In this interview, industry expert Dr. Vinay Mishra discusses the critical role of high-purity dianhydrides within the electronics and composites industries. He highlights recent advancements in material purity and their impact on applications from aerospace to semiconductor manufacturing.
Can you describe what high purity really means in the chemical industry?
A typical commercial chemical is not supplied as a 100.0 %-pure substance but rather with an indicated %-assay of the desired chemical component, e.g., >95 %, 98 %, 99.5 %, etc. The remaining components in the product are generally considered undesirable and can be one of four categories:
- By-products from the chemical production process, which are not fully removed from the final product.
- Small amounts of process chemicals that make it into the final product, as it is isolated from the process.
- By-products formed within the material after the commercial product is packaged. This is a frequent concern for materials which are sensitive to atmospheric moisture or oxygen.
- Tiny contaminants which may come from raw materials or from the process itself and pass through into the final product.
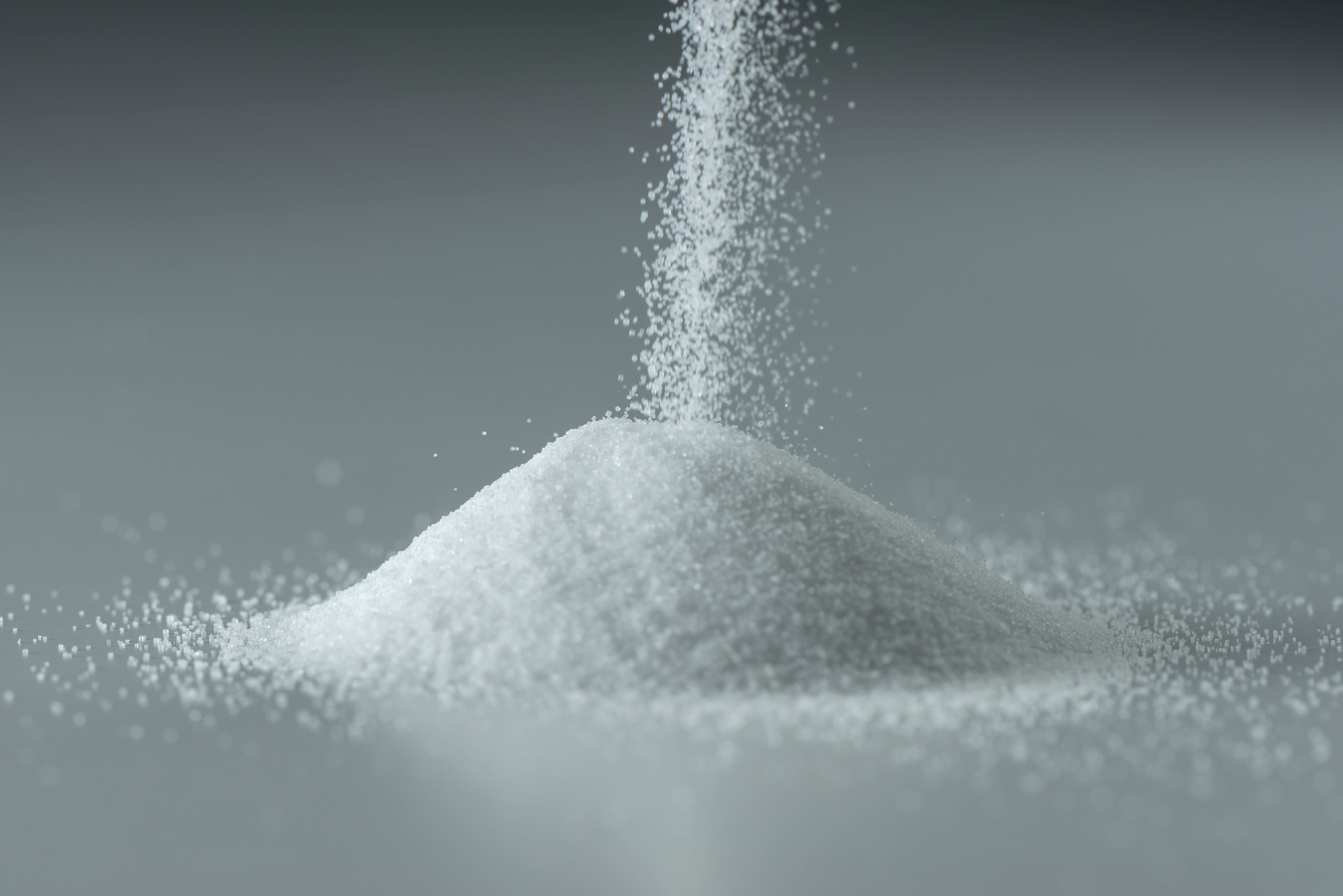
Image Credit: Kei Shooting/Shutterstock.com
So, how do manufacturers control the levels of such unwanted components in their products?
First, the levels of these undesirables deemed tolerable must be determined via a cost-benefit analysis for specific applications of the product. So in some way, the customer must be willing to share in the costs incurred in any reductions of the levels of such components.
The first two types of contaminants are generally controlled via process technology, and the third via improvements in packaging and storage conditions. The fourth category can require an all-encompassing effort. This can range from the detailed specifications of the chemicals used in the process, the interactions of these chemicals with materials of construction for the process equipment, and the material handling and storage after production.
For these undesirable components, what would be the typical acceptable levels in commercial chemical products?
For many commercial chemicals, the acceptable levels of the first three types of undesirables can get up to 1 % or 2 % for many chemicals. However, depending on the nature of the customer’s application, the fourth category can face limits on the order of parts-per-million (ppm) or even parts-per-billion (ppb).
Can you provide an overview of the importance of high-purity raw materials in industries like electronics and composites?
At a basic level, the term high purity for a commercial raw material may simply signify the amount of the primary chemical component present in it. In other words, purity may simply indicate a minimum guaranteed assay of the primary chemical component, e.g., “>97 %”.
However, the term has specific connotations for sophisticated applications in certain industries, where customers may treat an assay of >99.9 % as a given and rather demand the absence of specific undesirables. Such applications will then specify a maximum allowable amount of such contaminants, frequently at ppm-level or lower. High-purity raw materials are gaining prominence in the electronics and composite industries as their applications become increasingly sophisticated. They help minimize defects in downstream parts and assemblies and achieve consistent performance in applications that can be highly demanding.
Can you explain the connection between material purity and the overall performance of polymers in high-demand applications?
High purity monomers help to consistently achieve the target molecular weight of the desired polymer. This is important for ensuring the polymer performance is the best it can be, as well as consistent, e.g., from batch to batch. Lack of purity controls will invariably cause problems in this regard, something that advanced applications cannot risk.
Some high-performance polymers have additional requirements, e.g., keeping certain contaminants low in their building blocks and other raw materials. This is particularly important in aerospace composites used in high-temperature environments. For example, even low levels of iron can affect the thermo-oxidative stability of a structural composite made with polyimides. Similarly, polyimide dielectrics used in mobile phones and semiconductors can suffer reliability problems when even single-digit ppm levels of certain metals are present, e.g., iron, sodium, and calcium.
Jayhawk is well-experienced in producing fine organic chemicals with ultra-low metal or other inorganic content, measured in some cases on the ppb scale. For our dianhydrides like BTDA Ultrapure and 6FDA Ultrapure, we met our customers’ demands to limit specific metals and other ions to below 1 ppm. In some cases, we met even tighter specifications, e.g., of just a few tenths of a ppm.
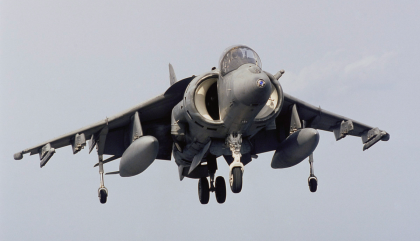
Image Credit: Jayhawk Fine Chemicals Corporation
In the context of electronics and composite materials, what are the main benefits of using these high-purity dianhydrides?
In electronics as well as composite applications, the final use of the components typically occurs well after production. While these industries use well-established processes for raw material approval and quality control, there is always the possibility that tiny variations in raw material compositions go unnoticed. While the likelihood is small, a potential risk exists for a compromised long-term performance of the final assembly. For demanding applications, customers can effectively mitigate such risk by simply switching to high-purity materials, which come with a far tighter raw material specification.
As the demand for more sophisticated electronics and advanced composites grows, how do you see the role of high-purity dianhydrides evolving in the market?
In electronics, polyimides are being used in progressively thinner films as electrical insulators. It is not uncommon to have films thinner than 10 microns, levels at which localized variations in the polyimide performance can lead to failure. This can be managed via a consistent molecular weight and macromolecular structure which are tied to the macro-level purity of the monomer.
In addition, even ultra-low levels of metal contamination in such thin polyimide films can have a major effect on its moisture sensitivity, thermal stability, and other characteristics tied to long-term performance. Similar factors are at play in high-temperature composite applications of polyimides as well.
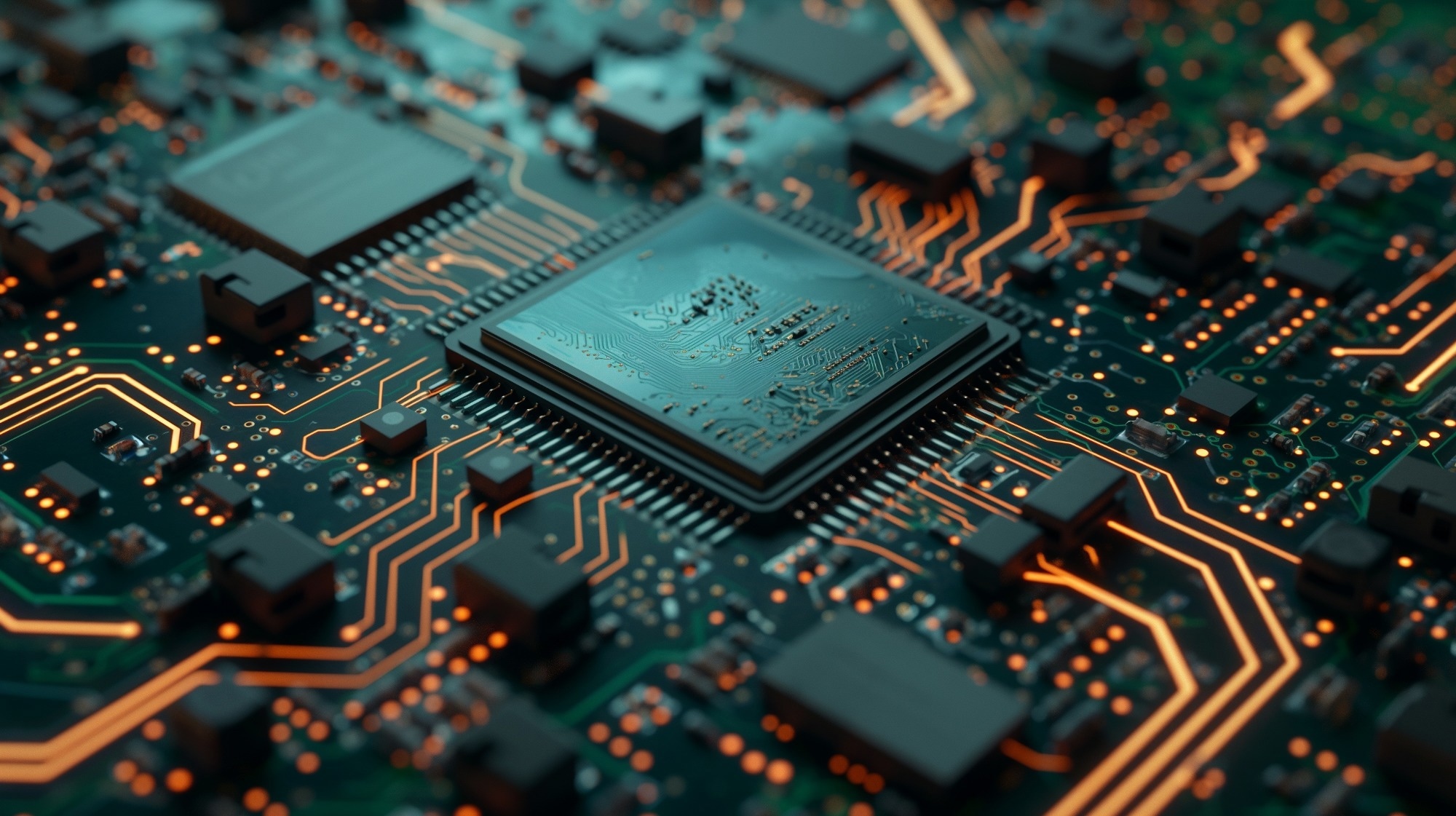
Image Credit: Sach336699/Shutterstock.com
For companies transitioning to high-purity raw materials, what benefits can they expect in terms of product performance and long-term reliability?
In the electronics industry, polyimides (PI) made with high-purity dianhydrides are used for various applications, either as thin films or varnishes to deposit ultra-thin coatings. Semiconductor manufacturing processes utilize such PI products in applications known as passivation layers, stress buffer coatings, redistribution layers, etc. Keeping metal contents in dianhydrides and other raw materials to a few tenths of a ppm allows for exceptional dielectric performance despite progressively thinning films and coatings within the electronics industry.
In the aerospace industry, carbon-fiber-reinforced composites made with PI matrix resins continue to gain new applications, such as within the jet-engine assembly. High-temperature-rated PI composites continue to replace metals in aerospace applications, leading to aircraft lightweighting and substantial fuel savings over their lifetime. However, long-term use of these products at high temperatures demands excellent thermo-oxidative stability. High-purity dianhydrides and other raw materials allow such PI composites to provide superior performance over the long term.
Looking to the future, what advancements do you foresee in the development of high-purity raw materials for polymers, and how will these impact the electronics and composites industries?
The biggest demands for advancement are expected from the electronics industry. As electronic devices continue to become more powerful, functional, and small at the time, polymeric dielectrics must provide exceptional electrical insulation at progressively thinning layers, already seeing single-digit microns in thickness. As a result, monomer producers are already being asked to ensure that metal levels are limited to the range of ppb or at least below 0.1 ppm.
Producers of raw materials such as dianhydrides are already stepping up to the challenge. For example, the Jayhawk Fine Chemicals site of Jayhawk Fine Chemicals Corporation already produces organic materials with metal content maxima in the ppb ranges. Such advancements in raw materials will drive continued adoption of polymeric dielectrics in electronics applications, enabling further innovation within this major industry that affects industrial as well as consumer use.
About Dr. Vinay Mishra 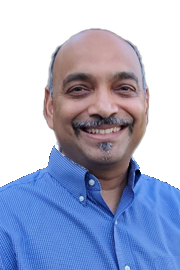
Dr. Mishra is the Technical Director of Thermoset Additives at Jayhawk Fine Chemicals Corporation, where he oversees the company’s thermoset technology strategies, specializing in coatings, composites, and adhesives. Since joining Jayhawk in 2019, Dr. Mishra has leveraged his expertise in epoxy and polyimide chemistries to support the company’s dianhydrides and other specialized monomers, focusing on high-purity materials for advanced applications.
With a commitment to innovation and collaboration, Dr. Mishra partners closely with clients to develop solutions for complex technical challenges, ensuring product reliability and performance for high-demand industries.
Disclaimer: The views expressed here are those of the interviewee and do not necessarily represent the views of AZoM.com Limited (T/A) AZoNetwork, the owner and operator of this website. This disclaimer forms part of the Terms and Conditions of use of this website.