Introduction In the thermal spray process the coating is built up from lamellas formed by rapid solidification of the melted or semi-melted droplets attached to the substrate. A typical coating structure is a pancake-like lamellar structure, where the flattening rate and adhesion between the lamellas, together with the coating material itself, define the main properties of the coating. Thermal spray coatings are often applied to improve the corrosion and wear resistance of the component. Therefore, low porosity and good adhesion are desired properties for the coating. HVOF (High velocity oxy-fuel) process is one the most potential methods for producing a good adherent coating with low porosity [1]. Ceramic coatings offer an interesting alternative to produce a protective layer over a steel structure due to the excellent chemical, corrosion and thermal resistance of the ceramic materials. Recently it has been demonstrated that the HVOF process is capable of producing denser coatings than plasma spraying [2-4]. Mechanical properties of coatings are in a major role when coatings are applied e.g. in wear environments. Thermal shock resistance is closely related to the fracture strength of the coatings. Combination of dense ceramic coating with steel substrate at elevated temperatures requires high coating fracture toughness. Some special properties are already demonstrated for nanocrystalline ceramics [5, 6]. Because of the relatively low temperature of the HVOF flame, the spray process must be carefully optimized in order to produce coating with a sufficient melting state and good lamella adhesion. In this paper the process mapping tool is introduced in order to optimize the HVOF spray process for ceramics. The effect of the microstructure on the mechanical properties of various ceramic composite coatings, when using nanostructured spray powder is discussed. In this paper properties of some ceramic coatings prepared by using HVOF and APS (Air Plasma Spraying) methods are discussed. Alumina and chromium oxide are commonly used ceramic coatings due their good resistance against wear and corrosion. Yttrium stabilized zirconia (YSZ) is used as a thermal barrier coating (TBC) and cordierite (2MgO .2Al2O3.5SiO2) as a component material has very low coefficient of thermal expansion [7]. These kind of composites are often used as refractory materials for industrial furnaces, heat exchangers, gas turbine engines and honeycomb shaped catalyst carriers in automobile exhaust systems [8, 9]. In contrast to cordierite, YSZ ceramics are frequently considered as a candidate for high temperature (HT) ceramic coatings [10]. In order to develop YSZ material with required properties, the information on microstructural optimization, property control, and understanding of the role of their nanostructure are strongly required - something already pointed out by Niihara, Sekino and coworkers [11-14]. Usually, the grains of tetragonal zirconia spontaneously transform to monoclinic structure in absence of a stabilizer, which results in a substantial degradation of the mechanical properties of this material [15, 16]. In all cases dense structure combined with good mechanical properties is of interest. It is tried to reach this goal by introducing HVOF spraying of nanocomposite materials. Experimental Procedure Spray Powder Development Different ceramic powders were produced by spray drying using various alloying elements. Novel powders based on alumina and zirconia were synthesized by using various chemical and mechanical routes at VTT and Osaka University. Production of alumina powders is described detailed elsewhere [17]. The YSZ-cordierite composition was prepared of three individual oxide powders, namely, ZrO2 powder (TZ-0, TOSOH Co., Japan) with a mean particle size of 30 nm, the 2.5 μm grade powder of near-stoichiometric cordierite (SS-600, Maruso Yuyaku Joint Vent. Setoshi, Japan), and Y2O3–powder with a mean grain-size of 33 nm (RU-P, Shin-Etsu Earth’s Co.; Japan) used as a stabilizer for monoclinic ZrO2. The investigated content of cordierite within the initial powder was 5 volume percent (vol.%). Slurries were grounded after mixing together by means of wet-ball-milling in ethanol for 24 h using zirconia balls having diameter of 5 mm. Subsequently, the slurries were dried and dry-milled for the additional consecutive 12 hours before agglomerating. Process Mapping and Coating Deposition Online diagnostic measurements were carried out for alumina using Tecnar DVP-2000 combined with Praxair HV-2000 spray gun and combustion chambers having size 19 mm and 22 mm. A large number of different spray conditions were measured by varying the total gas flow from 243 l/min to 361 l/min for propylene, and from 893 l/min to 1,050 l/min for hydrogen. Single splats were collected on polished stainless steel substrates in order to study the melting level of the particles under different spray conditions. The splats were produced by spraying using a low powder feed rate and the same standoff distance that was used in the coating deposition. Splats collected were studied by optical microscopy to determine the extent of melting of the particles. While the temperature data from diagnostic tests, based on the emissivity of a particle in-flight, provide the surface temperature of the particle, single splats enhance our understanding on the particle state. Variation of the spray parameters is presented detailed elsewhere [4]. The coatings were deposited using a Praxair HV-2000 spray gun. Nitrogen was selected as the carrier gas. The melting points of the oxide ceramics that are of interest for the present work vary from 2040˚C up to appr. 2700˚C. Therefore hydrogen and propylene was selected as fuel gases for alumina and chromia, and acetylene for zirconia based powders. Thermico CPF-2HP powder feeder was used to ensure sufficient powder feed rate also for experimental powders having a non-optimal size distribution and flow capability. Coatings were sprayed onto the steel plates having a size of 25×50×2 mm for microstructural and property characterization. The microstructural development was controlled by the traverse rate of the gun and the powder feed rate resulting to a certain thickness per pass. Reference air plasma sprayed (APS) Al2O3 (Sulzer-Metco 105SFP, -31+3.5 µm) and Cr2O3 (Saint-Gobain #3033, -15+5 µm) with APS NiCoCrAlY bond coat (Sulzer-Metco 461NS, -150+22 µm) were manufactured by Centro Sviluppo Materiali S.p.A. (Roma, Italy) with a Sulzer-Metco F4 torch [18]. Coating Characterization and Testing Electron microscopy using JEOL JSM-6400 (SEM) combined with PGT PRISM 2000 X-ray analyzer was used to study the coating microstructures. Hardness of the coatings was determined by Vickers microhardness method using a weight of 300 grams. Wear resistance of the coatings was evaluated by using rubber wheel abrasion test according to the standard ASTM G 65-91. Results A temperature-velocity plot for alumina is presented in the Figure 1 for hydrogen and propylene. Large variation in process conditions can be observed as well as two clear regions rising from use of different fuel gas. The optimization and analyzes for different process conditions are presented detailed elsewhere [4]. After process optimization coatings for more detailed testing were sprayed with conditions founded to be optimal for each material (Table 1). 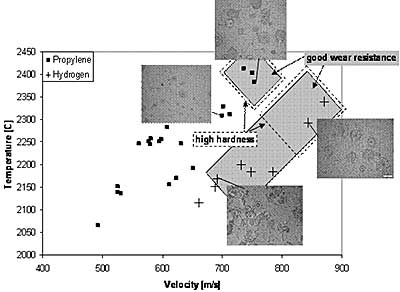 Figure 1. Temperature-velocity process map for alumina. Regions of good wear resistance and hardness of the produced coatings are outlined. Used limits are: hardness 1000 HV0.3, and abrasive wear 20 mg/30 min). Table 1. Summary of used powders. | Alumina | ref-Al2O3 | Praxair Al-1110, fused and crushed | 5-22 µm | Boehmite | n-Al2O3 -5% NiO | VTT, agglomerated and sintered | 2-21 µm | Boehmite | n-Al2O3 -5% ZrO2 | VTT, agglomerated and sintered | 2-29 µm | Chromia | ref-Cr2O3 | Norton, fused and crushed | 5-15 µm | Zirconia, Yttria | ZrO2-7%Y2O3 (7YSZ) | H.C. Starck, Amperit 825.090, fused and crushed | 5-15 µm | Zirconia, Yttria | ZrO2-6%Y2O3 (6YSZ)+ 5%Cord. | ISIR, VTT, agglomerated and sintered | 7-18 µm | The difference in microstructures of APS and HVOF sprayed ceramic coatings can be seen in micrographs in Figure 2. HVOF sprayed coatings show clearly improved density and less pores and cracks than the APS sprayed. Figure 3 compares wear resistance and hardness measured for various APS and HVOF sprayed coatings. 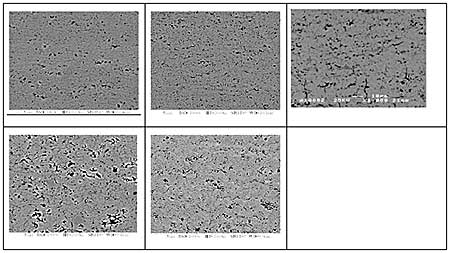 Figure 2. SEM micrographs of the coatings demonstrating differences in coating density between HVOF and APS processes a) Al2O3 (HVOF) [18], b) Cr2O3 (HVOF) [18], c) 6YSZ (HVOF) [18], d) Al2O3 (APS) [18], e) Cr2O3 (APS). 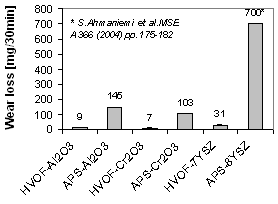 (a) 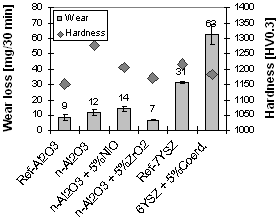 (b) Figure 3. a) Wear loss measured for various HVOF and APS sprayed ceramic coatings. b) Wear loss and hardness measured for HVOF sprayed ceramic coatings with various compositions. Discussion Figure 1 shows the different trend between fuel gases. The hydrogen-oxygen mixtures mainly results in a greater velocity of the particles compared to the propylene-oxygen mixtures. On the other hand, use of propylene offers a wider process window in terms of particle temperature and velocity, and therefore allows more variation in the process conditions. As a result, different temperature-velocity combinations produce a different melting state of the powder and different splat formation. With best melting state alumina splats are relatively well formed, with adequate spreading. With lower temperature-velocity range the degree of particle melting is decreasing. A clear correlation between particle melting behavior and the abrasive wear resistance and the hardness was found. HVOF Sprayed Coatings HVOF sprayed coatings show clearly improved density and less pores and cracks than the APS sprayed (Figure 2). Also the distribution of the pores of propylene offers a wider process window in terms of particle temperature and velocity, and therefore allows more variation in the process conditions. As a result, different temperature-velocity combinations produce a different melting state of the powder and different splat formation. With best melting state alumina splats are relatively well formed, with adequate spreading. With lower temperature-velocity range the degree of particle melting is decreasing. A clear correlation between particle melting behavior and the abrasive wear resistance and the hardness was found. HVOF sprayed coatings show clearly improved density and less pores and cracks than the APS sprayed (Figure 2). Also the distribution of the pores is more even and the size of the pores much smaller; this has been shown using image analysis techniques [18]. The difference is probably due to various factors. The typical temperature-velocity ranges for particles in ASP and HVOF spraying, which are the most important parameters affecting the coating quality show clearly different temperature and velocity profiles in the two techniques. In APS the particles are heated to a much higher temperature, but they obtain a considerably smaller velocity than in HVOF spraying. The plasma spray results in a considerably less dense and more porous structure than HVOF spraying because the droplets solidify already before they are fully flattened at the substrate, which obviously also results in poor interlamellar cohesion [19]. Oxide Coating Performance Figure 3a. demonstrates the vast difference in the performance of various oxide coatings sprayed by APS and HVOF spray. The abrasion wear resistance of the coatings as measured in a standardized rubber wheel abrasion test is improved more than ten fold, when the coating is made by HVOF spraying. The difference is more than 15 times with the alumina and chromia coatings where the spray parameters have been optimized. The HVOF zirconia coatings perform more than 20 times better than the corresponding APS coatings. However it must be noted that comparison reference value [20] is for Thermal Barrier Coating (TBC), where maximum density is not aimed. The developed cordierite alloyed yttria stabilized zirconia materials are candidates for high temperature use. Although there were some pores and cracks in the HVOF sprayed materials we were able to deposit a good quality coatings from 6% yttria and 5% of cordierite consisting material by HVOF demonstrating thus clearly that HVOF can be used to deposit also high melting temperature coatings that are candidates for thermal barrier coatings. It must be noted that no systematic process optimization was performed for HVOF sprayed zirconia coatings. Properties of the sprayed alloy coatings were quite close to those of the reference YSZ coatings. E.g, the abrasion resistance of the zirconia reference coating is only slightly higher than that of the alloyed coatings. This indicates that the cordierite alloying does not lower the mechanical properties of the coatings markedly and the high temperature properties may potentially be improved since cordierite alloying is expected to prevent high temperature grain growth of the coating [21]. As compared to the reference coating the hardness of all the coatings produced from the pure alumina nanopowder or ceramic alloyed nanopowders were as hard or harder than reference; only the coating produced using the nickeloxide alloyed nanocomposite powders were softer than the reference HVOF coating. The abrasion resistance of the various alumina based coatings also vary somewhat. The best wear resistance was obtained with the 5% zirconia alloying (Figure 3b). Conclusions HVOF spraying is demonstrated to be capable of producing oxide coatings with superior coating structure and wear properties as compared to conventional atmospheric plasma spraying. By alloying alumina with other ceramic materials coatings with increased hardness and wear resistance are produced. Best hardness, wear resistance and fracture toughness combination so far has been obtained with the Al2O3 – 5% ZrO2 coating. The abrasive wear resistance of the ceramic nanocomposite coatings seems to depend in a complex way on the mechanical properties of the coating such as hardness, fracture toughness and elastic properties. Coatings produced are considered to be potential candidates for a protective coating in harsh environments where good fracture toughness and excellent environmental resistance is needed. References 1. J.R. Davis (Ed.), “Handbook of Thermal Spray Technology”, Thermal Spray Society, ASM International, Materials Park, OH, USA, (2004) 338. A. Kulkarni, J. Gutleber, S. Sampath, A. Goland, W.B. Lindquist, H. Herman, A.J. Allen and B. Dowd, “Studies of the microstructure and properties of dense ceramic coatings produced by high-velocity oxygen-fuel combustion spraying”, Materials Science and Engineering, A369 (2004) 124–137. 2. A.J. Sturgeon, “The influence of fuel gas on the microstructure and wear performance of alumina coatings produced by the High Velocity Oxyfuel (HVOF) thermal spray process”, British Ceramic Proceedings, 54 (1997) 57-64. 3. E. Turunen, T. Varis, S-P. Hannula, A. Kulkarni, J. Gutleber, A. Vaidya, S. Sampath and H. Herman, “On the role of particle state and deposition procedure on mechanical, tribological and dielectric response of high velocity oxy-fuel sprayed alumina coatings”, Materials Science and Engineering, A 415 (2006) 1-11. 4. M.J. Mayo, “High and low temperature superplasticity in nanocrystalline materials”, Nanostructured materials, 9 (1997) 717-726. 5. F.A. Mohammed and Y. Li, “Creep and superplasticity in nanocrystalline materials: current understanding and future prospects”, Materials Science and Engineering, Volume 298A (2001) 1-15. 6. D.L Evans, G.R. Fisher, J.E. Geiger and Martin, F.W., “Thermal expansions and chemical modifications of cordierite. J. Am. Ceram. Soc., 63 (1980) 629. 7. Y. Hirose, H. Doi and O. Kamigaito, “Thermal expansion of hot-pressed cordierite glass ceramics”, J. Mat. Sci. Lett., 3 (1984) 153. 8. A.J. Dent, M. Oversluizen, G.N. Greaves, M.A Roberts, G. Sankar, C.R.A. Catlow and J.M. Thomas, “A furnace design for use in combined X-ray absorption and diffraction up to a temperature of 1200°C: Study of cordierite ceramic formation using fluorescence QEXAFS/XRD. Phys., B 208&209 (1995) 253-255. 9. Nettleship and R. Stevens, “Tetragonal Zirconia Polycrystal (TZP)”, Int. J. High Technol. Ceram., 3 (1987) 1–32. 10. E-H. Sun, Y-H. Choaa, T. Sekino and K. Niihara, , “Fabrication and mechanical properties of cordierite/ZrO2 composites by pressureless sintering”, J. Ceram. Process. Res., 1, (2000) 9-11. 11. E-H. Sun, T. Kusunose, T. Sekino, T. Adachi, M. Wada and K. Niihara, “Preparation of cordierite/ZrO2 nano-composite powders by a colloidal coating process”, J. Ceram. Soc. Jap., 110 (2002) 92-97. 12. E-H. Sun, T. Kusunose, T. Sekino and K. Niihara, “Fabrication and Characterization of Cordierite/Zircon Composites by Reaction Sintering: Formation Mechanism of Zircon”, J. Am. Ceram. Soc., 85 (2002) 1430-1434. 13. E-H. Sun, Y-H. Choaa, T. Sekino, T. Adachi and K. Niihara, “Pressureless sintering and characterization of cordierite/ZrO2 composites”, Mat. Res. Innovat., 6 (2002) 105-111. 14. M. Matsui, T. Soma and I. Oda, “Stress-Induced transformation and plastic deformtion for Y2O3-Containing tetragonal zirconia polycrystals”, Ceram. Soc., 69 (3), (1986) 198–202. 15. M. Watanabe, S. Lio and I. Fukuura, “Aging Behavior of Y-TZP”, Adv. Ceram., 12 (2000) 391–98. 16. E. Turunen, T. Varis, T.E.Gustafsson, J. Keskinen, P.Lintunen, T. Fält and S-P. Hannula, “Process optimization and performance of nanoreinforced HVOF-sprayed ceramic coatings”, Proceedings of 16th International Plansee Seminar, May 30 – June 3 2005, Reutte, Austria (2005), PM43. Vol. 1, pp. 422-433 17. G. Bolelli, V. Cannillo, L. Lusvarghi, E. Turunen, T. Varis, T. Fält and S.-P. Hannula, “Wear Behaviour of APS and HVOF Sprayed Ceramic Coatings”, International Thermal Spray Confernece, Seattle, 15th-18th May (2006), in press. A. Kulkarni, J. Gutleber, S. Sampath, A. Goland, W. B. Lindquist, H. Herman, A. J. Allen and B. Dowd, “Studies of the microstructure and properties of dense ceramic coatings produced by high-velocity oxygen-fuel combustion spraying”, Materials Science and Engineering, A369 (2004) 124-137. 18. S. Ahmaniemi, P. Vuoristo and T. Mäntylä, “Mechanical and elastic properties of modified thick thermal barrier coatings”, Materials Science and Engineering A, Volume 366, Issue 1, 5 February (2004) 175-182. A. Hirvonen, R. Nowak, Y. Yamamoto, T. Sekino and K. Niihara, “Fabrication, structure, mechanical and thermal properties of zirconia-based new ceramic nanocomposites”, Journal of the European Ceramic Society, (2005). Contact Details |