Some workpieces cannot be made using traditional procedures such as casting. In such instances, an additive manufacturing approach is a natural choice. The EWA project’s purpose is to optimize this method. It stands for “development of carbon-martensitic tool steels for the additive manufacturing of highly stressed forming tools using wire-arc additive manufacturing.”
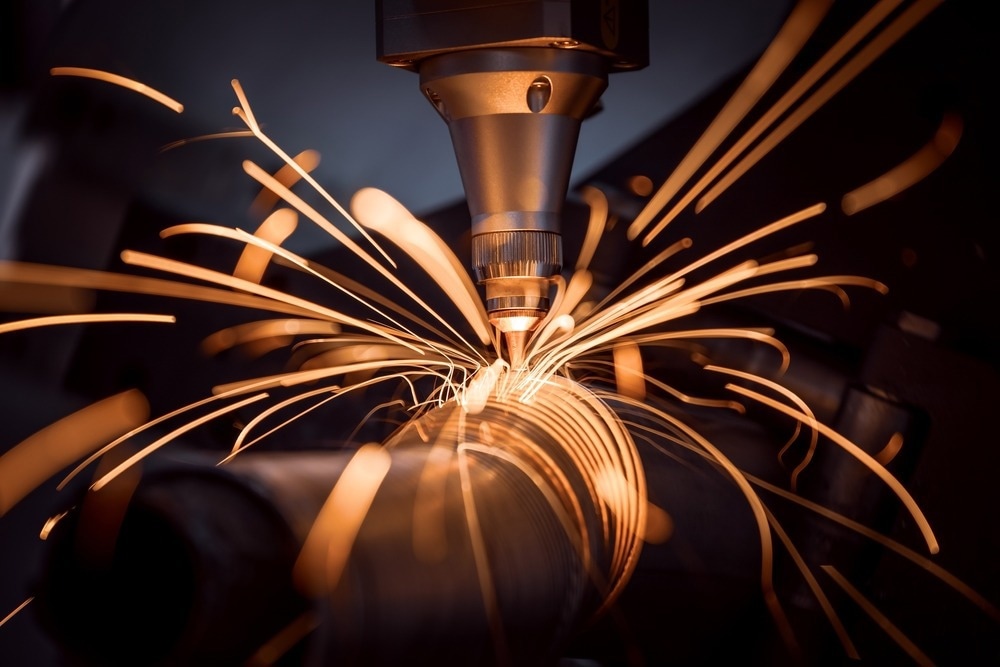
Image Credit: Andrei Armiagov/Shutterstock.com
Thin, powder-filled wires serve as the primary building blocks in this additive manufacturing technique.
To create punching and forming tools, additive processing is used. The Central Innovation Program SMEs of the Federal Ministry of Economics and Energy is funding Professor Sebastian Weber’s initiative at the Chair of Materials Technology at Ruhr University Bochum in Germany. On June 22nd, 2023, a kickoff event will mark the beginning of it.
Welding Without Rotary Swaging and Wire Drawing
Gas metal arc welding (GMAW) is the main foundation of the so-called wire-arc additive manufacturing (WAAM). Here, the initial components are low-cost metal wires. The EWA project uses so-called metal-cored wires, which are tubes with an outer diameter of at least 1.2 millimeters filled with metal powder.
These cored wires allow a high degree of flexibility in the alloy composition, which is produced directly in the cored wire. Due to the powder filling, which liquefies directly during welding, there’s no need to first produce a melt that would have to be reduced to the required wire diameter by means of rotary swaging and subsequent wire drawing.
Ulf Ziesing, Ph.D. Student, Ruhr University Bochum
Although it is frequently impossible to draw materials with high strength and a hard phase to the small diameter of the wires, they can be made as cored wires.
When using the WAAM technique, the material is applied solely where it is necessary by an underlying 3D CAD model. In other words, 90 to 100% of the material used during the process can effectively be retained all the way up to the finished workpiece.
Ziesing added, “This high degree of utilization translates into significant material savings and, consequently, an improved CO2 footprint compared to the conventional, casting-based processing route.”
Additionally, during GMAW, the molten material rapidly cools down, creating a state of high solution. All of this makes a workpiece produced using WAAM’s mechanical characteristics superior to those of a component manufactured conventionally.
Furthermore, it moves quickly—up to twelve kilograms of material can be applied in a single hour.
“All in all, this method has great potential for the production of individualized single components and complex small series in large format,” Ziesing concluded.