It used to be that, when designing a new military jet fighter, performance and capability took priority over cost. However, with the end of the cold war, defence contractors are finding that cost and producibility becoming major factors in the design equation. Laser forming is helping its customers reduce lead times and costs on large titanium structural components through the use of its laser metal deposition process (figure 1). Lasform is based on the ‘art to part’ concept, whereby a part is made directly from a customer’s CAD file using a sequential layering process. The parts produced are fully dense, require minimal machining and satisfy the customer’s requirements for performance and cost. 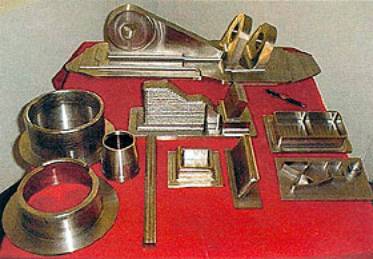 | Figure 1. Examples of the type of parts that can be made by laser forming. | Traditional Forming Techniques Today’s modern fighter aircraft contain a significant number of structural components made from hi-tech aerospace titanium alloys such as Ti-6A1-4V, Ti-6Al-2Sn-4Zr-2Mo-0.8Si, Ti-6Al-2Sn-4Zr-6Mo, Ti-l0V-2Fe-3Al and Ti-15V-3Cr-3Al-3Sn. Because of loading requirements and size and weight constraints, it is often desirable to make these components monolithic. In order to do so, it is necessary to either cast them as single components or to machine them out of large titanium billet. Casting Casting can produce many of these components to near net-shape, requiring only minimal finish machining. Many recent advances in investment casting technology allow complex components to be cast, which before could only be made as built-up assemblies. The benefits include cost and weight savings and overall performance enhancements. Despite these advantages, casting is limited in terms of the types of geometry that can be accommodated, as it is restricted by aspect ratios and section thickness changes. Castings are also susceptible to defect formation in the form of voids and inclusions, both of which can lead to the need for HIPing or expensive repair cycles. Finally, tooling costs are high for large components, and the tooling itself requires long lead times. These last two factors tend to make casting prohibitive for large prototype parts and for small production runs. Machining Alternatively, machining eliminates the need for tooling and significantly reduces costs for prototype parts and limited production runs. The downside to machining large titanium structural components is poor material utilisation, significant tool wear and long turnaround times. For example, a typical aircraft structural component consists of a large web area coupled with flanges and strengthening walls, basically a rib-on-plate structure. This type of geometry provides the necessary strength and stiffness while keeping weight to a minimum. However, producing one of these components from a single block of material requires the removal of over 90% of the original stock and takes a considerable amount of time. In order to reduce material waste and processing time, forging has been used to create machining preforms that are closer to the final part shape. Forging has the added benefit of affecting the microstructure and thereby enhancing certain mechanical properties. Paradoxically, though, material utilisation is of the same order as that of machining because most of the material is lost as forging flash or is machined away. Turn-around times are still relatively long, because titanium must be forged and heat treated in several repetitive cycles. Added to this is the fact that for most titanium alloys, forging must be performed at high temperatures, significantly increasing processing and tooling costs. The Lasform Process The Lasform process was developed in order to resolve these issues while maintaining quality and satisfying design requirements. Lasform takes the opposite approach to machining, in that material is added rather than removed. A near-shape geometry is built up using the laser deposition process, figure 2, and then machined to final dimensions. The process involves using a high power CO2 laser to melt together the substrate and the powder that is being deposited. The part is built up by this deposition process, and is moved in relation to the laser using CNC control. The CNC system follows a tool path generated directly from a 3D solid model. Figure 3 illustrates the equipment used. The process takes place in an inert gas chamber to protect the molten material from the effects of air. Argon is usually used, with oxygen levels kept below 50 ppm. This results in porosity-free material with excellent mechanical properties. 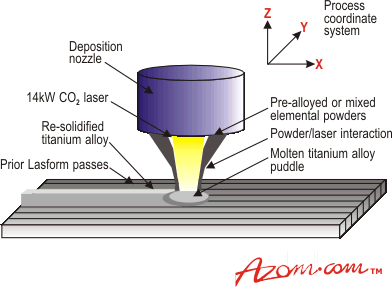 | Figure 2. The Lasform process. | 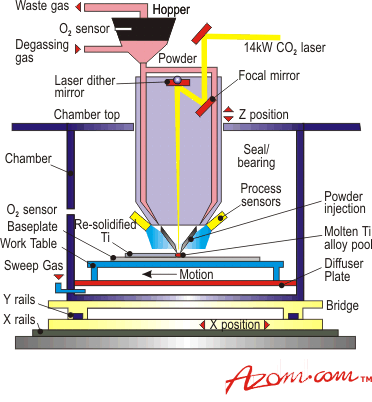 | Figure 3. Equipment used in the Lasform process | Advantages of the Lasform Process The potential savings in both time and material can best be described by using the example of a generic bulkhead structure used in airframes. These items use a rib-on-plate design that provides strength at low weight. Casting this part would be extremely difficult because of its size and shape. It would require a complex gating and riser system, would be susceptible to warping and internal defect formation, and would require several full scale test parts. Machining the part from a solid block of material would require a billet that was eight feet long by four feet by one foot high and weighing over 3600 kg. After machining away 95% of the original stock, the final part would weigh only 180 kg while the chips on the floor, when swept up, would collectively weigh almost 3.5 tonnes. Laserforming significantly reduces the amount of waste material by building up only the necessary geometry. In the case of the bulkhead, the ribs and flanges would make up 50% of the part’s final weight, or roughly 90 kg. A flat plate would be used for the web, and roughly 112 kg of material selectively deposited to create the ribs and flanges. The excess material, roughly 22 kg, would be machined away to produce the finished part. This would bring material waste to under 15%. The high deposition rate for the process coupled with reduced machining, give turn-around times of the order of weeks for a part, instead of months. The Lasform process has the added benefit of being able to create parts of almost any size. For the other manufacturing methods, as parts become extremely large, as in the case of the main carry-through bulkhead for the F-22 Raptor, cost and risks increase dramatically, while producibility decreases significantly. Casting is limited in terms of size, partly for reasons already stated, but also because of the lack of HIP furnaces large enough to accommodate such a large part. Machining a part this size is very expensive and time consuming, and forging becomes very expensive because of the cost of making a stamping die that large. Laserforming, on the other hand, has no such size restrictions. There is nothing in the underlying physics of the process that would limit the size of a part to some maximum value. The process is completely scaleable, from small parts weighing only grams, to parts weighing several tonnes. Another advantage of the Lasform process is the ease with which customers can integrate it into a design and build process. A customer simply supplies a CAD 3D solid model of its part. A part program, generated directly from the CAD model using off-the-shelf CAD software, is downloaded directly to the Lasform system and the part is made. It is then inspected, heat treated and shipped to the customer for finish machining and installation. Limitations of the Lasform Process Not all components and materials are amenable to the Lasform process. Many parts are too complex and beyond the current capabilities of the technology. Also, components made from less exotic alloys can be produced more cost effectively using conventional manufacturing processes. Lastly, a significant portion of the hi-tech aerospace alloys are considered unweldable. Materials Suited to the Lasform Process Titanium alloys are well suited for the Lasform process because most of them are highly weldable. They are also difficult and more costly to process using other means. In addition, the simple geometry of a large number of titanium structural components is appropriate for the current level of Lasform technology. Because Lasform is a layering process, and relies on the localised melting and solidification of the material being deposited, the resulting microstructure is similar to that of a casting. However, because both the cooling and solidification rates are orders of magnitude higher than for casting, the microstructure is much finer. This ability to create a fine microstructure gives Lasform Ti-6-4 the strength, ductility and crack initiation resistance of wrought material while maintaining the high fracture toughness and fatigue crack growth resistance of cast material. Table 1 shows some typical mechanical properties for the material. Table 1. Typical mechanical properties for Lasform Ti-6Al-4V. | Ultimate tensile strength (MN.m-2) | 830-900 | Yield strength (MN.m-2) | 900-1000 | Elongation (%) | 10-15 | Fracture toughness (MN.m-3/2) | 75-110 | Post Heat Treating For most titanium alloys, thermal treatments play a critical role in determining mechanical properties. Heat treating is often used to achieve application-specific properties. Lasform titanium responds to heat treating in the same manner as conventional titanium. Thus, customers can specify the same heat treatments they would normally use without the need for developing new ones. Summary The quality and performance combined with the cost and lead time reductions make Lasform an attractive alternative to conventional manufacturing methods. The convenience of electronic data transfer and the power of 3D solid modeling allow the process to be easily and seamlessly integrated into today’s design and production processes. The end result is a process that provides process capability at reduced cost without sacrificing quality or performance. |