Electrolytes
The electrolyte material is important in both anode and electrolyte supported fuel cells. Electrolyte powder can be transformed into supports, applied as a barrier layer or added to electrode layers to enhance the performance. fuelcellmaterials offers many surface area ranges and several types of formulations to meet the demands of customers (Figure 1).
.jpg)
Figure 1. Electrolytes
Nanoscale Electrolyte Powders
These are nanocrystalline materials containing 5-10 nm particles. Nano grade powders provide exceptional amounts of active surface area to lower processing temperatures and to expand triple phase boundaries.
Ceramic Grade Ceria Powders
fuelcellmaterials offers specific grades of samarium- or gadolinium-doped ceria powders for numerous cell structure applications. Tape cast grade powders are customized for methods that need high slurry solids loadings, such as slip or tape casting. Mid-grade powder is designed to offer superior sinterability at minimal processing temperatures. These powders are ideal for pellet pressing and other non-aqueous manufacturing methods.
Micron-Submicron Electrolyte Powders
fuelcellmaterials provides a wide choice of micron to submicron powders, such as LSGM and YSZ. The wide selection of particle size ranges guarantees that customers will always have access to the appropriate materials to meet all of their needs.
R&D Focused Materials and Support
fuelcellmaterials customize all of their products and businesses to suit the requirements of researchers across the world. The materials are provided in small quantities and can be shipped the next day so that the customer’s research is not interrupted. Figure 2 depicts the characteristics of the electrolytes offered by fuelcellmaterials.
.jpg)
.jpg)
.jpg)
.jpg)
Figure 2. Key characteristics of the electrolytes offered by fuelcellmaterials.
Cathodes
fuelcellmaterials provides a variety of powders with superior oxygen ion conductivity for all SOFC cathode requirements. The varieties include LSM, which is an industry tested standard, and LSCF and LSC, which can be applied for lower temperature applications. Composite powders such LSM/YSZ and as LSCF/GDC are also offered for application in multilayer cathodes. These composite materials broaden the triple phase boundary length to boost electrochemical performance.
fuelcellmaterials' cathode powders (Figure 3) are manufactured in a ISO 9001:2008 certified unit with stringent controls on vital features such as surface area, stoichiometry, and particle size distribution.
.jpg)
Figure 3. fuelcellmaterials' cathode powders
Expanded powder production capabilities facilitate the production of superior quality materials cost effectively at each step of a customer’s R&D process. fuelcellmaterials enables customer growth right from stage one of design & development to pilot scale, and eventually to meet megawatt volumes for full scale production.
By utilizing scalable processing equipment, fuelcellmaterials ensures similar powder characteristics at every stage of development. Expanded manufacturing capabilities allows fuelcellmaterials to offer quicker turnaround times to provide stringent delivery needs.
A Step Above with Inks and Pastes
Cells can be fabricated by the customers to improve the overall performance, using cathode inks and pastes. Cathode powders are designed for a broad range of processing methods such as screen printing, aerosol deposition, painting, and tape-casting. It is possible to obtain cathode powders in the form of a paste, which enables researchers to just focus on working on core technology. The key properties of the cathode powders are depicted in Figure 4.
.jpg)
.jpg)
.jpg)
.jpg)
Figure 4. The key properties of fuelcellmaterials' cathode powders
Coatings
fuelcellmaterials’ coating solutions deliver the reliability, stability and performance required for the challenging applications of customers (Figure 5).
.jpg)
Figure 5. fuelcellmaterials’ coating solutions deliver the reliability, stability and performance required for the challenging applications of the customers.
Chromlok™ System
The ChromLok™ system from fuelcellmaterials is an innovative technology that provides high-temperature protection to metallic parts used in solid-oxide fuel cell systems. The ChromLok™ system has many complementary oxide coatings designed to prevent the discharge of harmful chromium species from stainless steels when heated at high temperature.
Manganese cobalite (MCO) coating (Figures 6 and 7) is one of the coating systems offered by fuelcellmaterials, featuring superior protection and low resistance qualities. These qualities make it suitable for cathode active-areas that demand electrical conductivity. Additional coatings such as non-active, insulating coatings are compatible with a Ni-based anode side coating and common seal materials.
.jpg)
Figure 6. MCO coating after operation
.jpg)
Figure 7. Long term electrical performance of MCO coated ferritic stainless steel
This coating technology has been established over several hours of testing and over 10,000 coated parts. The success is due to its high performance, quality standards, and service. The team at fuelcellmaterials are able to offer customers access to their advanced facility, where they can help to create customized coatings to meet specific requirements.
Alumi-Lok™
fuelcellmaterials supplies an aluminization coating to shield the non-active area of the interconnects and crucial balance of plant components from the impact of high temperature corrosion. This coating ensures a cost-effective solution is maintained as it can be processed simultaneously like the other coatings on interconnects.
Prototype Manufacturing
Prototype manufacturing (Figure 8) covers the following aspects:
- Interconnect coating to meet specifications
- Prototype batches for process validation and stack tests
- Components are coated by the dedicated coating team
.jpg)
Figure 8. Prototype manufacturing
Manufacturing Scale-up
The manufacturing scale-up (Figure 9) involves:
- Contract coating batches for intermediate quantities
- Early stage manufacturing to meet specifications using fuelcellmaterials' proven production line
- Substantial cost reductions for large orders
.jpg)
Figure 9. Manufacturing scale-up
High-Volume Manufacturing
High-volume manufacturing (Figure 10) includes
- License product and transfer technology
- Easy integration of fuelcellmaterials’ technology into customer's manufacturing system
- Materials supply agreements to guarantee all requirements are met
.jpg)
Figure 10. High-volume manufacturing
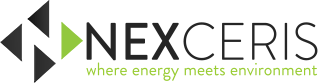
This information has been sourced, reviewed and adapted from materials provided by Nexceris, LLC.
For more information on this source, please visit Nexceris, LLC.