Nov 28 2017
.jpg)
Liquefied natural gas (LNG) has been a niche product for a long time because of its energy-intensive production process. Of late it is becoming a progressively hot topic. The reason for this is that liquefaction enables simpler transportation: in LNG form, natural gas can be transported in tankers meant especially for this purpose. For long-distance transport, this is more financially appealing than the construction of pipelines for non-liquid natural gas. In this article we can learn how natural gas travels from the borehole to the customer in the form of LNG, and what role chemical analyzes play in this process.
Liquefy Natural Gas, Save on Transport Costs
Natural gas condenses at about -162 °C. The process of liquefying it requires substantial energy expenditure that is why LNG had only limited commercial importance for a long time. However, in comparison to its gaseous equivalent, LNG offers benefits for transportation because it is not readily flammable and requires six hundred times less space. Thus, LNG can be transported via tanker truck and freight ship– in contrast to standard natural gas, which is transported via piping.
Liquefying natural gas thus allows it to be transported even to locations which are far from gas fields and not accessible via pipelines because of the difficulty involved in their construction or the high cost. The United States Department of Energy has designated LNG as a significant factor in accomplishing American economic and environmental targets1, based on the fact that natural gas is available in huge quantities and the CO2 output per joule of energy obtained from natural gas is 29% and 44% lower than that obtained from oil and coal2 respectively.
Pipeline Transport to Liquefaction Plant
After it has been extracted, raw natural gas that is meant for liquefaction into LNG is transported to a liquefaction plant via piping. The unprocessed natural gas contains many sources of contamination, usually including high quantities of water which have the potential to freeze or form solid hydrates with the hydrocarbons and CO2 also present. Hydrates and ice can block the pipeline. So as to prevent this, monoethylene glycol (MEG) is injected into the borehole flow at the wellhead, which provides frost protection in the pipeline and prevents the development of hydrates.
Removing Contamination
The flow does not straightaway reach the liquefaction plant from the pipeline outlet, as the sources of contamination in the gas (including the MEG that was previously added) must be eliminated first in order to prevent complications in the process later on. The flow first passes through the slug catcher. Here, the heavy, aqueous phase containing the lighter condensate (oil phase), the MEG and the gas phase are separated from one another, with the assistance of gravity. The MEG is prepared and reused.
The gas phase is then transported into the liquefaction plant. Further purification steps happen at this point before liquefaction starts: First, particles and any residual condensate are eliminated in the oil separator. The carbon dioxide and hydrogen sulfide are then eliminated via amine scrubbing process. Next, water vapor is taken away, a procedure that involves glycol dehydration. In this, the gas flows upward via an absorption column while a glycol (monoethylene, diethylene, triethylene, or tetraethylene glycol) flows in the opposite direction and the water is physically absorbed during the procedure. The structured packing of the column increases the contact surface of the gas and glycol, and therefore the water absorption. The glycol is recreated by vaporizing the absorbed water, and it can then be reused.
Lastly, the mercury is eliminated as it can corrode parts of the plant and catalysts that come into contact with the gas flow – mainly heat exchangers, which are usually made of aluminum and are required to cool the natural gas. Various adsorption procedures are available for the purpose of eliminating mercury, such as using ion exchangers, impregnated activated carbon filters or molecular sieves.
Glycol Recovery
After the separation process in the slug catcher, the monoethylene glycol is recovered from the aqueous phase. When it comes out of the slug catcher, the glycol is contaminated with water, salts and tiny corrosion particles. The MEG regeneration system eliminates most of this contamination, making the MEG suitable for reuse. Periodic analyzes of the glycol are essential to guarantee that it can continue being used.
This also applies to the glycol involved in the procedure of drying the natural gas. The parameters that need to be established here are the pH value, cations, anions, organic acids and water content. Ion chromatography is an appropriate technique for de-termining organic acids and ions in monoethylene, diethylene, triethylene, and tetraethylene glycol (for instance, chloride according to ASTM E2469). Any residual water can be determined using Karl Fischer titration. This is in compliance with ASTM and offers highly reproducible and precise results.
.jpg)
Table 1. Application examples for MEG analysis.
Number |
Title |
AN-C-062 |
Five cations including iron in monoethylene glycol |
AN-S-311 |
Organic acids in addition to standard anions in monoethylene glycol (MEG) applying a Dose-in Gradient |
Amine Scrubbing
CO2 and H2S are removed by means of amine scrubbing. During this procedure, an aqueous amine solution such as methyl diethanolamine (MDEA) absorbs both gases. In «accelerated» MDEA solvents, additives such as piperazine improve the chemical stability and the CO2 absorption capacity of the MDEA for more effective amine scrubbing.
Testing the gas scrubbing solution involves determining the amine concentration, the solvent strength, the alkalinity and the CO2 and H2S content – all of which can be measured via titration – as well as establishing the ratio of MDEA to piperazine (refer Figure 1) and the content in heat-stable salts, achievable through ion chromatography in both cases.
.jpg)
Figure 1. Ion chromatogram of the determination of MDEA and piperazine in a gas scrubbing solution. The sample was automatically diluted at a 1:20 ratio and injected without further sample preparation. The separation took place on the Metrosep C 4 - 150/4.0 column, and detection was carried out using conductivity detection without prior suppression.
Table 2. Application examples for gas scrubbing solution analysis.
Number |
Title |
AN-S-343 |
Heat-stable salts in an MDEA scrubber solution |
AN-PAN-1003 |
Amine («rich» and «lean») and free total CO2 |
AN-P-058 |
Amines in gas scrubber solutions using IC and pulsed amperometric detection |
Fractionation and Cooling
The natural gas currently is composed mainly of methane (over 90%) and ethane, as well as small quantities of nitrogen and heavier alkanes such as butane and propane. Propane and all heavy gases, which are referred to as natural gas liquids (NGLs), are separated from the natural gas flow during the following step using a fractionation column. Individual components of the NGLs are isolated from one another by means of additional fractionation, and can be sold as butane, propane and so on. In certain cases, they are also employed as coolants directly on site in the liquefaction plant. The residual lightweight natural gas fraction, which comprises of mainly methane and only small quantities of heavier hydrocarbons and nitrogen, is currently ready to be liquefied.
Cooling occurs in three steps, during which the gas flows through about 1,500 km of piping in total. So as to market the liquefied gas as LNG and gain permission to use it in a fuel gas system, part of the remaining nitrogen is removed during the last step.
Transportation as a Liquid
In the form of LNG, it is possible to transport the natural gas via special LNG tankers. This is the only reason for liquefying the natural gas: after transportation, LNG is commonly vaporized again so as to acquire energy from it. So far, the direct usage of LNG as fuel remains uncommon.
LNG tankers are usually identifiable from their spherical liquid gas tanks, the top half of which is above the deck. The spherical shape is perfect for both the pressure resistance and heat insulation of the tanks. As vaporization cannot be completely prevented even with good insulation («boil-off»), several mechanisms are in place to guarantee that the pressure in the tanks does not surpass the permitted maximum. For instance, the vaporized natural gas can be used for ship propulsion.
Returning to Gas
Once it has reached its destination port, the LNG has to be vaporized again. The regasification of the LNG happens in a heat exchanger, where a warmer medium pushes the LNG to the ambient temperature. The natural gas is then sent on its way to the customer in gaseous form through pipelines.
.jpg)
Figure 2. The LNG process with selected secondary processes and the associated chemical analyzes.
References
[1] http://energy.gov/fe/science-innovation/oil-gas/liquefied-natural-gas (accessed November 25th, 2016)
[2] http://naturalgas.org/environment/naturalgas/ (accessed November 25th, 2016)
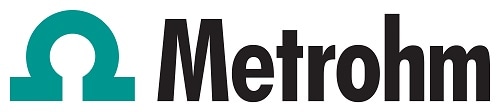
This information has been sourced, reviewed and adapted from materials provided by Metrohm AG.
For more information on this source, please visit Metrohm AG.