Metallic powders produced by inert gas atomisation are supposed to be spherical in shape, but in fact suffer from a major problem know as ‘satelliting’ in which smaller particles get stuck to their surface. This problem gets worse as powders are made finer, resulting in poor flow properties and a lower than expected packing density, which can be critical for advanced HVOF and plasma spraying applications.
Following the award of a SMART R&D grant by the UK Government, Atomising Systems limited, based in Sheffield, UK, has constructed a full-scale production metal gas atomiser fitted with a novel system to suppress satellite formation. The system greatly improves the particle shape of finer powders for applications such as thermal and HVOF spraying. ‘It permits an existing system to be modified to make much more spherical powders,’ says John Dunkley, Technical Director of ASL. ‘Thermal spraying is perhaps the most interesting potential application. It is a question of enhanced flow properties, which may also be useful for the brazing paste people and for metal injection moulding.’
Increased Incidence of Satelliting
In recent years there has been an increasing demand to produce finer powders, which in the 1970’s and 1980’s meant median sizes of 60-100 microns and in the 1990’s, for HVOF spraying, meant 20-30 microns. This need to produce smaller particles removed the necessity to build very large equipment to avoid ‘splatting’, which was seen as a major drawback in terms of capital and clean-down costs. Smaller plants were built in the range of 2-5 metres tall and 1-2 metres in diameter and this, combined with the need to produce finer particles, led to a much higher incidence of ‘satelliting’. ‘Satellites are almost invariably found in inert gas atomised powders,’ says Dunkley. ‘The degree of incidence depends on the design of the atomiser, the operating conditions, the alloy characteristics and the fineness of the powder.’
Results of Inter Particle Collisions
In gas atomisation, surface tension leads to spheroidisation of droplets of molten metal well before freezing. If collisions then occur between droplets during freezing, misshapes can easily be produced. If a small liquid droplet hits a large cold particle, the result is a ‘splat cap’, in which the larger particle has a partial covering of ‘splatted’ material, figure 1. If a small cold particle impacts a hot near frozen droplet, the result is a ‘satellite’, figure 1. To overcome this problem, some suppliers have developed special methods for low-satellite production, while others try to do what they can with standard equipment.
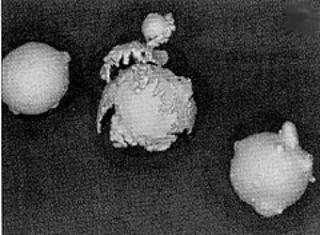
|
Figure 1. A splat capped particle (centre) and a satellited particle (right).
|
Causes of Inter-Particle Collisions
The cause of inter-particle collisions is unclear. However, the team at ASL has observed that, inside atomisers, after just a few seconds of operation, the view of the atomisation plume is totally obscured by a dense cloud of dust circulating in the atomising chamber. This cold powder is drawn into the atomisation plume, which the ASL team believes causes the problem. On the basis of this theory, and using ASL’s anti-satellite technology, the ASL atomiser withdraws gas from the atomising chamber, removes the powder in it, and introduces cleaned gas around the atomisation plume. This removes the dust cloud normally observed.
Avoiding Inter-Particle Collisions
‘Essentially, it surrounds the atomising spray with cleaned gas,’ says Dunkley ‘to avoid cold powder being sucked into the spray’, the ASL atomiser is of modest height, with a watercooled vessel just 3.5 metres tall and 1.5 metres in diameter. Gas is exhausted at about 1 metre from the top to a cyclone and backup filter. The melting furnace has two coils with nominal capacity of 40kg and 120kg respectively. The system is capable of processing melts of alloys from zinc to steel and atomising with nitrogen at rates of 5-20kg/min.
Evaluation of the Anti-Satelliting Concept
This novel concept is currently in the early stages of evaluation. However, initial results have been very encouraging. Experiments using the system have been carried out on the alloy FeSi14, which was used as a model for thermal spray materials such as NiCrBSi. It melts at ~1250°C (liquidus) with a freezing range of 40-50°C. Using small melts of 25-30kgs, all nozzles tested were close-coupled and operated at melt flow rates between 2-29kg/min, and at gas flow rates from 10-30m3/min at pressure of 10-30 bars.
Improved Properties of Powders Produced Using Anti-Satelliting Technology
The results show that without using the anti-satellite device, the three melts produced powders with a mean apparent density (AD) of 3.86g/ml and tap density (TD) of 4.76g/ml. Most would not flow at all. In comparison, the melts atomised with the anti-satellite system produced powders with an average apparent density of 4.52g/ml and tap density of 5.14g/ml. All powders flowed at speeds from 17-24 secs per 50g. As a percentage of solid density of 7.1g/ml for this alloy, the data shows that AD was raised from 55 to 64.3% and TD was raised from 67.6 to 71%. In the case of the coarser G46S, AD was as high as 66%, with TD at 74%. ‘The density data gives a numerical measure of packing efficiency,’ explains Dunkley ‘and thus allows comparisons of the cited powders with those currently produced. The flow data is also standardised and reflects the much improved rheology of the powders.’
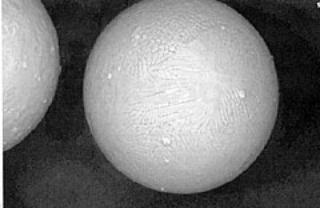
|
Figure 2. A near spherical particle made using anti-satelliting technology..
|
Summary
ASL is continuing to use the atomiser both with and without the anti-satellite system to build up data on the response of different alloys. ‘To date we have used FeSi14 as a model alloy for NiCrBSi type thermal spraying, some brazing alloys of the Cu-P system and stainless steel,’ says Dunkley. The evaluation of a range of narrow-sized powders produced without the anti-satellite device showed that about 90% of particles were ‘satellited’, while with the device, this fell to about 10%. ‘These new powders are of particular interest in HVOF spraying and other advanced spraying techniques, in which very fine powders with good flow properties are needed to optimise performance,’ says Dunkley. He also believes that the dense-medium industry, which uses a slurry of powder for mineral or scrap separation, would also be interested, particularly in the powder’s optimised theology.
Clearly, for applications requiring finer spherical powders with good flow and density, this new system appears to provide the answer to producing good spheres.
|