Scientists from China and Pakistan have collaborated on a new paper investigating the use of regenerated lignocellulosic nanofibrils for green solvents. In the study, a novel two-step and scalable process was presented for the synthesis of emulsions from these materials, with the effect of treatments analyzed. The research has appeared in the journal Polymers.
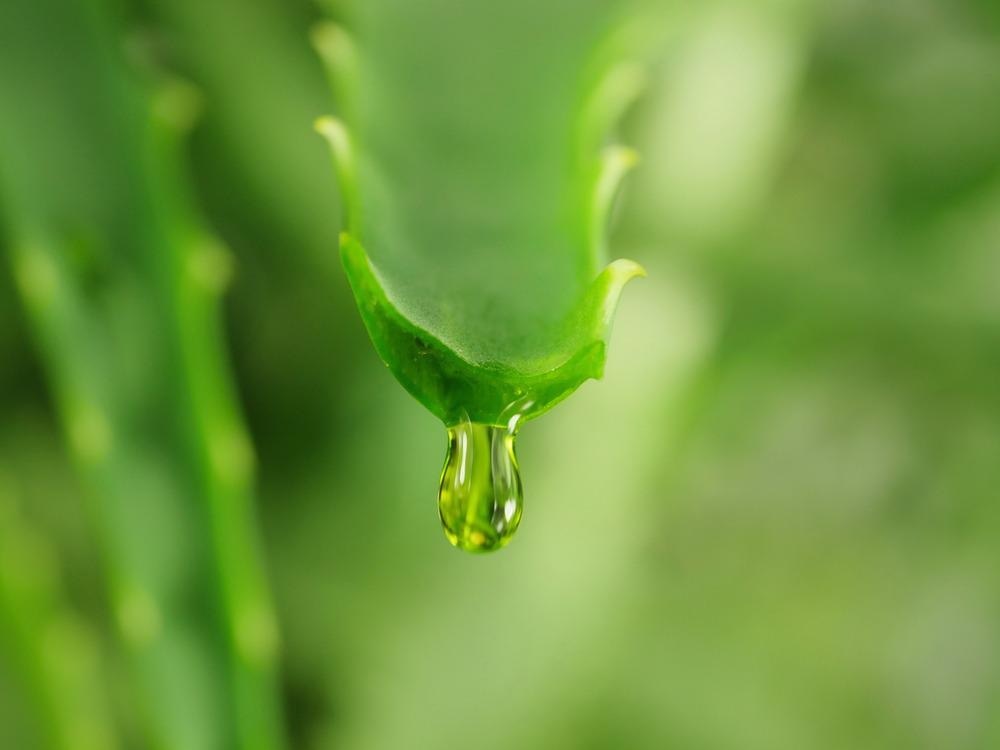
Study: Lignocellulose Extraction from Sisal Fiber and Its Use in Green Emulsions: A Novel Method. Image Credit: Krasowit/Shutterstock.com
Sisal Fibers
Biomass has been extensively explored as a raw material for several technologies in various industries. Biomass sources such as sugarcane bagasse, rice husk, wheat straw, pineapple peel, and corn straw are all sources of materials such as lignin, cellulose, and hemicellulose.
Amongst the various biomass sources that have been investigated in recent decades, sisal fibers have relatively high cellulose and hemicellulose contents and low lignin content. Furthermore, this organic material is relatively abundant, representing 2% of all cultivated plant matter.
Sisal fibers come from the plant Agave sisalana. This plant has a ten-year lifespan, in which time it will have produced between two hundred and two hundred and fifty leaves, with one dried leaf containing 4% fiber by mass. They possess suitable properties such as low density, mechanical strength, biocompatibility, and biodegradability.
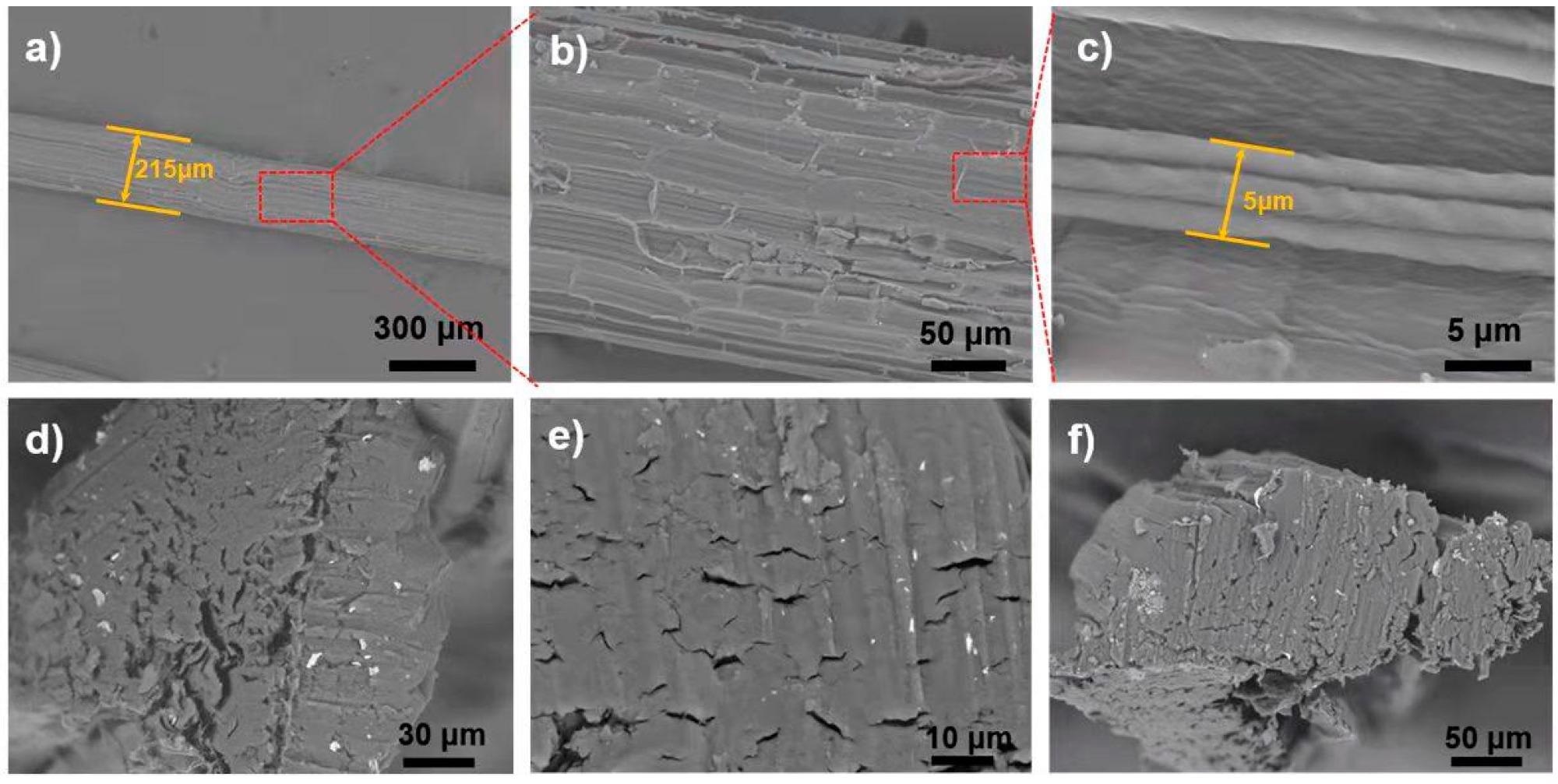
Scanning electron micrograph of different segments of raw sisal fiber: (a) Cross-sectional view of raw sisal fiber and visual demonstration of numerous microfibrils intertwined with each other. (b) SEM image of the red rectangular area selected in panel (a). (c) Magnified SEM view of the marked red rectangular area from panel (b). (d–f) Cross-sections of a raw sample with different magnifications. Image Credit: Pirah, S et al., Polymers
Due to their properties and abundance, sisal fibers have been used in the production of several products such as textiles, composites, surgical sutures, cellulose nanowhiskers, and Pickering emulsions.
Nanocellulose and Regenerated Lignocellulosic Nanofibrils
Nanocellulose has been evaluated in recent years for its use in several applications. The three types of nanocellulose are bacterial nanocellulose, cellulose nanocrystals, and cellulose nanofibrils. However, the commercial applications of nanocellulose materials are hindered by harsh extraction methods such as alkaline treatment and bleaching to recover it from wood biomass.
The use of harsh extraction methods and reagents presents economic and environmental problems for the utilization of nanocellulose materials. Furthermore, its viability for applications such as Pickering emulsion stabilizers and hydrophobic films is hindered by the hydrophilicity of this material due to the presence of abundant hydroxyl groups.
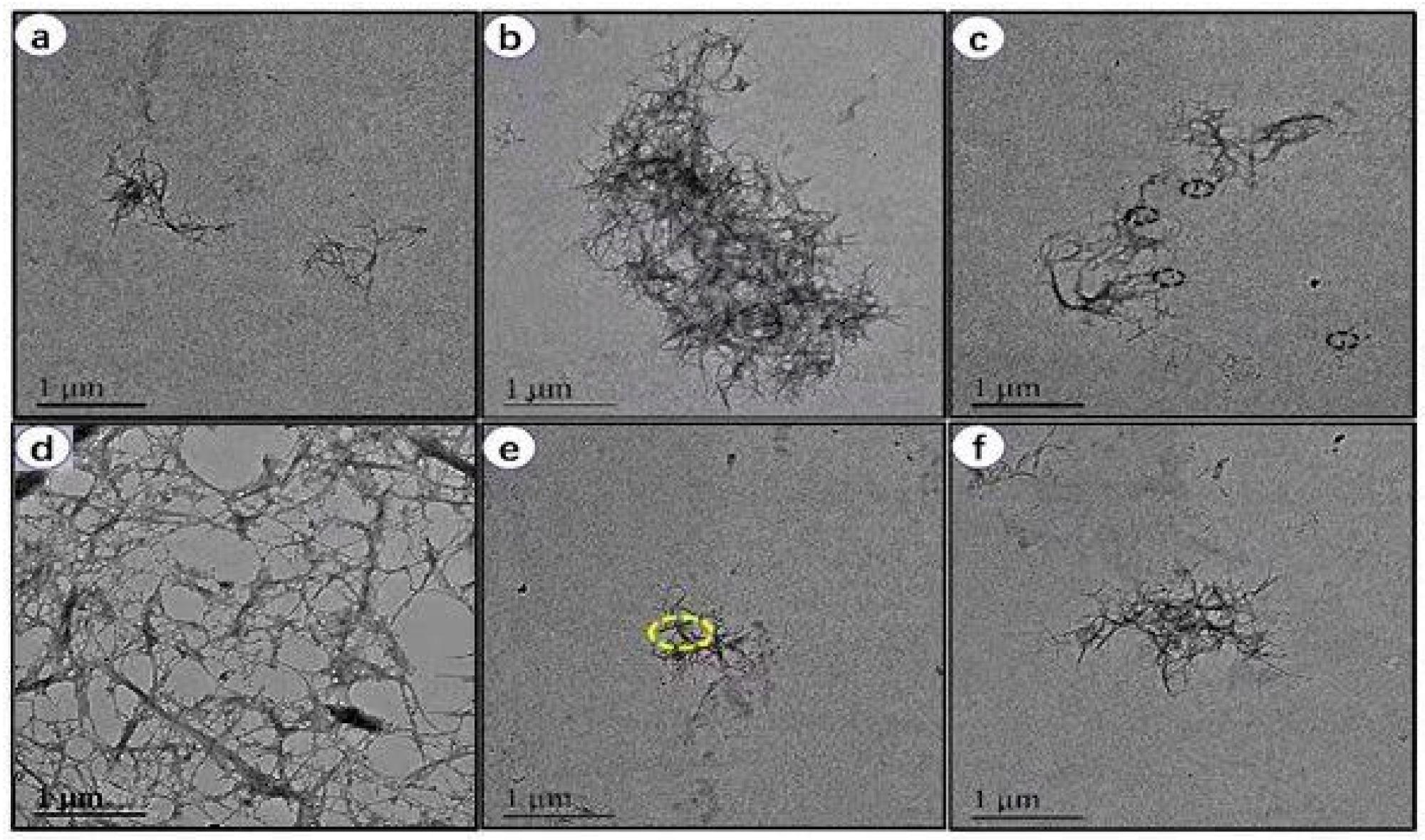
TEM images of lignocellulosic nanofibers (LCNFs): (a) TEM image of raw sisal fiber without phosphoric acid treatment. (b–e) TEM micrograph of nanofiber after treatment with phosphoric acid. The size of nanofiber is reduced significantly from micrometer to nanometer range. (f) Magnified view of selected yellow circle area from panel (e). Image Credit: Pirah, S et al., Polymers
Another issue is the strong intermolecular forces in the polymer network of nanocellulose materials. This is due to strong interactions between cellulose, lignin, and hemicellulose. Dissolution in common solvents is difficult. To overcome this issue, research has turned to the development of regenerated lignocellulose nanofibrils.
Regenerated lignocellulose nanofibrils are relatively easy to extract and are readily available. Research has indicated that the properties of these nanofibrils are enhanced by the residual lignin present in them, such as hydrophobicity, thermal stability, antioxidant properties, and mechanical stability.
To date, several lignocellulosic nanofibril extraction methods have been reported. These include chemical methods such as inorganic acid hydrolysis, pulping, and TEMP oxidation and physical methods such as grinding and ultrasonication. Additionally, methods that combine chemical and physical methods have been developed.
The use of recovered lignocellulose nanofibrils in Pickering emulsions as stabilizers and other components provides a route to green solvent synthesis. Studies have demonstrated the suitability of these materials for emulsification compared to other types of natural emulsifier. However, there is a lack of study on using sisal fibers to prepare recovered lignocellulose nanofibrils.
The Study
The paper published in Polymers has demonstrated a novel two-step scalable process for preparing recovered lignocellulose nanofibrils from sisal fibers. Fiber dissolution and ultrasonication were employed to prepare the oil-in-water emulsion. Small portions of fibers were cut and then soaked in water, and agitation and heat were used to dissolve the fiber portions in phosphoric acid.
The authors optimized fiber, water, and phosphoric acid ratios and dissolving condition parameters. Water was then poured into the solution to regenerate the nanofibrils until neutral pH was reached. Excess water was removed once the nanofibrils had settled to produce concentrated solutions. A highly concentrated solution was produced using centrifugation.
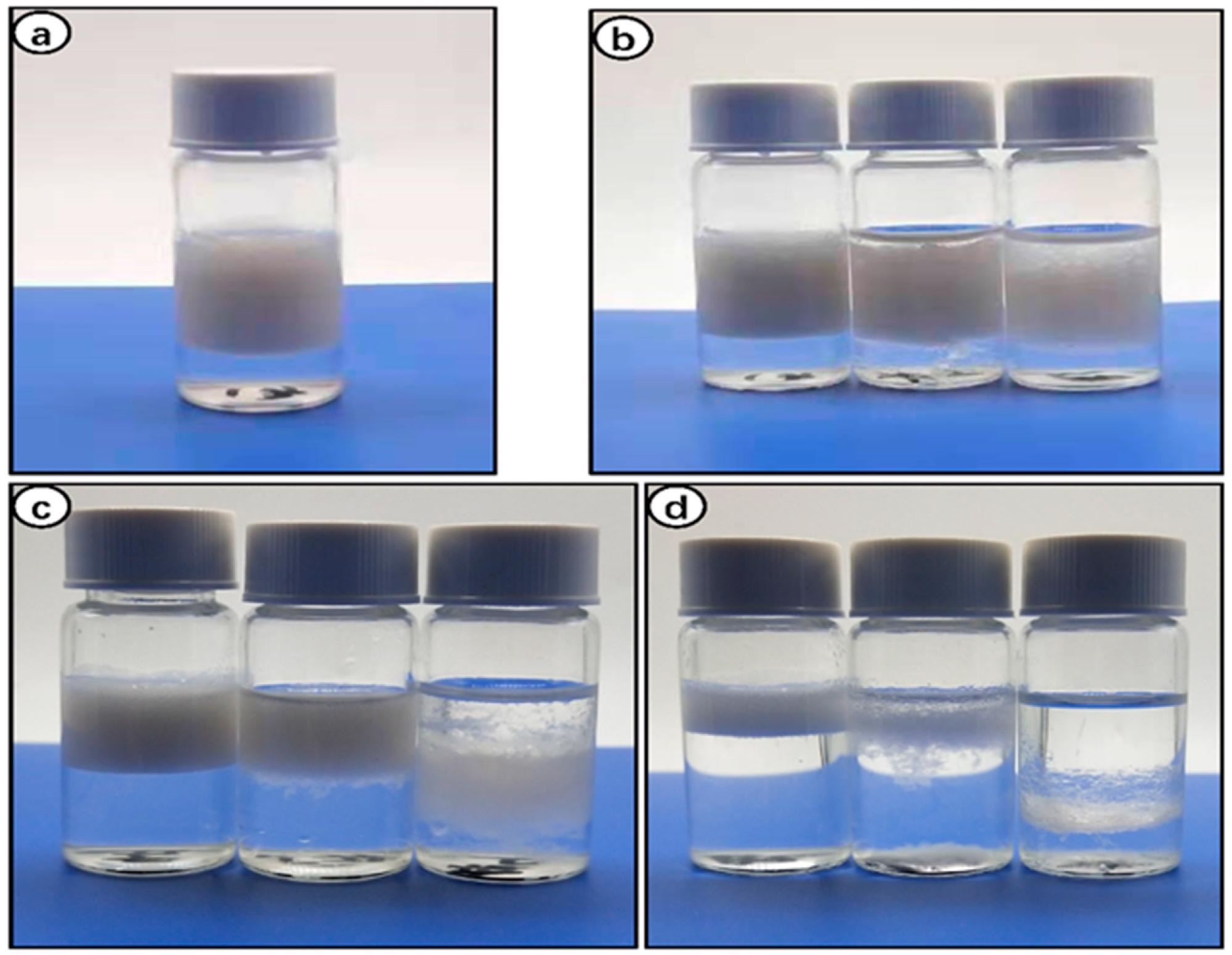
Oil/water Pickering emulsions after dispersing at 10,000 rpm for 3 min: (a) O/W, 1:9; RLCs = 0.5% (oil phase = n-hexadecane, water phase = RLC suspension). (b–d) From left to right, O/W ratio = 1:9, 3:7, 5:5. (b) RLCs = 0.5%; (c) RLCs = 0.3%; (d) RLCs = 0.1%. Image Credit: Pirah, S et al., Polymers
FTIR, XRD, TEM, and optical microscopy were employed to characterize the resulting concentrated solution. Finally, the authors used these recovered nanofibrils to produce a green Pickering emulsion. Optical microscopy was employed to observe emulsion particle sizes.
Study Findings
The study has demonstrated the dissolution of sisal fibers in phosphoric acid, which is a green solvent. The process is benign, cost-effective, environmentally friendly, and non-volatile. A rapid and efficient process, the dissolution is non-derivative, and the authors have stated that it can produce excellent results.
Using the recovered lignocellulosic nanofibrils for Pickering emulsion stabilizers is highly suitable and produces stable emulsifiers with moderate settlement rates. Emulsions prepared with these nanofibrils possess the advantages of limited oil droplet mobility and stability due to the production of viscous aqueous solutions and suspensions.
The prepared Pickering emulsions can be considered for use in technical emulsions and applications such as tack coating and fog sealing. Future anticipated industrial uses of these emulsions include applications in food, medical science, and cosmetics. In summary, this study has demonstrated a novel and powerful synthesis route for emulsions using recovered lignocellulose nanofibrils from sisal fibers, an abundant and renewable natural resource.
Further Reading
Pirah, S et al. (2022) Lignocellulose Extraction from Sisal Fiber and Its Use in Green Emulsions: A Novel Method Polymers 14(11) 2299 [online] mdpi.com. Available at: https://www.mdpi.com/2073-4360/14/11/2299
Disclaimer: The views expressed here are those of the author expressed in their private capacity and do not necessarily represent the views of AZoM.com Limited T/A AZoNetwork the owner and operator of this website. This disclaimer forms part of the Terms and conditions of use of this website.