Aluminum alloy is extensively utilized in various industries, such as the aerospace industry, automotive sector, smartphones, as well as industrial systems. Aluminum has some special qualities that make it a good option for replacing heavier materials like steel or copper, especially in the manufacturing of automotive structures. These unique features include superior strength-to-weight ratio, remarkable ability to form different shapes, resistance to corrosion, and easy recycling. All of these attributes make aluminum a top choice for helping cars become lighter, which in turn leads to reduced fuel consumption and sustainable operations.
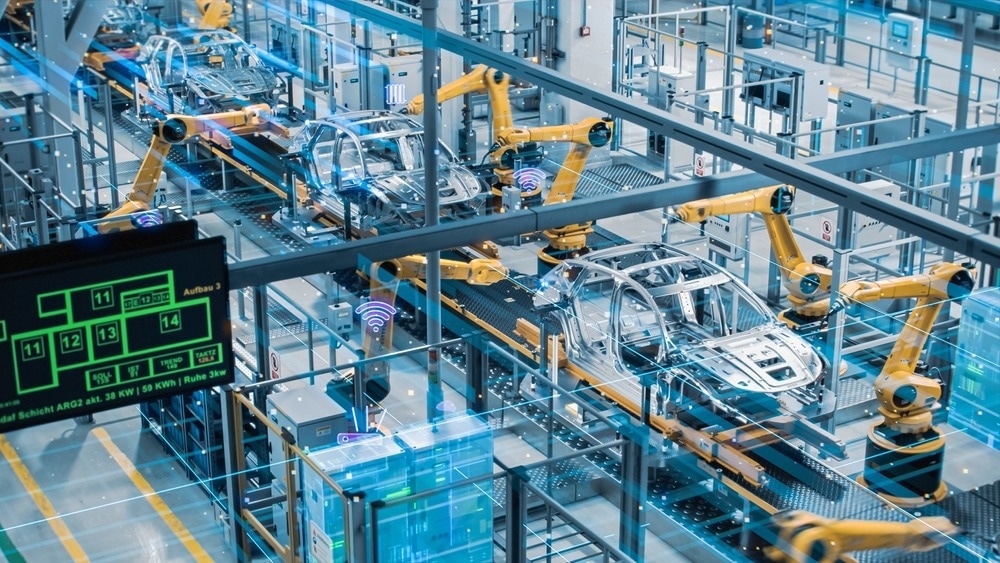
Image Credit: Gorodenkoff/Shutterstock.com
Which Automotive Structures Utilize Aluminum Alloys?
In the past, the use of aluminum alloys in car manufacturing was somewhat limited, mainly applied to manufacturing smaller parts within the vehicle's structure. Nevertheless, the popularity of aluminum alloys has steadily increased as modern testing has proved their improved durability as compared to traditional counterparts.
In today's automotive industry, aluminum has emerged as the preferred material for constructing vehicle frames. Many car manufacturers have embraced the lightweight qualities of aluminum to create chassis, effectively replacing the previously dominant iron. This shift to aluminum alloy chassis has led to significant improvements in vehicle performance, all while ensuring enduring robustness.
Furthermore, aluminum's natural polish and glossy appearance make it a visually appealing choice for car interiors. Opting for aluminum alloys in the interior enhances the aesthetic appeal, ensuring that interior components maintain a fresh and polished look. As a testament to this trend, since 2014, various cars with a composition of 100% aluminum have been introduced, highlighting the growing importance of aluminum alloys in the design and production of automobiles.
Aluminum alloys bring notable advantages to high-performance automobiles, primarily due to their outstanding shock-absorption capabilities. This beneficial feature enables manufacturers to strategically design specific areas on the car's body for absorbing concentrated forces. This design approach helps avoid situations where all the force would be concentrated on the driver, leading to a more evenly distributed and safer handling of impact forces.
Moreover, aluminum's ability to effectively absorb force extends to enhancing impact resistance in various other parts of the vehicle. This significantly contributes to fortifying the overall safety of the vehicle in case of a collision, as it aids other vehicle components in maintaining their original shape. Essentially, aluminum's shock-absorption properties play a pivotal role in advancing vehicle safety and mitigating potential damage resulting from impacts.
Novel Aluminum Hybrid Composites for Lightweight Automotive Structures
Composites based on aluminum, well-known for their low weight and impressive strength under tension, have gained prominence as a prominent alternative material. These lightweight composites are gaining popularity, especially in the automotive sector.
Among the various materials used for reinforcement, fly ash stands out due to its cost-effectiveness and low weight. Aluminum matrix composites that incorporate fly ash particles as reinforcement are positioned to overcome cost-related challenges in a range of applications, including engineering and automotive industries.
As per recent research published in the journal Materials, over the last few decades, substantial research and development efforts have been dedicated to advancing metal matrix composites (MMCs), leading to the emergence of innovative materials with diverse applications.
In the latest study, researchers created a lightweight composite material using a stir-casting process. This process involved adding reinforcement powders, specifically carbon nanotubes and fly ash, to pure aluminum. The inclusion of fly ash serves a dual purpose; it helps reduce the overall material cost and contributes to achieving a composition with low density. The primary aim of this research is to determine the ideal weight percentage of fly ash required to achieve favorable mechanical properties.
To accomplish this objective, an artificial neural network was employed. This neural network was used to pinpoint the minimum volumetric wear under specific conditions, offering a data-driven approach to optimize the composite material for improved performance.
In the process of stir-casting aluminum for composite manufacturing, it was successfully shown that fly ash can be added to the composite material at levels of up to 15% by weight. By introducing fly ash and carbon nanotubes (CNT), substantial enhancements in the material's characteristics were achieved. Specifically, the hardness of the aluminum nanocomposite increased significantly, going from 73 BHN to 89 BHN. The inclusion of reinforcements resulted in a notable improvement in compressive strength, with values rising from 485 MPa to 512 MPa. Moreover, the tensile strength of the composite exhibited a remarkable 36% increase compared to the unreinforced composite.
Furthermore, the study unveiled that when the fly ash content reached its maximum (15%) under specific conditions, including a load range of 15.5 to 23 N and an RPM range between 200 and 375, the composite showed minimal wear. These findings underscore the potential of fly ash and CNT as effective reinforcements in aluminum nanocomposites, offering enhanced mechanical properties and resistance to wear.
What are Novel Developments in Aluminum Casting Alloys for the Automotive Sector?
Traditionally, aluminum die-casting alloys have been employed in crafting suspension systems, engine parts, and gears. Nevertheless, as aluminum casting techniques continue to advance, die casting has evolved to allow the creation of multiple body parts as a unified piece. This technological advancement is set to boost the utilization of aluminum die casting, especially for the commercialization of electric vehicles (EVs).
As per the latest article published in The Eurasia Proceedings of Science, Technology, Engineering & Mathematics (EPSTEM), there is a projected substantial uptick in the demand for aluminum die-casting components in the EV industry. The capacity to manufacture elements as a single unit not only simplifies production procedures but also contributes to the overall efficiency and weight reduction of electric vehicles. These aspects are crucial for enhancing their performance and environmental advantages.
According to the study, there is a projected increase in the average aluminum alloy content per vehicle by 20 kg by the year 2025. Aluminum casting is expected to remain the primary shaping method in the automotive sector.
Among the emerging manufacturing techniques, high-pressure, thin-walled aluminum die casting is expected to take the lead. The application of high-pressure aluminum die casting is expected to continue growing, extending into the year 2040. High-pressure die casting (HPDC) is a technology well-suited for high production rates, and presently, around 50% of the world's production of light metal castings is achieved through this technology.
World’s Leading Automotive Manufacturers Prioritizing Aluminum Alloys
In late 2022, Volvo unveiled its intentions to embrace mega-giga casting technology for constructing body-in-white architectures. This innovative approach involves employing large aluminum castings, with its primary goals being to optimize interior space usage and enable the creation of multiple vehicles sharing common modules based on the same body-in-white components.
Mega-casting technology comes with several advantages, such as reducing assembly time and the overall length of the assembly line. It involves molding a portion of a vehicle with as many integrated components as possible, simplifying the primary assembly process. This approach aligns with the broader industry trend of adopting more efficient and streamlined manufacturing methods.
Notably, Tesla has also introduced Giga-casted parts for the front of their future Model 3, showcasing a similar commitment to advanced casting techniques. Furthermore, Volkswagen recently unveiled its "Project Trinity," which is expected to embrace Tesla-like manufacturing processes, including potentially adopting aluminum mega-casting solutions.
These developments highlight the automotive industry's ongoing transition toward innovative and efficient manufacturing technologies aimed at improving production speed and product quality.
The automotive sector has progressively embraced aluminum alloys owing to their essential engineering characteristics. This transition underscores the industry's acknowledgment of the vital contribution made by aluminum alloys in enhancing vehicle efficiency, performance, and sustainability. Consequently, aluminum alloys have emerged as a fundamental material in the automotive industry, sustaining progress in vehicle design, production, and overall performance.
More from AZoM: The Impact of 3D Printing on Prototyping in the Automotive Industry
References and Further Reading
Lee, N., 2023. Aluminum Alloy - Prospective Trend For Automobile Manufacturing. [Online]
Available at: https://mrssteel.com.vn/blogs/steel-news/aluminum-alloy-automotive-manufacturing
Nirala A. et. al. (2022). Assessing the Mechanical Properties of a New High Strength Aluminum Hybrid MMC Based on the ANN Approach for Automotive Application. Materials. 15(6). Available at: https://doi.org/10.3390/ma15062015
Baser, T. et. al. (2022). New Trends in Aluminum Die Casting Alloys for Automotive Applications. The Eurasia Proceedings of Science Technology Engineering and Mathematics. 21, 79-87. Available at: https://doi.org/10.55549/epstem.1227541
Automotive News Europe, 2023. Giga Presses -- the giant die casts that are reshaping car manufacturing
Available at: https://europe.autonews.com/suppliers/giga-presses-help-toyota-volvo-hyundai-cut-production-costs
Disclaimer: The views expressed here are those of the author expressed in their private capacity and do not necessarily represent the views of AZoM.com Limited T/A AZoNetwork the owner and operator of this website. This disclaimer forms part of the Terms and conditions of use of this website.