Wedge wire, or as it’s sometimes known, profile bar, is mostly used in the manufacture of screens. It is classified as a type of screen wire as it is associated with a family of shapes that are utilized in the manufacture of screens, which are situated in a wide range of applications.
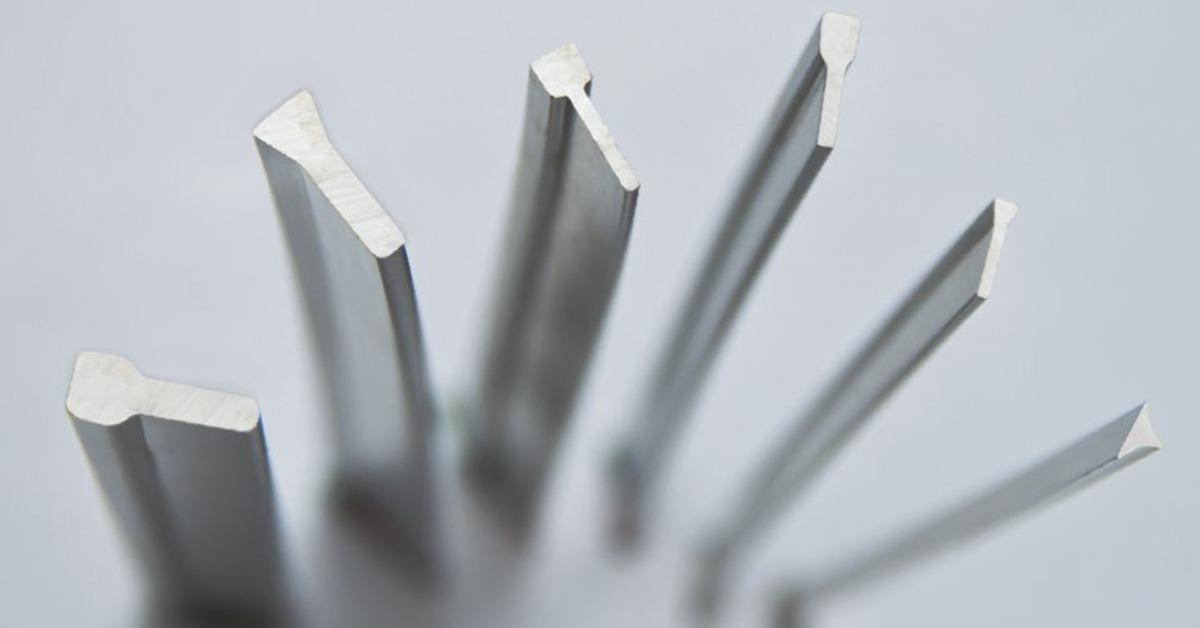
Image Credit: Ulbrich Stainless Steels & Special Metals, Inc.
The product has a triangular shape that has various ranges in height, width and radius on both the nose and corners. Alloys, temper and surface requirements vary depending on the application the screen will be used in. There will be a thorough explanation of this detail later.
Screens themselves are utilized across a wide range of industries. Some of the end uses most frequently used include water filtration, mineral processing, pulp and paper manufacturing, food processing, oil extraction as well as in applications for architecture.
Screen forms may differ as well, coming in cylindrical, flat and basket form depending on functionality of the end use.
At a glance wedge wire, may appear to be a very simple and straightforward product. This couldn’t be further from the truth. Extreme care and attention must be taken when designing a specification for wedge wire.
End users need to carefully consider when making the appropriate selection in order to design a screen appropriate for the application. Screens then rest on a support which can be supplied in round wire, screen wire, or roll formed strip, as well as many other options.
This forms a kind of screen panel, something akin to a strainer used in the home for making pasta, except much more complex.
What Materials and Alloys are Used for Wedge Wire?
Wedge Wire is very effective for separating and filtering solid materials from liquids. This can be crucial in numerous settings, but depending on the kind of application, the alloy and materials required can vary.
Filtering fluid in a market like the food and beverage industry, such as a microbrewery beer tank, may demand a different type of alloy than an application in the oil and gas market, like a well screen.
Selection of an alloy may also depend on manufacturing processes and additional elements that may need to be added to the wire before it is ready for use. In some instances, welded wedge wire is required, while in others, the profile supplied just needs to be placed on the support rod.
Alloy selection is key to the success of the end product. Thus, questions such as is the screen being utilized in a caustic or high temperature environment? Is weight a factor? Is there a need for a softer alloy that is more ductile, or is the preference for something that has high mechanical properties?
As a result, screens are manufactured using a wide range of different alloys depending on the end use. Wedge wires are manufactured out of carbon steel, red metals, stainless steels, aluminum, duplex grades and various other high performance alloys, including Inconel.
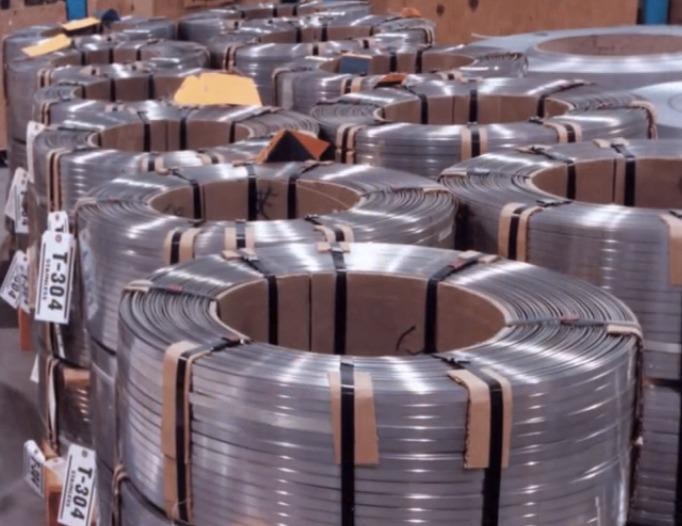
Image Credit: Ulbrich Stainless Steels & Special Metals, Inc.
There are several options for alloys. These include:
- 300 Series Stainless Steel
- 400 Series Stainless Steel
- 2205 Duplex Stainless Steel
- Aluminum
- Carbon Steel
- Nitronic
- Nickel alloys such as Hastelloy, Inconel and Monel 400
- Titanium
A typical popular selection is stainless steel wedge wire due to the wide variety of grades and, of course, price considerations on offer. After alloy selection, establishing the appropriate size for the application is the next phase of the process.
Ulbrich can supply this material from around .032 inches thick to almost any wire thickness exceeding that number. Wedge wire can also be supplied in any temper from annealed to full hard.
Selecting thickness and temper will also be dependent on the application. The end use of a novel wire shape can differ, and because of the various industries that may require filtration, it can be extremely useful.
Where and How is Wedge Wire Used?
After the wedge wire itself is fabricated, it will have to lie on a support, which, as previously mentioned, can include round or screen wire or even strip/sheet.
Screen wire and wedge wire screen is often manufactured in two, at times three, types of screens: Flat screen and Cylindrical screen are the most dominant types, but within cylindrical, there can be round and basket screens.
Flat screen is comprised of screen wire cut to precise lengths and is dry fit or welded to the screen’s structure. Conversely, cylindrical screens are made up of a spool of screen wire fed into a machine that winds the wire into a cylinder and subsequently welds the wire to the supports as the screen rotates and expands.
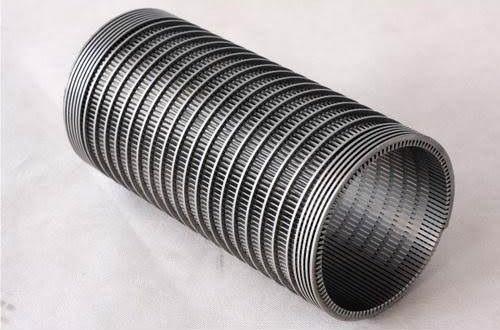
Image Credit: Ulbrich Stainless Steels & Special Metals, Inc.
If necessary, cylindrical screens can but cut and rolled flat into a flat screen configuration, and flat screens can also be roll formed into cylindrical screens. Each of these will depend on the application.
Specific Applications include:
- Architectural Applications
- Food Processing
- Microbrewery Beer Tanks
- Mineral Processing
- Oil and Gas - Well Screens
- Pulp and Paper Manufacturing
- Water Reservoir Intakes
Wedge wire could be utilized in all of the above industries as well as many more applications across other industries. Wherever filtration may be required, wedge wire should be carefully considered due to its effectiveness and the fact that it can be supplied as a final product.
Obviously, the selection in alloy and thickness will be dependent on what market and segment the screen is employed in. A metallurgist or technical expert can assist if there are any particular questions on this.
Physical Factors with Wedge Wire
It is crucial to consider physical factors like consistency, uniformity and surface finish within a wire when weighing up a suitable wedge wire for any application. A key factor for screens is the continuity of finish, especially within architectural applications. Generally, scratches and other visual defects will be easy to see in most screens.
With architectural products, how much reflectivity is present can have a serious impact in parallel to the consistency within the surface of the wedge wire. When looking from panel to panel, that can have an effect of visual discontinuity if one run is not identical to the other.
When making a successful screen, consistency within a spool of wedge wire is crucial. If the wedge wire manufacturer doesn’t possess the right equipment or have the necessary procedures in place for validating uniformity within a spool, the screen wire manufacturer runs many risks.
Variations in the spool means loss of continuity within the slots of that screen. The best-case scenario is a possible rework of a screen, but then there’s also the worst-case scenario, where the whole screen ends up scrapped. This causes a loss of time and labor, and time relative to that particular screen.
On top of that, there is the potential of missing a customer’s deadline.
Meeting Specifications and Testing
While numerous wedge wires have acute tolerances, that doesn’t necessarily mean that all wedge wire customers have the capacity to verify their final shape in order to authenticate that it meets both mechanical properties and corner/nose measurements.
Some screen manufacturers do have vision systems to validate the screen slot widths between wedge wires and may be able to observe cross-sections of the wedge. In most cases, trust is placed in the producer of the wedge wire, and that specification is being met.
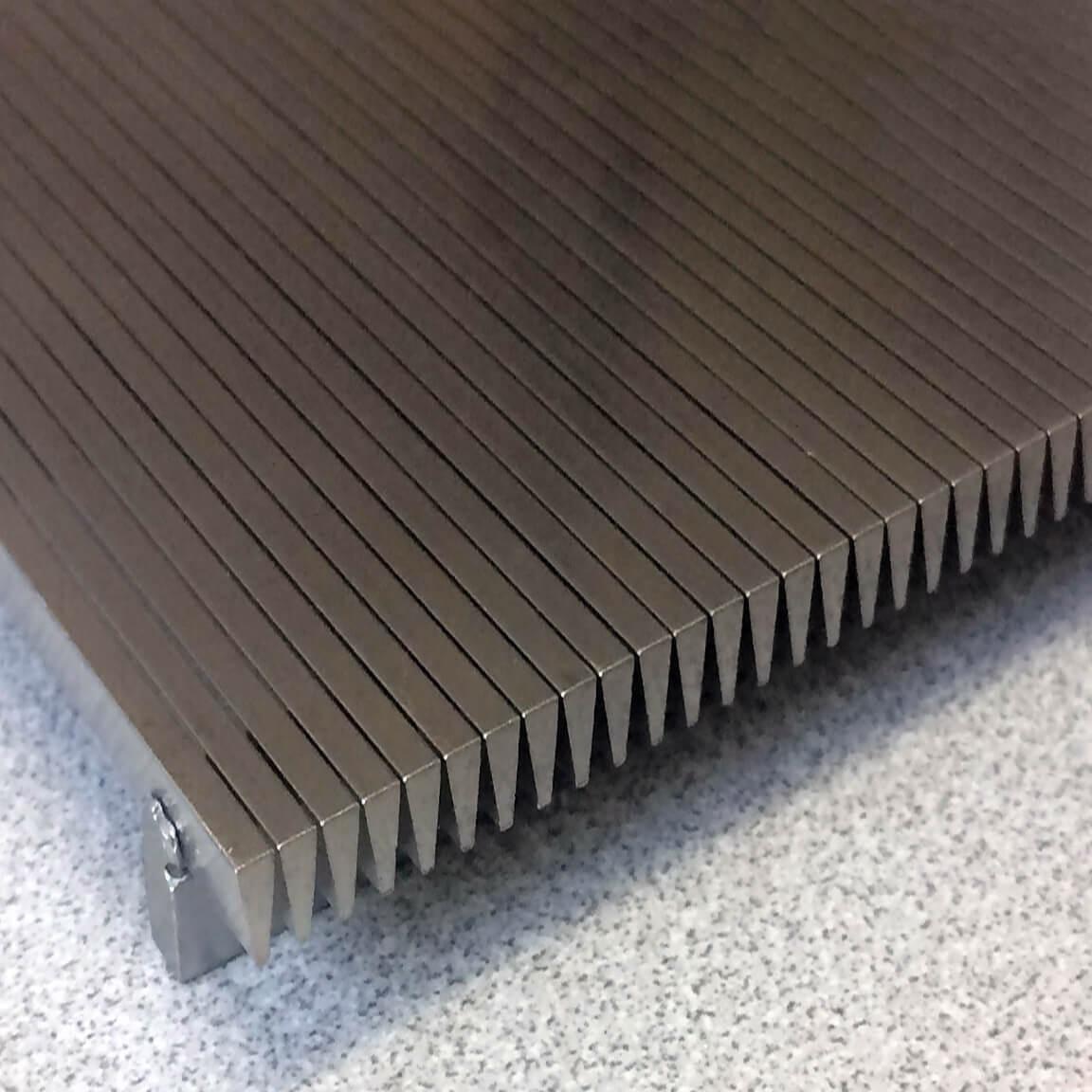
Image Credit: Ulbrich Stainless Steels & Special Metals, Inc.
That is why it’s crucial for screen manufactures to situate themselves with a vendor who strictly adheres to the guidelines set by them and the screen designers.
It’s not uncommon to run into a situation where Ulbrich has reviewed a customer print and then had to submit a request for revisions only to have the customer state, “My current supplier makes it to print.”
As a follow up Ulbrich always requests a sample to corroborate the measurements and in the great majority of cases, the wedge wire isn’t to print and the customer is unaware of the fact.
As with several other industries, the specifications of screen wire continue to get tighter and tighter. As a result, it’s vital to choose a wedge wire vendor who not only invests in the most up-to-date technology for wire production but also invests in suitable testing equipment and vision systems to ensure orders are received as intended.
Coming to a long-term understanding of all the factors that go into producing a successful wedge wire/profile bar is a critical factor too. Due to the diversity of products Ulbrich manufacture, quality systems from other industries flow through its entire business model.
The same quality standards and care that have gone into successful manufacture in aerospace and medical applications for decades also apply to Ulbrich’s wedge wire production as well as all other products manufactured by the company.
Ulbrich Wedge Wire
This material can be supplied by Ulbrich to meet a business’s exact specifications. Through Ulbrich’s annealing, wire drawing, flat wire rolling, wire shaping processes, the end product can be delivered in a final shape that meets the print requirements exactly.
Key factors to consider include managing the radius of both the corner and the nose of the shape. These are critical control points in the production process because they will establish the screen’s filter performance and how it separates undesired material, which immediately impacts flow rates (how fast fluids pass through the screen).
Slot width and corner radiuses are extremely dependent on application and are key dimensions to consider when selecting a wire because this will determine the size of materials allowed through the filter.
Ulbrich’s industry-leading tight tolerances and metallurgical support can assist the decision-making process when considering what dimensions to choose and other factors that need to be regarded, such as variations in hardness, inconsistent finish, or other quality issues. Please contact Ulbrich today to learn more.
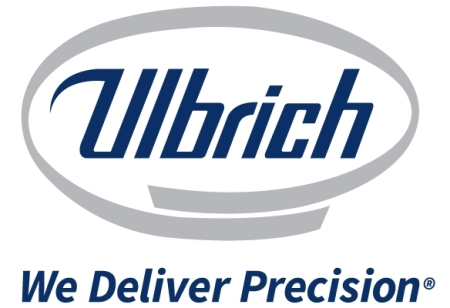
This information has been sourced, reviewed and adapted from materials provided by Ulbrich Stainless Steels & Special Metals, Inc.
For more information on this source, please visit Ulbrich Stainless Steels & Special Metals, Inc.