AZoM spoke to Yannick Galais, General Sales Manager of Luxinar, about Luxinar's laser technology and how it is used in the automotive industry.
What is the history of Luxinar over its 22 years of operation?
Luxinar was established in 1998, 22 years ago. Over the last 22 years, we have launched some major products in the marketplace. For example, the MULTISCAN VS and HE, which have been the fastest marking systems available in the market. Even now they are still the fastest CO2 laser marking systems.
In 2004, we also introduced a 600 W laser. That was the first ever sealed 600 W laser available on the market, and we won a Queen's Award for innovation for that technological breakthrough. We built on that success and over the following years, we were awarded a second Queen's Award for international trade and growth in export markets. In 2017, we reached a turnover in excess of £30 million.
The last year has been a major year in our history. We rebranded the company and we are now Luxinar Ltd in the UK. We launched the new branding at the Laser World of Photonics exhibition in Munich last year.
We are a UK company and we are based in the north east of England. We have got a brand new factory that we moved into in 2016, which was built according to our needs. Across our sites, we have 173 employees, and we also have six sales offices; two in southeast Asia, two in Europe, a sales office based in the HQ in Hull, and a sixth one in Detroit. All of these offices have sales and technical support facilities so that we can provide technical support and support from an after-sales point of view to all of our customers around the world.
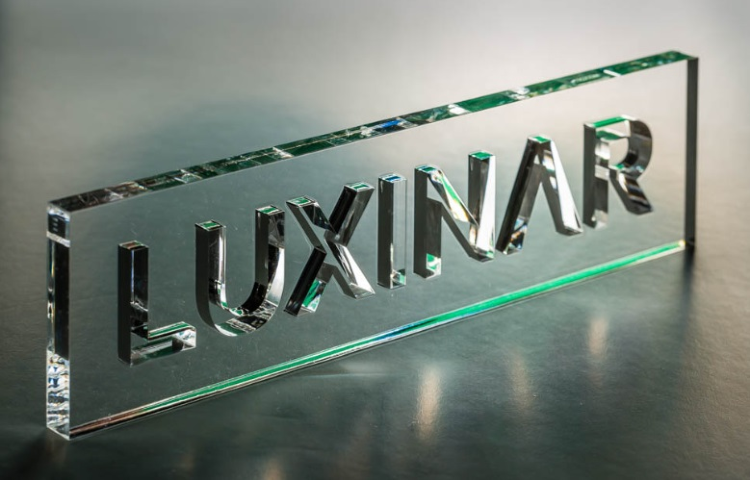
Image Credit: Luxinar
What products do Luxinar provide?
We have got two families of products: the sealed CO2 laser sources and the MULTISCAN marking system, which is the fastest in the marketplace. Our sealed CO2 laser includes a range called the SR Series, which is from 80 W to 250 W.
These are fairly unique in the marketplace because they are IP66 rated, which means they are fully sealed and there is no ingress of any kind of water, dust, or other elements that could contaminate the beam. The range also includes sealed CO2 laser sources from 350 W to 1 kW. All these lasers have been designed with industrial applications in mind, so they are extremely reliable.
They are also easy to maintain or to service. I would even say that they are maintenance-free, to a certain extent, due to the fact that they are sealed. One of the major characteristics of our lasers is that they all come with at least 20 percent headroom compared to the rated power. This will give users an extended lifetime for all the laser sources.
Our second range is the MULTISCAN. This has two products within the range: the MULTISCAN HE and MULTISCAN VS. They are basically the same modules with the same 125 W laser, water-cooled system, power supply electronics, software, beam delivery system, and scanners.
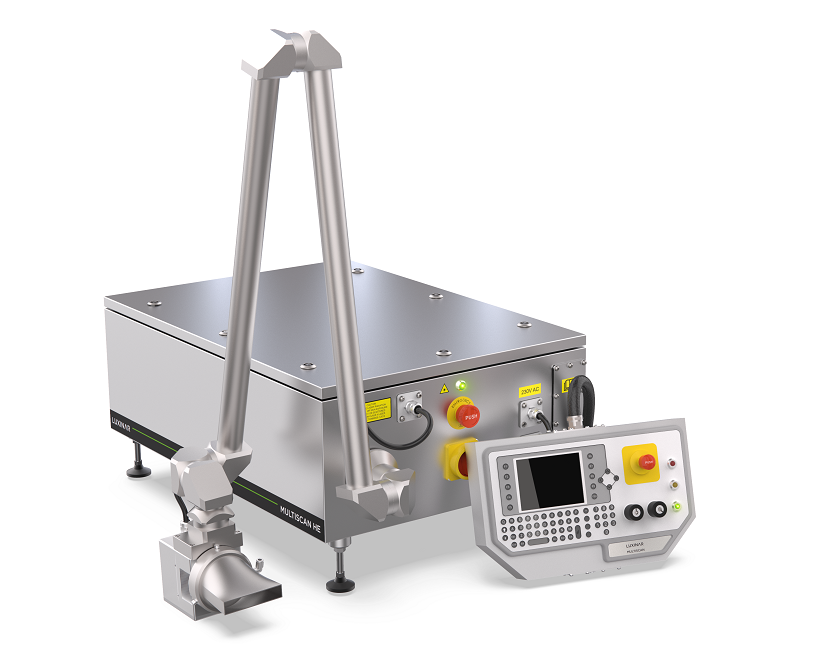
MULTISCAN HE. Image Credit: Luxinar
However, the HE is designed for harsh environments, whereas the VS is more suited to cleaner environments, such as a clean room or a lab. Both of the systems are plug and play, and once they have been installed, users can forget about them and they will continuously mark your product.
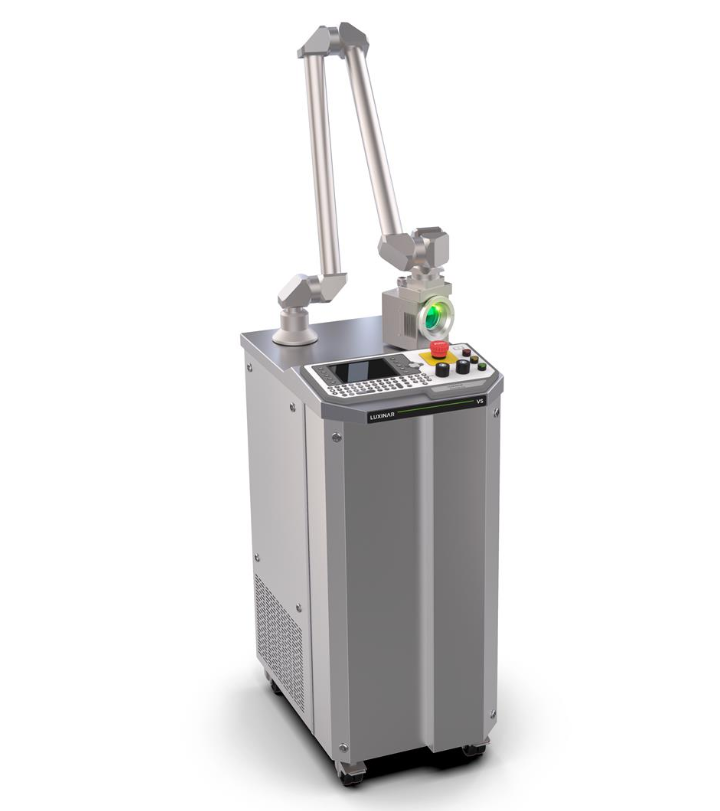
MULTISCAN VS. Image Credit: Luxinar
In what type of markets and applications have Luxinar’s products found success?
In terms of the markets where we operate and where our lasers are used, the most significant ones are the electronics, glass, and fashion markets. Fashion is an interesting market. Here our products are used to finish denim and make stonewashed or worn look jeans.
We have also found applications in packaging, for kiss cutting labels (cutting the top layer without cutting the carrier underneath) and stickers, for example. In the food and beverage industry, we make micro perforations in plastic packaging film to allow packaged vegetables and fruits to last longer on the shelves.
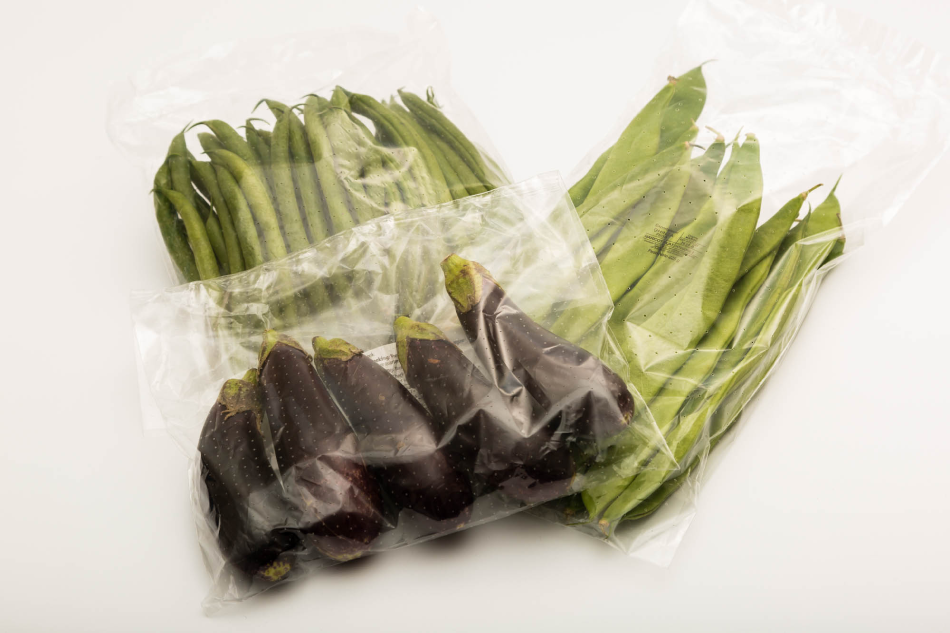
Image Credit: Luxinar
However, we have found great success in the automotive market. Within the automotive market, there are more than 19 applications for which our lasers are used. These include rubber windscreen wiper cutting and marking, textile cutting of seat belts, and spoiler paint removal which enables the bonding process onto the body of a car.
But I'm going to focus on e-mobility and the electric motor, and also how we can bring the laser beam to the work piece. In terms of e-mobility, the components of stop and start motors are very often made of copper strips, which are coated with a dielectric made from enamel to prevent short-circuiting. But, during the process, the enamel has to be removed in order for the components to be welded together. The coating can be made of different kinds of materials, such as PEEK, PFA-PI, or PA, and the thickness of this coating can also vary from application to application.
There are different ways of removing this coating, and the conventional method would be to use mechanical tools. However, there are several issues with this method. The first one is that it is a contact process, meaning you will damage the surface of the copper. But, most importantly, you are going to remove a thin layer of copper during the process. As copper is an extremely expensive material, you do not want to lose these fine particles of copper over a period of time. It could be worth a lot of money.
An alternative to this method would be to use CO2 lasers. This is a totally contactless process, meaning the copper surface isn’t damaged. There is no ablation or loss of copper material, and, as it is a digital process, it can be changed quickly with very little downtime and very little changeover for new tools, as there are a limited number of tools that are required in this process. It is a very versatile, very flexible process in comparison.
In our application laboratory, we have been able to remove roughly 31 mm² of enamel in 3.1 seconds, showing that it is also a very fast process.
Most of the components you'll find in cars or components are made of plastics or composite materials. There are plastics everywhere. CO2 lasers can easily process plastic components, whether this is for cutting, drilling, ablating (removing materials) or marking. With most of the plastic we can process, the processing speed is linear to the power of the laser, so it is very easy to anticipate or to predict what kind of process speed you can get according to the laser you are going to use.
Some examples of the parts we have processed with lasers include ABS, HDD, and PP. What is common with all of these materials is that there is no need for a post-processing process or cleaning process. The edges are very clean and you can use the part immediately after being processed by the laser.
Again, it is a digital tool, so there is very limited or even no investment in tooling and jigs. The changeover and downtime are also extremely quick.
The interesting question with lasers is that yes, you can process all these components, but how do you bring the laser beam to the work piece?
Luxinar develops laser technology for cars
Luxinar has also found applications in robotics. Could you tell us how Luxinar lasers are used in this area?
On the production line, automation and speed are key, so being able to bring the laser to the work piece, from both an automated and robotics point of view, is extremely attractive for car manufacturers.
One method of bringing the beam to the work piece is to mount the laser on the robots. That means that the laser has to withstand several Gs of acceleration forces when the laser on the robot moves. Our lasers are designed to handle these acceleration forces.
They are also lightweight, which means that the robot does not need to be a heavy duty sort of robot structure. It is well designed for this kind of application, but it is necessary to have a fairly complex beam delivery system with either a scanner or cutting edge at the end of the robotic arm to process the components.
The second method of bringing the beam to the work piece is to have a stationary laser, a stationary beam delivery system and a moving component in front of the laser. The car dashboard, as shown in the video in the presentation, is presented in front of the laser beam and manipulated to show the different sides to be processed.
The third method would be a stationary laser as before but the beam would be taken to the work piece by an articulated arm. The articulated arm is attached to a robot which will follow the contour of the part to process. The laser will cut excess material on A-pillars in the car, as shown in the video in the presentation, and the robot will only handle the lightweight, articulated beam delivery system.
How does Luxinar support customers with their applications?
To support our customers in terms of proof of concept, we have an application lab in Hull at our headquarters. We also have smaller labs in our different offices around the world.
If a customer needs to make holes or cut material on an automotive component, for example, they would send us some samples and we would use a range of equipment to get as close as possible to the process they are going to design. For instance, we have carried out work with our robot cell where we followed the contour of 3-D complex components. We also have a 3-D scanner for applications where the depth of focus changes. We will choose the right equipment according to the customer’s specifications.
We have some measurement equipment to make sure that what we have done for the customer can be measured and that it meets their specifications. I want to emphasize, however, that these are only pieces of equipment used for the proof of concept. We do not sell the full system. It is to help the customer to design their own solutions.
Where can our readers go to find more information?
Readers can find more information on our website, www.luxinar.com, where they will find the whole product range, applications, and products we could offer them and markets we are involved with. Readers can also contact me directly on my email address, and I will respond very quickly to your request.
If readers want more information about what the laser can do, feel free to contact us. We have 20 years of experience, so we are able to support customers in many different ways.
Our lasers are from 80 W to 1 kW, meaning we should be able to accommodate most applications, and it is important to say that we are not restricted to the automotive industry. We operate in far more markets and sometimes even in markets we have not thought about before. I would urge readers to be adventurous and just send us their samples.
While I have spoken about some specific applications in e-mobility, plastic parts processing and robotic applications, we are involved in packaging, and electronics too. Do not hesitate to contact us, and our lab will help you in your proof of concept and finalize your ideas and your design.
About Yannick Galais
Yannick Galais is a General Sales Manager at Luxinar Ltd, where he is responsible for sales to the Americas, UK, France, Spain, Portugal, and India, as well as for internal sales. He is in charge of the applications and technical support departments.
Yannick has a Bachelor of Science degree in Mechanical Engineering from Polytech University Tours, France, and a Master's degree in Business Development from INSA Toulouse University, France. New business development is also a key component of Yannick’s role.
Disclaimer: The views expressed here are those of the interviewee and do not necessarily represent the views of AZoM.com Limited (T/A) AZoNetwork, the owner and operator of this website. This disclaimer forms part of the Terms and Conditions of use of this website.