The high-temperature performance of epoxy formulations cured with dianhydrides has been described in a previous article. The high crosslink densities achieved from the utilization of dianhydrides result in high glass-transition temperatures (Tg) and high retention of strength at elevated temperatures, at times, higher than the Tg itself.
The second feature comes from a relatively high rubbery plateau modulus for such highly crosslinked epoxies. For instance, Figure 1 demonstrates the dynamic modulus and tan δ vs. temperature for standard liquid epoxy, which is cured with BTDA (benzophenonetetracarboxylic dianhydride).
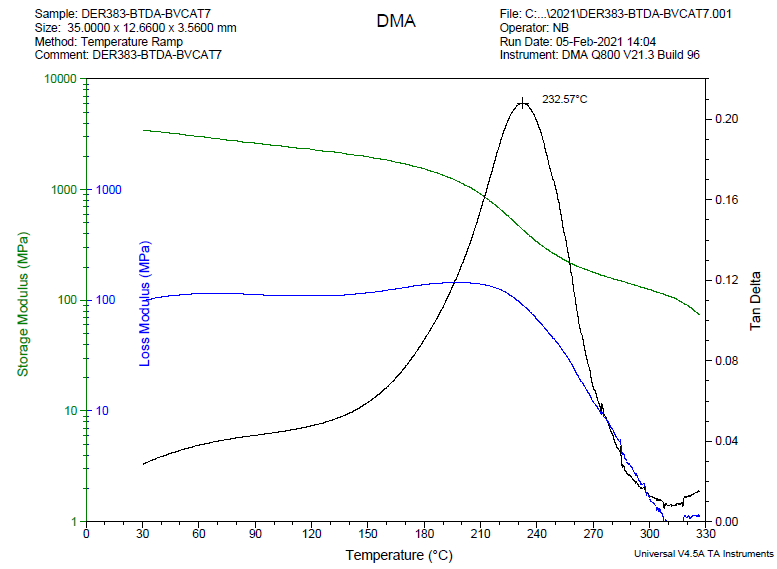
Figure 1. DMA data showing dynamic shear moduli and tan(δ) vs. temperature for standard liquid BPA epoxy resin (EEW 181) cured with BTDA (0.5 A/E ratio) at 200 °C. Note the high rubbery plateau for storage modulus, indicating a fairly strong material even above the Tg. Image Credit: Jayhawk Fine Chemicals Corporation
An epoxy adhesive does not have to use an all-or-nothing approach to benefit from a dianhydride. The utilization of a solid dianhydride as the only curing agent may not even be practical for some adhesive applications. This is when a combination with a liquid monoanhydride can be the best choice.
Table 1 demonstrates three example formulations utilizing a dianhydride in combination with MTHPA, which is a popular liquid anhydride for epoxy formulations. In these instances, the liquid anhydride acts as a low viscosity reactive diluent and carrier in which the dianhydride particles are dispersed to form a paste curative.
Table 1. Example formulations demonstrating the combined use of dianhydride and monoanhydride curing agents. Source: Jayhawk Fine Chemicals Corporation
Component |
Weight |
Weight |
Weight |
Part 1: |
BPA liquid epoxy resin, EEW 189 g/eq |
100.0 |
100.0 |
100.0 |
Part 2: |
BTDA* (dianhydride) AEW 161 g/eq |
21.3 |
26.5 |
29.8 |
MTHPA+ (monoanhydride), AEW 166 g/eq |
41.7 |
32.5 |
25.0 |
Latent cure accelerator, as needed |
—- |
—- |
—- |
Thickeners, fillers, additives, as needed |
—- |
—- |
—- |
A/E Ratio for formulations: |
0.72 |
0.68 |
0.63 |
Cure cycle: 10 minutes @ 150 °C; post-cure @ 200 °C suggested for best properties |
Expected Tg = 150 °C-180 °C based on overall formulation and cure conditions. |
* BTDA: benzophenonetetracarboxylic dianhydride
+ MTHPA: methyl tetrahydrophthalic anhydride
Based upon the needs of the application, for example, optimizing mechanical properties or balancing high Tg with handling characteristics, the ratio of the dianhydride to liquid anhydride in the blend can be optimized.
A substantial amount of BTDA can be dispersed in the MTHPA due to its relatively low viscosity, giving the formulator the freedom to maximize Tg while keeping the adhesive viscosity manageable.
This concept is also useful for applications that go beyond adhesives, for example, molding compounds or prepregs.

This information has been sourced, reviewed and adapted from materials provided by Jayhawk Fine Chemicals Corporation.
For more information on this source, please visit Jayhawk Fine Chemicals Corporation.