Historically, the evolution of aerospace materials processing has been driven by the unyielding quest for lighter, stronger, and more durable materials. From the initial days of wood and fabric in aircraft construction to the sophisticated alloys and composites used today, the journey has been remarkable. Yet, in recent years, another transformative force has begun to reshape the aerospace landscape: additive manufacturing, commonly known as 3D printing.
No longer a novel technology for hobbyists or limited to prototyping, additive manufacturing is taking a central role in the production of critical aerospace components.
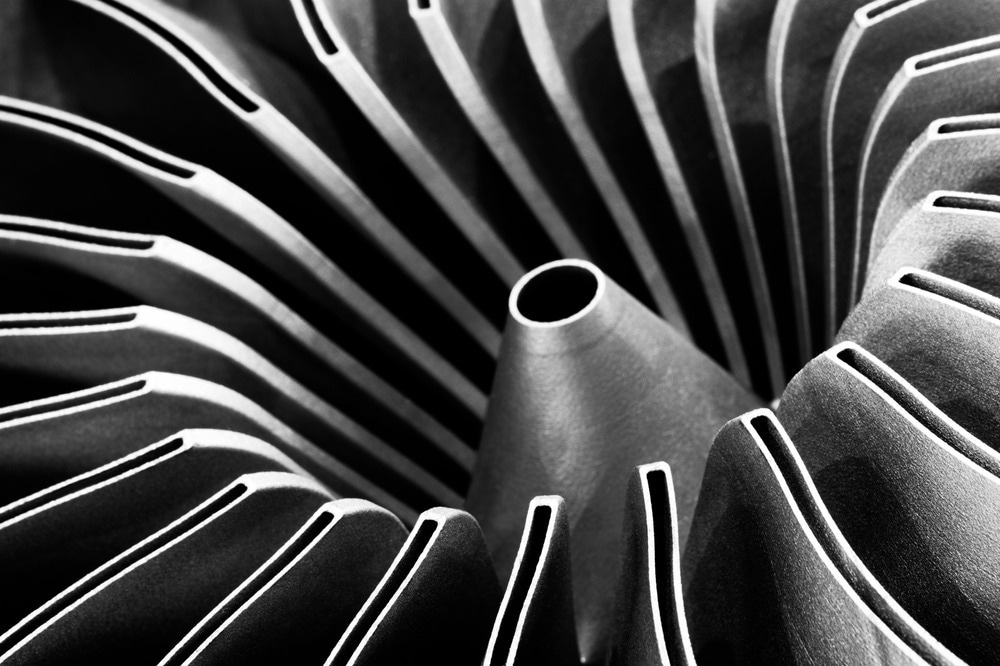
Image Credit: Matveev Aleksandr/Shutterstock.com
This manufacturing technique, which involves adding material layer by layer to create intricate designs, offers unprecedented flexibility and precision. The potential applications of additive manufacturing aerospace are vast, from optimizing existing parts for weight and strength to creating entirely new designs that were previously deemed impossible with traditional manufacturing methods.
The promise of additive manufacturing in aerospace extends beyond just creating parts; it heralds a new era in aerospace design and innovation. As we delve deeper into the world of 3D printing, it becomes evident that this technology is not just an evolution but a revolution in how aerospace materials are processed and how aircraft are designed and built.
The Shift to 3D Printing
Since its inception, additive manufacturing in aerospace has represented a transformative shift in how products are conceptualized, designed, and produced. In the aerospace sector, this shift is even more pronounced.
Historically, aircraft components were crafted through subtractive methods, where materials were carved, molded, and refined from larger blocks of raw materials. However, the inherent inefficiencies, wastage, and design constraints posed by these traditional techniques have given way to the precision, customization, and efficiency of additive manufacturing in aerospace. By building components layer by layer, additive manufacturing in aerospace provides unparalleled freedom in design, enabling engineers to conceive parts that were once deemed unmanufacturable.
Application Spectrum
The aerospace industry is increasingly embracing additive manufacturing for a variety of applications. From intricate turbine blades to lightweight structural components and even cabin fixtures, additive manufacturing in aerospace is leaving its imprint. One of the most notable applications of additive manufacturing is in the design and production of engine components, which benefit from the ability to produce complex geometries and internal structures.
This not only leads to components that are lighter but also enhances their performance. For instance, aircraft engine components with internal cooling channels, made possible only by additive manufacturing, can lead to more efficient and cooler-running engines.
Beyond individual components, the holistic approach to aircraft design is also evolving. Engineers are now empowered to rethink traditional design philosophies, incorporating more efficient, lightweight, and intricate designs that can streamline aircraft performance and functionality with the aid of additive manufacturing.
The Green Advantage
Additive manufacturing in aerospace is not only revolutionizing how aircraft parts are made but also introducing a more sustainable approach to manufacturing. In conventional methods, a significant amount of material is wasted as scraps and off-cuts. In contrast, 3D printing, by its very nature, utilizes material only where it's needed, drastically reducing waste.
This translates to significant raw material savings, especially when using expensive aerospace-grade materials. Additionally, the ability to produce lightweight components through additive manufacturing in aerospace directly contributes to fuel efficiency in aircraft, leading to reduced carbon emissions during flights. In a world increasingly conscious about environmental impact, the benefits of additive manufacturing extend beyond mere technicalities, placing the aerospace industry on a more sustainable trajectory for the future.
Delving into the Technicalities of Additive Manufacturing
Principles of 3D Printing
At its core, 3D printing or additive manufacturing is a process where materials are added layer by layer to build intricate structures based on digital models. The genesis of the model begins with Computer-Aided Design (CAD) software, which allows engineers to create detailed three-dimensional digital replicas of the desired part. This digital model is then sliced into thin horizontal layers by specialized software to guide the 3D printer.
While the overarching concept of additive manufacturing is consistent, several methods of 3D printing have emerged, each with its unique strengths:
Stereolithography (SLA)
This process involves the use of ultraviolet lasers directed at a vat of liquid photopolymer resin. The laser hardens the resin layer by layer, forming the object.
Selective Laser Sintering (SLS)
Here, a high-powered laser fuses tiny particles of material, often metal or plastic, layer by layer. The unfused powder remains to support the structure, negating the need for additional support.
Fused Deposition Modeling (FDM)
In FDM, a thermoplastic material is heated and extruded through a nozzle, laying down material layer by layer. It’s one of the more commonly used methods in additive manufacturing, especially for prototypes and less critical parts, due to its accessibility and affordability.
Aerospace Materials in Focus
The aerospace industry demands materials that meet rigorous standards of strength, durability, and weight. Additive manufacturing frequently employs:
Metals: Titanium, popular in additive manufacturing, has a high strength-to-weight ratio. Other metals, like aluminum and Inconel, also find their applications due to specific characteristics conducive to flight applications.
Ceramics: While not as commonly used as metals in additive manufacturing, ceramics find niche applications, especially in areas exposed to high temperatures.
Polymers: In the realm of additive manufacturing, lightweight and versatile polymers like PEEK (Polyether Ether Ketone) and ULTEM have properties suitable for non-structural components in aircraft.
It's paramount that these materials retain their inherent properties, ensuring that the final 3D-printed component is reliable, safe, and fit for its intended aerospace application.
Quality and Precision
Given that aerospace components have a direct bearing on flight safety, there's no margin for error in additive manufacturing. Ensuring the highest standards of quality and precision in 3D printed parts is imperative. Advanced scanning and inspection methods are employed post-production to verify the structural integrity and accuracy of printed parts.
However, additive manufacturing in aerospace isn't without its challenges. Factors such as material behavior during printing, layer adhesion, and internal stresses need to be accounted for. Overcoming these challenges requires a deep understanding of both the 3D printing technology and the specific requirements of aerospace components. Thankfully, with continuous research, advancements, and stringent testing protocols, additive manufacturing is adept at harnessing the potential of 3D printing while ensuring the utmost safety and performance of its components.
Highlights from Recent Research and Studies [2]
Innovative Applications
Additive manufacturing, especially metal-based, is becoming a game-changer. Drawing insights from the recently mentioned study, "Metal additive manufacturing in aerospace: A review," here are some highlights:
• Engine Components: One of the main attractions of metal additive manufacturing is the ability to produce intricate and high-strength components for engines. This not only reduces the weight but also enhances the performance and longevity of the parts.
• Structural Components: With advancements in additive manufacturing, the study highlighted the growing use of 3D-printed metal parts for critical structural components, pointing towards potential weight savings and increased structural integrity.
• Potential Future Applications: As the technology matures, the review suggests an increasing trend towards printing larger and more complex parts, hinting at the possibility of full-scale wing sections and major fuselage components being manufactured through this method in the not-so-distant future.
Success Stories
The study "Metal additive manufacturing in aerospace: A review" showcased several instances of successful integration of metal 3D printing in aerospace:
• Boeing: Highlighting the power of additive manufacturing, the study sheds light on Boeing's initiatives, which have seen the incorporation of titanium 3D printed structural components, leading to significant cost savings without compromising safety or performance.
• Rocket Propulsion: The review touches upon various aerospace entities harnessing additive manufacturing aerospace for rocket propulsion systems. Such components, which can be optimized for unique flow characteristics, are redefining rocket engine efficiency and reliability.
• Lessons and Takeaways: Emphasizing the nuances of additive manufacturing, the study underscores the need for stringent quality control, especially given the high-stakes nature of aerospace applications. It also emphasizes the necessity for continuous research into novel metal alloys tailored for specific aerospace needs, ensuring optimal strength-to-weight ratios and durability.
Conclusion
Additive manufacturing, or 3D printing, is becoming a transformative force within the industry. By enabling intricate design possibilities, reducing material waste, and allowing rapid prototyping and customization, this technology is reshaping the very fundamentals of how aircraft components are conceived, designed, and manufactured.
Drawing from insights provided in the "Metal additive manufacturing in aerospace: A review," it's evident that 3D printing is not just a passing trend but a revolutionary shift. It's facilitating the creation of components that were previously deemed impossible or too resource-intensive to manufacture using traditional methods.
As we peer into the horizon, the potential of additive manufacturing stretches far beyond our current applications. With deepening research and evolving technology, we might soon witness entire aircraft structures, from wings to fuselages, being printed with unmatched precision and customized properties. This could pave the way for aircraft that are lighter, more fuel-efficient, and potentially even more adaptable to specific mission requirements.
More from AZoM: How Does Stainless Steel Compare to Carbon Steel?
References and Further Reading
V. Mohanavel, K.S. Ashraff Ali, K. Ranganathan, J. Allen Jeffrey, M.M. Ravikumar, S. Rajkumar (2021). The roles and applications of additive manufacturing in the aerospace and automobile sector. materialstoday-proceedings. [Online] Available at: https://www.sciencedirect.com/science/article/abs/pii/S2214785321035227
B. B. Milner, P. Gradl, G. Snedden, M. Brooks, J. Pitot, E. Lopez, M. Leary, F. Berto, A. du Plessis (2021). Metal additive manufacturing in aerospace: A review. Materials & Design. [Online] Available at: https://www.sciencedirect.com/science/article/pii/S0264127521005633.
A.A. Shapiro, J.P. Borgonia, Q.N. Chen, R.P. Dillon, B. McEnerney, R. Polit-Casillas, L. Soloway (2016). Additive manufacturing for aerospace flight applications. J. Spacecraft Rockets. [Online] Available at: https://doi.org/10.2514/1.A33544.
Disclaimer: The views expressed here are those of the author expressed in their private capacity and do not necessarily represent the views of AZoM.com Limited T/A AZoNetwork the owner and operator of this website. This disclaimer forms part of the Terms and conditions of use of this website.