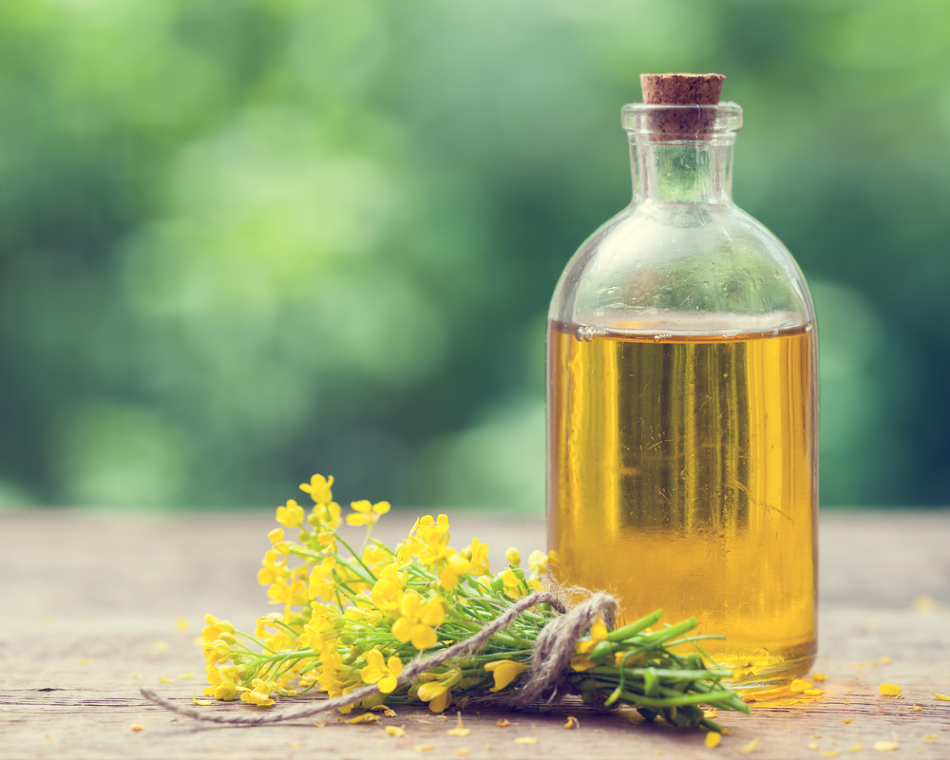
Image Credit: Chamille White/Shutterstock.com
A novel green recyclable rubber polymer developed by Australian scientists can help to reduce the ever-growing environmental impact of the traditional non-reusable synthetic and mineral materials used in manufacturing and construction. The new material is composed of sulfur and canola oil and can be combined with fillers derived from recycled plastic waste to create reusable construction materials of the future.
As part of the global efforts to reduce the environmental impact of synthetic plastic waste, the development of novel polymer materials that can be easily recycled and reused in a sustainable circular economy is gaining substantial interest from the research community and industry.
Most recycled plastic waste is mechanically reprocessed into new source materials or melt-processed to manufacture new goods. This often leads to chemical and mechanical degradation of the recycled material, limiting its possible applications.
Industrial Waste as Source Material for Green Recyclable Polymers
Combining sustainable source materials, such as renewable biomass, agricultural, or industrial waste with newly developed processing methods, paves the way towards the next generation of green recyclable polymers, as it enables polymers to break down into reusable macromolecular building blocks
Elemental sulfur is an abundant and inexpensive by-product of the oil refining industry that is used for the manufacturing of a wide range of commodity chemicals and materials, such as sulfuric acid, fertilizers, and vulcanization of natural and synthetic rubbers. Sulfur supply (over 60 million tonnes produced each year) greatly exceeds demand, creating large stockpiles of unwanted raw material.
Under normal conditions, sulfur atoms predominantly form cyclic eight-atom molecules with a chemical formula S8. Upon heating, at a temperature of around 120 °C, sulfur melts into a clear yellow liquid and larger polyatomic rings, consisting of up to 35 atoms, can be formed.
Further heating of the sulfur melt (above 159 °C) initiates a ring-opening polymerization of the ring-shaped monomers into polymeric sulfur of high molecular weight. However, this process is reversible and sulfur polymers readily depolymerize back to the ring-shaped monomeric state.
Rubber Polymers with High Sulfur Content as an Alternative to Conventional Rubber
With the invention of the inverse vulcanization process in 2013, the synthesis of chemically stable and processable sulfur-based polymer materials (with a sulfur content of 50-80 wt%) became possible.
In the conventional vulcanization process, a small amount of sulfur is used to form crosslinks (bridges) between hydrocarbon polymer chains, converting the organic polymers into more durable and wear-resistant materials such as vulcanized rubber.
Conversely, the inverse vulcanization process uses a large amount of sulfur and a small amount of an organic additive (usually unsaturated hydrocarbon) that acts as a crosslinker and stabilizes polymeric sulfur against depolymerization.
Based on the inverse vulcanization process, a research group led by Dr. Justin Chalker, associate professor at Flinders University, Australia, has synthesized a groundbreaking rubber polymer. The polymer is made by a random co-polymerization of canola oil (a type of rapeseed oil with a very high content of unsaturated fats) and 50 wt% sulfur.
Structurally, the new polymer is very similar to natural or synthetic rubber, consisting of a network of crosslinked macromolecular chains, which makes it insoluble in most common organic solvents. It is also a highly sustainable material, as its synthesis does not require any organic solvents and uses only elemental sulfur (industrial by-product) and renewable plant oil.
Heat and Pressure Converts Rubber Powder into Versatile Material
Flinders scientists, together with collaborators from Deakin University and the University of Western Australia, have developed an innovative method called reactive compression molding (RCM), which enables the processing, recycling, and reusing of the new rubber polymer.
Once the polymerization process is complete, the final product (a soft, brown rubber) is dried and ground into powder. The powdered rubber is then compressed in a hot press at a pressure of 10 MPa and a temperature of 110 °C. Within minutes, the material converts into a flexible rubber compound.
Although the temperature required for the RCM to take place is far lower than the temperature of the original inverse vulcanization process (180 °C), the combination of heat and pressure is sufficient to trigger sulfur-sulfur metathesis reaction (cleavage and reforming of the bonds between the sulfur atoms) at the interfaces between the compressed polymer particles. This leads to the formation of a continuous macromolecular network within the material.
Recycling of Rubber Polymers through Reactive Compression Molding
According to the Australian scientists, the reactive compression molding process is ideally suited for recycling and reusing of the rubber polymer. Their research shows that the new material can be ground up into a powder and remolded at elevated pressure and temperature many times without any degradation of its physical and chemical properties.
The relatively low temperature during the RCM process minimizes the thermal degradation of the material.
Click here to find out more about plastic and rubber testing equipment
Even after several RCM cycles, the remarkable material retains its strength and elasticity and can be shaped into tubing, insulation mats, coatings, and other products traditionally manufactured from conventional rubber.
Once these products have reached their end of life or are no longer needed, they can be ground up and recycled into something new.
Construction Materials with Tunable Properties
As stated by Ph.D. candidate Nic Lundquist, the leading author of the research, the most important advantage of the RCM method is the possibility to manufacture unique composite materials with tunable mechanical properties.
By using the rubber polymer as a moldable reactive matrix that can bind fillers such as plant fibers, sand, recycled plastic waste and carbon fiber, the researchers have created new composites that can be used as sustainable construction materials in the future.
Find out more about materials characterization equipment
Two of the newly developed composite materials, one containing sand and the other plant fiber filler (50 wt% coconut coir), exhibited compression moduli of approximately 12 MPa (nearly double that of the rubber polymer alone) with much higher stiffness and elastic moduli.
The plant fiber composite is particularly suitable for building insulation, while the sand composite may replace non-recyclable construction materials such as bricks and concrete. The latter possibility is of particular interest as cement is a non-renewable resource with a major environmental impact, causing air pollution and contributing more than 8% of global greenhouse gas emissions.
Multi-Use Rubber Polymers Boost Sustainability of Construction Industry
The versatility of the green recyclable rubber polymer was demonstrated in an experiment where the powdered material was first used to purify water contaminated with iron (due to the high sulfur content, the material can bind to metals like iron), removing more than 90% of the contaminant in 24 hours.
The iron-laden rubber was then subjected to RCM to manufacture insulation mats and other recyclable construction materials.
The newly-developed RCM process opens up the possibility for a new class of multi-purpose rubber polymers that can be efficiently recycled and reused to serve as a technological base for the manufacturing of future sustainable construction materials from recycled plastic waste.
References and Further Reading
N. Lundquist et al. (2020) Reactive compression molding post-inverse vulcanization: A method to assemble, recycle, and repurpose sulfur polymers and composites. Chem. Eur. J., Available at: https://doi.org/10.1002/chem.202001841
W. J. Chung et al. (2020) The use of elemental sulfur as an alternative feedstock for polymeric materials. Nature Chem., 5, 518–524. Available at: https://doi.org/10.1038/nchem.1624
Flinders University (2020) Revolutionary ‘Green’ Bricks Made from Recycled Plastic and Organic Waste. [Online] www.scitechdaily.com Available at: https://scitechdaily.com/revolutionary-green-bricks-made-from-recycled-plastic-and-organic-waste/ (Accessed on 20 June 2020).
M. Irving (2020) "Green" recyclable rubber gives new life to single-use building materials. [Online] www.newatlas.com Available at: https://newatlas.com/materials/recyclable-rubber-reuse-building-materials-plastic/ (Accessed on 20 June 2020).
Flinders University (2020) Building bricks from plastic waste. [Online] www.phys.org Available at: https://phys.org/news/2020-05-bricks-plastic.html (Accessed on 20 June 2020).
E. Turner (2020) Researchers discover New Rubber Material to create Green Construction Material. [Online] www.tmrblog.com Available at: https://tmrblog.com/researchers-discover-new-rubber-material-to-create-green-construction-material/ (Accessed on 20 June 2020).
Disclaimer: The views expressed here are those of the author expressed in their private capacity and do not necessarily represent the views of AZoM.com Limited T/A AZoNetwork the owner and operator of this website. This disclaimer forms part of the Terms and conditions of use of this website.