The power generation and mining industries use expensive equipment in extremely aggressive environments. As a result, machinery is frequently shutdown for repair and maintenance, which is costly and can have a direct impact on production or consumer supply. Also conventional techniques such as welding and plasma spray processes do not provide adequate surface properties to extend the service life of many parts and components. To overcome what is a common problem for these industries, researchers at CSIRO Manufacturing and Infrastructure Technology, in Australia, are using solid state industrial lasers to increase efficiency, reduce repair costs by reducing downtime and potentially extend a component’s life through improved surface engineering.
In-Situ Repair of Erosion Damage
A major issue for power generation and mining industries is wear and erosion management,’ says Dr Nazmul Alam, project leader for the CSIRO laser research team in Adelaide. ‘With this technology, repairs can be carried out in-situ without dismantling the whole structure.’
Repair or Replacement for Components
CSIRO is using a Nd:YAG laser. Its beam can be transported through a flexible optical fibre to the workplace for use in damage repair and surface coating or cladding. ‘This is a rapid process with a small localised heat ‘footprint’, which results in less distortion in the finished products,’ says Alam. ‘In some cases it means that components that require accurate geometry can be repaired - without this technology replacement is the only option.’
How the Laser Repair Technique Works
The high density of the laser energy provides fast melting of consumables on the surface, in powder and wire form, without extensive damage to surrounding areas. ‘Nickel, cobalt and tungsten carbide-based alloys are currently being used in the process,’ says Alam. The technology offers a controlled dilution process and is capable of producing an overlay with a dilution with the substrate as low as 3-5%, which maintains the desired properties of the filler materials. ‘Controlled dilution guarantees a true metallurgical bond with the parts,’ says Alam, ‘and the rapid process results in faster cooling, which provides finer microstructures and improved wear properties.’
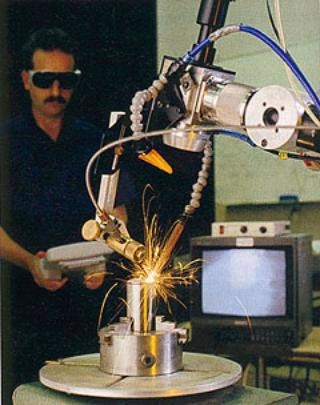
|
Figure 1. Laser repair of a valve seat using stellite wire.
|
Advantages of Laser Repaired Sections
Laboratory tests have shown that the overlays generated by the process are of extremely high quality without porosity or cracking. Also, the resulting overlay surface is much smoother than conventional weld overlays and requires less post-process machining. The significant benefits of the new technology include:
• Higher productivity
• Less distortion in repaired components
• Higher metallurgical properties and service properties in clad layers.
Suitability of the Process
At the moment the process has only been developed for steel components. In the power generation industry, for example, procedures for in-situ repair of turbine blades have been developed. This opens up the possibility of successfully restoring blades without removing them from the turbine. ‘Further research is needed to develop suitable alloys and processes for specific applications,’ says Alam. However, to check the effective use of the lasers for repair, Pacific Power International in Newcastle, New South Wales, is conducting a feasibility study. ‘We know that the overlay is of high metallurgical quality, but we do not know how the working environment will affect the overlay’ says Alam. ‘We are conducting some field trails to determine its reliability.’
Summary
High wear and erosion are common problems for many parts and components in the power generation and mining industries. This technology addresses the targeted regions of components that are subjected to wear, enhancing their service life and as a result, reducing the frequency of machine down time. If effectively adopted across both industries, the researchers claim that this technology could potentially save the power generation and mining industries millions of dollars in repair costs.
|