Pump shafts are used in countless types of rotating equipment. Fundamentally, they are exploited in any industrial application requiring the transport of fluid from one location to another. Here, the causes and consequences of cracks in pump shafts and how they are detected are considered.
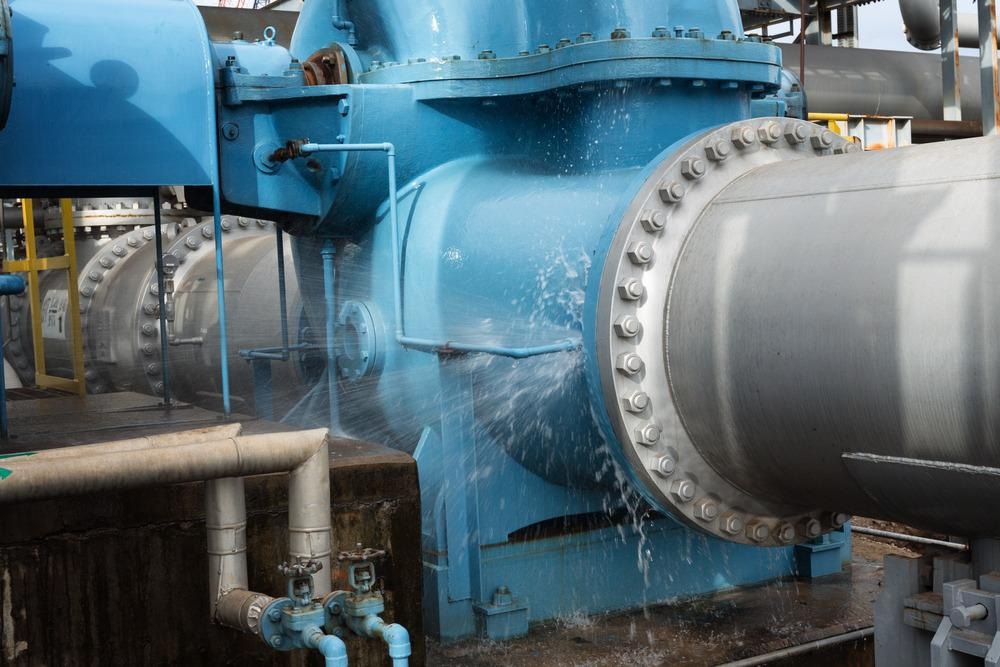
Image Credit: Photostriker/Shutterstock.com
Generating and Transmitting Torque
In terms of industry sector, perhaps the most prevalent use of centrifugal pumps is in mining, where high performance is expected under extreme conditions, although as noted they find use in a diverse range of applications.
Typically a pump shaft constitutes the central component within a centrifugal pump rotor and carries around it all the necessary components for function and performance. The components which include spacer sleeves, bearings and impellers are contained within a seal.
Rigged with blades, a series of impellers allow shafts to generate and transmit torque by rotation when they deflect fluid, converting mechanical power into pump power. A good example of pump power is the use Jet Edge Waterjet Systems make of water in its series of ultra-high-pressure pump products.
In these, water can be applied to sample cutting or the creation of multiple abrasive jets driven in continuous operation mode.
Pump Shaft Quality (PSQ)
Pump shafts tend to be made from high spec. stainless steel that can be altered in shape as required for any particular pump application.
To be applicable to the rotating industries and minimize the extent of wear and tear, shafts are prepared by turning, grinding and polishing them, the finish indicated by the Pump Shaft Quality (PSQ) where usually high diametrical tolerances are required.
General Wear and Tear
Although shafts have a seal, passing through the non-rotating pump casing, offering protection from both air ingress and potential fluid leakage, the materials within shaft seals always start to wear down because of friction.
In addition to this, wear always arrives in rapid deterioration of impellers. In most cases, this results from velocity speed where the outer impeller edge experiences high tip velocities.
Also common is uneven wear due to turbulence where high speeds induce irregular fluctuations within a fluid. Increasing fluid speeds cause directional changes that can lead to eddies if the fluid is fast enough and able to cause sufficient drag between inter and intra layers of fluid.
Crack Formation
Continuous applied loading degrades the materials that shafts are composed of. The strength and modulus of a material can become undermined creating areas of localized stress which induces excessive plastic deformation leading to cracks.
High thermal stresses and fatigue are also responsible for many crack initiations. Maximum stress can be anticipated where a shaft surface makes contact with a fluid because these are the points where thermal gradient extremes are located often in combination with bending effects.
Pumps can also experience cracking by the on-set of corrosion, although this rarely escalates to machine-shaft failure. Overload is another mechanism that can prove problematic.
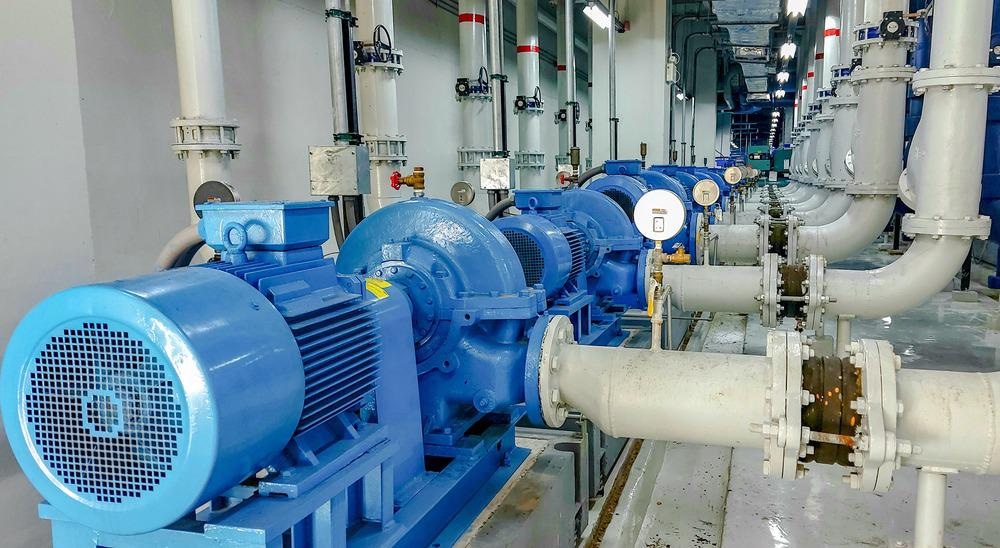
Image Credit: Wisarut pumipak/Shutterstock.com
If left undetected, crack propagation can lead to fracture of the rotor from the reduction of its cross-section which, through time, will become unable to withstand dynamic loading which ultimately can instigate fast brittle fracturing.
Vibration Monitoring
A propagating crack in a pump shaft can affect pump vibration. Vibration monitoring is its own science, but in the simplest of terms, 1 x rpm (or IX) and 2 x rpm (or 2X) vibrations mean vibration frequencies that are the same as the rotation speed (one oscillation per rotor revolution) and 2 x the rpm (two oscillations per revolution).
Deviations in 1X and 2X vibration vectors flag as an early diagnosis of a cracked shaft. Unbalance-like excitations emerge when cracks appear. Vibrational modes becoming visible in the radial direction with 180° phase differences where 1X and 2X vibration signals are predominant in the axial direction.
An open crack fosters 2X vibrations; the amplitude of these can be proportional to although a highly nonlinear function of crack depth. Steady-state 1X and 2X vibrations are not usual at around 26 microns and 7 microns, respectively, but can rise to ca. three times the established normal operating vibration as a crack propagates.
Orbit Observation
Another means of diagnosing a crack in a shaft is the study of rotor orbits. Cracks making contact with pumped liquid together with mechanical or thermal stresses can magnify bows that can emanate from a propagating crack. Bows can generate high amplitude 1X vibrations. In addition to these, high 2X vibration components can cause internal loops to appear on rotor orbits, indicating unbalances surrounding a shaft.
Crack and Failure Mitigation
Crack-related issues are often attributable to catastrophic pump failure and therefore extensive investigation has been undertaken over the years to mitigate the risk of cracks appearing.
In short, any intervention that minimizes friction throughout pump infrastructure makes pump shaft failures less likely.
Fluid turbulence, for example, can be reduced by intelligent and ergonomic system design where valve placement, the number of tees and elbows can be minimized. Innovative load spreading across components will lower the likelihood of failure while Hof B. et. al. reported the use of minimum continuous safe flow (MCSF) to obviate excessive wear within pumps required to continuously operate.
Thermal management in this context includes the elimination of temperature spikes often identified with low-flow operating regimes. The future will likely see the introduction of more “smart” components including pump shafts that have the ability to flag the approaching failure. This is a beguiling area of cross-fertilization between engineering and artificial intelligence, amongst other disciplines.
References and Further Reading
Nasir Tamin M. et. al. (2017) Fatigue Failure Analysis of a Centrifugal Pump Shaft. [Online] IntechOpen. Available at: https://www.intechopen.com/chapters/56973
Hof B. et. al. (2010). Eliminating Turbulence in Spatially Intermittent Flows. Science 19 (327) 1491 https://doi.org/10.1126/science.1186091
Disclaimer: The views expressed here are those of the author expressed in their private capacity and do not necessarily represent the views of AZoM.com Limited T/A AZoNetwork the owner and operator of this website. This disclaimer forms part of the Terms and conditions of use of this website.