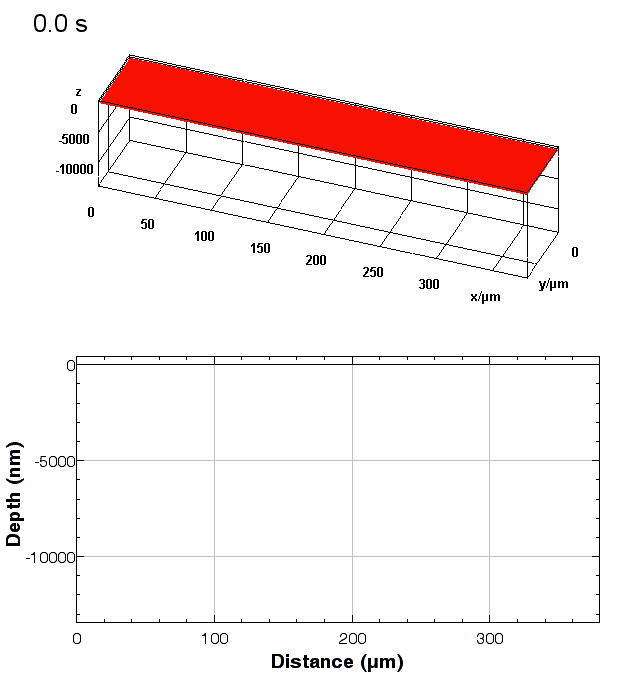
In situ monitoring of electrochemical etching of 300 µm trenches. Image Credit: Park Systems
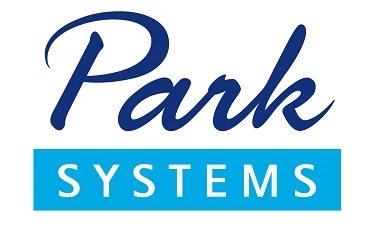
This information has been sourced, reviewed and adapted from materials provided by Park Systems.
For more information on this source, please visit Park Systems.