Hydrocarbon streams leading to ethylene steam cracking furnaces often contain considerable levels of corrosive products, water and salts. Contaminants in the inlet hydrocarbons can severely impact ethylene production in a number of ways.
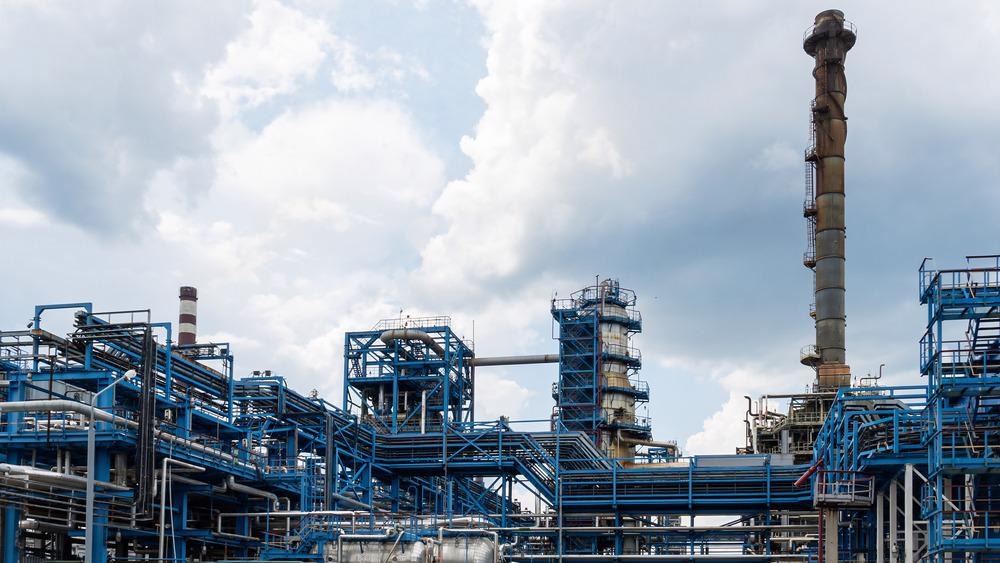
Image credit: kalyanby/shutterstock.com
Sodium and iron oxides are known to be coke promoters, and when present, they can inhibit the run time of the ethylene furnaces before decoking is necessary, and in some cases, diminish the life of the furnace tubes by as much as one third.
Unplanned or frequent decoking cycles results in ethylene production loss, reduced furnace tube life and leads to increased maintenance costs. Frequent decoking will also result in more particulates being released into the atmosphere and can generate real environmental concerns over excessive emissions.
The naphtha filter rating: established the best compromise to improve furnace protection
IFT between water & naphtha at the cracking plants and in the refineries range from 1 to 20 dyne/cm and is extremely stable. This also necessitates the use of high efficiency liquid-liquid coalescers for separation.
Naphtha feedstocks can store considerable amounts of solid particulate in the form of corrosion products, and both aqueous and solid contaminants must be removed. Stand-alone particulate filtration may be required for the feedstock, and in others cases, include a coalescer system with pre-filters.
Thus, to protect the steam cracker, a filter with a complete rating of 10 μm should be used.
Numerous types of filters are available, including depth, pleated, string wound, and advanced high flow capacity designs that utilize laid-over, crescent-shaped pleats. Backwash type filters become more economical than the disposable type when the solids loading is high.
While the initial capital investment is higher, but the operating costs are significantly lower.
High Efficiency Liquid-Liquid Coalescers
Separating emulsified water in the feed hydrocarbon to the steam cracker can be a complicated process. Pall Corporation has designed and patented new non-disarming coalescer media that is manufactured with unique, formulated polymers and fluoropolymers.
These high efficiency coalescers are well-suited to emulsions with interfacial tensions as low as 0.5 dyne/cm.
High efficiency coalescer systems with coalescer elements are stacked on top of separator elements.
An important consideration for a coalescer system is suitable prefiltration to extract solids. The coalescer system also offers the following process benefits:
- Enhanced control of the naphtha to steam ratio due to reduced fouling of control valves and flow meters
- Lengthened furnace tube life as a result of incorporating liquid-liquid coalescers, which facilitated the elimination of sodium attacks that significantly reduce the lifespan of the tubes
- Lowered fuel gas consumption due to less fouling
- Lowered particle and CO2 emissions as a result of a reduction in annual decoking operations
- Reduced fouling and plugging in the cracking coils
- Reduced maintenance costs associated with mechanical cleaning of the transfer line exchangers
- Reduced CO formation and concentration in the cracked gas
High efficiency liquid-liquid coalescers and filters used for the treatment of liquid or gas hydrocarbon feeds in ethylene plants were found to enhance the productivity of the steam cracker while reducing emissions by reducing the frequency of the decoking process.
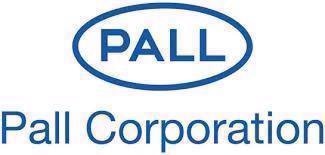
This information has been sourced, reviewed and adapted from materials provided by Pall Corporation.
For more information on this source, please visit Pall Corporation.