.jpg)
For more than 50 years the K Show has been the biggest internationally renowned trade fair for the plastics and rubber industry in the world and this year's K 2013 is no different. SABIC, a global leader in the Chemical, Polymer and Innovative Plastics industries, is at K 2013 showcasing a diverse range of their Innovative Plastics technologies and solutions in the mass transport sector, amongst others.
In this interveiw, AZoM talks to Kim Choate, Mass Transportation Marketing Director of SABIC’s Innovative Plastics business to find out more.
SABIC’s Innovative Plastics business offers a diverse range of solutions for specific applications, could you tell us a little more about the mass transport industries you serve?
I would like to talk about a couple of things in the aerospace and rail industry that are driving the new technologies that SABIC is showcasing at K 2013.
Aerospace Sector
In the aerospace sector we see several things happening. The number of planes is projected to double in the next 20 years, so there's big growth in the industry.
Research by Boeing forecasts that between now and 2032, there will be demand for 35,280 new airplanes, valued at $4.8 trillion USD. 14,350 of these new airplanes (41 percent of the total new deliveries) will replace older, less efficient airplanes.
Globally, airlines are experiencing growing pressure to not only reduce operating costs and improve customer experience, but also adapt to meet a multitude of tougher greenhouse gas emissions regulations. Innovative Plastics offers solutions that can help airlines meet the challenges of an ever changing market.
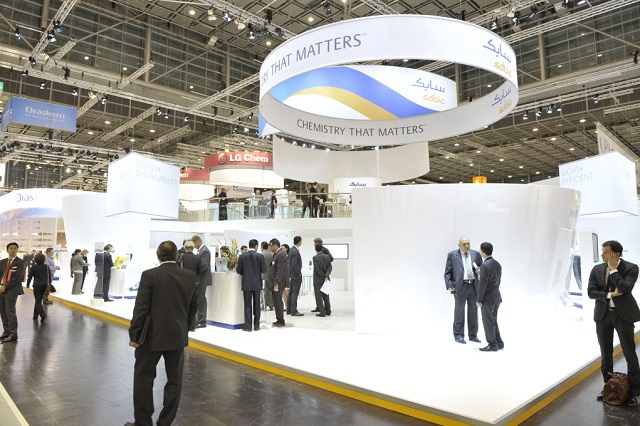
The impressive SABIC Stand at K Show 2013
Improved Aesthetics, Textures, Performance
Product wise, if you look at what's happening within the airlines and the industry itself, everyone is looking to differentiate their own brand, and to use a customized interior with unique finishes, colors and textures to drive this distinction. So, the airline brands are all competing to get that loyal customer experience and brand consistency across fleets.
At SABIC, we're seeing big industrial design trends that are driving a greater demand for a range of textures and different aesthetics inside the plane. This in turn has driven us to introduce some innovative combinations of technologies, not just one technology. One of the good examples that we have at K 2013 is our LEXAN™ XHR film and sheet along with LEXAN FST resin for injection molded parts.
These new products offer a range of benefits including weight reduction opportunities over more traditional materials, in a format that helps to meet tighter regulations while offering designers a diverse range of textures, colors and finishes to meet the exacting needs of their brands and customers.
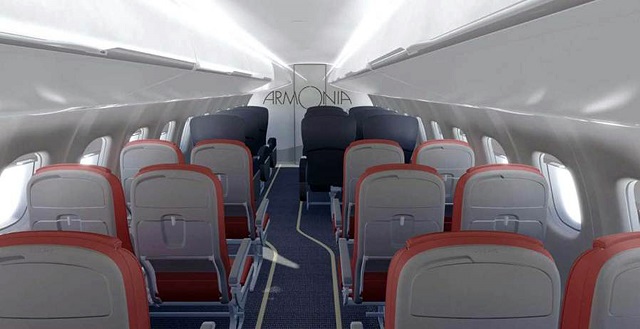
Geven Selected LEXAN XHR sheet for its Carribean Airlines
By offering a diverse product range based on a platform of proven technology, key customers can come to SABIC for a complete solution where they used to have to go to 3, 4, or 5 different companies to get their materials. From a manufacturing perspective, they can fulfill a range of requirements with materials from one supplier, all color matched to look the same and behave the same as they make the parts.
As a company, SABIC has invested a lot of time and development into how we can offer the right textures and colors with a consistent feel across different parts and materials that can be used with their current manufacturing capabilities. This family of consistent products is really driving a lot of change in the aerospace sector.
Enabling Improved Fuel Efficiency through Weight Reduction
If you look at the cost, 25 to 50 percent of the cost to operate an airline is actually just due to fuel, depending on the type of plane. Anything that can be done to reduce the weight burden of the interior, to improve efficiency, or to make the plane fly further or with less weight is of extreme value.
At the K 2013 show we have several solutions on display that help the aerospace industry improve efficiency. One of the key streams of recent development we are highlighting is a result of the fact that we're seeing an increase in demand to replace aluminum parts with injection molded plastic parts that can ultimately reduce part for part weight by up to 40 percent.
One particular development we have on display here at the K show is the innovative tray table arms that offer weight reduction in a luxury feel product. The polymer technology here is also being used in multiple other applications to address different parts and requirements, including mechanical parts throughout the plane as well.
Passenger Safety and Comfort
As global regulations change and improve, passenger comfort and safety are also high on the agenda for aerospace designers and OEMs. The challenge here is to offer unprecedented levels of safety without compromising on comfort, look and feel.
Designers and engineers are continually looking to quickly develop innovative and cost effective solutions for every part of an airplane, including the parts that passengers don’t necessarily see or notice. To support this, SABIC’s ULTEM 9085 product has been designed to not only meet customer requirements and regulatory specifications but to also be used in 3D printing manufacturing.
3D printing offers the industry the opportunity to make small batch parts very quickly, whereas before they were spending several months and large sums of money to make tooling for specific products and bespoke manufacturing processes.
Designers and engineers can now email a file and receive the parts with very short lead times. Or, they can quickly develop a mock up in the material the final product could be made from. This is potentially game changing in the industry.
In addition to increased demand for materials that deliver a consistent brand experience in terms of color and texture, we are also seeing the need for products that combine all of these factors and that can be used with a manufacturer’s existing equipment and skills.
For example, the lightest airline trolley in the world is the Norduyn trolley. At K 2013 they're on display featuring SABIC brand colors – we’re even serving complimentary drinks on them at the show. This is a great example of how the unique products from SABIC offer customers across the industry the ability to feature custom colored, custom designed, high performance products with a great consistency in quality, look and feel.
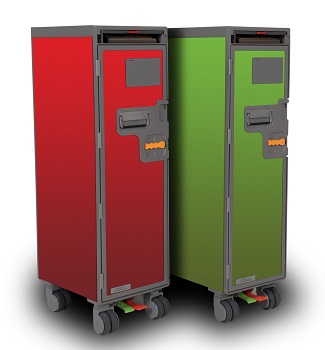
LSG Sky Chefs/ Norduyn award-winning in-flight trolleys
In the Rail Sector
In the rail sector, light-weighting is also important, but increasing regulation of the different parts is also becoming a primary concern. There's a new European regulation that's coming and it's driving unified - in some cases higher - stage D and regulatory requirements for the materials used in the railway industry. It affects much more than just the European market, but fortunately, because we've had this investment in unique products and solutions for the mass transportation sector for over a decade, we have technologies ready.
We've introduced several new products that are enabling manufacturers to meet the requirements of these new regulations using their existing production techniques very easily.
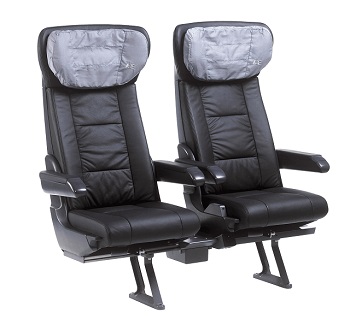
One particular example that we have on display is a business class rail seat from Grammer. We helped them with the interior parts as well. We have the seat here on display that people can look at and can sit in. We helped them create a drop-in solution that could be custom colored and has helped them to consolidate a range of parts, as well being able to go to market and meet the new, higher regulation using our materials without the need for excessive investment in new technology or re-tooling to any of their production costs.
In general, I would say those are still the big drivers for us – helping customers meet their needs efficiently. We continue to evolve more and more technologies for aesthetics as well as light weighting.
Grammer Railway seat using LEXAN FST resin
Can you tell us a little bit more about some examples of the materials you are replacing with light weight plastic and polymer solutions, offering improved performance and reducing weight etc.?
We are seeing an increase in the number of different applications of our materials and solutions. There are a number of inherent materials that we typically replace, some are plastic, some were thermoset, and some were metal. In all cases, thermoplastics can help to enable light-weighting vs. traditional materials, and specifying a different type of plastic can help to meet improved regulatory and performance specifications.
On average, we're getting 12-plus percent weight improvements. It's happened across the board but there's still a lot of aluminum and thermoset materials that are used. Thermoplastics should strongly be considered for manufacturing speed and efficiency, as well as light-weighting at the same time.
We are particularly interested in how your solutions are blending with innovative manufacturing techniques to reduce development lead times and improve product performance. Can you explain the benefits of your ULTEM and 3D printing and why it's valuable from a technical perspective?
ULTEM 9085 resin, first of all, is already a material that is used heavily in the aerospace industry; so many companies know how the product performs and how it offers some unique properties over other materials. Because it's also able to be used in 3D printing, our customers have a material that has been demonstrated to ‘work’ even before you start to make a part. They can print production parts with the confidence that they're going to pass the regulatory requirements, versus having to make the parts wondering whether they will perform in their final application.
Also, because our customers are able to rapidly prototype products with the specific mechanical performance as it would have in its final production, even very complex designs can be printed and tested, offering unbelievable opportunities to rapid prototype and test new parts.
Strong, lightweight, flame-retardant ULTEM 9085 resin helps to address one of the biggest challenges for aerospace OEMs – the ability to produce small volume parts quickly and cost-effectively. Together with Fused Deposition Modeling (FDM®) technology from Stratasys, Inc., this material enabled Stratasys’ customer, Taylor-Deal Aviation LLC – based in Dallas, Texas – to create specialty fluid and air handling parts in hours rather than weeks, while meeting the latest industry regulations for flame, smoke and toxicity. Photo courtesy of Taylor-Deal Aviation LLC.
ULTEM 9085 resin offers the ability to take out a lot of weight, versus the metal that's always traditionally been used, with a manufacturing technique (3D printing) that offers extremely low time limits to make parts. The fact that ULTEM 9085 resin is the industry’s material of choice in 3D printing lets designers and engineers make the parts they want quickly in a format that they know will meet the regulatory requirements.
The aerospace industry in particular is increasingly realizing the benefits of 3D printing in product development, particularly when it comes to being able to quickly test new designs and features in the finished material.
I was quite interested to read about the replacement and enlargement of the global fleet in the aerospace industry. Do you find that you are getting involved much earlier in the design process of these new aircraft?
I would say yes. Even some of the new aircrafts – we're already involved with multiple airlines to help design and suggest innovative materials to help achieve greater performance, efficiency and quality.
I would say we are involved earlier and more broadly than we were before. So the breadth of the technology they want to use and the changes that they would like to see are broader than they have ever been, as well as the willingness to look at and evolve in line with new technologies available in the market.
Our products offer some unique opportunities for improved performance and the market wants to understand these opportunities as early in the design process as possible.
With respect to existing fleets of aircraft, are you finding that this market is growing for your products and services?
We are engaged in the retrofit market, across the board and at all production tiers. I can say that in almost every case, we're actually able to offer lighter weight solutions and help to reduce the costs for the airlines, as well as their tier suppliers. More recently we have found that a collaborative approach on new manufacturing technologies allows our customers to quickly and efficiently get their parts ready to go to market earlier and with greater precision.
I would say that what makes SABIC unique in this space is that we're really collaborating very closely with OEMs all the way through the value chains for these industries. It's really helped drive a total solution. That's something that we're very proud of, something that we work very hard at.
One of the key factors affecting the automotive industry, at the minute, is the full life cycle cost of materials. Are you finding there's more focus on it for you?
Obviously there is definitely piqued interest in the life cycle of every product. First of all, how long the materials last in retrofitting is one of the benefits we have. Many of our materials last longer than some traditional materials, so there is benefit for everyone.
The retrofitter is obviously trying to help the airlines save money by extending the life of the new interior. You do see an improved trend, whether it be gearing the manufacturing process of the planes originally and/or what they do with the materials when they retrofit. There are several technologies that allow us to take that material and use it again either in planes or another industry because we're so broad. We can actually enable those materials to be used many times and enhance the life cycle. We can get two or three or four life cycles versus just one and put it in a landfill with traditional materials.
The final piece I would like to focus on is what's next for SABIC?
What you will see next, over the coming months for us, is a broader portfolio - especially with the rail regulations…making sure our materials meet the regulations, that we’re set up in the right way to drive the right cost and manufacturing capability for the rail tiers so they can meet the new demand.
Also, you are going to see a breadth in both aesthetic and light weighting capabilities for some new technologies that will be out between now and Hamburg Airshow.
At the Hamburg Airshow SABIC will feature even more technologies that are friendly to the designers of the airlines. They all want that new experience. Custom materials, custom colors, they all look and feel different and you're going to see much broader expansion of design freedoms that the retro designers will have to make their future design.
I would say, along the way we're not going to lose that spirit of collaboration. We're going to be closely tied with the airlines and OEMs to make sure that we're delivering materials that are relevant to them, helping their processes throughout the value chain.
Have you identified any new potential markets with the new products that you're developing? Have you found any obscure industries, companies coming to you now looking for advice on where your materials might fit in their space?
I really focus on mass transportation, but I can see one example is Stratasys System's new 3D printing. We started that collaboration specifically to help the aerospace industry succeed and get production up fast and efficiently, but in an extremely reliable format. As a result of that we've expanded to multiple industries and enabled multiple industries to make parts and look at designs and draw from the collaboration we have there.
I wouldn't necessarily characterize Stratasys as obscure, either. They're a major player in 3D printing. Their collaboration has been great for us. We are very pleased to be a part of it.
So what does the future hold for SABIC technology?
At the K Show specifically, what we're seeing here and what we're demonstrating is really a diverse and relevant portfolio that can serve the needs of customers from multiple industries.
This is how our business is oriented, focusing on our customers, focusing on their trends and challenges. It's demonstrated in the booth, all of our displays are pointing at the multiple solutions we have across multiple different parts of our business that address some very common, very important trends within multiple industries.
Whether it's mass transportation, automotive, we're also focusing on building and construction so you'll see a lot of LEXAN polycarbonate solutions in the building and construction industry whether it's sheet materials for cladding and glazing, for roofs, etc.
Another important area for us is the medical field, the healthcare industry. Between our Polymers business and our Innovative Plastics business, we've got a great selection of solutions within the healthcare industry.
They're really helping to enhance patient and caregiver safety. I think if you look specifically on the Innovative Plastics side, we're introducing antimicrobial materials that are really important - we think - in helping reduce healthcare associated infections in hospitals.
That's really important for anyone that has to visit a hospital or anyone who has visited. On the Polymer side, we're featuring a solution which is a replacement for glass. It's a plastic solution for dispensing medicine. It has exceptional clarity.
The intent is to really enhance dosing accuracy so there is much less chance that you're going to have an inaccurate dosage which, in turn, helps enhance safety for patients.
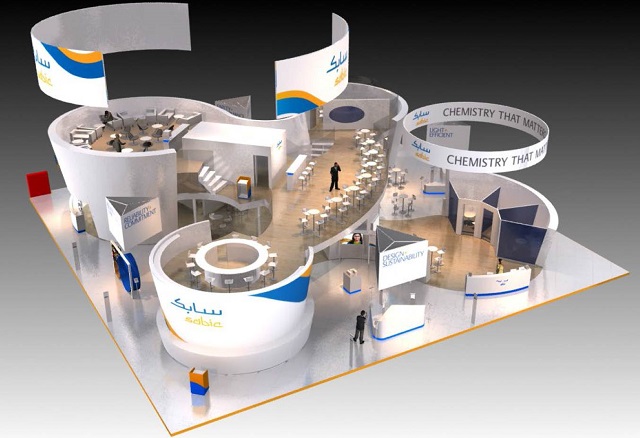
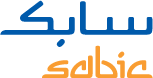
This information has been sourced, reviewed and adapted from materials provided by SABIC Innovative Plastics.
For more information on this source, please visit SABIC Innovative Plastics
Disclaimer: The views expressed here are those of the interviewee and do not necessarily represent the views of AZoM.com Limited (T/A) AZoNetwork, the owner and operator of this website. This disclaimer forms part of the Terms and Conditions of use of this website.