Introduction The semi-solid forming processing is well known as a novel technology of combining the advantages of both casting and forging for producing complex-shaped components [1]. The thicker components produced by this process exhibits better mechanical properties than those by conventional squeeze casting [1-3]. In this process, it is very important to achieve semi-solid slurry of fine and spherical primary crystal structure, namely non-dendritic structure. To produce fine and spherical primary crystals of aluminum alloys, many research works have been carried out. Flemings [1] introduced a processing route for achieving a spherical crystal structure, by mechanical stirring of molten metal during solidification, and explained that rotational fluid flow breaks the dendritic crystals generated on the mold wall and stirring impeller. Gabathuler and Alusuisse [4] compared other routes; using grain refiner of titanium boronite, MHD (electromagnetic or magneto-hydrodynamic) stirring and intense ultrasonic wave, and concluded that the electromagnetic route was the most effective. Tzimas and Zavaliangos [5] compared other routes of spray casting and SIMA (stress induced melt activated) process with MHD process, and concluded that MHD route is inferior to the other two routes because of non uniform distribution of primary crystals in billet. Adachi et al. [2] and Kaneuchi et al. [3] showed that spherical crystals structure can be achieved by holding molten metal for an appropriate time at temperature between liquidus and solidus. Both succeeded in constructing commercial machines, in which elaborate processing and equipment are required especially for controlling temperature. Then we recognized that the physical introduction of nuclei in to the molten metal and holding it at suitable temperature is important and stirring is more effective for making the uniform distribution of crystals in the whole billet rather than breaking the dendritic crystals. The purpose of the present paper is to prove this concept, which may be of fundamental knowledge for developing advanced semi-solid forming process. Experimental Procedure Alloys Tested For importance of industrial application, AC4CH (Al-7%Si-0.4Mg) was taken as the main alloy of this research and for comparison Al-17%Cu alloy; The former has a higher solid density than liquid and the latter has a lower solid density than liquid. The chemical composition of the AC4CH used is shown in Table 1. Cooling curves of these alloys were taken by differential scanning calorimeter and the liquidus temperature of AC4CH was determined as 881 K and Al-17%Cu as 883 K. Microstructures of both alloys before remelting are shown in Figure 1, exhibiting dendritic structures. Table 1. Chemical Composition of AC4CH used in the present study mass. | 7.02 | 0.11 | 0.38 | <0.01 | <0.01 | <0.0 | <0.0 | Bal. | 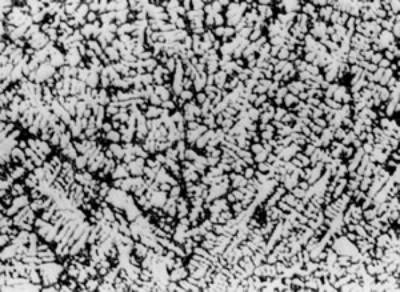 (a) 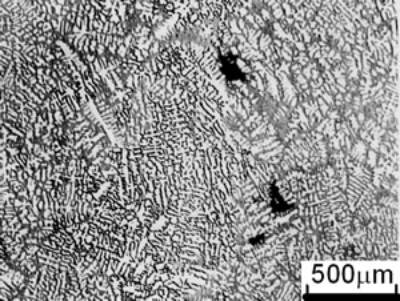 (b) | Figure 1. Microstructure of raw materials; (a) AC4CH, (b)Al-17%Cu. | Producing Semi-Solid Metal The experimental apparatus is schematically shown in Figure 2. It is made of a stirring unit, a temperature measuring unit, a mold unit and a base unit. The mold unit was preheated in a furnace at 523 K and AC4CH alloy was melted and superheated to 933 K in another furnace and poured into the mold at 923 K. Then the mold unit was put on the base unit and the measuring unit was set. When the molten metal temperature decreased to a given value (see Table 2), the stirring unit actuated at a given rotation speed (see Table 2) was set and the rod was inserted as shown in Figure 2. As soon as the temperature showed recalescence, the stirring unit was removed and the rod was taken out from the molten metal. Since then the molten metal cooled at a rate controlled by using brick or iron for the base unit. When the temperature decreased to 858 K, which was determined using Al-Si binary phase diagram data [6] and cooling curve data mentioned above and that corresponds to about 64 vol% of solid fraction, the mold unit was raised with tongs and quenched into a pool of water. The quenched metals were cut longitudinally and their microstructures were inspected on whole cross-sectional areas. The average grain size was evaluated using an optical microscope with an image analyzer integrated to personal computer with Image-Pro Plus software. 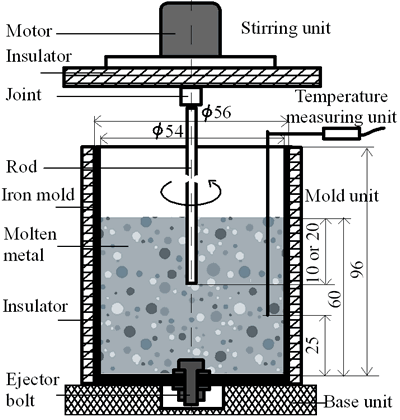 | Figure 2. Schematic illustration of the experimental apparatus used in the present study. | Table 2. Experiment Conditions | Alloy for molten metal | AC4CH | AL-17%Cu | Rod material | AC4CH | SUS303 | AC4CH | AL-17%Cu | Rod diameter (mm) | 8 | 8 | 35 | 8 | Rod insertion depth (mm) | 20 | 20 | 10 | 20 | Rod insertion Temp. (K) | 918 | 908 | 898 | 888 | 888 | 888 | 888 | 908 | 883 | Rod rotation speed(min-1) | 90 | 90 | 180 | 180 | 180 | 180 | Quenching Temp. | 858 | 858 | 858 | 858 | 858 | 868 | Cooling rate (K/min) | 11.5 | 11.3 | 13.2 | 12.7 | 4.8 | 4.7 | 6.8 | 6.8 | 9.7 | Rod preheating Temp. (K) | RT | RT | RT | RT | 623 | RT | | | | | | | | | | | | | Note: Experiments for AC4CH and AL-17%Cu alloy specimens without stirring were quenched at 858K and 868K respectively. RT = Room Temperature. Cooling rate is from insertion end to quenching into water. 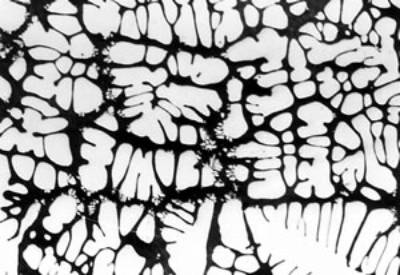 (a) 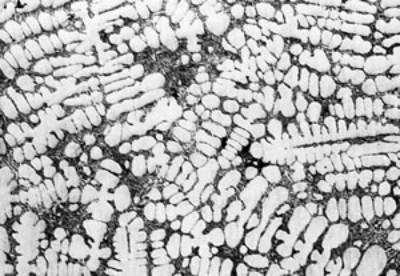 (b) 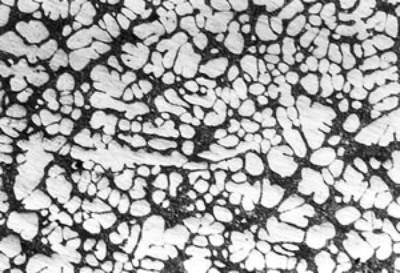 (c) 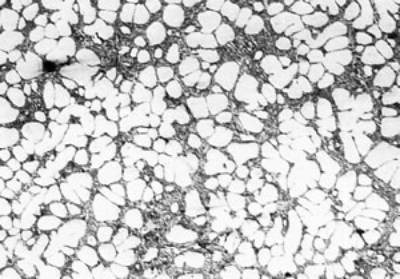 (d) 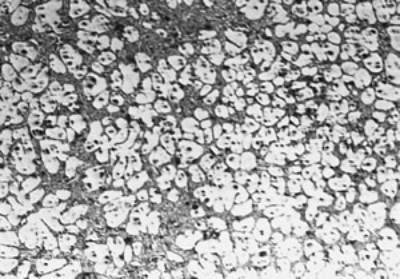 (e) 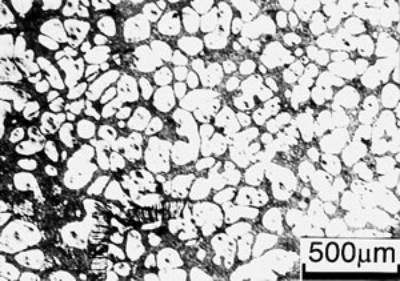 (f) | Figure 3. Microstructures of AC4CH alloy specimens; (a) without rod insertion,(b) Ex. 1 insertion at 918K, (c) Ex. 2 insertion at 908K, (d) Ex. 3 insertion at 898K, (e) Ex. 4 insertion at 888K with cooling rate of 12.7K/min, (f) Ex. 5 insertion at 888K with cooling rate of 4.8K/min. | The conditions of every experiment are summarized in Table 2. Firstly, using AC4CH rod of 8 mm in diameter and iron for the base unit, we checked the effect of rod insertion temperature in Ex.1 to Ex.4. Secondly, the effects of rotation speed and rod material were checked using a brick base in Ex.5 to Ex.7. In Ex.8, the preheated large rod was tested. Finally, the effect of solid density (Al-17%Cu) was checked in Ex.9. Results and Discussion Effect of Rod Insertion Temperature Figure 3 shows the microstructures of specimens obtained in Ex.1 (b) to Ex.5 (f) where the rod insertion temperatures were varied and that obtained in another experiment without rod insertion (a). Figure 4 shows the distribution of grain size of the solidified specimens. It can be seen that the primary crystals of the specimen without rod insertion are dendritic. However, the primary crystals of the specimens with rod insertion become finer and more spherical as the rod insertion temperature decreases as shown in Figures 3 (b)-(e). In the specimen with rod insertion at 918 K, (b), the primary crystals still retains a dendritic structure and the average grain size is almost similar to those of the specimen without stirring. At the rod insertion temperature of 908 K, spheroidization of primary crystals has begun. Although the microstructure is partly dominated by dendritic crystals, many spherical primary crystals are observed (c). At the rod insertion temperature of 898 K, the spheroidization of primary crystals increases and separates from each other (d). Temperature of 888 K is the closest insertion one to the liquidus temperature of the alloy. The finest and the most spherical crystals structure of about 88 µm were obtained (e). Decreased heat extraction by changing the base material from iron to brick, the cooling rate of semi-solid metal is decreased from 12.7 K/min to 4.8 K/min and the microstructures becomes coarser (about 97 µm) at the same insertion temperature (f), where the definition of cooling rate will be shown in Figure 6. 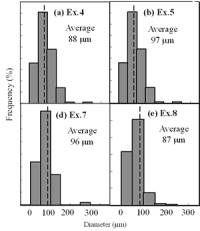 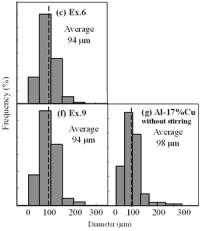 | Figure 4. Distribution of grain size of the specimens with globular primary crystals at indicated experiment conditions. | In order to define the distribution of spherical primary crystals, the cross-sectional areas of specimens were divided into two parts, (1) more spherical crystals part (hatched) and (2) more dendritic crystals part (non-hatched), after microscopic inspection on whole cross-sectional areas of the specimens. Figure 5 illustrates those distributions. The experiment without rod insertion has no spherical primary crystals area (a). High insertion temperature of 918 K makes no spherical crystals area even though the molten metal is stirred (b). From Figures 5 (c), (d) and (e), the amount of spherical primary crystals area increases as the rod insertion temperature decreases. Among these results, the higher the rod insertion temperatures, the lower the positions of primary crystals area are. This phenomenon may be related to time interval between insertion of rod and recalescence of molten metal. In a longer time interval, the crystals have enough time to settle at the bottom. But at a shorter time, because the rod insertion is immediately followed by recalescence, spherical crystals do not have a chance to settle at the bottom. The primary crystals stay in the higher position near the rod insertion depth. Figure 6 shows the cooling temperature profile of AC4CH during solidification measured in the experiments mentioned above. Now we notice two kinds of time interval: time interval t1 from rod insertion start to insertion end (recalescence) and time interval t2 from recalescence to quenching. As mentioned above, time interval t1 affects the distribution of spherical crystals. Then comparing the microscopic structures in Figure 3 with the time interval t2, it has been found that the primary crystals size increases with increasing t2. That should be due to coarsening of primary crystals in the range of temperatures between liquidus and solidus [2,3]. 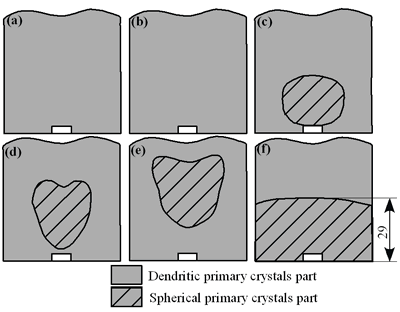 | Figure 5. Distribution of primary crystals of AC4CH alloy specimens; (a) without rod insertion,(b) Ex. 1 insertion at 918K, (c) Ex. 2 insertion at 908K, (d) Ex. 3 insertion at 898K, (e) Ex. 4 insertion at 888K with cooling rate of 12.7K/min, (f) Ex. 5 insertion at 888K with cooling rate of 4.8K/min. |  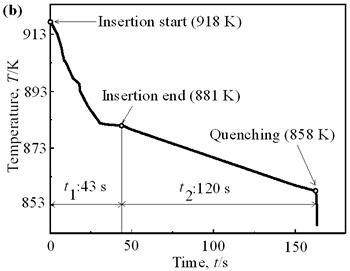 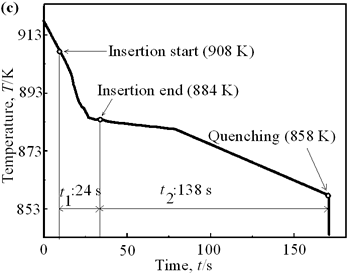 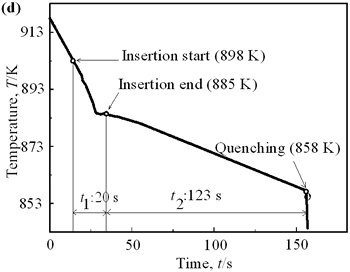 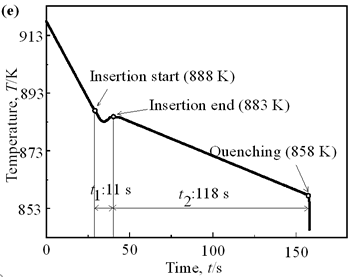 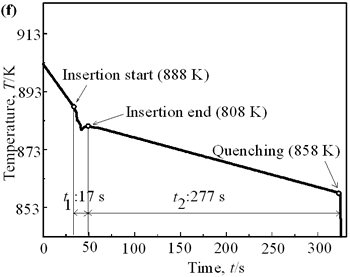 | Figure 6. Cooling curves of AC4CH alloy specimens; (a) without rod insertion,(b) Ex. 1 insertion at 918K, (c) Ex. 2 insertion at 908K, (d) Ex. 3 insertion at 898K, (e) Ex. 4 insertion at 888K with cooling rate of 12.7K/min, (f) Ex. 5 insertion at 888K with cooling rate of 4.8K/min. | Effect of Rod Rotation Speed and Rod Material Figure 7 shows microstructures and distribution of primary crystals obtained in Ex.5 to Ex.7. Effect of stirring rod rotation speed can be slightly seen in (c) and (d) for Ex.6 with 180 min-1 that shows finer primary crystal size of about 94 µm and wider spherical areas of distribution than (a) and (b) for Ex.5 with 90 min-1. Higher stirring rod rotation speed gives thinner primary crystal size. Figure 7 (e) and (f) show the result of Ex.7 in which SUS303 stainless steel stirring rod was used with experimental conditions same as Ex.6 (c) and (d). Measured t1 was 20 s and t2 was 250 s. In this figure, it can be seen that spheroidoization is similar but the size of primary crystals become larger by 96 µm and the distribution of spherical crystals take higher position and has less area. These results suggest that when the rod is made of the same material as the molten metals, it could act as a nucleation site. If not, when the rod is made of material other than the molten metal, the refinement and the spheroidization of primary crystals might be due to the breaking up of dendritic structure as Flemings [1] mentioned. | Figure 7. Microstructures and distributions of spherical and dendritic crystals of AC4CH alloy specimens; (a), (b) Ex. 5: using AC4CH rod with 90min-1 rotation speed, (c), (d) Ex. 6: using AC4CH rod with 180min-1 rotation speed, (e), (f) Ex. 7 using SUS303 rod with 180min-1 rotation speed. | Preheated Larger Rod Experiment The purpose of this experiment is to obtain an ingot of whole spherical crystals area. The results described above suggest that it is effective to increase nuclei by increasing rod diameter. Then 35 mm diameter rod of AC4CH which is 4 times larger than previous experiment was used to prove the suggestion. After some tests on metal sticking, the experimental conditions for the rod insertion were determined, namely: the rod was preheated to 623 K, insertion temperature of molten metal 908 K and insertion depth was 10 mm. Then Ex.8 was carried out and its results are shown in Figure 8. The microstructure shows that primary crystals are almost spherical and fine solid particles of 87 µm with the size distribution shown in Figure 4, which is the finest in this research are obtained as shown in (a). The distribution of spherical crystals area almost covers the cross-sectional area of specimen as shown in (b). Accordingly, we could say it is approaching the best condition for an industrial application.  (a) 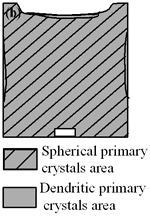 (b) 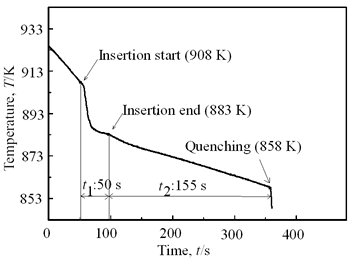 (c) | Figure 8. Microstructure (a), distribution of spherical primary crystals (b), and cooling curve (c) of AC4CH alloy specimen on experiment Ex. 8. | Seeing the cooling curve of Ex.8 (c) in Figure 8, time interval t1 is similar as Ex.1 and time interval t2 as Ex.3. In both experiments, the spherical areas did not exist or were minimal. Nevertheless in Ex.8 whole spherical area can be obtained. A possible explanation is that the larger diameter rod has a larger amount of nucleated crystals, which provide many crystals and absorbs a larger contact area with the molten metal, leading to more heat from molten metal. Accordingly much supercooling and time interval t1 is required. Furthermore, larger number of nuclei provided by stirring may restrict the growth of individual crystals, leading to less coarsening during solidification although time interval t2 is longer. This might be the reason why the finest spherical crystals structures can be obtained in Ex.8. Effects of Density Difference between Solid and Liquid Figure 9 shows the results of experiments for Al-17%Cu which has higher solid density than liquid. Figures 9(a) and (b) show for an experiment without stirring there are no spherical crystals area; every primary crystal becomes dendritic with average grain size of about 98 µm and they have floated to the meniscus. The remaining molten metal sinks to the bottom and becomes eutectic crystals. In Figure 9(c) and (d), the results of Ex.9 whose experimental conditions are almost similar to Ex.6 except for the molten material indicates clearly that size of spherical primary crystals of 94 µm and the distribution of spherical crystals are almost same. But the position of the distribution is in the top part of molten Al-17%Cu alloy, contrary to the result in AC4CH alloy as shown in Figures 5 and 6. So the effect of density between primary solid and liquid is very clear. | Figure 9. Microstructures ((a), (c)) and distributions of primary crystals ((b),(d)) of Al-17%Cu specimens; (a),(b) without stirring, while (c),(d) stirring according to conditions in Ex. 9: with Al17%Cu on 20mm insertion depth. | Conclusions Spheroidization and distribution of primary crystals of AC4CH aluminum alloy in mold by inserting and rotating a rod in the molten metal in various processing conditions have been carried out. The results are summarized as follows: • The rod that is made of the same alloy as the molten metal acts as a nucleation site and provides nuclei for the formation of fine and spherical primary crystals. • The distribution of the refined and spheroidized primary crystals in an expandable area in mold can be obtained by optimizing rod insertion temperature, rod rotation speed, cooling rate, and rod diameter. • Time interval from rod insertion start to insertion end (recalescence) affects the distribution on spherical crystals, and time interval from recalescence to quenching affects the size due to coarsening in the temperature range between liquidus and solidus. • The process successfully produced an ingot with 54 mm in diameter and 55 mm in length with homogeneous spherical and fine primary crystal with an average grain size of 87 µm. Acknowledgements This study is supported by a Grand-in-Aid for Science Research on Priority Area (B), “Platform Science and Technology for Advance Magnesium Alloys” and the 21st Century of Excellency (COE) Program from the Minister of Education, Culture, Sport, Science and Technology of Japan. References 1. M. C. Flemings, ”Behavior of Metal Alloys in the Semi-solid State”, Metall. Trans. A 22A (1991) 957-981. 2. M. Adachi, M. Uchida, S. Satou, H. Sasaki, Y. Harada and N. Ishibashi, “The Latest Rheocasting Machine” , J. Japan Institute of Light Metals 51 (2001) 568-574. 3. T. Kaneuchi, R. Shibata and T. Imamura, “Development of Semi-Liquid Die Casting Process Generating Spherical Primary α-Phase in Shot-Sleeve”, J. Japan Foundry Engineering Society. 74 (2002) 595-599. 4. J. P. Gabathular, D. Barras, Y. Kranhenbuhl and J. C. Weber, Proceeding of the 2nd Int. Conf: “Semi-solid Processing of Alloys and Composites”, ed. by S. B. Brown and M. C. Flemings, The Minerals, Metal & Material Society, Pennsylvania (1993) pp. 33-46. 5. E. Tzimas and A. Zavaliangos, “A Comparative Characterization of Near-Equiaxed Microstructures as Produced by Spray Casting, Magnetohydrodynamic Casting and the Stress Induced, Melt activated Process” , Mater. Sci. Eng. A289 (2000) 217-227. 6. T. B. Massalski, “Binary Alloy Phase Diagrams Vol. 1”, ed. by J. L. Murry, L. H. Bennett and H. Baker, American Society for Metals, Ohio (1986) p. 165. 7. K. Nakagawa, K. Hoshino and T. Otani, “Effect of Molten Metal Stirring on Microstructures of Al-2 Mass% Si Alloy”, J. Japan Foundry Engineering Society, 75 (2003) 185-190. 8. S. Iwasawa, T. Yamaguchi, S. Saikawa, K. Hayashi, S. Kamado and Y. Kojima, Structure and Mechanical Properties of Hypereutectic Al-Si Alloy Produced by Thixocasting Process”, J. Japan Foundry Engineering Society, 74 (2002) 291-297. 9. F. Tanabe, T. Motegi and M. H. Robert, ”Influence of AC4CH Billet Structures on Thixocasting Force”, J. Japan Foundry Engineering Society, 75 (2003) 474-478. 10. S. Kamado, A. Yuasa, T. Hitomi and Y. Kojima, “Effect of Stirring Conditions on Structure and Apparent Viscosity of Semi-solid AZ91D magnesium Alloy”, J. Japan Institute of Light Metals 42 (1992) 734-740. 11. E. F. Emly, “Principle of Magnesium Technology”, Pergmon Press, London (1966) pp. 788-857. Contact Details |