In a factory, a line fills up to 50,000 cans per hour, and then seams the filled cans. An “Automated Clean in Place” program featured in the filling machines allows them to be cleaned by flushing with large volumes of water and chemicals.
Water Intrusion Problem and Solutions
Allied Reliability Group uses oil analysis to monitor the main oil reservoirs. Over a period of five months, the main drive encountered recurring problems with water intruding into the gearbox and oil tanks. The oil was frequently changed and the seals were examined and replaced, but these actions did not solve the issue.
Allied Reliability Group suggested supplying dry air to the oil reservoirs. The overpressure was limited to a small level to prevent blowing out the seals. This method eliminated the water intrusion problems.
In the same factory, a bottle washing machine is used to rinse bottles before they are filled. The translation chain is driven by gearboxes to move bottles through the machine. Vibration measurements have been successfully employed for condition monitoring of the ingoing shaft that operates at 55 rpm.
However, the outgoing shaft runs at only 1 rpm, much too slow for accurate vibration measurements. For this reason, oil analysis is carried out on the shaft lubrication reservoir every three months.
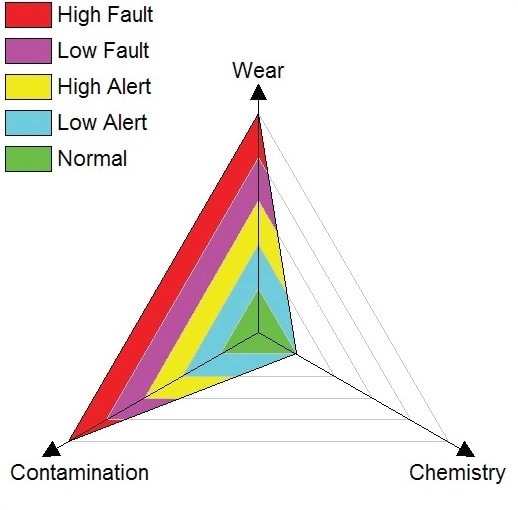
Figure 1. Oil analysis detects problems in slow moving shaft
A sudden increase of wear particles in the oil was observed using the 5200 Minilab. The first step was to change the oil and re-running the oil analysis, but the new analysis also showed a high level of wear particles. The number and size of wear particles continued to increase, showing particles larger than 40 µm. The machine was shut down and inspected at the first planned stop. The inspection showed a severely damaged bearing on the outgoing shaft.
The issue was resolved by overhauling the reduction gearbox. If this problem had not been identified by oil analysis, the gearbox would have broken down and caused other components to fail. Production would have been lost because the line could not run the rinsing machine until the repairs were complete.
The same factory uses a labeling machine that can run at 60,000 bottles per hour. The high complexity and structural limitations of this equipment means that oil analysis can only monitor certain parts of the machine. Oil analysis of the gearbox reservoir showed a large increase in the dielectric constant, an increased viscosity, and a water intrusion.
An inspection of the gearbox revealed a large amount of glue intruded into the oil reservoir due to a seal failure. If the problem had not been detected by oil analysis, the gearbox would eventually have stopped, causing high repair costs and production losses. Accurate oil analysis delivered relatively inexpensive corrections that addressed the issue during the next scheduled production stop.
A steel mill employs a cold rolling process, where metal stock passes through one or more pairs of rolls to reduce its thickness and thickness variations. The skin pass is the final cold rolling pass, involving the least amount of thickness reduction, usually 0.5% to 1%.
The skin pass also produces a smooth, uniform surface on the rolled steel plate. The numerous reducers that drive the skin pass are lubricated from a shared oil reservoir holding 6,000 liters (1585 gallons) of Shell Omala 220 oil.
A recent oil sample revealed an increased ferrous index, a drop in viscosity from 220 cSt to 82 cSt, and an increased number of particles. Allied Reliability Group advised the steel mill to urgently examine the oil reservoir. The inspection revealed that several heating elements failed which caused an increase in the particle count and ferrous index. The inspection also showed a failure in the circulation pump which caused the oil to overheat and reach high local temperatures.
The steel plant replaced the broken heating elements, repaired the circulation pumps, and replaced the oil during a previously planned outage. A new oil sample taken from the same point revealed that the issue was solved. If the plant had continued to run the machine with bad oil, the gearboxes would have been damaged, ultimately leading to increased repair expenses and production loss due to an unplanned outage.
In the same steel plant, the vibrations of faster-moving shafts are monitored using vibration measurements. However, a shaft driving a gearbox at 9 rpm moves too slowly to make effective vibration measurements. Therefore, an oil sample is analyzed every three months.
The most recent oil sample revealed an increase in particle count and ferrous particles. Vibration analysis of other shafts driven by the same gearbox did not reveal any anomalies. The gearbox was opened up and examined at the next planned stop. The rolling elements of the slow moving axle revealed clear signs of grinding.
The bearing’s outer ring was black because of the extreme heat produced by the grinding. The bearing would have obviously broken down if it had not been replaced. In this application, oil analysis saved a considerable amount of money by minimizing repair costs and by avoiding a production outage.
In a steel producing plant, gases from steel convertors are removed by using a 3 meter diameter fan that turns at 1000 rpm. These gases are very hot that fan blades have to be cooled down with water. As a result, steel dust is adhered to the fan blades, causing them to go out of balance.
To compensate for this imbalance, four oil chambers are integrated into the fan, arranged at 90° from each other around the diameter of the fan. Oil is pumped between the chambers to balance the fan. In this balancing system, oil analysis is carried out on a regular basis.
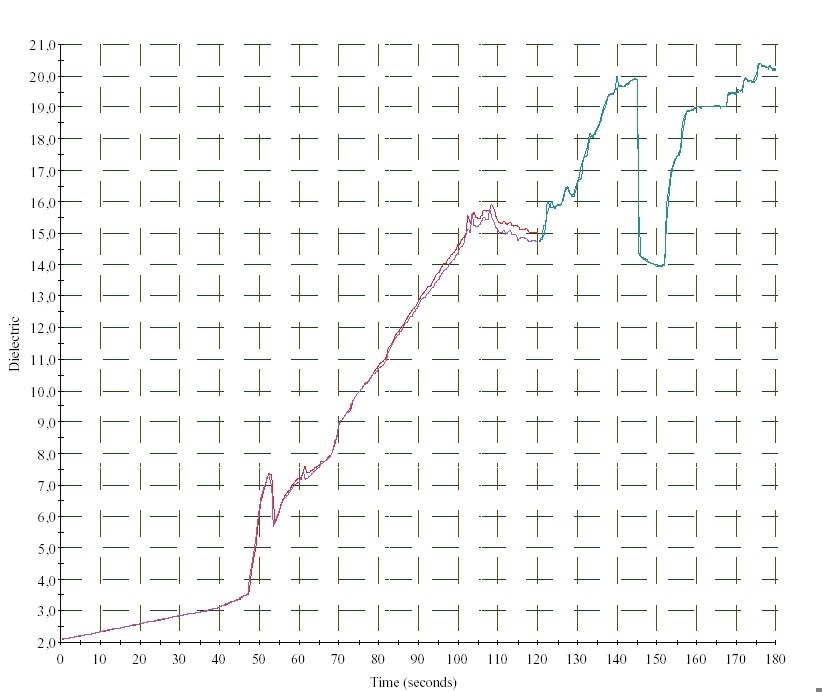
Figure 2. Oil analysis detects problem in fan balancing system
At a certain point, a large increase in the level of water and contaminants was identified in the oil. The issue was immediately reported to the maintenance team, which planned an inspection at the first scheduled stop. A couple of days after the analysis was carried out and before the inspection, the oil pump crashed because of the high water level. An inspection revealed a problem with one of the seals, allowing the cooling water from the fan blades to enter into the balancing system.
An oil sample retrieved from a piston compressor revealed a high water level and the presence of ferrous particles. The compressor was overhauled based on these results. During this inspection, the camshafts revealed high water levels. The wear was presumably caused by the reduction in the lubricating properties of the oil due to water intrusion. A failure of the water separator caused this water intrusion. Here, oil analysis minimized repair costs and eliminated a production outage.
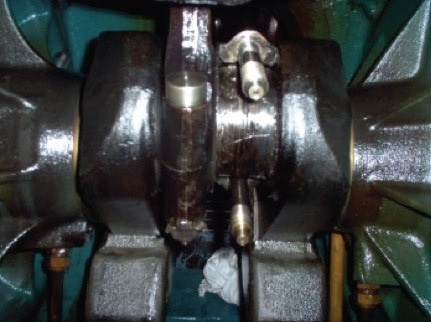
Figure 3. Oil analysis identified problem in piston compressor
These applications are typical of the savings in repair costs and lost production that can be provided by oil analysis. Asset health monitoring finds defects early to prevent unexpected failures and help the organization plan and schedule maintenance. The 5200 Minilab provides clear indications of metal wear, lubricant chemistry and contamination. The instrument also generates machinery health trend analysis to support data driven predictive and preventive maintenance decisions. Lubricant condition monitoring also conserves oil and reduces oil disposal costs by driving maintenance on an as needed basis.
Niels Maes, Asset Health Analysis, Allied Reliability Group
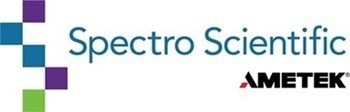
This information has been sourced, reviewed and adapted from materials provided by AMETEK Spectro Scientific.
For more information on this source, please visit AMETEK Spectro Scientific.