By Surbhi JainReviewed by Susha Cheriyedath, M.Sc.May 19 2022
In an article recently published in the journal Additive Manufacturing, researchers discussed the utility of a versatile thermally induced crosslinking binder for the additive manufacturing (AM) of robust structures.
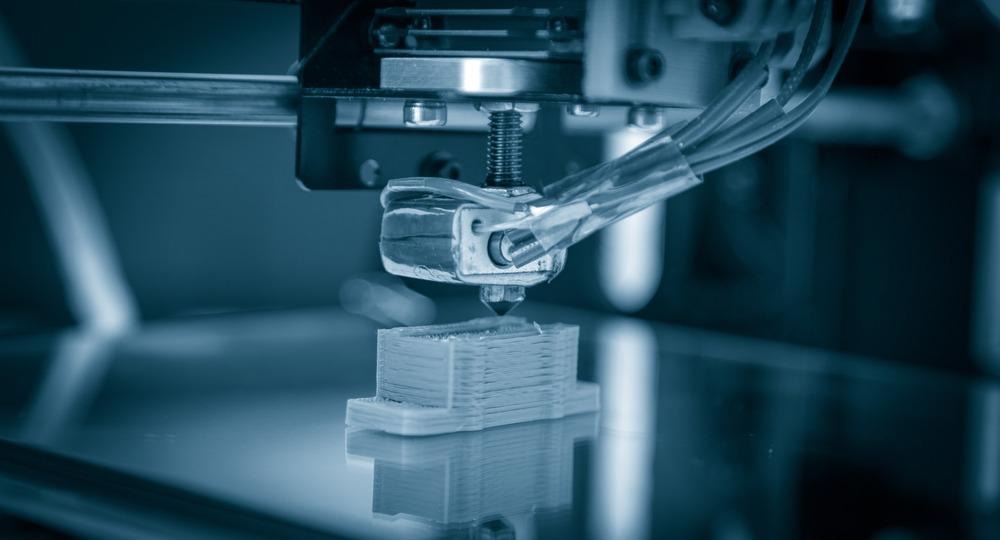
Study: A versatile thermally initiated crosslinking binder for additive manufacturing of strong structures. Image Credit: Alex_Traksel/Shutterstock.com
Background
Many attempts have been made to transition the mode of production from conventional manufacturing to AM for a number of materials, including structural ceramics, polymers, alloys, and various functional materials.
Due to its rapid production rates, powder self-support, wide material compatibility, and capacity to accomplish large-scale and high-volume production, binder jetting additive manufacturing (BJAM) is considered to be one of the most promising AM technologies for industrial applications. The inability of even state-of-the-art commercial binders to give high green strength has become a key technical barrier for BJAM, preventing its widespread adoption.
The current BJAM binder's bonding process is based on the formation of a binder–powder interfacial connection. Although polymer binders have a clear advantage over inorganic or low molecular organic binders in terms of network continuity, improving their crosslinking density, which is responsible for their poor green strength, remains difficult. The fundamental difficulty for BJAM binders is to preserve their universality for varied powder materials while obtaining high green strength.
About the Study
In this study, the authors discussed the potential of a versatile thermally initiated crosslinking (TIC) binder solution made up of an initiator ink and an in-bed monomer/crosslinker mixture for BJAM to address the issue of low green strength. BJAM's binder was designed using a TIC technique to achieve binder universality and high green strength at the same time.
The team conducted three-point bending tests to measure the flexural strength of SiC green parts with varied crosslinker and monomer contents, SiC and plaster green parts using a commercial binder, and Al2O3 and 316 stainless-steel green parts using the TIC binder.
The researchers used the simultaneous thermal analyzer (STA) to measure the thermogravimetry (TG) curve of P(AAm/Bis). The TIC binder was used to print a range of powders into green parts with high flexural strength in the range of 10.1–13.9 MPa and a fine geometric structure such as thin-walled structures, cantilevers, and 3D surfaces.
Observations
At their ideal binder proportions, the flexural strength of 316L stainless steel parts and green Al2O3 could reach 10.1 and 13.9 MPa, respectively. The SiC green parts' one-dimensional (1D) volume and size change were both less than 1.7% and 0.6%, which showed that the AAm and Bis crosslinking procedure was truly a near net size process for green parts.
A thin rod with a 3 mm x 5 mm x 40 mm dimension could raise a weight of 1 kg, while a 1.5-mm-thick sheet could support a weight of 0.5 kg. At a 12 wt.% AAm content, the maximum effective flexural strength of 13.2 MPs was achieved.
The TG curve of P(AAm/Bis) showed a 98.28% weight loss with a 1.72% residue at 800 °C in air, wherein this residual amount occupied only 0.32 wt.% of the green portions, which indicated the binder's reasonable burning capabilities. The addition of the AAm and Bis powders reduced the powder packing density by 6.5–10% at the optimal green strength formulation.
To pack the printed powder, the TIC binder could build a uniform, continuous, and strong crosslinked network. The created TIC binder provided green components with a flexural strength of 10.1–13.9 MPa for many powders, including Al2O3, SiC, and 316L stainless steel.
For complex and fine geometric shapes, the TIC binder also demonstrated exceptional robustness and print reliability. It was demonstrated that the created binder could produce a high flexural strength of green sections. Crosslinkers and monomers, which were pre-dispersed consistently in the printed powder, helped the TIC binder work during the crosslinking process. Owing to the presence of primary amine groups in the monomer, the TIC binder could induce good interfacial interactions with printed powders. More crucially, the TIC binder could create a high-strength and continuous crosslinked network on its own. These characteristics allowed the TIC binder to combine the printed powders to form robust green pieces.
Conclusions
In conclusion, this study elucidated that the proposed TIC binder is suitable with a variety of powdered materials and provides great print stability for intricate fine structures. The TIC binder's spatial distribution density and crosslinking density were critical criteria for achieving high green strength. The binder also had a number of advantages, including an extremely fast curing time, low cost, and reduced burnout.
The authors believe that the created TIC binder solution will solve the problem of low green strength in BJAM technology, allowing it to be used more widely in the industrial business. They also mentioned that the obtained characteristics, when paired with the benefits of ultrafast curing speed, low cost, and minimal burnout, indicated that the TIC binder solution has the potential to have a significant impact on BJAM advancement.
More from AZoM: What are Profile Roughness Parameters?
Disclaimer: The views expressed here are those of the author expressed in their private capacity and do not necessarily represent the views of AZoM.com Limited T/A AZoNetwork the owner and operator of this website. This disclaimer forms part of the Terms and conditions of use of this website.
Source:
Lv, X., Ye, F., Cheng, L., et al. A versatile thermally initiated crosslinking binder for additive manufacturing of strong structures. Additive Manufacturing 102893 (2022). https://www.sciencedirect.com/science/article/abs/pii/S2214860422002913