Research institutions around the world are exploring ways to transform the production of high-quality sheets. One way to achieve this cost effectively is by the reduction of graphene oxide into rGO, also known as reduced graphene oxide. However, this technique has a drawback related to the quality of graphene sheets produced, which show properties that fall short of the theoretical potential of perfect graphene when compared to other techniques such as mechanical exfoliation. However, improvements can be made to overcome this issue.
Graphite Oxide
Graphite oxide, a compound made up of oxygen, hydrogen and carbon molecules, is synthetically produced by treating graphite with strong oxidisers, such as sulphuric acid. These oxidisers react with the graphite and remove an electron in the chemical reaction. This reaction is called as a redox reaction, wherein the reactant is oxidized and the oxidising agent is reduced.
In the past, the most common technique used for producing graphite oxide was the Hummers and Offeman method, wherein graphite is treated with a mixture of potassium permanganate, sulphuric acid and sodium nitrate. Nevertheless, other techniques have been recently developed that are considered to be more efficient, reaching levels of about 90% oxidization. Graphene oxide is a by-product of this oxidization. The interplanar spacing between the graphite’s layers is increased when the oxidising agents react with graphite. The compound which is completely oxidised can then be dissolved in water to produce graphene oxide.
Graphene oxide and graphite oxide share similar chemical properties, but have different structural properties. The main difference between graphene oxide and graphite oxide is the interplanar spacing between individual atomic layers of these compounds. This increased spacing, which is caused by the oxidisation process, disrupts the sp2 bonding network. This means, both of these compounds are electrical insulators.
Conversion of Graphite Oxide to Graphene Oxide
The process of converting graphite oxide into graphene oxide can damage the individual graphene layers. The conversion of graphite to graphite oxide already damages individual graphene platelets and reduces their mean size. Therefore, further damage can have a detrimental effect.
However, graphite oxide can be turned into graphene oxide by a number of methods. Sonication, stirring and a combination of these two are the most common methods. Sonication is very effective in exfoliating graphene and exfoliating graphite oxide, but this technique also tends to damage the graphene flakes and reduces them from microns to nanometers; this method also creates a wide range of graphene platelet sizes. Mechanically stirring is less laborious, but can take a significant amount of time to accomplish.
Conversion of Graphene Oxide to Reduced Graphene Oxide
Reducing graphene oxide to create reduced graphene oxide (rGO) is an important process as it considerably impacts the quality of the rGO produced, which impacts, in terms of structure, how close the rGO will come to high-quality graphene. In large scale operations, rGO is the most suitable solution because of the relative ease in producing adequate amounts of graphene to preferred levels of quality.
Reduction can be achieved through a number of ways, based on thermal, chemical or electrochemical methods. Although some of these methods can produce high quality rGO, analogous to pristine graphene, they can be quite complex or take a considerable amount of time to perform.
Techniques for Reducing Graphene Oxide
Earlier, scientists have produced rGO from graphene oxide by treating graphene oxide with hydrazine hydrate and sustaining the solution at 100 for 24 hours; heating graphene oxide in distilled water at varying degrees for different lengths of time; exposing graphene oxide to hydrogen plasma for a few seconds or exposing it to another form of pulse light, such as those generated by xenon flashtubes; and through linear sweep voltammetry, to name a few.
Using chemical reduction to reduce graphene oxide is a scalable technique; however, the rGO produced has substandard yields in terms of electrical conductivity and surface area. Reducing graphene oxide at temperatures of 1000°C or more produces rGO that has a very high surface area, close to pristine graphene. However, the heating process tends to damage the structure of the graphene platelets and substantially reduces the mass of the graphene oxide, producing vacancies and imperfections.
The last example described above may ultimately provide a solution for large-scale production of rGO. Electrochemical reduction of graphene oxide has been shown to create high quality rGO that is almost similar in terms of structure to pure graphene. In this process, different substrates such as glass or indium tin oxide are coated with a thin layer of graphene oxide. Then, at each end of the substrate, electrodes are placed to create a circuit through the graphene oxide. At the end, linear sweep voltammetry is performed on the graphene oxide in a sodium phosphate buffer at different voltages.
The resulting graphene oxide through this technique demonstrated a high carbon to oxygen ratio and also showed electrical conductivity readings higher than that of silver (8500 S/m, compared to approximately 6300 S/m for silver). Other advantages of this method are that no toxic chemicals were used. However, the scalability of this method has come under considerable scrutiny due to the difficulties in depositing large-scale graphene oxide onto the electrodes.
Conclusion
Eventually, once rGO has been produced, it can be functionalised for use in different applications. For instance, rGO can be treated with other chemicals or can be combined with other two dimensional materials to create new compounds. Thus, the properties of rGO can be improved to suit commercial applications.
About Graphenea
Graphenea is a leading graphene producer for industrial and research needs. Graphenea has developed a leading synthesis and transfer process to obtain high uniformity monolayer graphene films on any substrate.
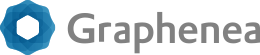
This information has been sourced, reviewed and adapted from materials provided by Graphenea.
For more information on this source, please visit Graphenea.