The thermocouple is the smallest part of a thermal element, consisting of two electrical conductors that have very different Seebeck coefficients to produce the maximum thermoelectric voltage possible. Semiconductor blocks are typically used and are linked at the ends with copper. Hitherto, bismuth telluride in n- and p-doping is the most suitable material for ambient temperature applications (Figure 1).
.jpg)
Figure 1. Thermocouple
Peltier Element
Peltier elements are thermoelectric components capable of pumping heat from one end of the device to the other end based on the direction of current. An advanced Peltier element comprises several thermocouples that are electrically connected by copper bridges in series (Figure 2). Ceramic plates made of aluminum oxide are used to thermally bond the copper bridges. However, the copper bridges are electrically separated from each other.
.jpg)
Figure 2. Peltier element
Peltier Module
Thermally coupled heat sinks and Peltier elements are the components of a Peltier module (Figure 3). The electric energy applied to pump is irreversibly transformed into heat in the Peltier elements, and requires effective dissipation. Moreover, heat generated is reversibly pumped by the Peltier elements from one side to the other based on the direction of the current flow. This leads to the absorption of heat on one side, but the amount of heat absorbed is much lower than the amount of heat released on the other side. Consequently, heat transfer must be taken place across large-sized heat sinks line on each side of the Peltier element. The heated or cooled air is diverted with the help of powerful fans.
.jpg)
Figure 3. Peltier module
Controlling a Peltier System
Pulse width modulation involving control of the average current by the length of high frequency current pulses is used to control Peltier elements. Another commonly used method is voltage regulation. However, simple on-off control is recommended due to the possibility of reduced component life caused by the heavy load on the Peltier element. Peltier modules can be regulated by reversing the direction of the current, but reversing the polarity prior to equalizing the temperature in the Peltier element will expose the Peltier element to enormous thermal stress.
Advantages and Drawbacks of Peltier Systems
The following are the advantages of Peltier elements:
- Highly reliable, durable, and requires less maintenance as they do not contain moving components that are prone to wear
- Vibration and noise-free operation
- Lightweight and smaller footprint
- Low manufacturing cost
- Absence of refrigerants that are ozone depleting or flammable
- Eliminates the entire cooling system consisting of condenser components, compressor, large evaporator, and inductor
- Peltier elements require no maintenance and are easily replaceable in the event of failures
- Accurate metering of the cooling effect when compared to traditional compressors, thanks to the advanced control technology
- System function can be reversed by reversing the polarity
The following are the drawbacks of Peltier elements:
- Cold and hot sides are very close to each other, posing a challenge for efficient heat transfer from and to the module; large heat sinks with fans are used for this purpose.
- A Peltier module’s performance relies on the required temperature difference. Complex multistage elements are required to achieve greater temperature differences.
- In Peltier elements, the current behaves a refrigerant in the cooling cycle and its flow influences the pumping capacity. Hence, the pumping capacity needs to compensate for the loss of power due to the irreversible conversion of the current into Joulean heat and the resulting heat loss on the cold side, prior to a net cooling capacity results. Therefore, it is necessary to accept a multiple of heat pumping capacity for power loss in Peltier systems.
- Conversely, in compressor systems, the cooling capacity is above the work to be invested by roughly two folds.
Areas of Application of Peltier Technology
Thermoelectric cooling technology is applied in areas requiring low level cooling and where energy efficiency is not a priority or using compressors is not feasible due to their size. Peltier-based coolers are ideal for campers or cars for active cooling of beverages and foods, thanks to their portability and option of directly plugging into a 12V electrical system.
Thermocycler used for multiplying DNA sequences employs Peltier temperature control to achieve three different reaction temperatures in quick succession for this polymerase chain reaction. Due to their small size, Peltier elements can be used to cool scintillators in order to reduce the noise of the photodiodes. Unlike compressors whose operation relies on their position, Peltier modules are used to construct battery-operated mobile devices, such as refractometers, rheometers, viscometers, and density meters.
Since the amount of heat dissipated by Peltier elements is more than the amount that they can pump, they can be used to cool computer processors to a temperature below ambient temperature. Multistage Peltier modules are used in dew point mirror hygrometers and IR sensors, thanks to their ability to create a temperature difference of over 100k. Peltier technology is also suitable for heating and cooling of diffusion cloud chambers involved in the detection of particles such as positrons, electrons, and alpha radiation.
Peltier technology is also used in the cooled incubators involving incubation at or around ambient temperature (15 - 30°C), or in areas involving heat input, eliminating the technical complexity and drawbacks of a compressor system.
Conclusions
Peltier technology paves the way for special applications, where maximum energy efficiency or cooling power is not required. It is scalable and location independent, facilitating the development of tiny or portable systems. Cooling capacity can be finely metered with the help of Peltier modules, providing efficient temperature control at lower temperature gradients. However, the inefficiency of Peltier technology makes it inferior to compressors in applications like household refrigerators and freezers.
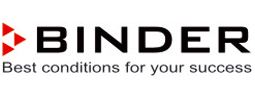
This information has been sourced, reviewed and adapted from materials provided by BINDER GmbH.
For more information on this source, please visit BINDER GmbH.