A new finding in optimizing the heterojunction of metal alloy and carbon fiber by laser processing was considered in the journal Materials. Because of their high potential for usage in lightweight constructions, the production of heterojunctions with a good bonding interface among metals and nonmetals has received considerable attention.
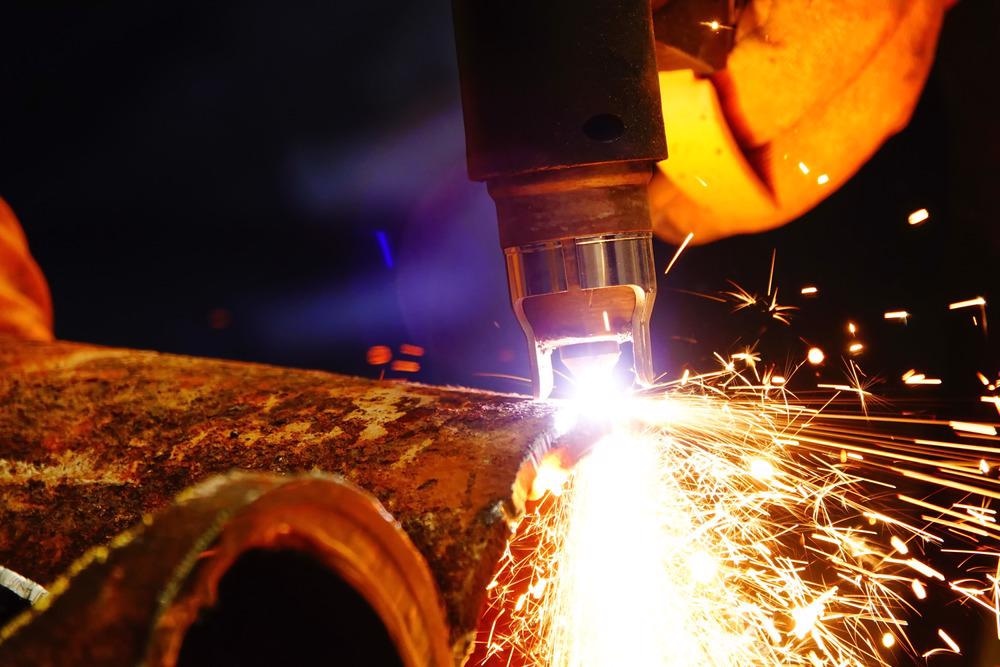
Study: Robust Heterojunctions of Metallic Alloy and Carbon Fiber-Reinforced Composite Induced by Laser Processing. Image Credit: pinkfloyd yilmaz uslu/Shutterstock.com
Laser joining innovation, which has evolved as a quick and dependable procedure, has demonstrated its viability and distinct advantages in attaching metal to polymer matrix composites. An optimal laser joining configuration was used to achieve a high-quality combining of titanium alloy and carbon fiber-reinforced composites in this study.
The cross-sectional microstructures of laser-produced joints show that micro-bubbles around the contact have been efficiently suppressed and removed as a result of the constant clamping pressure applied to the connected area during the joining process. Tensile studies indicate that joint strength improves with structural density on a titanium alloy surface, and the peak fracture strength of joints exceeds 60 MPa even after a high–low temperature alternate aging test.
Schematic diagrams showing the joined area (a) and the optimized laser joining configuration (b). Image Credit: Wang, H., et al., Materials
Developing New Materials for Heterojunction
Developing lightweight materials has long been an aim of sophisticated manufacturing companies such as automobile engineering and aerospace. Properties such as low density, high specific strength, and superior chemical resistance, several light materials, notably carbon fiber- and glass fiber-reinforced thermoplastics (CFRTP/GFRTP), have already been increasingly used to replace metals.
The difficulty of achieving high-strength heterojunctions among metals and thermoplastic composites is unavoidable in actual CFRTP/GFRTP applications. In response to this requirement, numerous procedures for combining metals and thermoplastics, including such adhesive bonding, mechanical fastening, and thermal welding, have been developed over the last few decades.
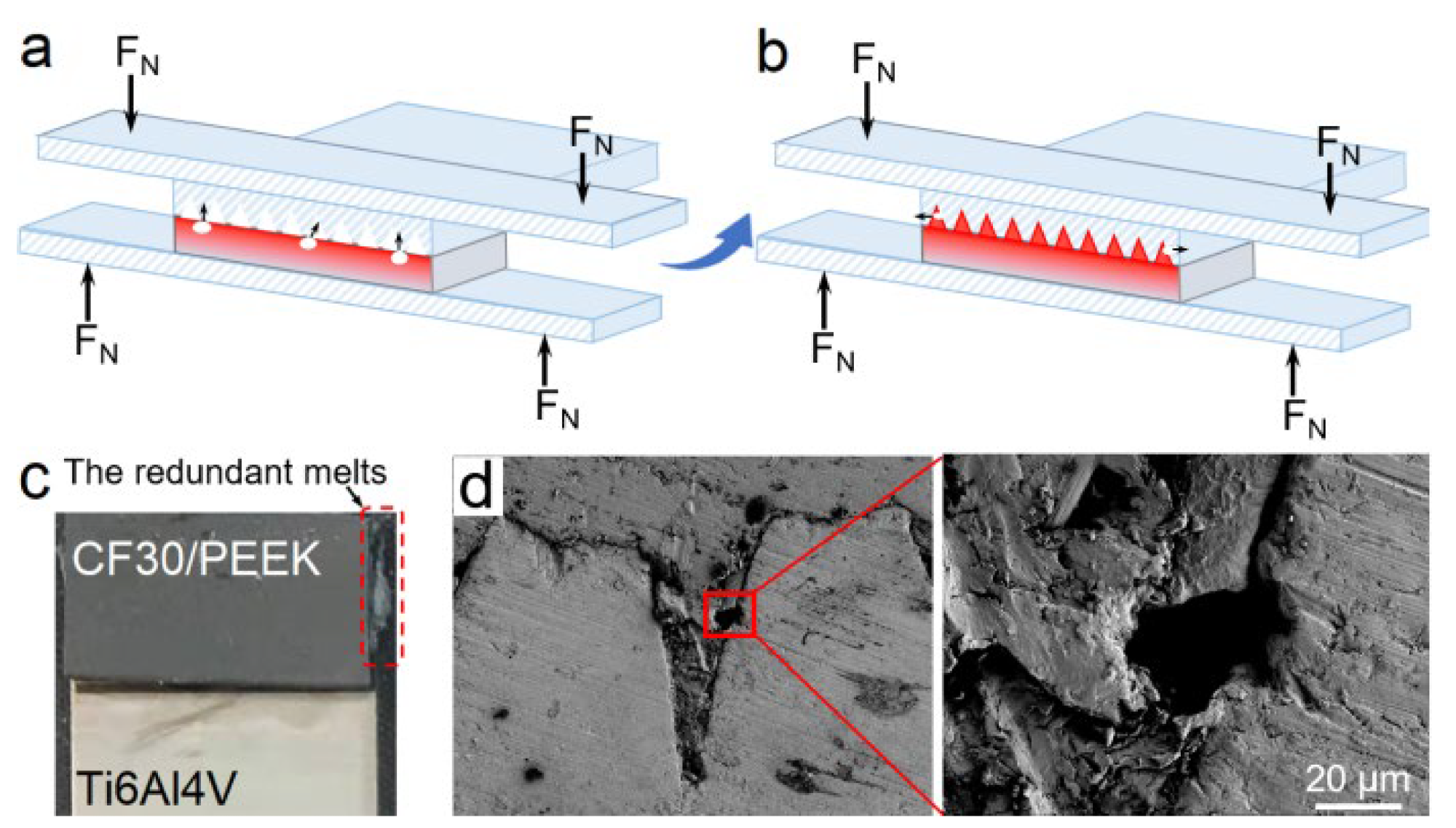
(a,b) Schematic diagrams showing the movement of the PEEK pyrosis-produced bubbles during the laser joining process. (c) Spill-out of the redundant melts after the laser joining process. (d) Cross-sectional microstructures of typical Ti6Al4V-CF30/PEEK joints (Sdf = 63.8%) with few microbubbles remaining near the interface. Image Credit: Wang, H., et al., Materials
Better Heterojunctions is Created
As a result, a simple optimized laser joining arrangement was proposed to decrease porosity along the joining contact and to build strong mechanical interlocks among titanium alloy and carbon fiber-reinforced polyetheretherketone (CF30/PEEK).
The mechanical squeezing pressure continually given to the joined area during the laser bonding process, where the laser-induced bubbles are pushed out from the melting zone due to the motion of melted polymers, is the process for minimizing porosity flaws. In this study, heterojunctions with bonding strengths of more than 60 MPa were created and persisted even after long-term high–low temperature alternating aging testing.
Laser Irradiation Using PEEK Matrix
When the heat of the PEEK matrix near the interface rises to the melting point throughout laser irradiation, the PEEK matrix melts, and the melted matrix material, along with the short carbon fibers combined in it, is forced to flow and complete the microgrooves or gaps among micropillars under clamping pressure. The process is supported by the displacement of air between the microstructures. The good mechanical interlocks formed around the interface contribute significantly to joint strength.
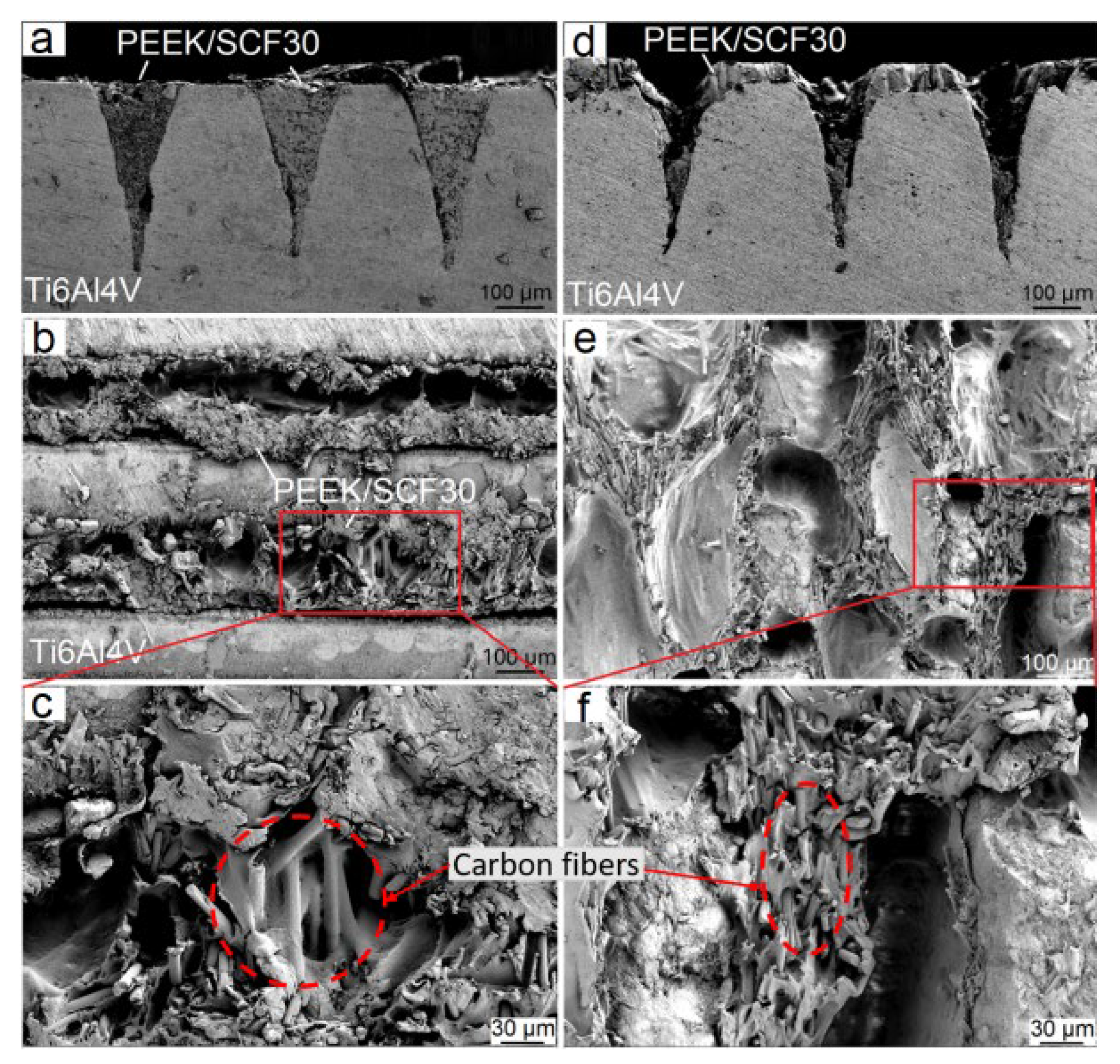
Typical cross-sectional images of the fractured joints ((a), (Sdf = 63.8%), (d), (Sdp = 85.6%)) and the morphologies of the detached surfaces (b,c,e,f) after tensile tests. Image Credit: Wang, H., et al., Materials
Laser Joining Procedure
On the focus plane, a continuous laser scanning system was used to perform the laser joining procedure. When the materials near the interface are heated to a melted condition, the melted materials are pushed to flow and fill the microgrooves due to the clamping pressure. The molten composites are cooled and solidified as the laser beam drifts away from the irradiation surface, leading in mechanical interlocks at the connecting contact.
When the materials near the interface are heated to a melted condition, the melted composites are pushed to flow and fill the microgrooves due to the clamping pressure. The molten composites are cooled and solidified as the laser drifts away from the irradiation surface, resulting in structural interlocks at the connecting contact.
Because of the tensile-induced peel stress at the borders of the overlap zone, joints with a greater structural density (>95%) fail owing to fracture of parent polymers near the connected area. When the structural density is less than 91.5 percent, the joints fail through an interfacial shear rupture with breaking. The high-performance heterojunctions that were created have a lot of promise in the aerospace and automotive industries.
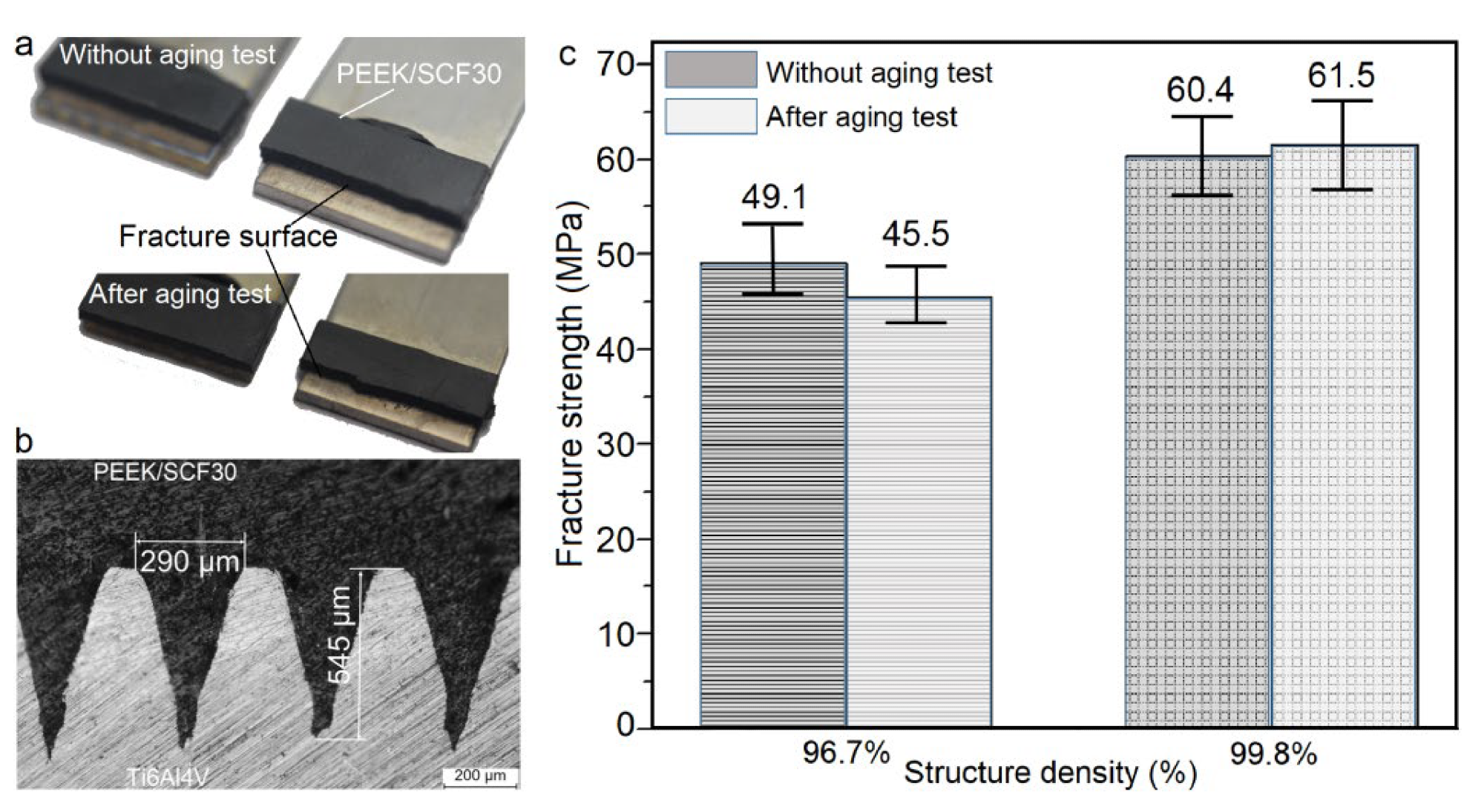
(a) The failure of Ti6Al4V-CF30/PEEK joints before and after the aging test. (b) The typical cross-sectional microstructures of the joint after the aging test. (c) Fracture strength of the LAJ-produced Ti6Al4V-CF30/PEEK joints before and after high–low temperature alternating aging tests. Image Credit: Wang, H., et al., Materials
Heterojunction Function
An interface among two layers or areas of different semiconductors is referred to as a heterojunction. In contrast to a homojunction, these semi-conductive materials exhibit asymmetrical band gaps. Numerous solid-state technology has revolutionized, such as semiconductor lasers, photovoltaic panels, and transistors, benefit from engineering the electronic energy bands. A heterostructure is a device that combines numerous heterojunctions, though the two phrases are usually used interchangeably.
This technology has a significant benefit in that it has a very high transconductance and the possibility for very high-speed operation. High electron mobility transistors (HEMTs) utilize heterojunctions to operate at substantially higher frequencies (over 500 GHz). The correct doping strategy and band alignment produce extraordinarily high electrons mobilities by forming a two-dimensional electron gas inside a dopant-free zone with minimal scattering.
References
Wang, H., et al. (2021). Robust Heterojunctions of Metallic Alloy and Carbon Fiber-Reinforced Composite Induced by Laser Processing. Materials 2021, 14(23), 7469; Published: 6 December 2021 https://www.mdpi.com/1996-1944/14/23/7469
Disclaimer: The views expressed here are those of the author expressed in their private capacity and do not necessarily represent the views of AZoM.com Limited T/A AZoNetwork the owner and operator of this website. This disclaimer forms part of the Terms and conditions of use of this website.