An automated method for measuring the dynamic deformation of a micromirror surface across its full deflection range at its resonance frequency was recently reported by DHM users at Silicon Austria Labs GmbH, the winner of the Lyncée Tec Challenge 2022.
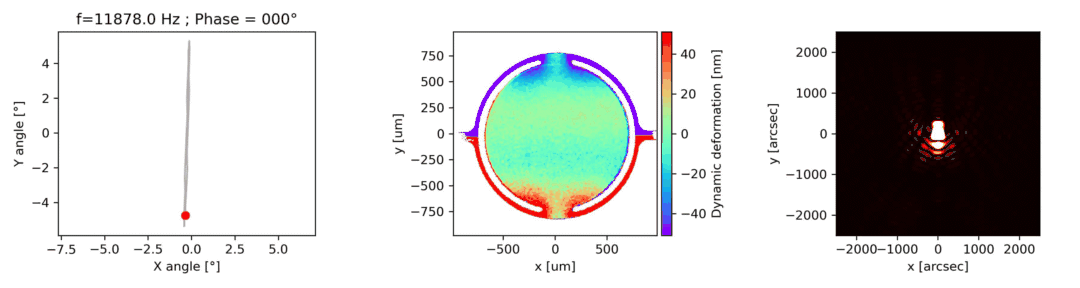
Dynamic deformation at resonant frequency and corresponding point spread function of the micromirror over its entire deflection range. Image Credit: Park Systems
A motorized goniometer is integrated into the DHM® sample holder to control the microdevice's tilt and tip. Data acquisition, mirror deflection angle, and goniometer angles are synchronized using the stroboscopic module. The mirror’s reflective surface is measured for each deflection angle when aligned perpendicular to the DHM®’s optical axis. This allows for accurate quantification of dynamic deformation across its full deflection range.
Simulations can be effectively validated against experiment data to enhance MEMS design.
The fully automated workflow has four main steps outlined in the following sections.
1. Determination of the Resonance Frequency
As demonstrated in Figure 1, the microdevice’s resonant response is determined by conducting a frequency sweep and utilizing the intensity image data. Due to interference patterns, higher mirror oscillation amplitudes reduce the DHM's measured intensity. A single measurement per frequency suffices to determine the frequency corresponding to maximum oscillation amplitude. This technique ensures quick results.
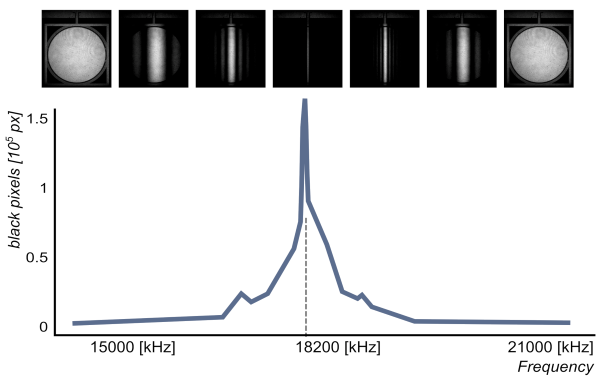
Fig 1. Intensity frequency scan. The frequency scanning step has been set to 200. This value sets the frequency resolution. Minimum steps are 0.1 Hz. Image Credit: Park Systems
2. Maximum Deflection Angle Determination
The maximum mirror deflection angle is also measured using intensity image data, as depicted in Figure 2. The mirror is actuated at resonance frequency while the goniometer automatically sweeps the tilt or tip of the microdevice. Movement speed is lowest when the mirror oscillates at its maximum angle. Therefore, the goniometer angle for which the intensity image has the largest amplitude corresponds to the maximum vibration angle.
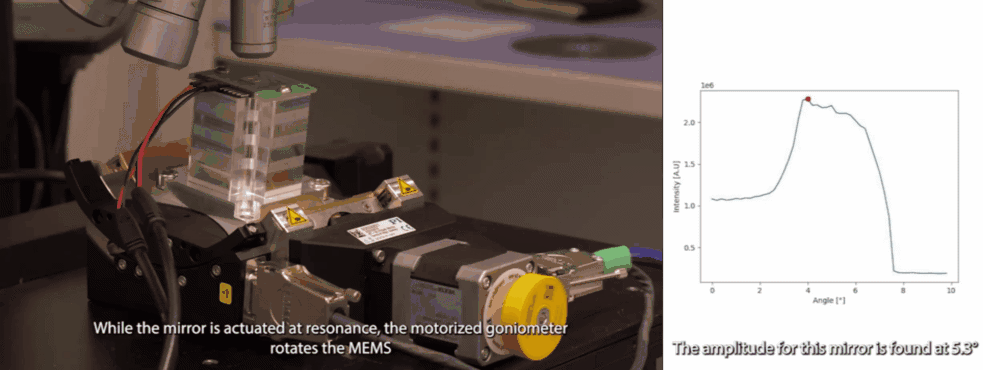
Fig 2. Maximum angle measurement using amplitude analysis. Image Credit: Park Systems
3. Micromirror Response Phase Shift at Resonant Frequency Adjustment
The phase difference between the mirror excitation signal and response is calculated by scanning the excitation signal phase offset when the goniometer is set at the maximum mirror deflection angle, as demonstrated in Figure 3. The image on the right displays the phase shift value as the median point of the graph of the DHM image intensity versus phase offset function.
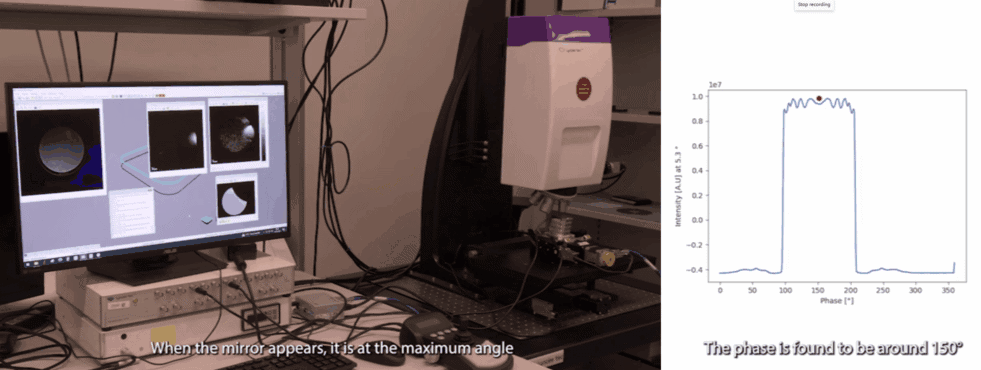
Fig 3. Determine the phase shift between mirror movement and excitation. Image Credit: Park Systems
4. Mirror Characterization Over the Full Deflection Angle Range
The motorized goniometer modifies the microdevice tilt and tip using the parameters calculated in the preceding stages. The mirror’s reflective surface is measured while positioned along its complete deflection range perpendicular to the DHM®’s optical axis, as illustrated in Figure 4.
This measurement can be interpreted as surface dynamical deformation, a vibration map, and an evaluation of optical aberrations, as presented in the following section.
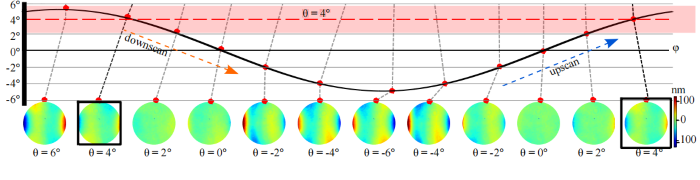
Fig 4. Slow axis upscan and downscan micromirror dynamical deformation for a scan angle of ±4°. Image Credit: Park Systems
Optical Aberrations Characterization
Dynamic deformation measurements allow the evaluation of optical aberrations at any phase of the mirror oscillations. For example, at the maximum scan angle of the micromirror, trefoil is visible for the fast axis when the low axis exhibits both trefoil and comma.
In the specific case illustrated in Figure 5, the slow axis demonstrates a dynamic deformation of 250 nm, which results in an 8% reduction in contrast to the diffraction limit for the same aperture. The hysteresis observed in this axis, where the difference in dynamic deformation for upscan and downscan is 45 nm, accounts for a 0.6% contrast loss. The fast axis exhibits a dynamic deformation of 1600 nm, causing a 96% reduction in contrast. In fast axis mode, image quality deteriorates as the angle increases.
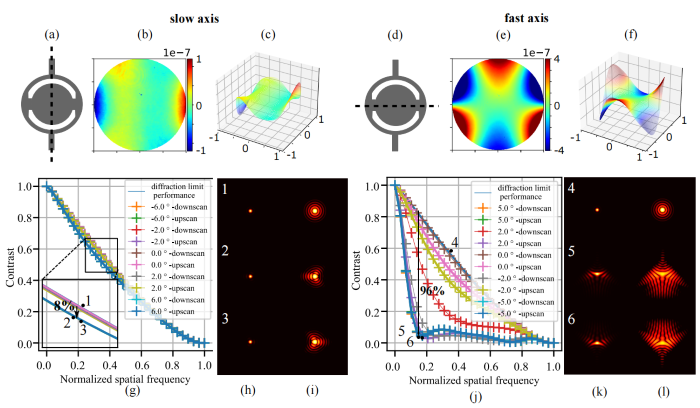
Fig 5. The surface plot of measured dynamic deformation at maximum scan angle. Aberration such as Trefoil is visible for fast axis. Slow axis has Trefoil, Comma as dominant aberrations. Modulation transfer function resulting from deformation in mirror when operating in torsion mode and bending mode are presented in the plots respectively. Image Credit: Park Systems
I am very much impressed by the DHM, on how we can use the laser trigger pulses down to 7.5ns and record the high resolution- surface topographies of a high-speed scanning micromirrors. We received support from Yves on improving our measurements, to deal with high velocity at zero crossing of mirror. Also, I am grateful for his immediate responses and contribution to paper reviewing within a short notice period.
Pooja thakkar, Junior Scientist, Photonic Systems, Silicon Austria Labs
Besides having good enough resolution in all 4 dimensions to image such a small and mechanical deformation, the key aspect of stroboscopic holography for high deflection MEMS mirror is to explore the parameter window space first (full field) contrary to a scanning technique – i.e LDV – that would do it frequency first. This enables easy and precise measurement, and a straightforward processing scheme.
Clement Fleury, Senior Researcher, Photonic Systems, Silicon Austria Labs
Experimenal characterization of dynamic deformation at larger optical scan angles has for long time remained underexplored. Digital holographic microscopy offers superior lateral, axial and temporal resolution, allowing us to study peculiar effects in angle resolved membrane dynamics. Lyncée Tec offers you the right tool for the job.”
Dr. Jaka Pribošek, Senior Scientist, Photonic Systems, Silicon Austria Labs
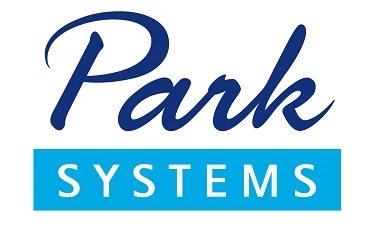
This information has been sourced, reviewed and adapted from materials provided by Park Systems.
For more information on this source, please visit Park Systems.