Ceramics are finding an increasing range of applications, however, the limitations for their use often relate to surface phenomena such as fracture initiation effects, environmental degradation and complex tribological interactions. Typical applications for surface engineered ceramics include:
• Ultra-low friction ceramic bearings with MoS2 lubricating coating
• Diamond coated silicon nitride and cemented carbide cutting tools for machining advanced aluminium alloys and metal matrix composites
• Low friction biomedical components such as ceramic femoral heads or alumina dental prostheses coated with diamond-like carbon
• Sputtered titanium layers to enhance the wetting of SiC and Si3N4 materials by brazes and improve joint strength
• Plasma sprayed yttria coatings for high performance crucibles and furnace elements
• Ion implanted waveguides in LiNbO3 for electro-optic devices
Surface Engineering Processes
There are a large number of surface engineering processes which are used in the treatment of metals ranging from deposition of relatively thick coatings (>1mm) by weld overlaying to very thin surface modification by ion implantation (<1µm) However, there are relatively few techniques which are applicable to ceramics, table 1. This is because ceramics are relatively inert, strongly bonded substances and their high melting temperatures lead to low bulk diffusivities, e.g. by vacancy mechanisms. These characteristics hamper equilibrium treatments for surface modification by reaction or diffusion, and hence the non-equilibrium mechanisms involving energetic ion bombardment can provide a useful set of alternatives. In addition, ceramics are often insulators that make use of electrical-based coating techniques such as electroplating difficult. Thus, plasma, ion beam and laser beam treatments show the greatest promise for the surface engineering of ceramic materials.
Table 1. Examples of surface modification technologies for ceramics.
|
Plasma spraying
|
Improved high temperature protection
Reduced interaction with molten metals or glass
|
Chemical Vapour Deposition (CVD)
|
Sealing of pores and cracks
Reduced friction and wear
High temperature protection
Improved optical properties
|
Physical Vapour Deposition (PVD)
|
Reduced friction and wear
Joining
Improved optical properties, filters, thermal management
|
Ion implantation
|
Improved friction and wear
Improved toughness and fatigue
Modified reflectivity
Catalytic activity
|
Laser treatment
|
Sealing cracks and pores
Improved friction and wear
Improved toughness and fatigue
Etching of device structures
|
Fracture Toughness
Ion Implantation
The fact that ion bombardment can introduce a large biaxial compressive residual stress in the surface of a ceramic material has been known for over 20 years. The damage created by the ions as they come to rest in the material (and to a lesser extent the ions themselves) causes an expansion of the layer which puts it into compression and closes surface flaws. This improves toughness for ceramics where surface flaws dominate behaviour. In addition, the ion implantation will modify the plasticity of the surface layer and hence reduce the likelihood of fracture mechanisms based on dislocation pileup for crack initiation. Ion implantation with nickel has been shown to considerably improve the fracture toughness of alumina despite treating only the outermost layers of the material (<1µm).
Ion Beam Mixing
Similar improvements in toughness can be achieved by ion beam mixing. In this process a thin layer of a metal (such as nickel or titanium) is evaporated onto the ceramic surface and then bombarded with an ion beam (generally of argon or another inert gas) to mix it with the surface layer of the ceramic. The advantage of this technique is that much higher metal contents can be achieved in the surface layer without recourse to expensive metal ion implantations since large area, high current ion beams are relatively easy to produce from gaseous source materials.
Laser Processing
Improvements in toughness can also be achieved by laser processing of ceramic surfaces. In the laser glazing process the surface of the ceramic is locally melted and can flow to fill pores or cracks. This process can effectively seal porous materials for use in vacuum equipment as well as improve the toughness of the ceramic. Alternatively the laser can be used to melt a thin metal coating deposited onto the surface that will penetrate and fill surface flaws and improve the toughness in much the same way as for the ion implantation techniques.
Friction and Wear Resistance
Wear in brittle material depends not only on their hardness, but also on the friction coefficient (which controls the magnitude of the tensile shear stresses) and the fracture toughness. Ceramic on ceramic friction can be very high (µ>0.5) in a range operating environments. The contact of basically brittle materials in non-conforming contacts can lead to wear by fracture process which leads to very short component lifetime Increasing the fracture toughness of the ceramic surface or reducing friction will thus improve wear performance.
PVD Deposited Lubricating Coatings
In order to reduce ceramic/ceramic friction a thin lubricating coating such as molybdenum disulphide or diamond-like carbon can be used. Durable MOS2 coatings applied to silicon nitride ball bearings by PVD processes maintain friction coefficients of <0.1 for over 100,000 cycles in vacuum, figure 1. In this application the hard nitride substrate gives excellent load support to the MoS2 coatings and performance is thus considerably better than similar coatings on bearing steels (52100, 440C etc). The low friction occurs due to shearing in the coating. A reduction of friction coefficient to ~0.15 can be achieved in air by coating the bearing surface with diamond-like carbon by plasma CVD or ion beam processes. In this case the inert carbonaceous film reduces the adhesion between the sliding counterfaces and its excellent wear resistance gives the necessary durability.
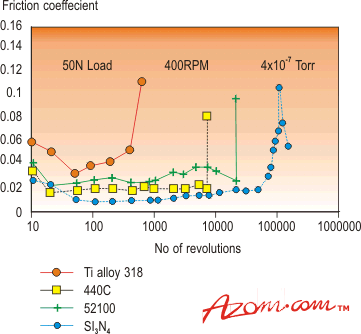
|
Figure1. Variation in the co-efficient of friction with number of cycles for a range of MoS2 coated bearings. The best performance gains were for coatings on Si3N4.
|
Laser Alloying
Similar friction reductions can be achieved by laser alloying, e.g. when titanium is laser alloyed with zirconia, a reduction in the coefficient of friction against a steel pin is observed. This is due to the formation of a titanium-rich oxide layer which is behaving as a solid lubricant.
CVD Diamond Coatings
The extreme hardness and chemical inertness of diamond makes it an ideal candidate material for tribological applications. Silicon nitride and cemented carbide cutting tool inserts coated with CVD diamond are now under development for the machining of advanced aluminium alloys (e.g. Al-13% Si) and metal matrix composites which cannot be processed successfully using existing tools.
Ion Implantation
The wear resistance of ceramics can be considerably improved by ion implantation. The process is complex and a number of distinct regimes of behaviour are observed. For instance ion implantation of alumina by titanium or yttrium, with the dosage up to a maximum, increases the hardness and abrasive wear resistance at the onset of amorphisation. This increase is accompanied by an increase in friction. Once sufficient energy has been deposited into the ceramic and amorphisation takes place the ceramic is softened again and the friction is reduced. However, it retains some of the compressive stress generated by ion bombardment and the amorphous layer can act as a lubricant if it reaches the surface. Considerable reductions in wear with the bonus of low friction are produced by this treatment.
Summary
It is thus evident that what is ideally needed on a ceramic surface is a hard, tough, low friction layer which is well bonded to the substrate. Both ion implantation and vapour deposition can produce layers that fulfil some of these criteria, but no process generates all of the desired properties. Surface treatments thus need to be optimised for each tribological application.
Corrosion Protection
Although ceramics are generally considered to be chemically inert there are often corrosion problems that depend on the operating environment. For instance, silicon nitride bearing materials wear rapidly in aqueous environments due to a corrosion based mechanism. In addition, non-oxide ceramic materials such as silicon carbide can be catastrophically oxidised at elevated temperatures (~1000°C) when thermal cycling disrupts the formation of the protective oxide scale. Complex coatings are under development to protect these materials for structural use in furnaces and incinerators.
Coatings for Graphite and Carbon
Graphite and carbon-carbon composites are good high temperature structural materials for use in vacuum but are oxidised rapidly in air at temperatures above 600°C. The oxidation resistance of graphite at higher temperatures can be improved by coating with CVD silicon carbide, but problems with cracking of the coating are encountered during thermal cycling. One solution is to deposit a borosilicate glass under the silicon carbide layer which is molten at temperatures around 900°C. This can flow into cracks as they are formed and seal them. Complex multilayer systems are under development to improve on the lifetime of these coatings.
Joining of Ceramics
The joining of ceramics to metals or other ceramics is relatively difficult due to their refractory nature and thus a number of techniques have been developed to improve bonding. Vapour deposition processes have been used in joining, both to modify the wetting behaviour of the ceramics and deposit reactive materials that are needed for bonding.
Brazing
Brazing of ceramics such as silicon nitride involves high temperatures (in excess of 850°C) and reactive alloys such as eutectics containing titanium. The elevated temperature is required to bring about a reaction to produce an interfacial compound (in this case titanium nitride and titanium silicide). One problem with brazing can be the wettability of the ceramic by the braze material at the joining temperature. Using conventional brazing techniques it is often difficult to get the braze to flow into the joint adequately. For this reason the braze material can be coated onto the bonding surface to ensure that an even distribution of material is achieved. Sputtering processes are ideal for this as the correct braze composition is easier to achieve from a solid braze source target. Alternatively a thin layer of nickel or titanium can be deposited onto the ceramic surface to improve its wettability to the braze.
Electronic and Optical Properties
The use of ion implantation, PVD and CVD for device fabrication in the microelectronics industry is well established. There is now an increasing interest in using the technologies to produce electro-optical devices; ion implantation techniques are under development for the fabrication of waveguide lasers e.g. by the helium implantation of Nd:MgO:LiNbO3 or Nd-YAG substrates. One of the greatest challenges for optics is the development of a computer based on an all-optical photonic switch which would replace the switching done by electronic transistors. It has been suggested that optical non-linearity could be used for switching of this type and ion implantation is being investigated as a method for tailoring the non-linearity of electro-optic materials in order that such devices can be made.
Thin coatings produced by PVD or CVD are used to change the IR transmission of architectural glass for building thermal management (i.e. to keep heat in the winter months and heat out during the summer). Similar coatings are used for filters or anti-reflection layers. This represents the largest scale use of surface engineered ceramic materials.
Conclusions
Monolithic ceramic materials and ceramic composites are being evaluated in a number of industries, e.g. aerospace, automotive. However, to generate the required surface properties, surface treatment is necessary in some applications. A range of surface treatment technologies are available for ceramic materials but many of the procedures developed for the treatment of metals need to be modified if they are to be used for ceramics. For instance the spray efficiency and adhesion of plasma sprayed oxide coatings on ceramic substrates is much worse than on metals. As these technical problems are solved and the performance requirements for components become more severe there will be an increasing industrial utilisation of surface engineered ceramics.
|