Feb 27 2013
Throughout 2013, the Navy Metalworking Center (NMC) is celebrating 25 years as an Office of Naval Research (ONR) Manufacturing Technology Program (ManTech) Center of Excellence and is looking to build on its advancements in metalworking and manufacturing technology.
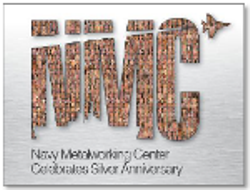
Since its inception in 1988, NMC (formerly known as the National Center for Excellence in Metalworking Technology) has grown and adapted to the Navy's evolving needs and manufacturing advancements.
"NMC has adeptly answered Navy ManTech's call to implement project results, and they do that through their industry partnerships and strong program and project management skill sets," said Gregory D. Woods, NMC's ONR ManTech Program Officer. "NMC routinely strives to balance innovation with the practical application of advanced manufacturing processes to improve ship construction."
Through the years, NMC has advanced and applied a vast range of metalworking technologies to defense-related manufacturing issues. Technologies include friction stir welding, plasma arc cold hearth melting, centrifugal casting, flow forming, semi-solid metalworking, investment casting, powder injection molding, superplastic forming, single crystal fabrication, hot isostatic pressing, electroslag surfacing, plasma coatings, hybrid laser arc welding, hydrostatic extrusion, advanced hull coatings, automated thermal plate forming, and electron beam direct manufacturing.
"We are very honored that ONR has trusted us to operate this important program for the long term," said Edward J. Sheehan, Jr., President & Chief Executive Officer, Concurrent Technologies Corporation (CTC). CTC operates NMC, which is one of seven ONR ManTech Centers of Excellence. "Our longevity and record of success is a testament to our highly capable and dedicated program and technical staff. NMC was CTC's first contract, and we intend for it to be a cornerstone of our company for a long time to come."
Throughout its 25-year history, NMC has supported the metalworking manufacturing needs of a significant number of Navy ship and air platforms, along with other Department of Defense (DoD) weapon systems, including the F/A-18 Hornet, F-14 Tomcat, F-22 Raptor, H-53 Sea Stallion, V-22 Osprey, T-45 Goshawk, MH-60R Seahawk, MH-60S Knighthawk, RAH-66 Comanche, Phalanx Close-In Weapon System, LPD 17 class amphibious transport dock, M777 Lightweight Howitzer, Navy Unmanned Combat Air System, CVN 76 Nimitz class aircraft carrier, and Expeditionary Fighting Vehicle. Today, NMC supports Navy ManTech's Investment Strategy, which focuses on five key Navy platforms: the Virginia Class Submarine, DDG 51 Class destroyer, Littoral Combat Ship, CVN 78 Class aircraft carrier, and Joint Strike Fighter.
NMC works closely with Navy weapon system primes, government and industry partners to develop the best technical solutions and to ensure likelihood of implementation. "As you might expect, NMC's achievements are the result of the hard work, dedication and talent of many people across a wide area," said Daniel L. Winterscheidt, Ph.D., NMC Senior Program Director, who is marking his 10th year in that role in 2013. "First, our CTC employees have outstanding technical and administrative skills. Each project also leverages the expertise of the Navy shipbuilding community and private companies. Finally, we are thankful for the direction and ongoing support of the Office of Naval Research."
The Center initially focused on metallurgy and metalworking manufacturing research and development to enhance system operability and to improve military readiness. In recent years, ONR's mission has been to optimize and implement innovative manufacturing solutions in the U.S. industrial base that reduce the total ownership cost of Navy weapon systems. NMC's portfolio of nearly 300 projects has contributed significantly to the Navy's goals to improve the performance, affordability, and sustainability of DoD weapon systems, and will result in cost savings of hundreds of millions of dollars for the acquisition of major platforms, including the Virginia Class Submarine, DDG 1000 and DDG 51 Class destroyers, the CVN 78 Class aircraft carrier, and the M777 Lightweight Howitzer.
NMC's efforts have been recognized by outside agencies, including the DoD Joint Defense Manufacturing Technology Panel (JDMTP). In 2008, NMC earned a Defense Manufacturing Technology Achievement Award for developing the LASer-welded corrugated-CORe (LASCOR) metallic sandwich panel technology that has been implemented on DDG 1000 and is saving the Navy considerable acquisition cost. NMC won the 2010 Defense Manufacturing Technology Achievement Award for the development and commercialization of a weld shaver system that was implemented in the construction of DDG 51 and DDG 1000 and has wide applicability for military ships, DoD weapon systems, and commercial structures. In 2012, an NMC-developed alternative brazing system was a finalist for the award.